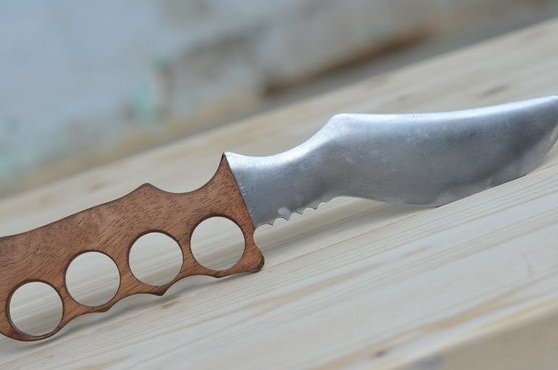
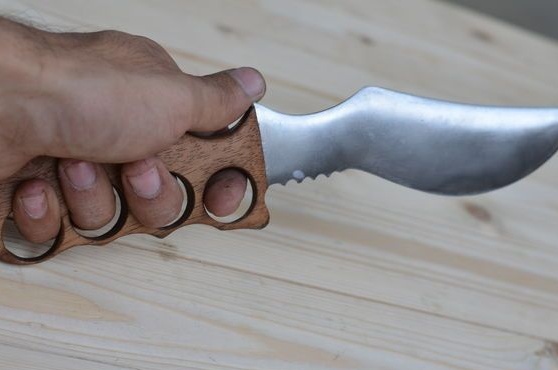
This time we’ll try to figure out how to make such a knife with an interesting handle with holes for the fingers. In some ways, this handle resembles brass knuckles, in fact, no one forbids using the knife for such purposes. It is not difficult to make this knife, but it uses not such a small set of tools. The material used is old sheet steel with a high carbon content, since it is such steel that can be hardened.
As for the profile of the blade, as for me, it seems not too convenient, but this does not interfere with making any other that you like.
Materials and tools for homemadeused by the author:
Material List:
- sheet steel (high carbon);
- wood for the handle;
- paper, pencil, drawing accessories for making a template;
- epoxy adhesive.
Tool List:
- belt grinding machine ();
- ;
- clamps, vice;
- marker;
- scissors;
- a drill with a bat for drilling large holes;
- whetted;
- ;
- heat source for hardening;
- oil for hardening;
- sandpaper and more.
The process of making a knife:
Step one. Material preparation
First of all, we prepare the material for making the blade. For these purposes, the author used sheet metal. He was lying around a bit, so it was covered with a layer of rust. We clean the rust with a grinder.
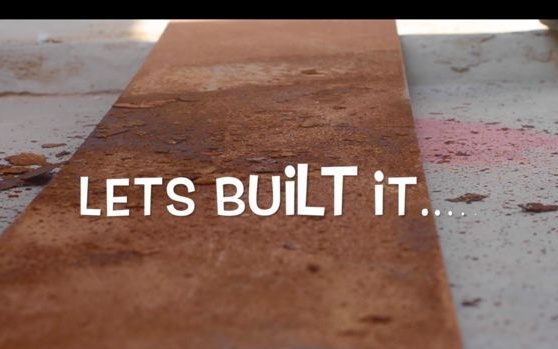
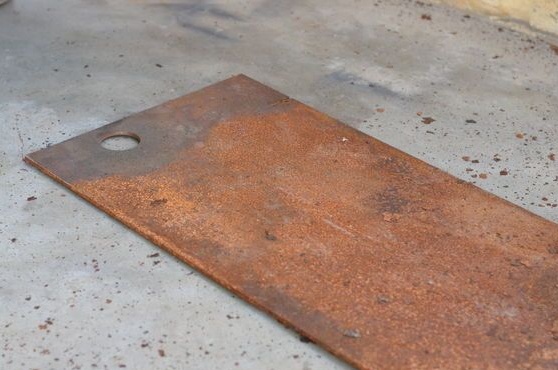
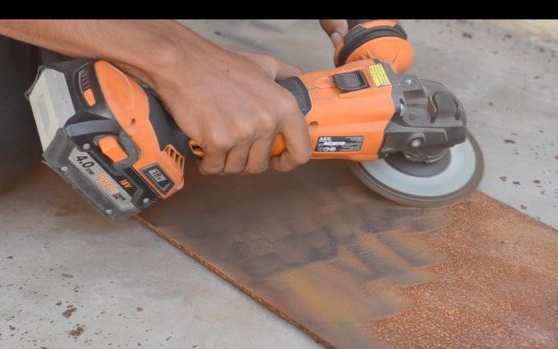
Step Two We make a template
On the Internet you can find a huge number of ready-made patterns for knives. Just print them on the printer, and then cut them out. Also, no one bothers you to come up with your own knife design. After cutting, glue the template to the sheet metal.
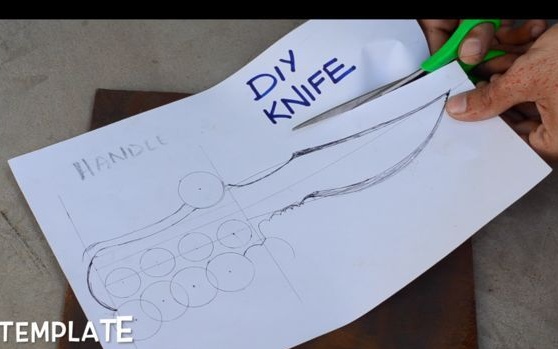
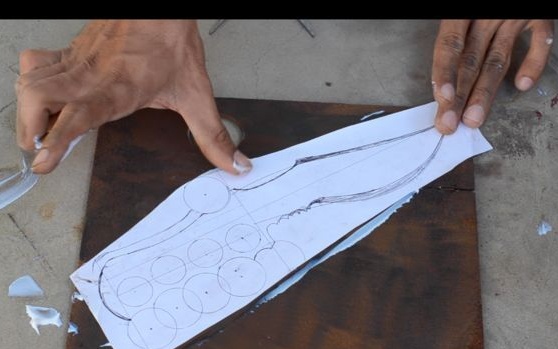
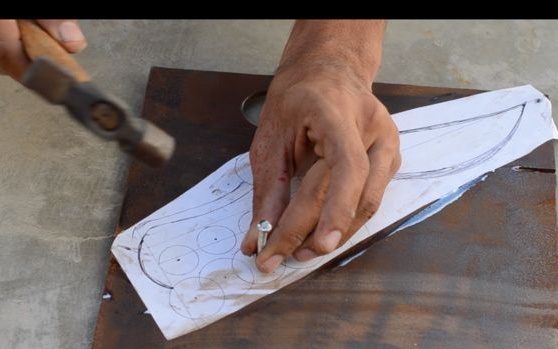
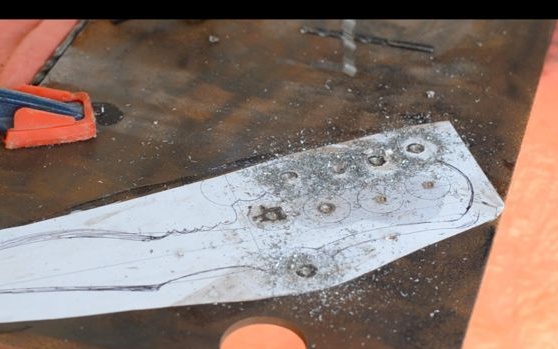
Step Three Drill holes
The author made the pen quite difficult to manufacture, but it contains all the uniqueness of the knife. The most difficult is to drill large diameter holes for your fingers. For these purposes, you will need a drill, or rather a drilling machine, as well as bits of the desired diameter.
In addition, with the help of a drill, the author also cuts the knife profile in some places, which can be done with the help of a grinder and other device it would be difficult.
For hard-to-reach spots you can use ordinary drills. Just drill a series of holes, and then this part can be broken off along the line of holes.
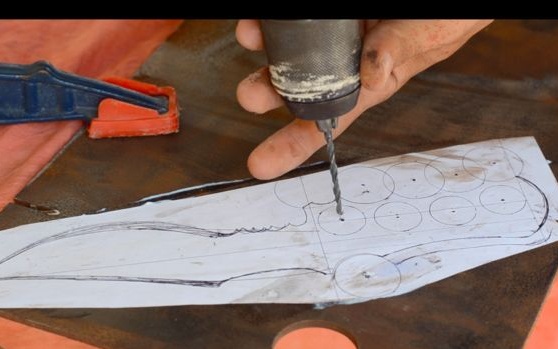
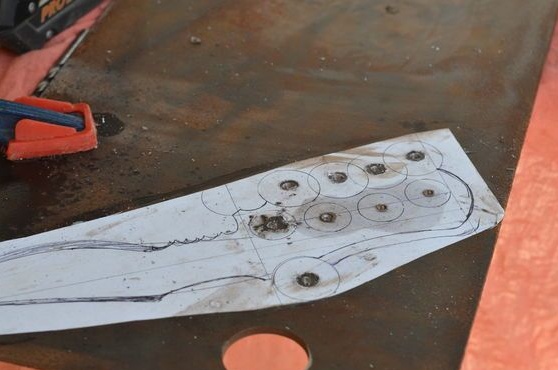
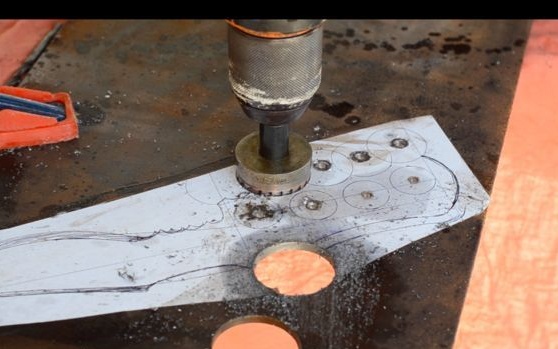
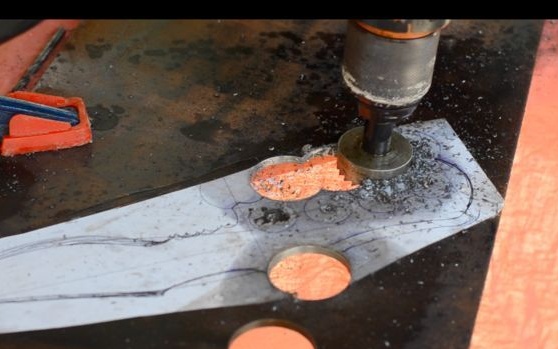
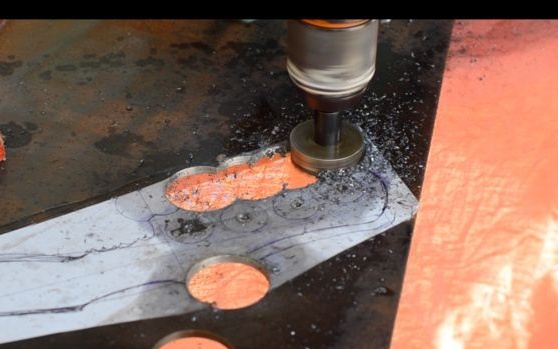
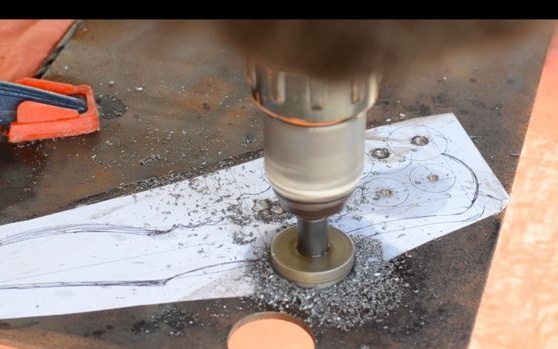
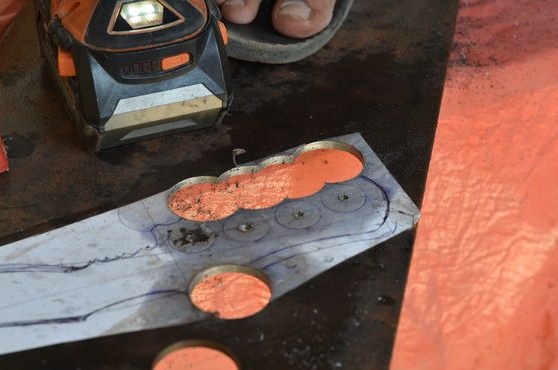
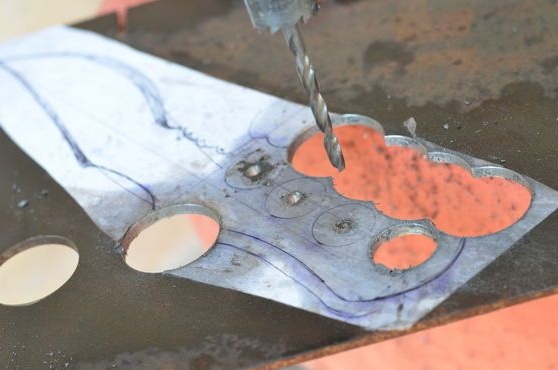
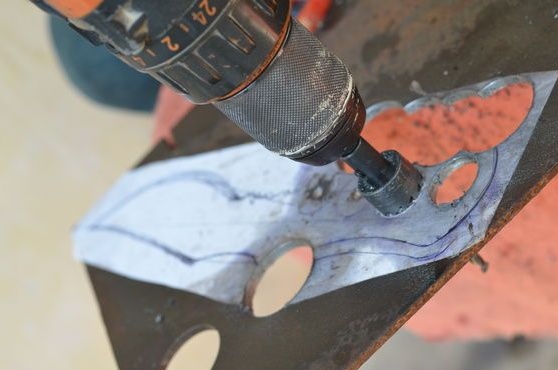
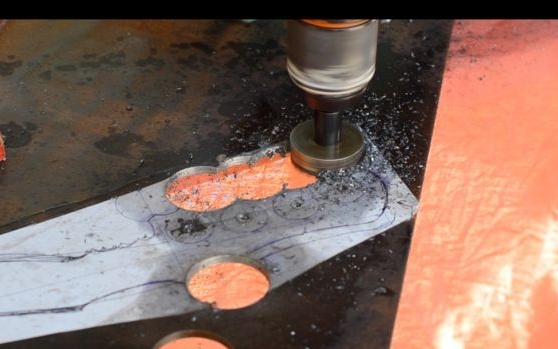
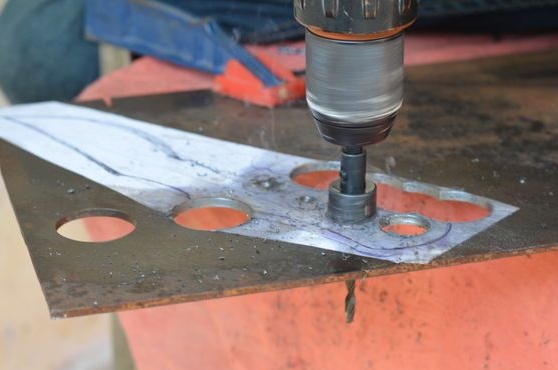
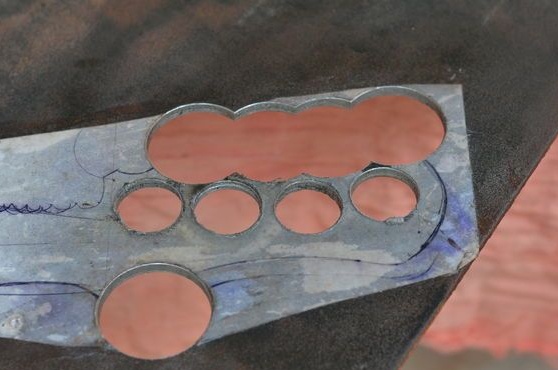
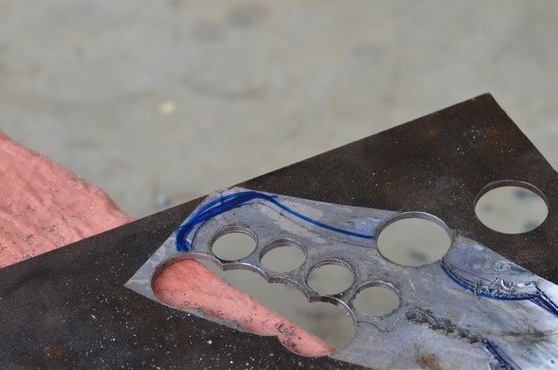
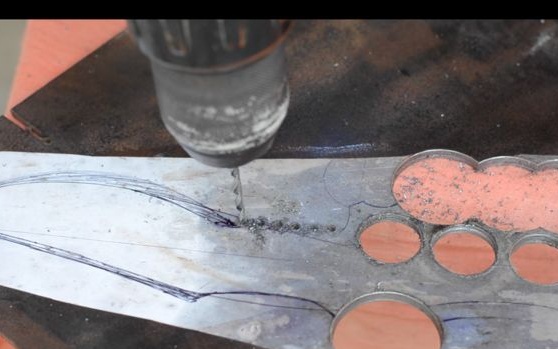
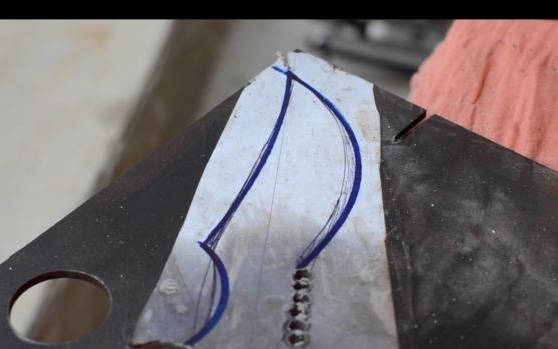
Step Four Cut a rough profile
Now you can cut the rough profile of the knife.Of course, a metal band saw will do the job best, but not everyone has such a tool. But this is not a problem, the profile can be cut with a grinder, you just need to spend more time and effort. And if you release the metal by heating and smooth cooling, it can be easily cut manually with a hacksaw.
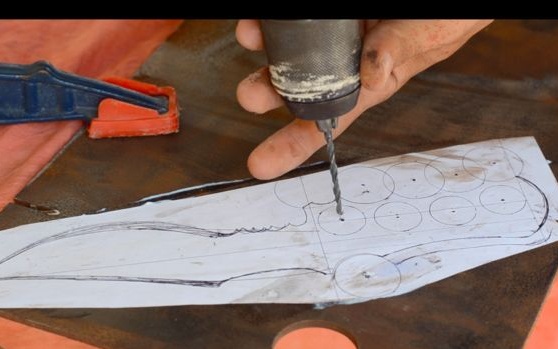
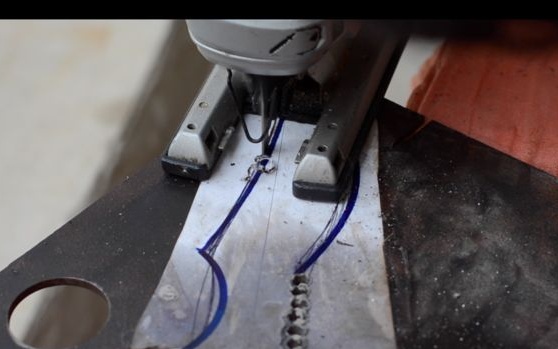
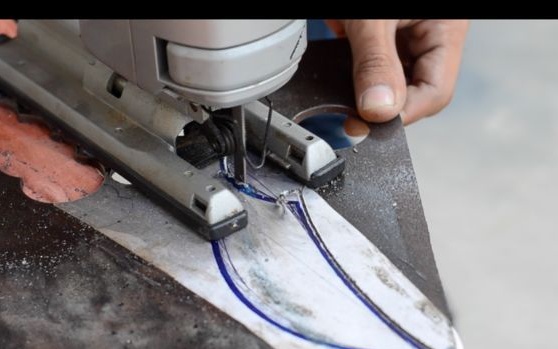
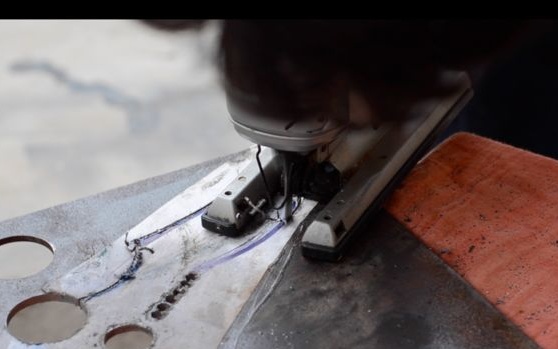
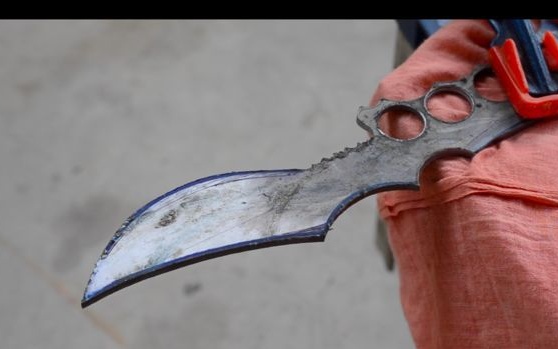
Step Five Coarse grinding of a profile
We proceed to rough grinding the profile of the knife. Your task will be to remove all the rough edges that remain after cutting the metal. Here you can use various tools, a belt grinder, a grinder, a grinder and more. As for hand tools, you can work with files, carefully holding the knife in a vise. Using an electric tool, do not overheat metal. If it changes color, then the steel is already overheated and will not be as strong as it was. However, hardening will help return the steel to its original state.
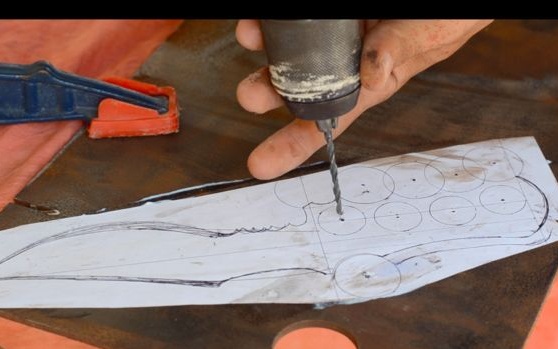
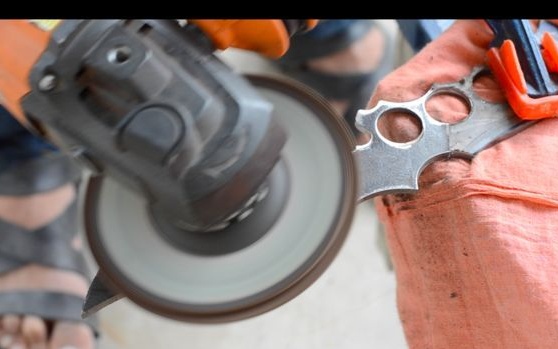
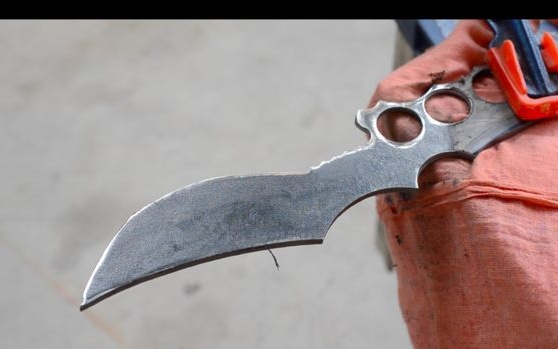
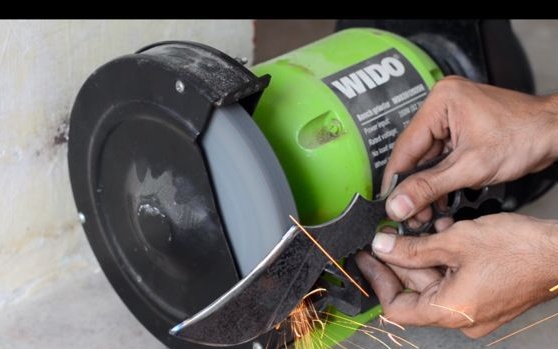
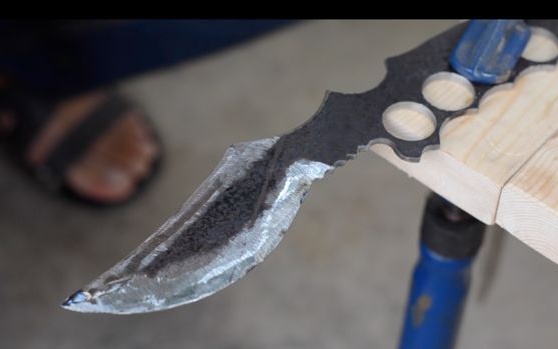
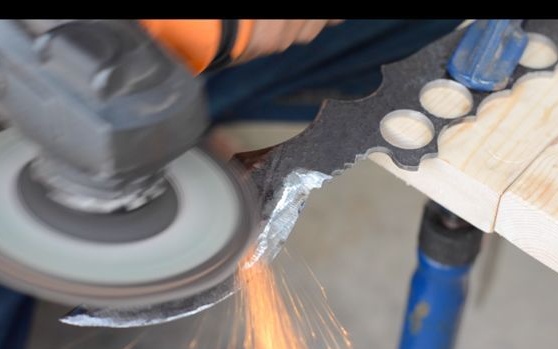
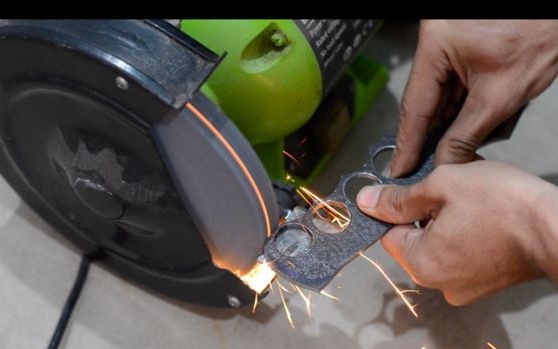
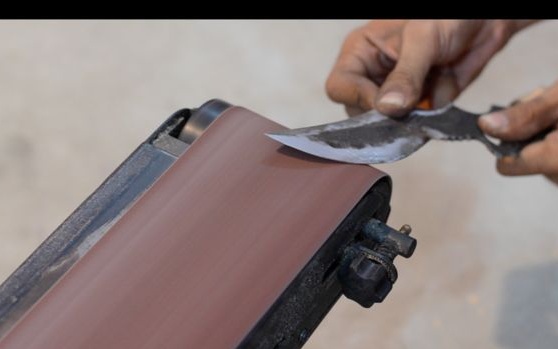
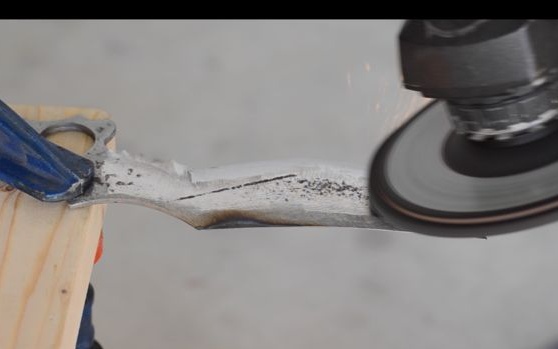
Step Six Metal polishing
At this step, the author makes the surface of the metal absolutely smooth and shiny. Such work is carried out using an orbital sander. If there is no such method, then you have to work manually. First we use larger paper, and then everything is smaller and smaller. As for the cloves and other relief places, we correct them with the help of files.
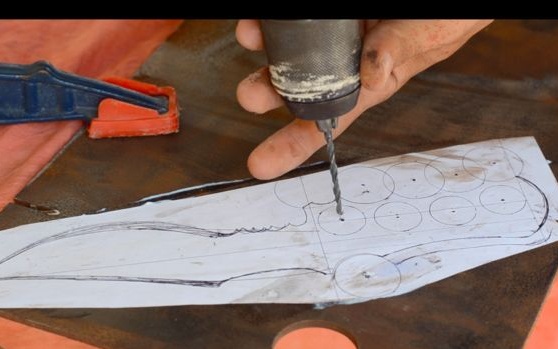
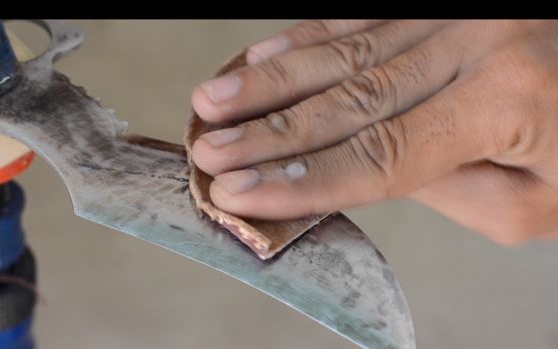
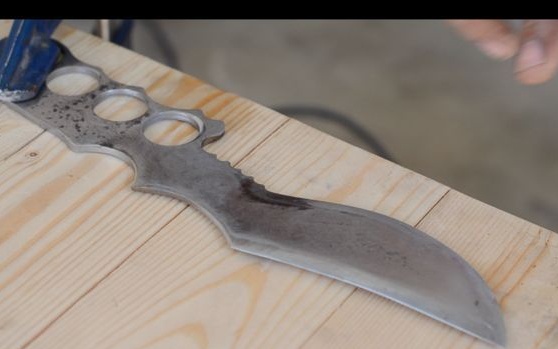
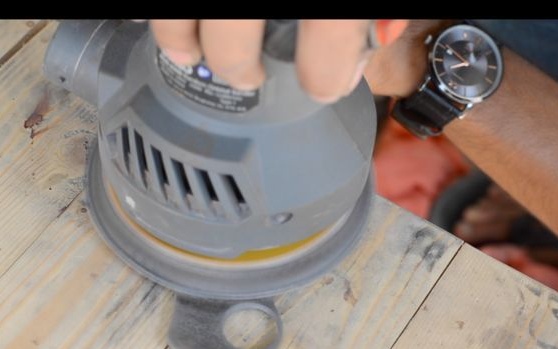
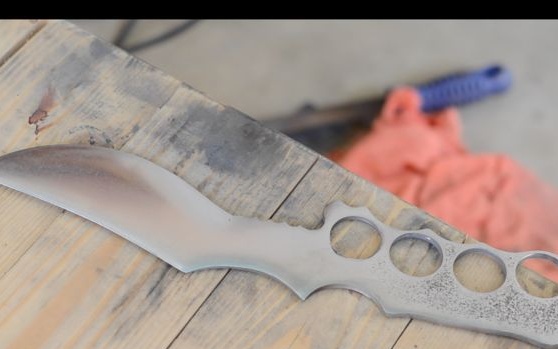
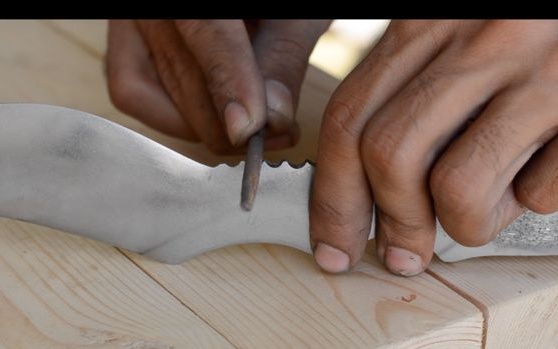
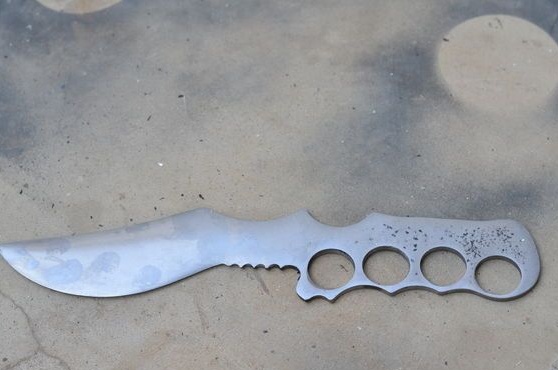
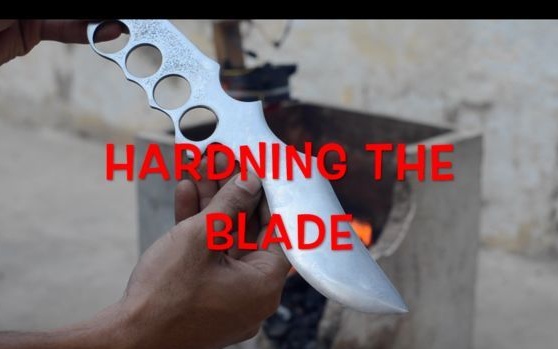
Seventh step. Metal hardening
Before this step, you must complete all metal processing work, not counting the sharpening. Hardening will make steel hard, the knife will remain sharp for a long time. For hardening, the author used a very simple method. We need good coals, we heat the knife in them to such a temperature until the metal ceases to be attracted by a permanent magnet. Usually its color becomes bright yellow. If the desired temperature cannot be obtained, a forced air supply will be required. It can be done with an ordinary household hairdryer.
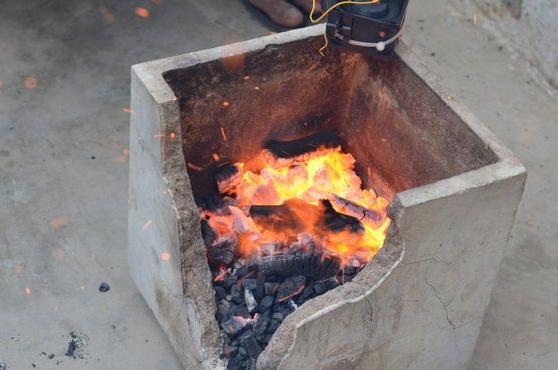
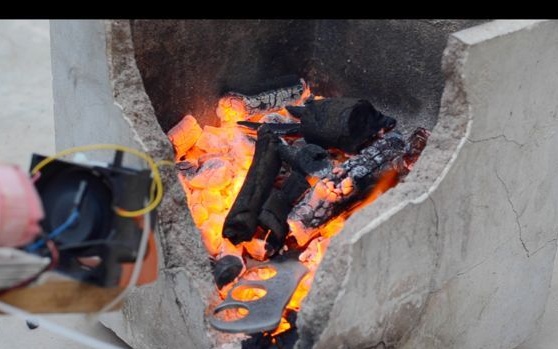
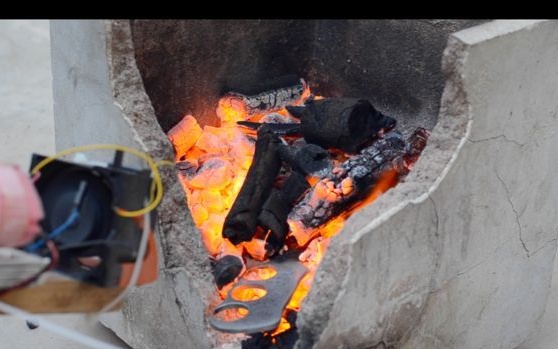
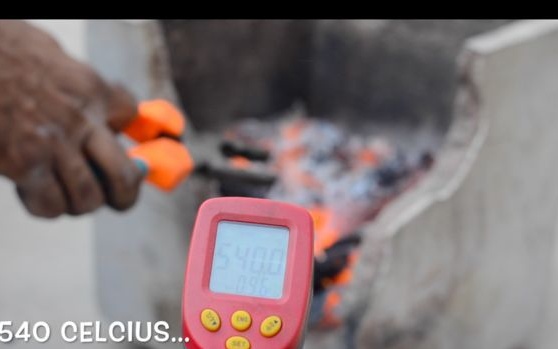
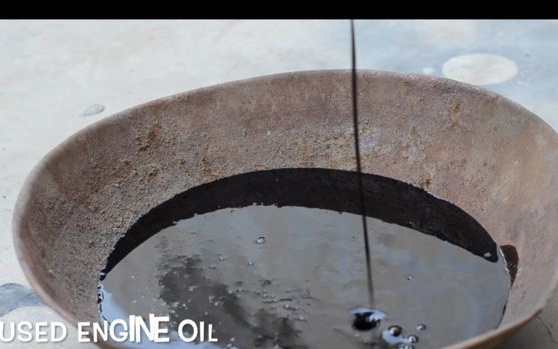
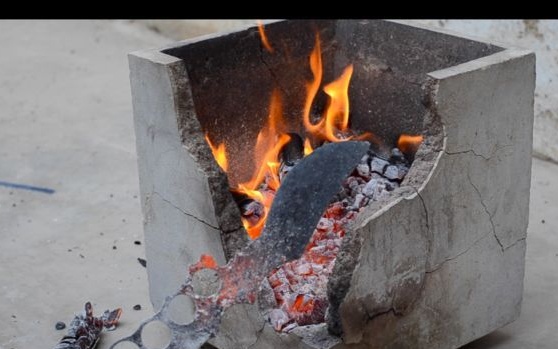
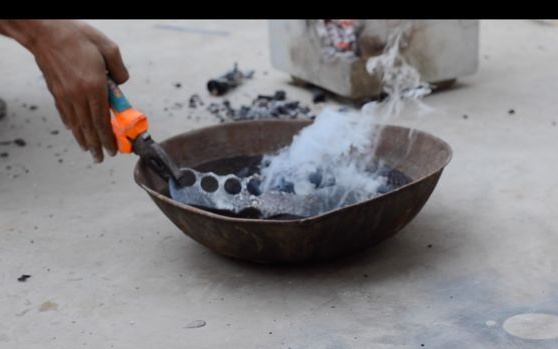
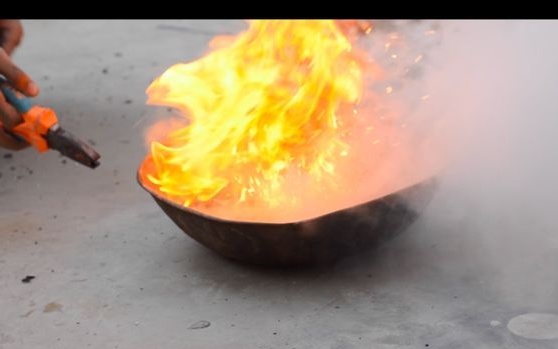
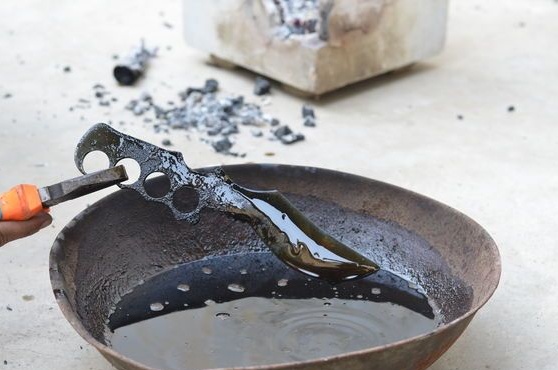
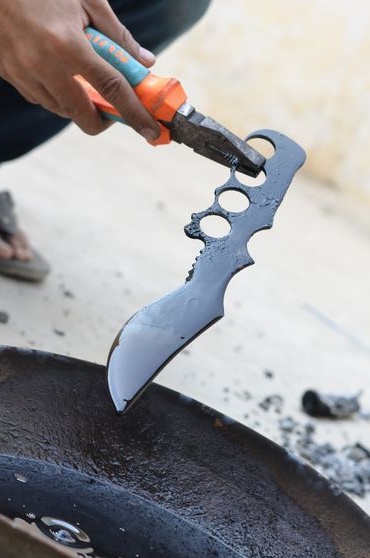
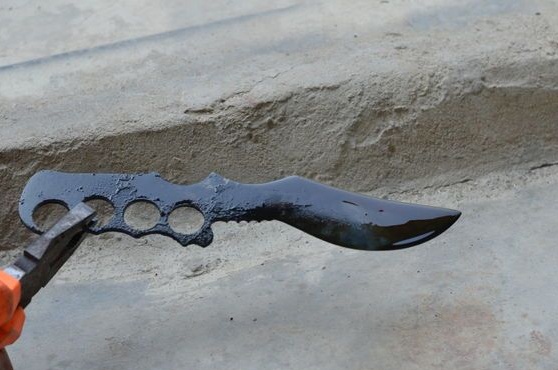
When you heat the metal to the desired temperature, cool it in old engine oil, the oil can also be heated so that the metal does not deform.
After quenching, the author forgot to perform another step - this is the release of metal. If it is not done, your blade will be too fragile and crumble at the slightest blow. For a vacation you will need an ordinary household oven. We heat it to a temperature of about 200 degrees Celsius, place the knife for an hour and allow the oven to cool with the door closed.
Step Eight. Final grinding
After tempering, the metal will have scale, burnt oil and other impurities. All of them will need to be cleaned and the metal brought to its final state. For such purposes we use sandpaper, a belt grinder or an orbital grinder.
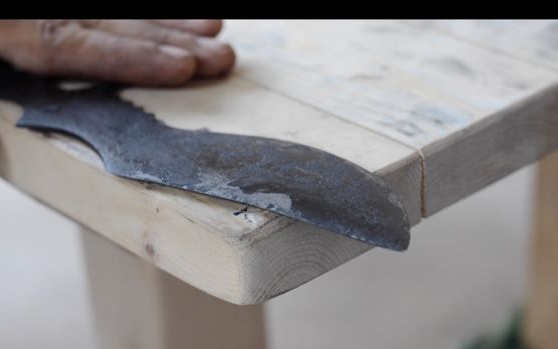
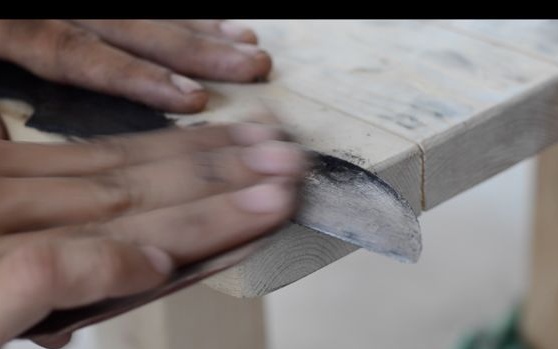
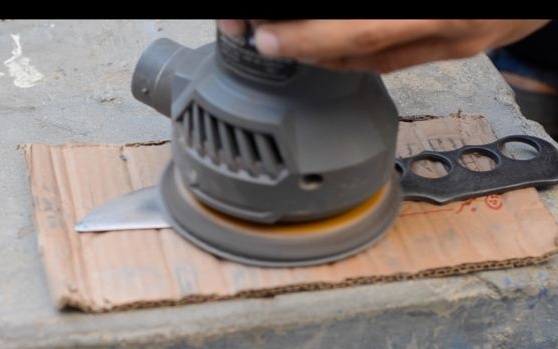
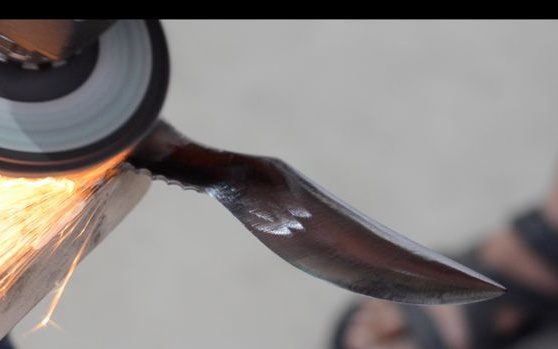
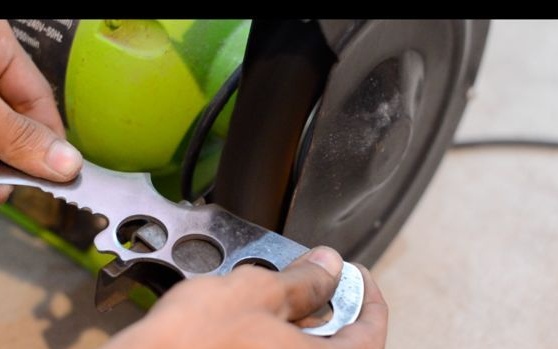
Step Nine. Wood handle finish
To decorate the handle with wood, you will need to find two thick little things. We cut off excess from them, adjust to the maximum size, and then just glue to the knife. Epoxy adhesive is used for bonding. Before bonding, sand the metal thoroughly and wipe it with acetone so that the glue sticks securely.
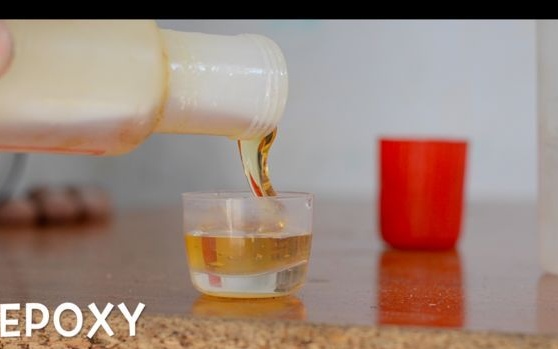
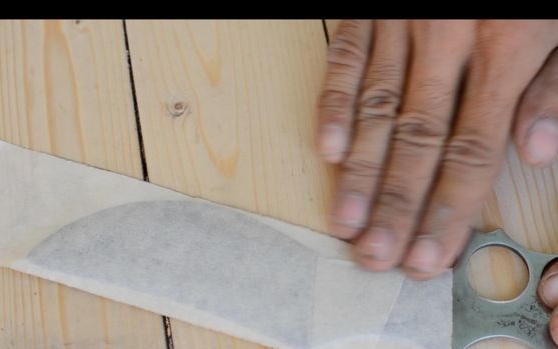
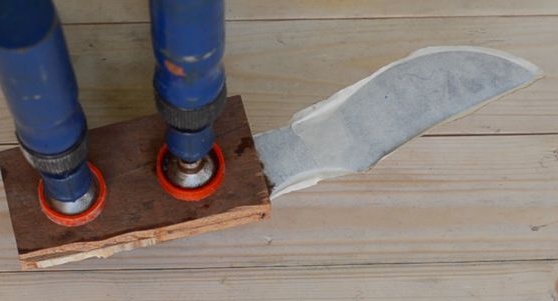
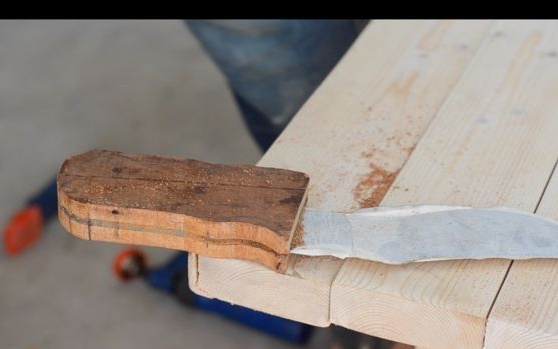
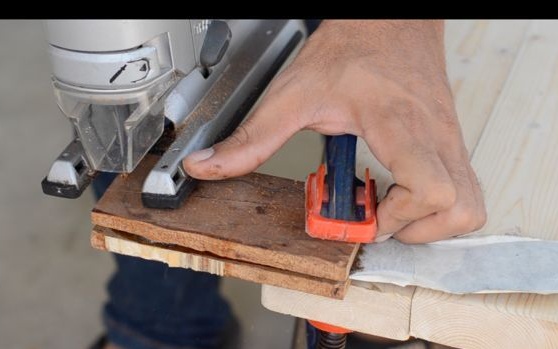
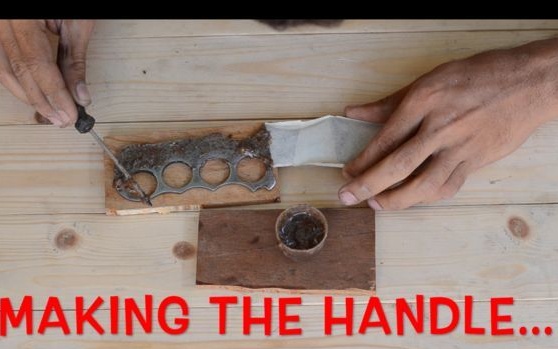
When the glue dries, it usually takes a day, it is possible to form a handle profile. We just need to grind off the excess, make the handle absolutely smooth. Large pieces of wood can be removed with files on wood. Well, all other work is carried out on a belt grinder, as well as an orbital machine.
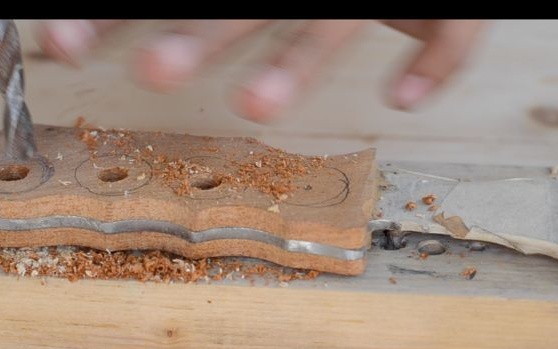
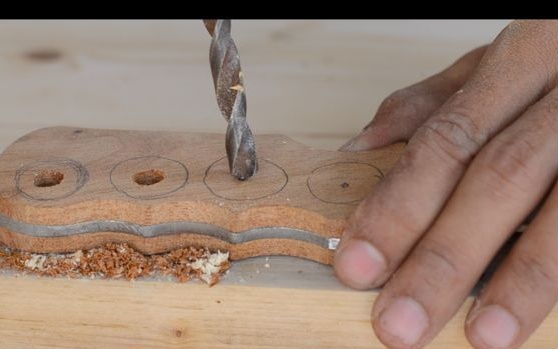
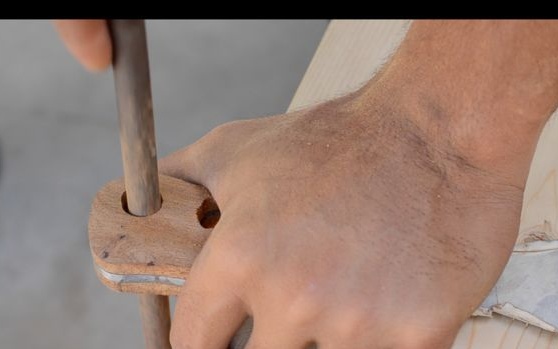
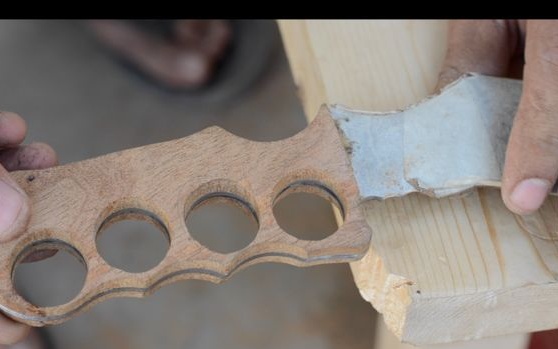
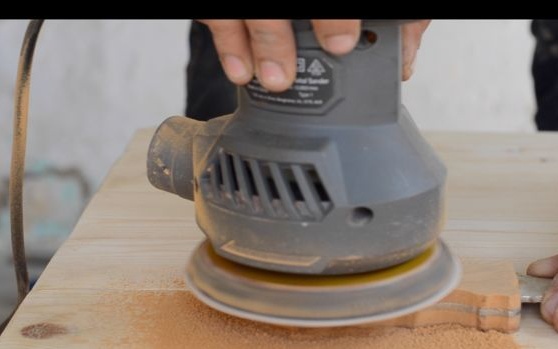
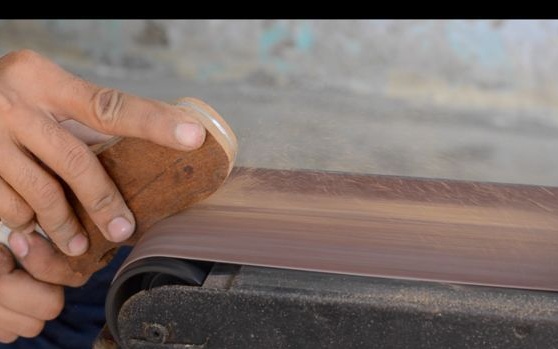
In the right places, do not forget to drill holes for your fingers. First, drill small holes, and then bore them to the desired diameter.
Step Ten Protective layer
The knife is ready, apply varnish or other protective coating, such as linseed oil, to the wood. Thanks to this, the pen will look more beautiful, and even it will not absorb moisture and, as a result, crack.
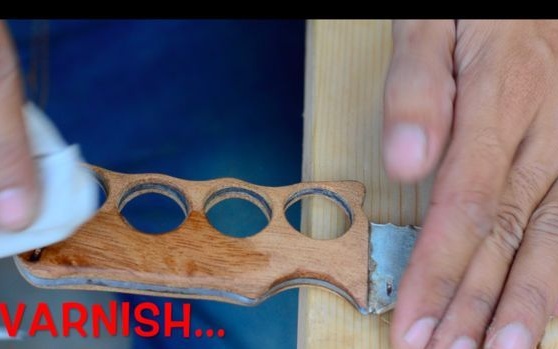
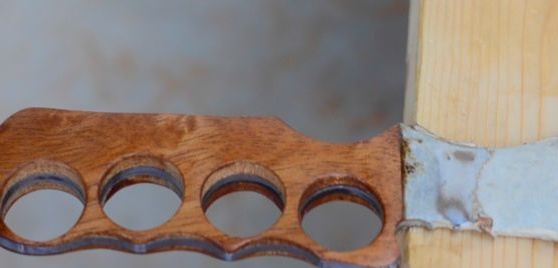
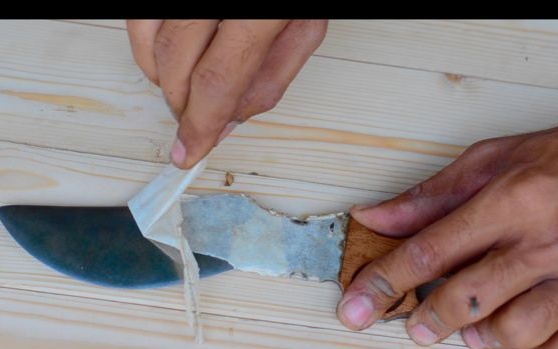
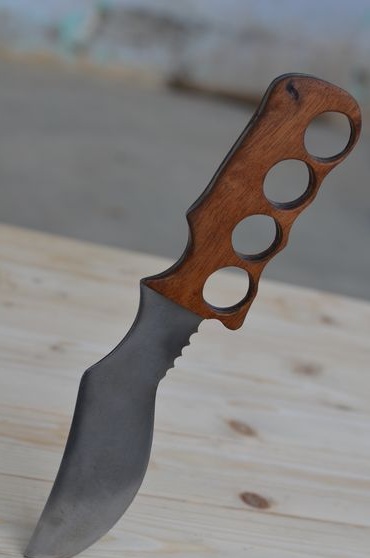
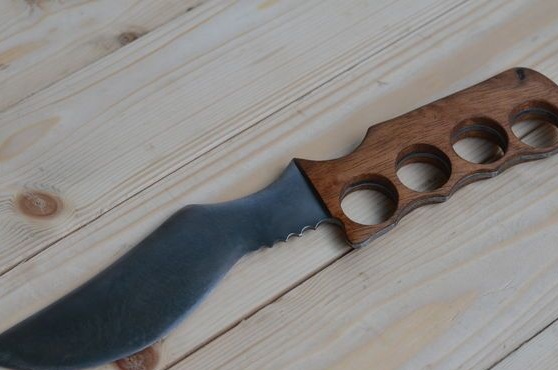
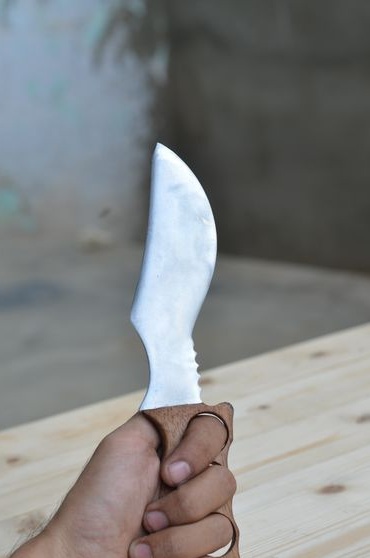

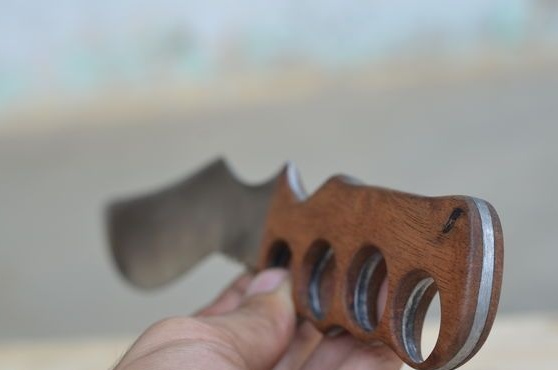
All that remains for you now is to sharpen the knife properly. Good luck