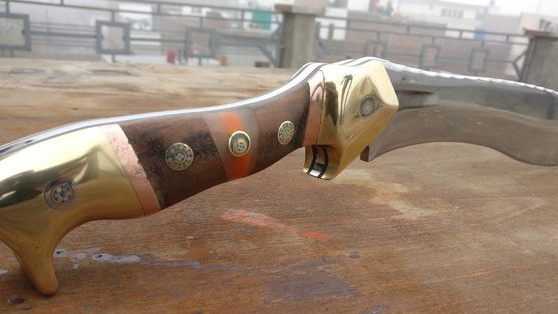
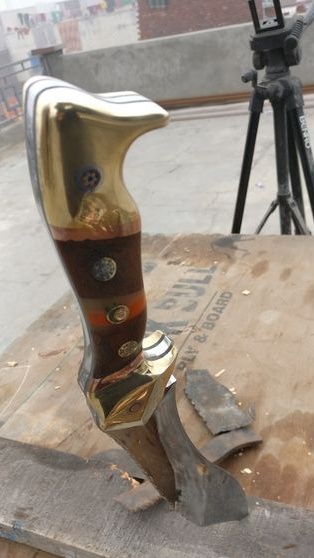
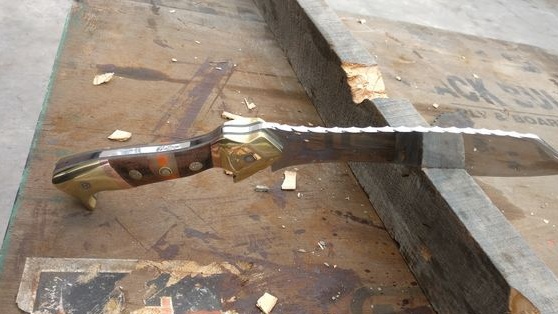
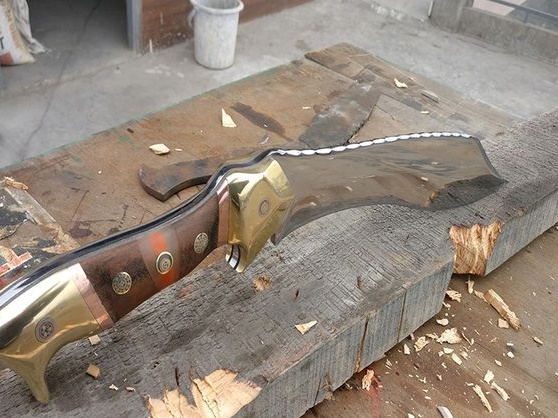
The homeland of the Kukri knife is Nepal. The kukri blade has a characteristic “falcon wing” profile with sharpening along a concave face. It is believed that kukri comes from the Greek copis, which has a similar bend, and came to Nepal with the army of Alexander the Great in the 4th century BC. e. The knife was exactly in this style and decided to make a master.
Tools and materials:
-Spring steel;
-Brass;
-Brazilian nut;
-Phosphor;
-Mikarta;
-Mosaic pin;
-Epoxy adhesive;
-Back paper from 60 to 1000;
-Polishing paste;
-USHM;
Cut-off wheel;
-Petal circle;
-Polishing wheel;
-Drilling machine;
-Hammer;
-Anvil;
-Vise;
- Files;
-A device for sharpening knives;
-Nadfiles;
-Centimeter;
-Paper;
-Pencil;
-Marker;
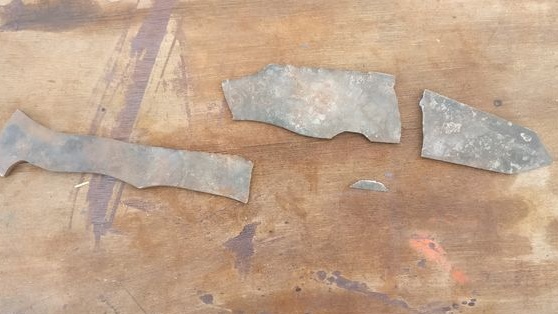
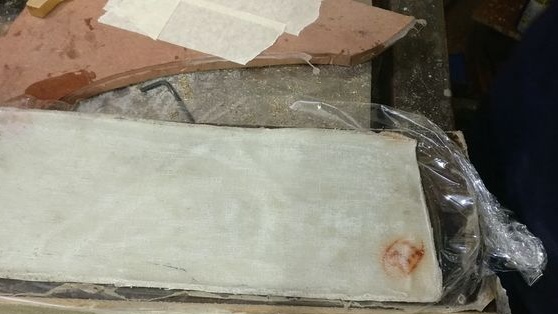
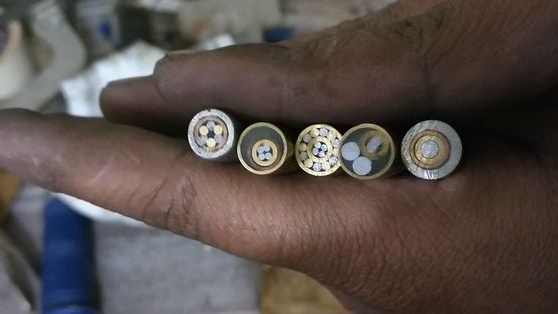
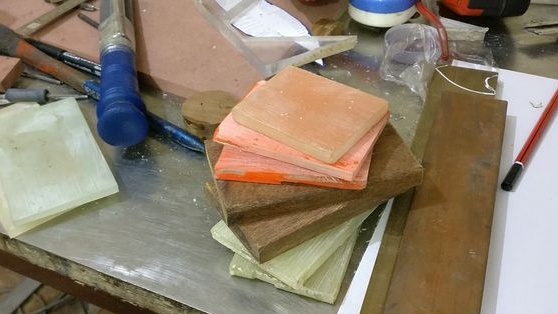
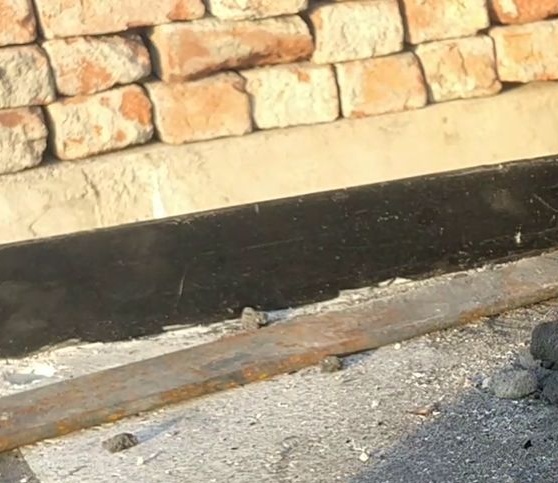
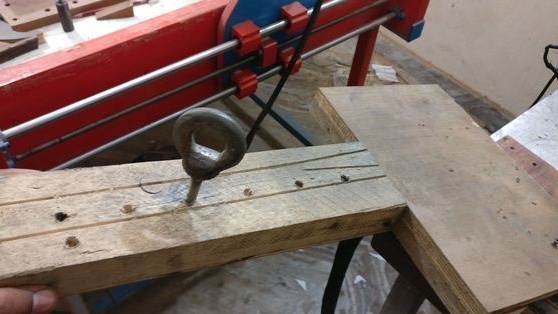
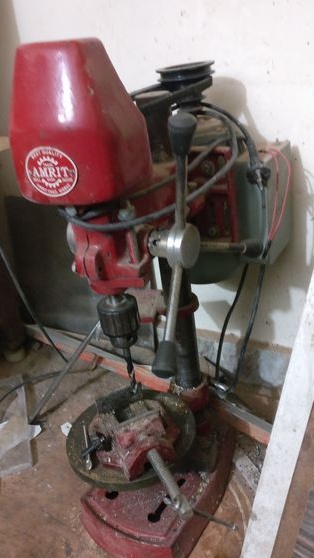
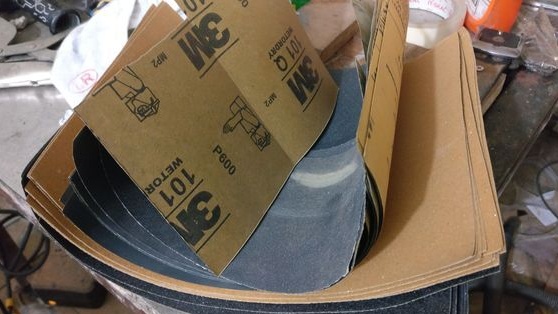
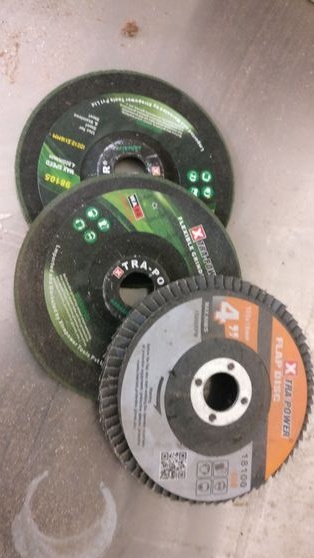

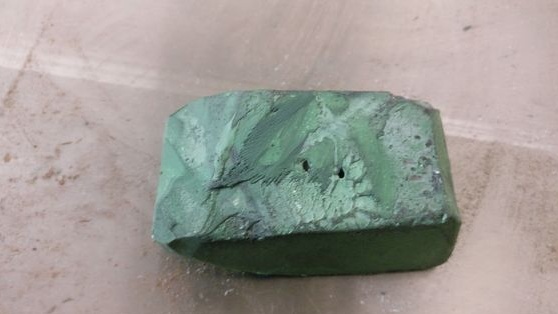
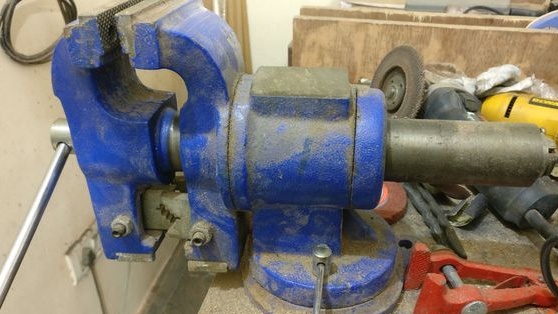
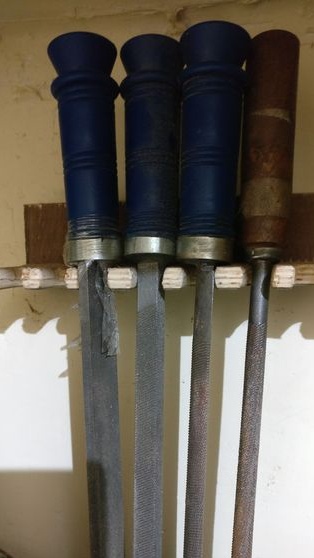
Step One: Forging
In Nepal, such knives are made of spring steel. The best are the springs of German cars. The master also used spring steel.
Heats the metal and forging gives it the desired shape.
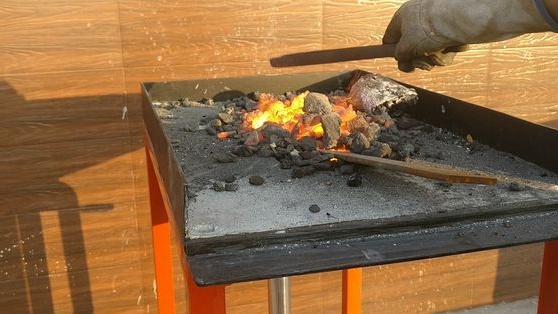
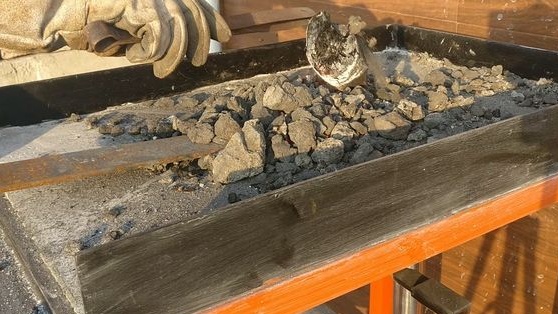
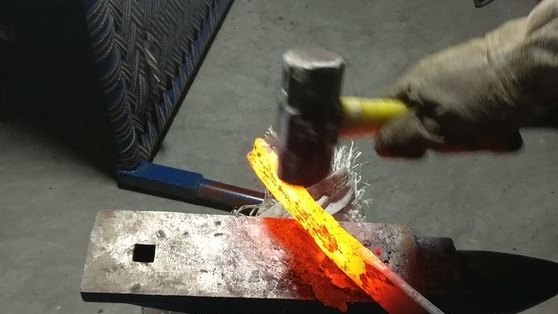
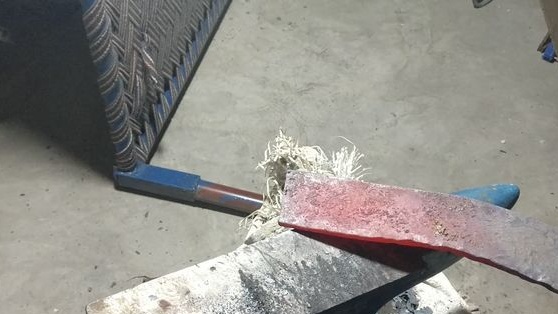
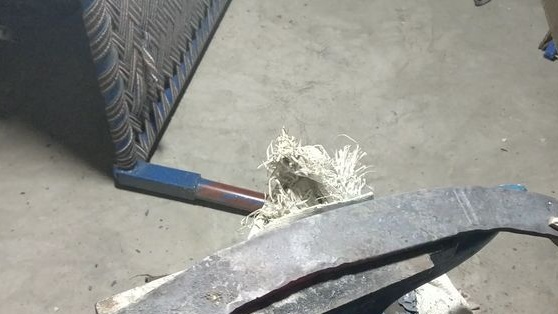
Step Two: Turning
With the help of angle grinders, he grinds the workpiece.
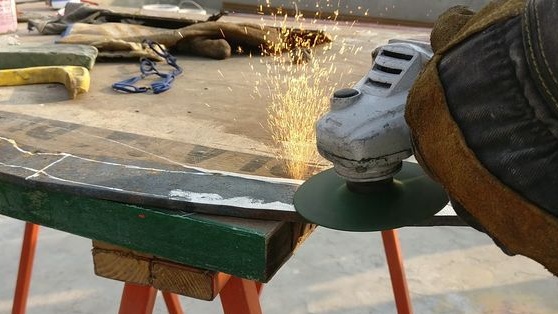
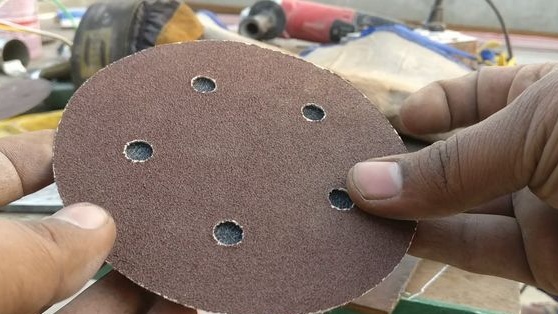
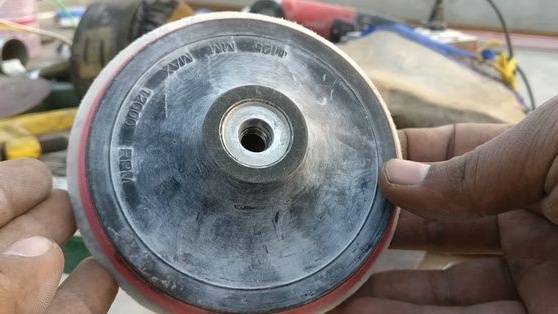
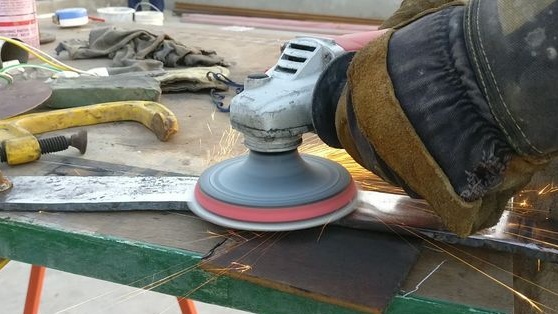
Step Three: Design
The blank is placed on a sheet of paper and circled. Then draws the details on the template. Transferring the drawing to the workpiece.
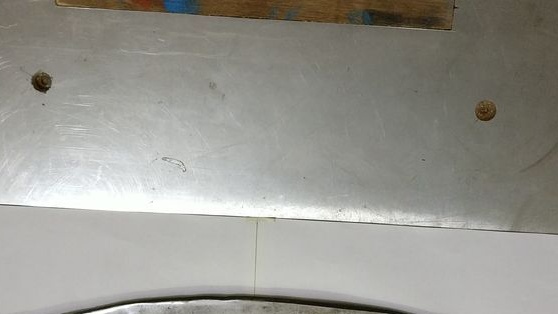
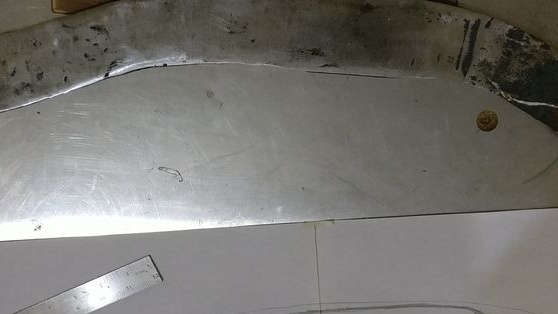
Step Four: Form
With an angle grinder and a file, it forms the shape of a knife.
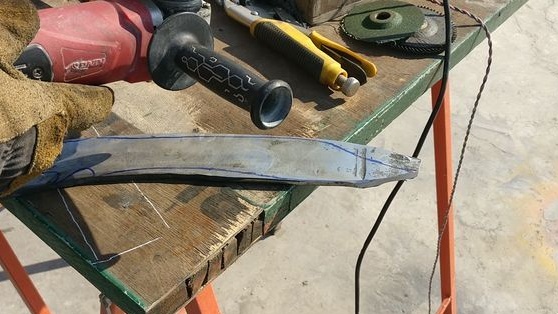
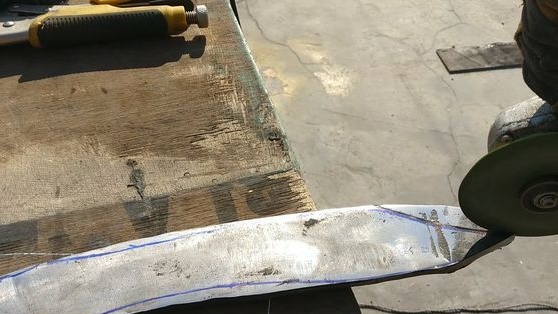
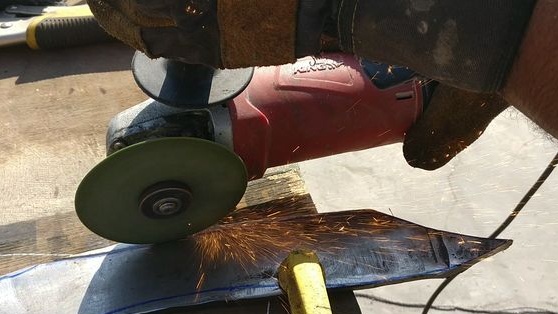
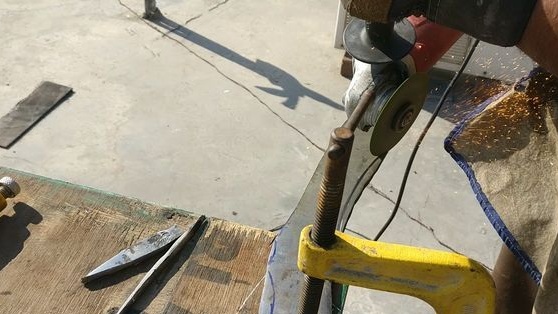
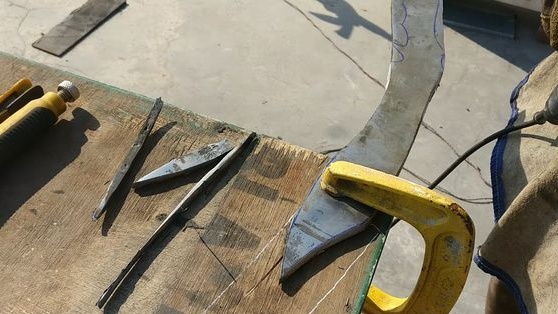
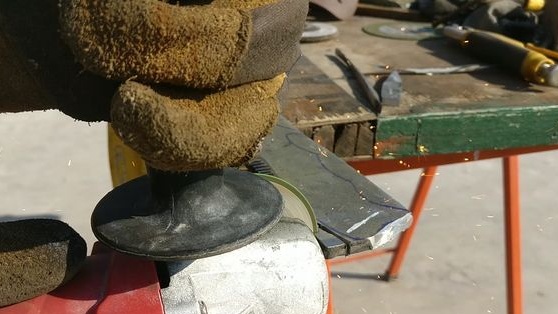
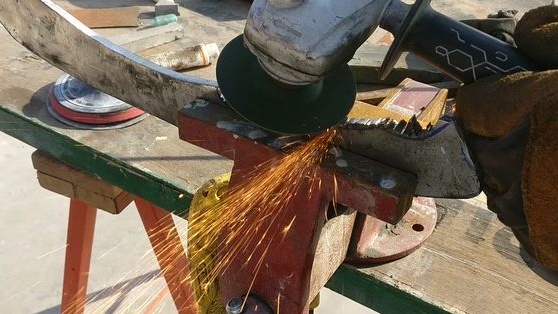
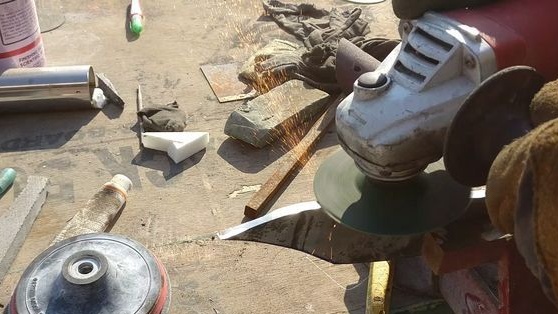
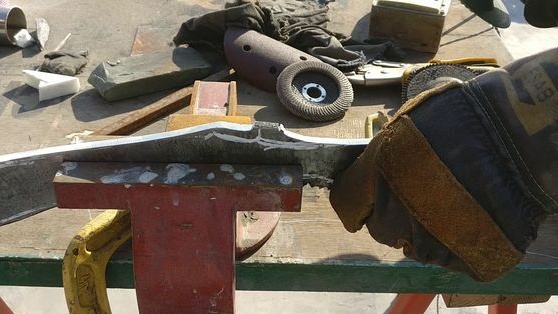
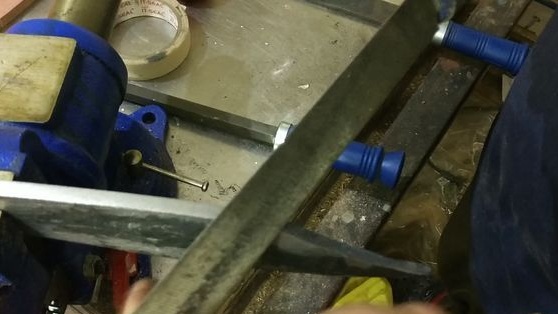
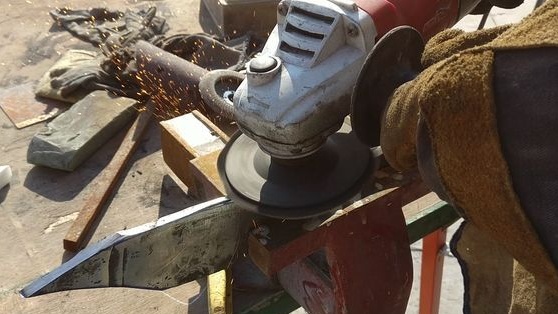
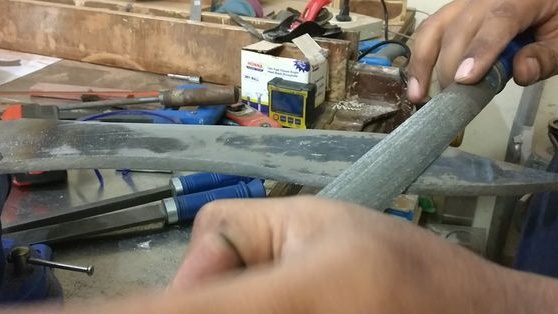
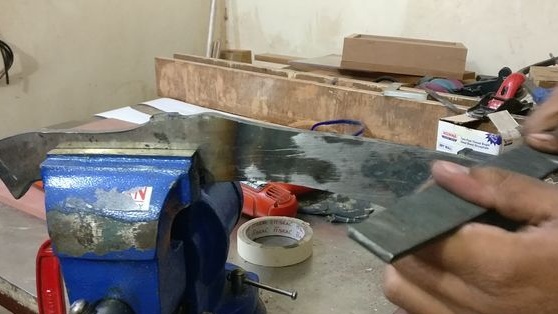
Step Five: Labeling
Next, the master needs to identify the processing location. Marker draws unworkable areas.
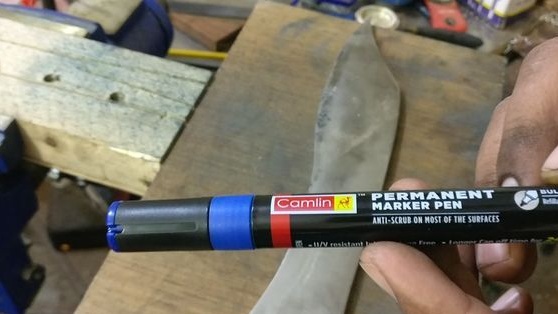
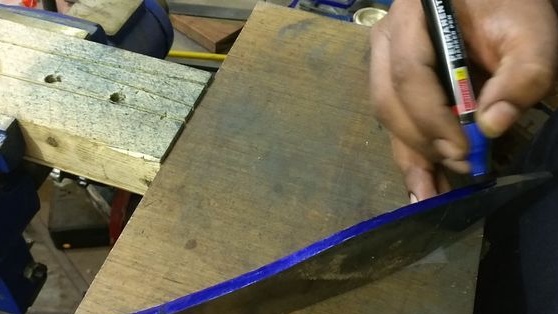
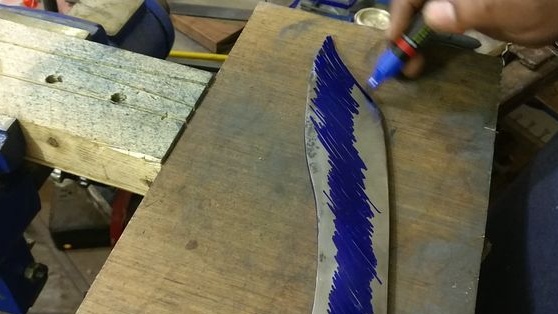
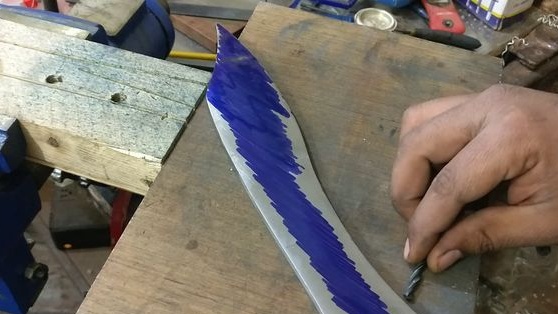
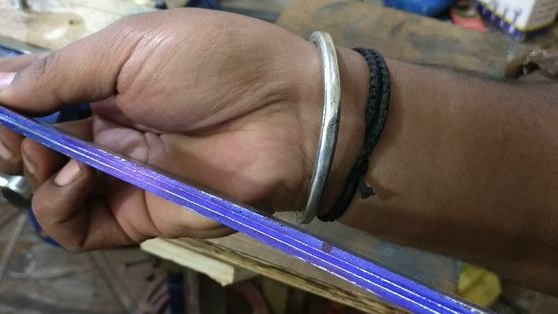
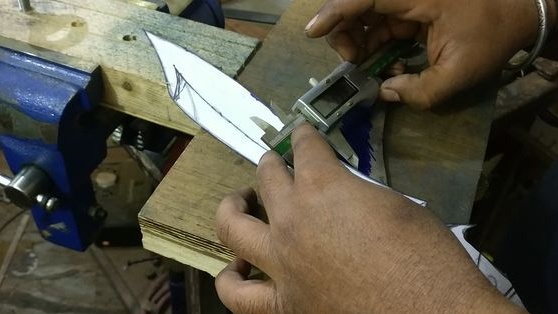
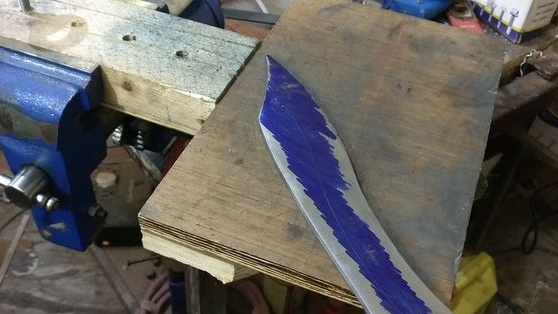
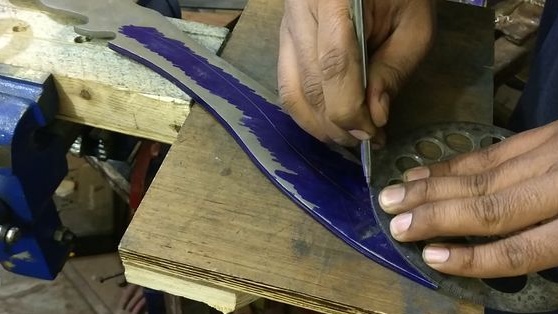
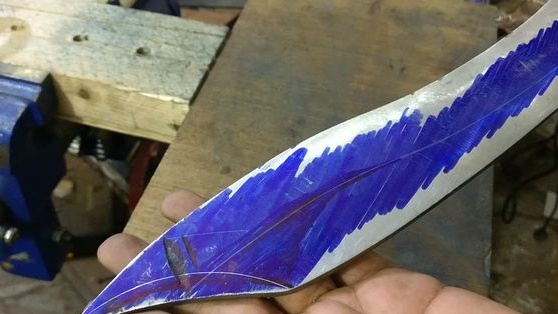
Step Six: The Faces
In order to correctly and evenly bring out the edges of the knife, the master uses a special device. The device allows you to draw faces on both sides with the same angle.
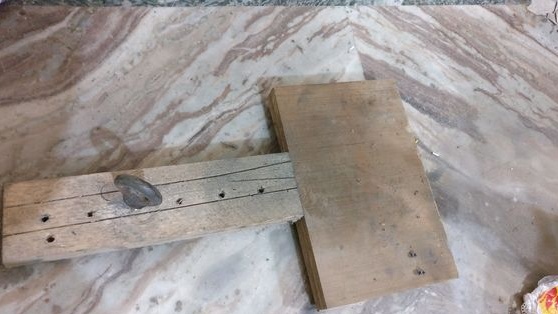
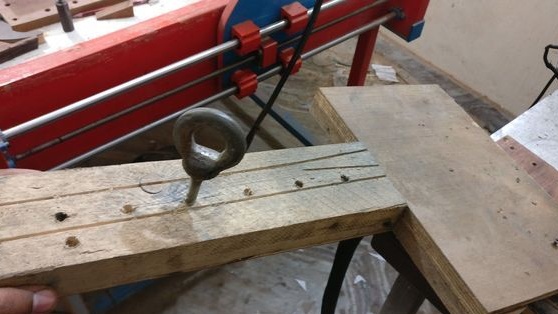
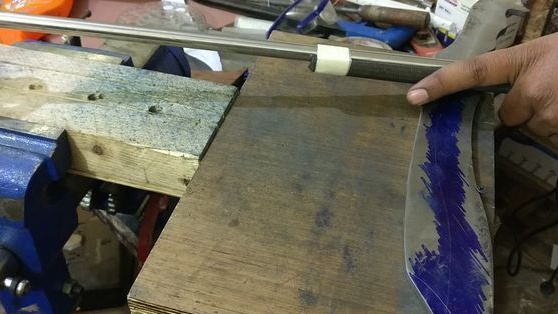
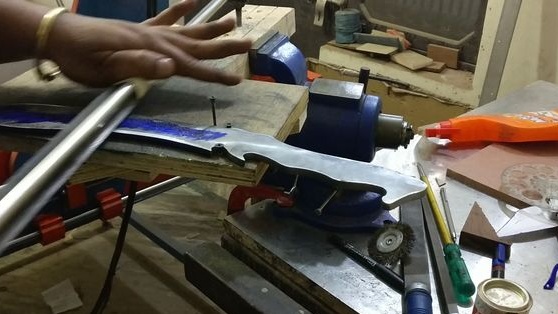
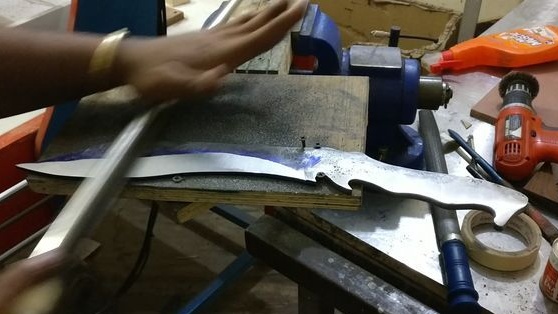
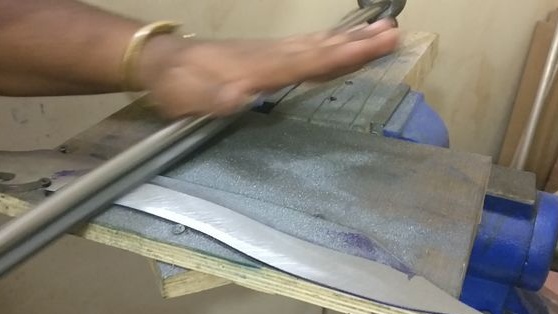
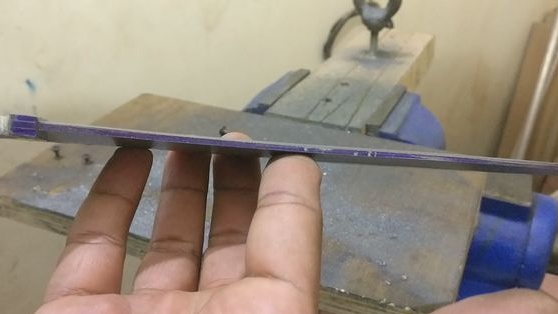
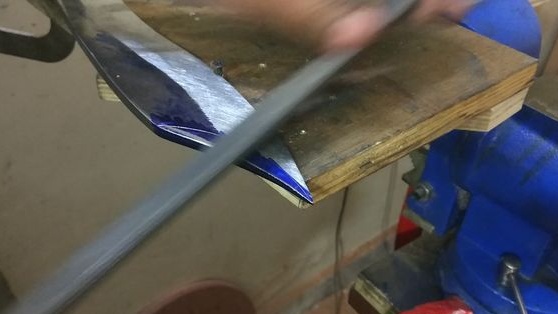
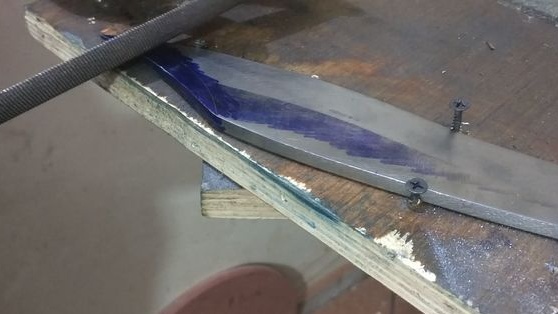
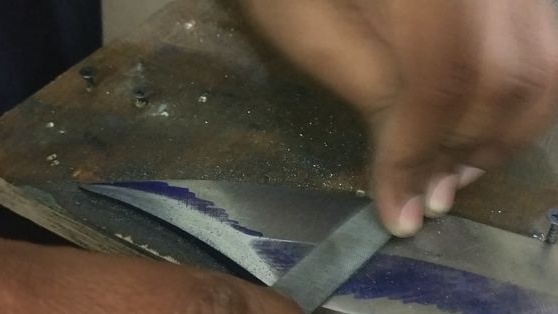
Seventh step: seritor
The master makes the butt of the knife wavy. He does all the work with the help of files.
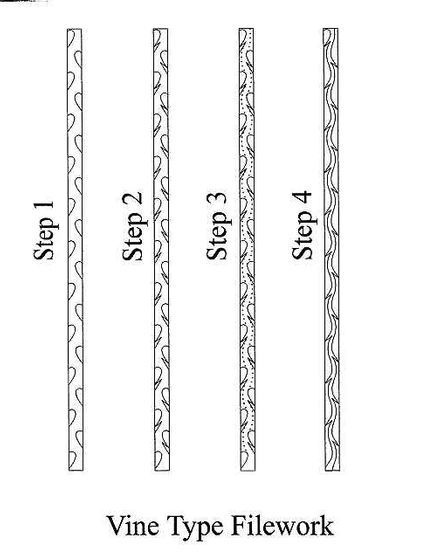
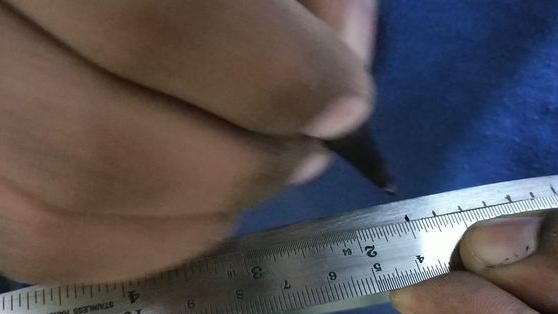
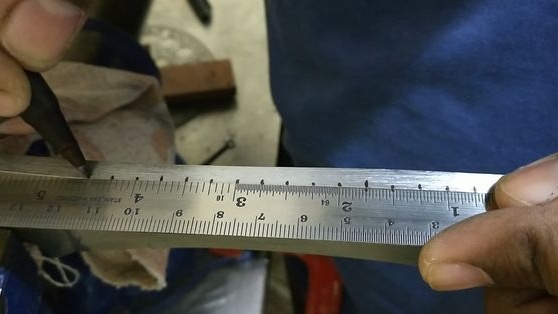
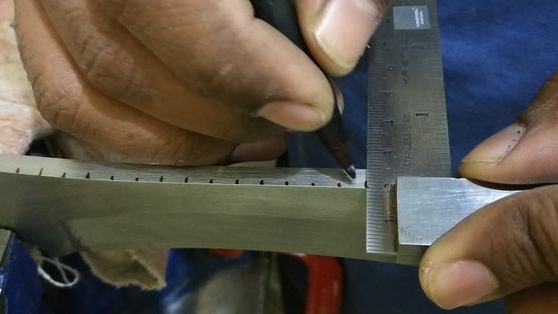
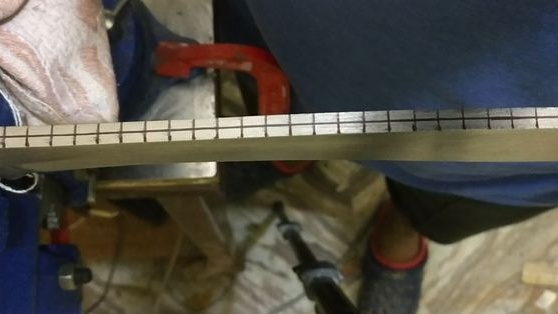
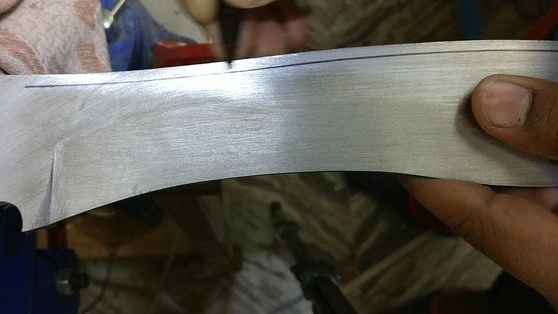

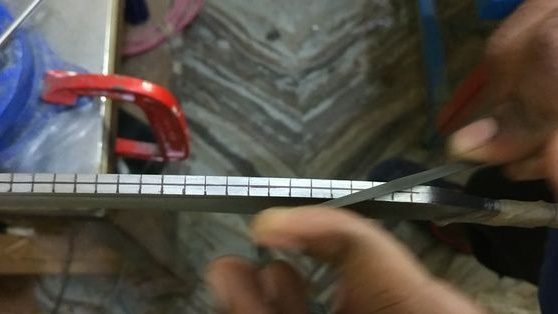
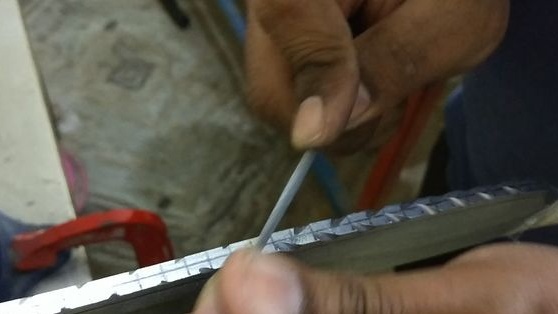
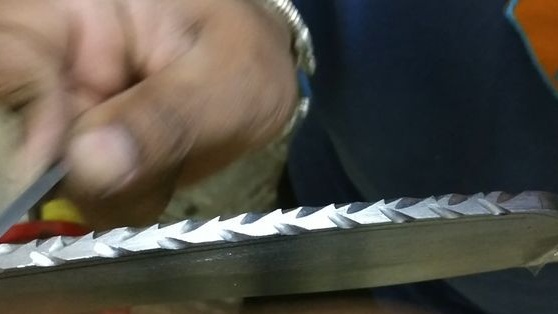
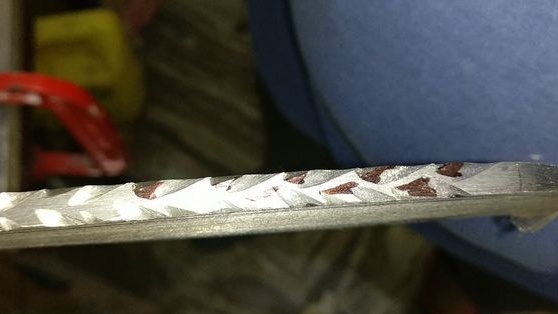
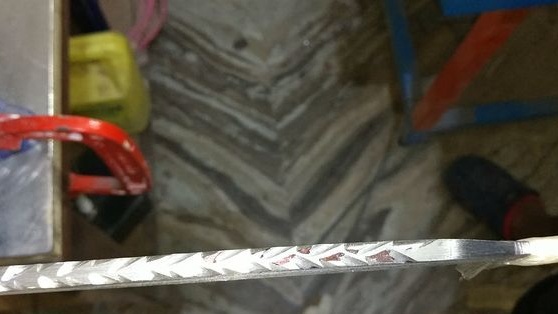
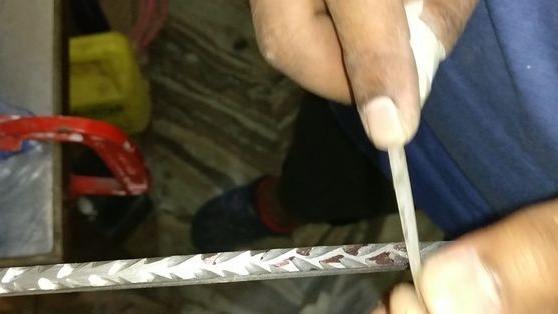
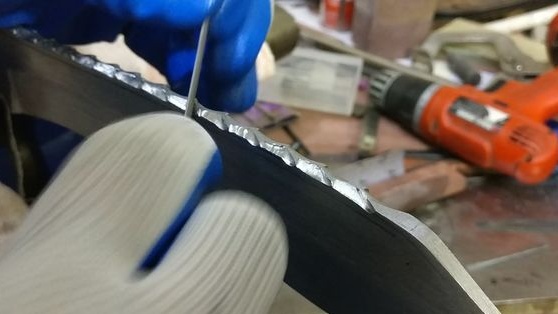
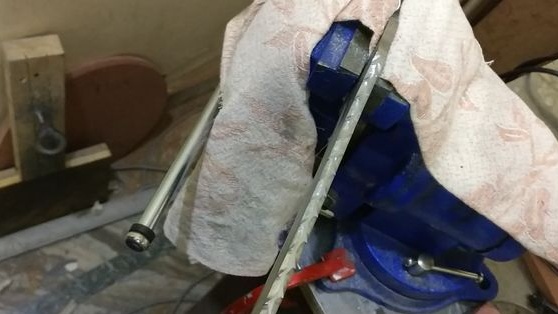
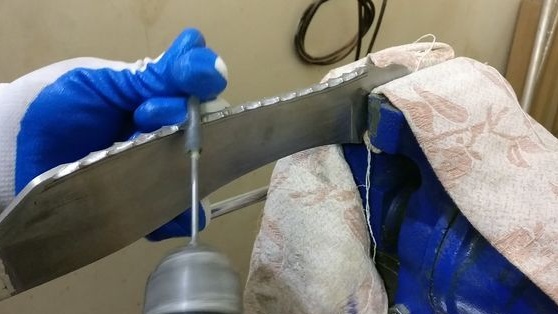
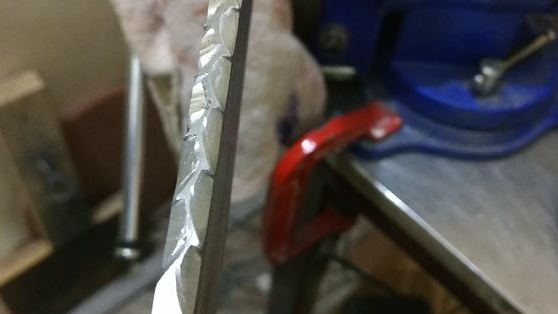
Step Eight: Pen
The master makes a pen from different materials. Knead epoxy glue. Pouring over molds. Adds phosphor to forms. After the glue hardens, it takes out of the mold and grinds. Glues pieces of epoxy, wood and mikarta with each other. Brass glues along the edges.
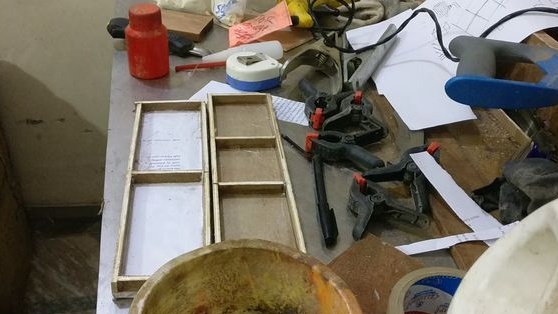
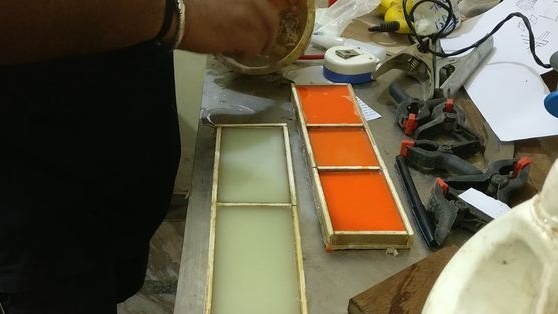
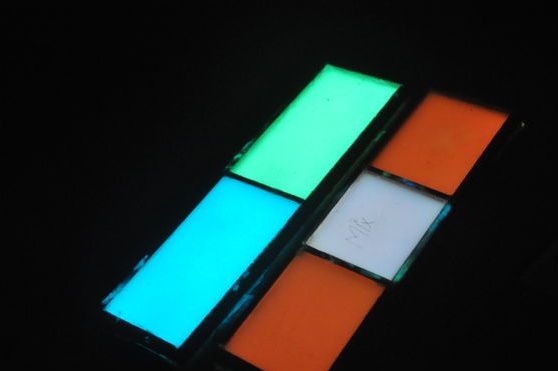
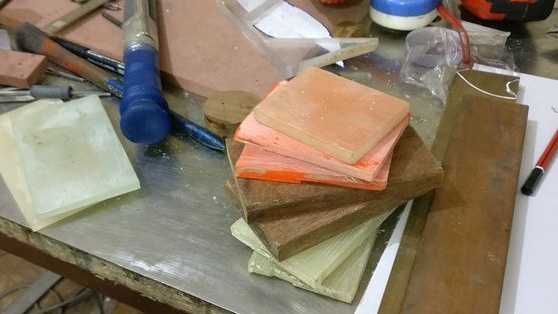
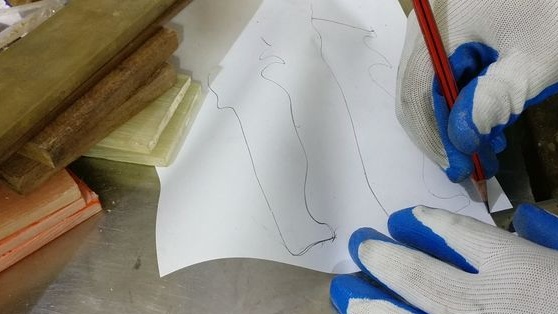
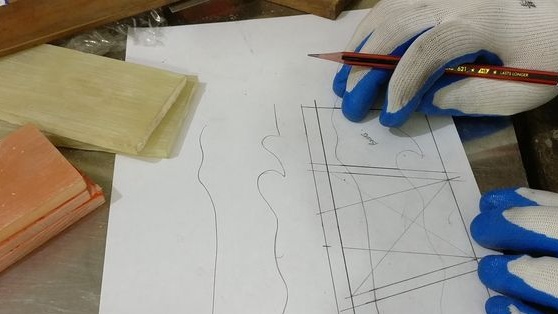
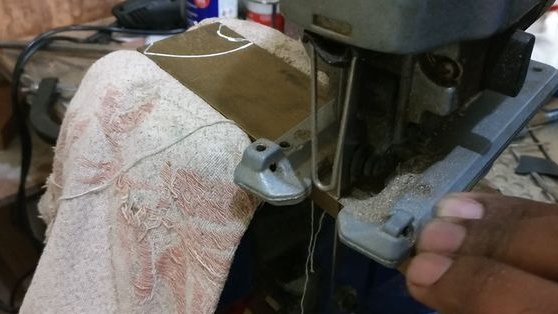
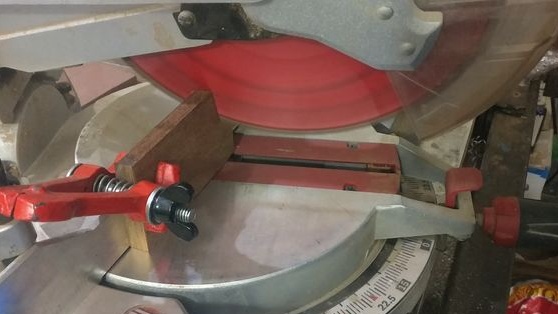
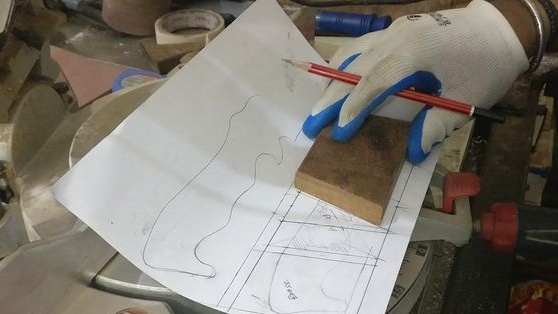
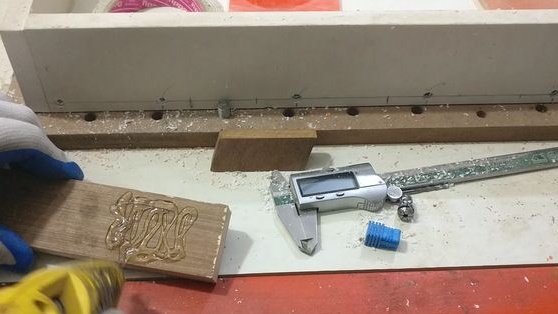
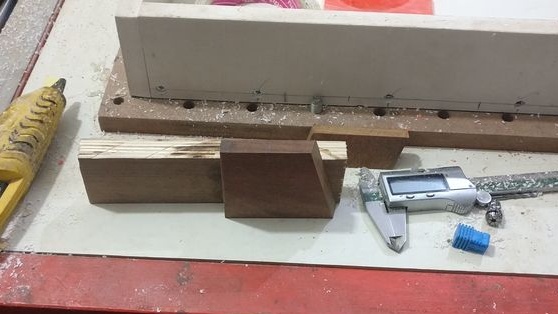
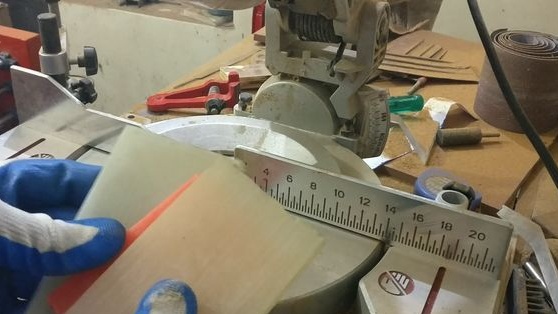
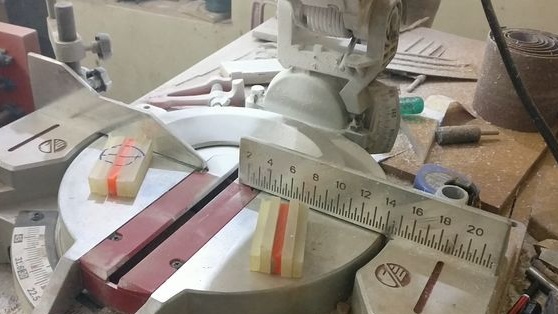
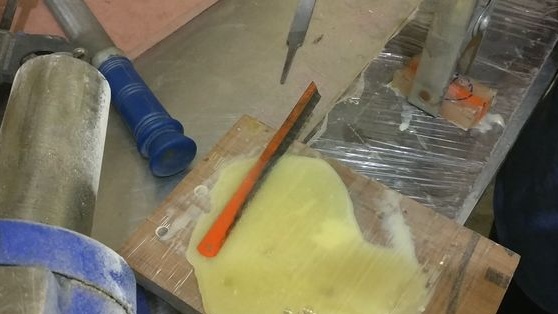
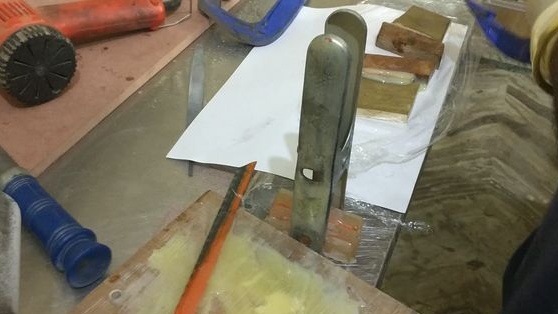
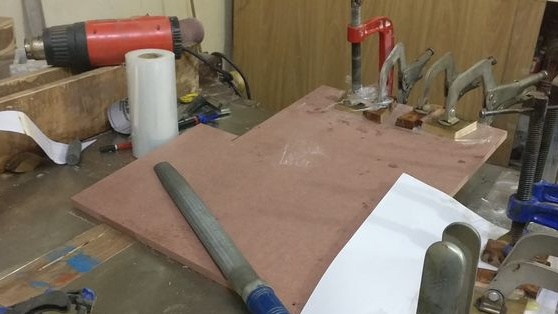
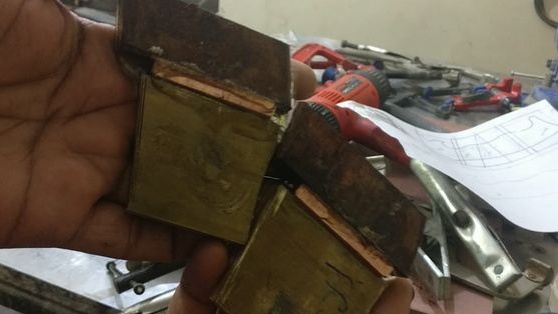
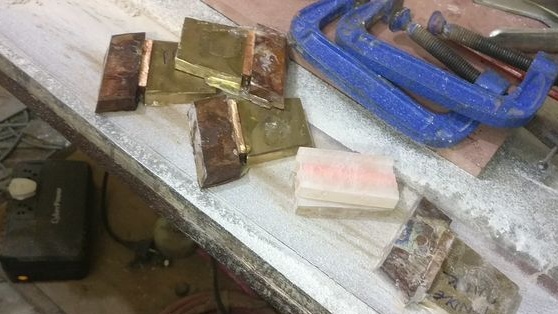
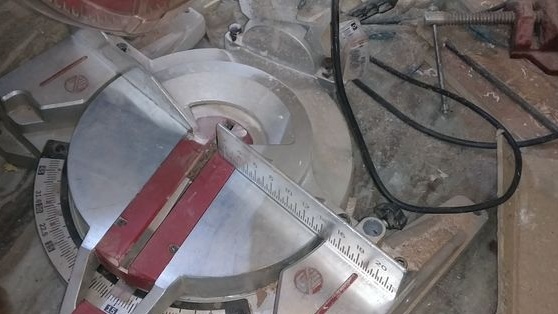
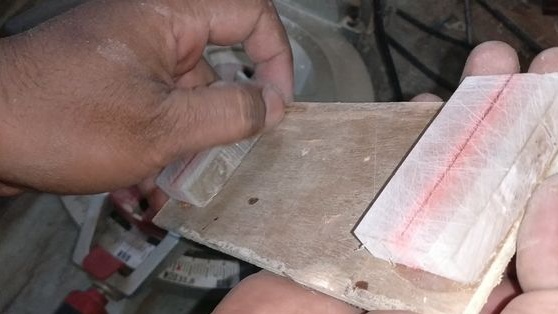
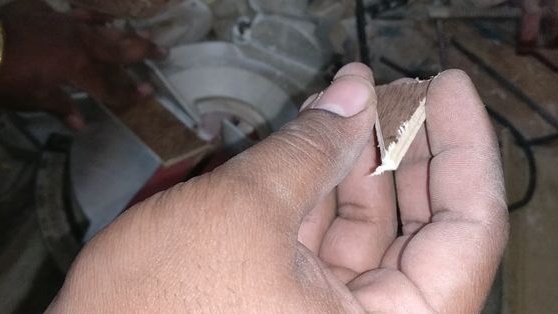
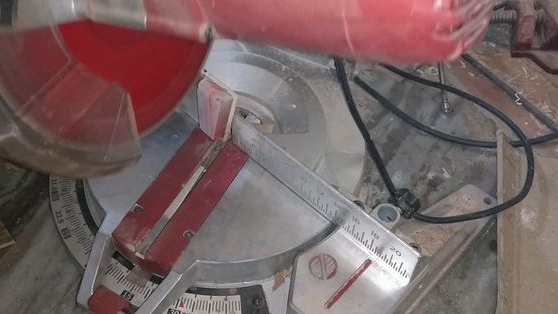
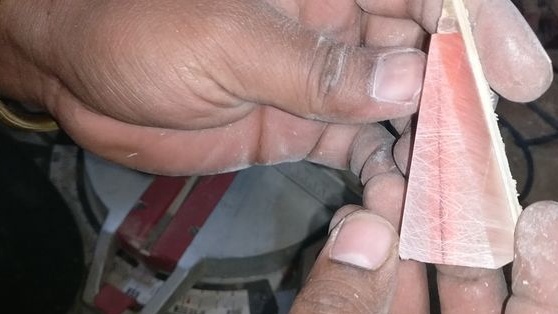
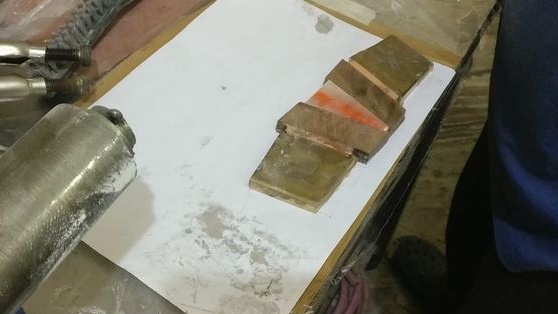
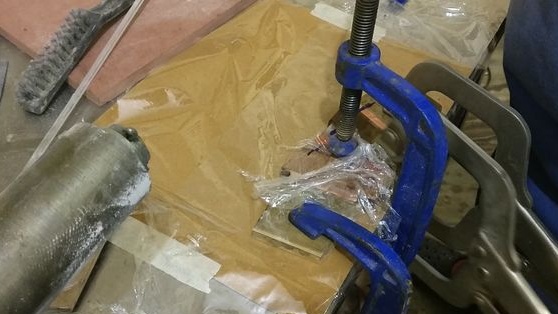
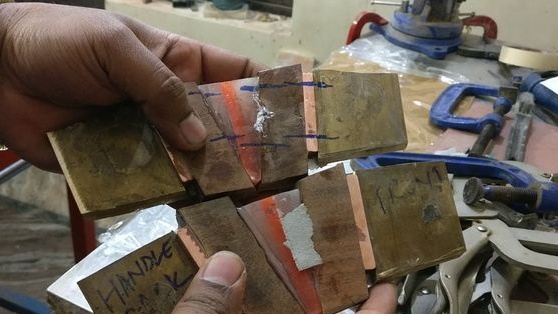
It transfers the contour of the knife handle to the handle blank. Clamps the workpiece in a vice and processes. After processing, drills 4 mm holes for pins in the pads and knife handle. To lighten the weight of the knife, 10 mm holes are drilled throughout the handle.
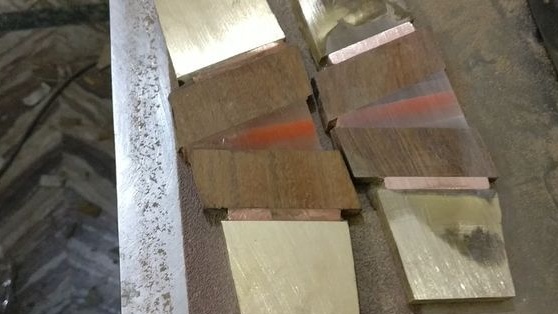
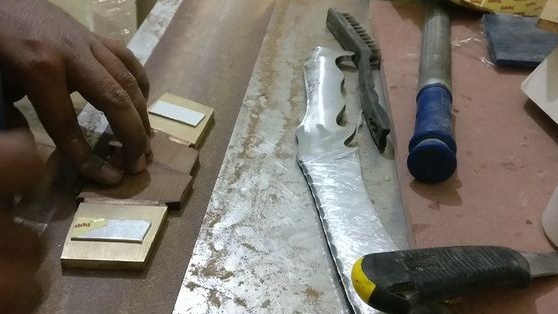
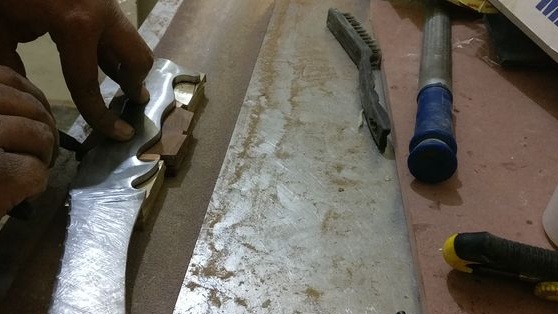
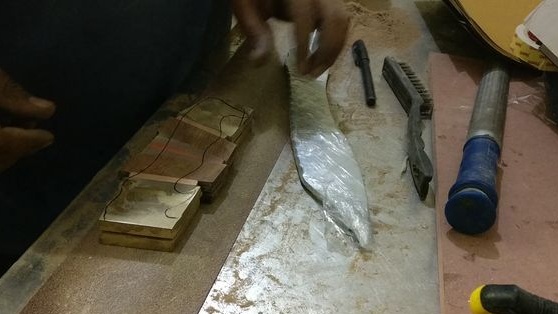
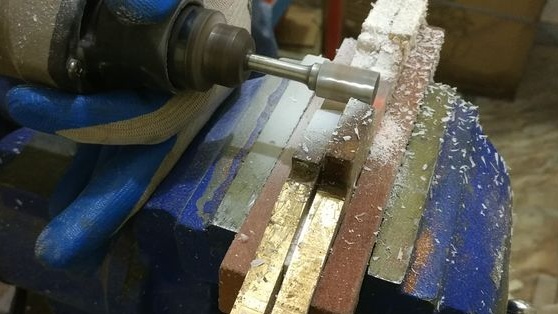
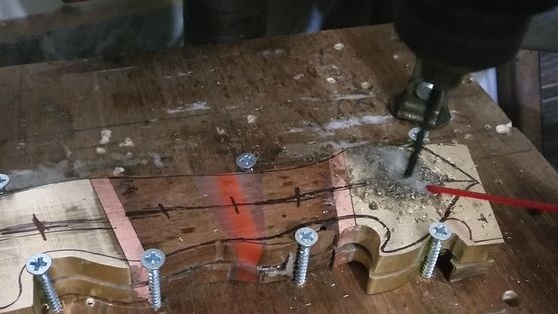
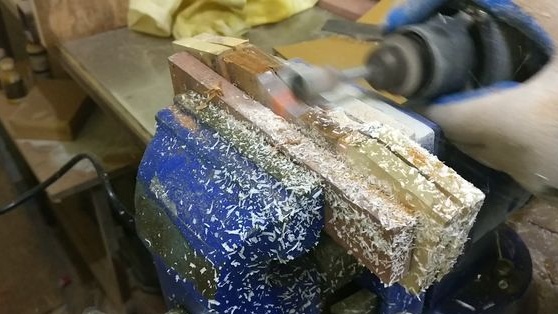
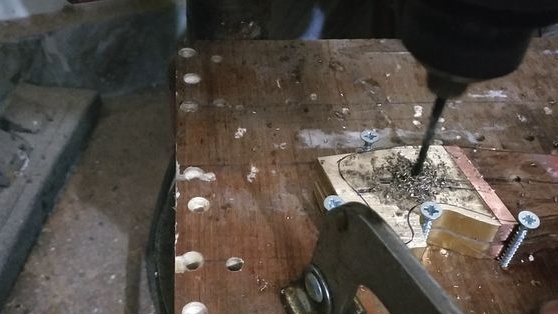
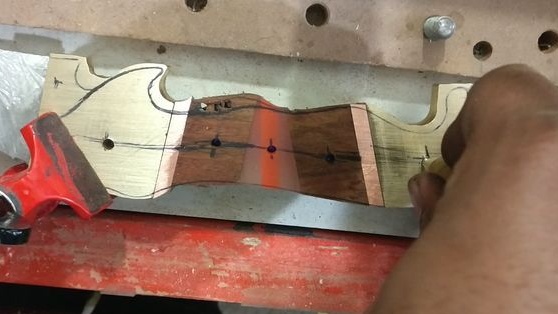
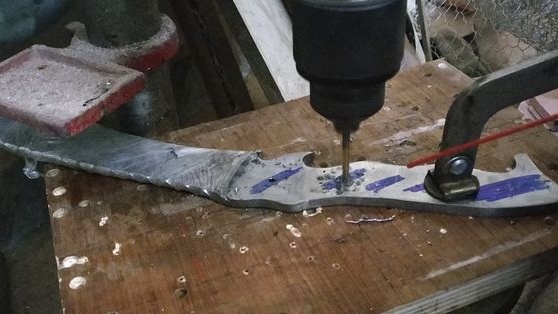
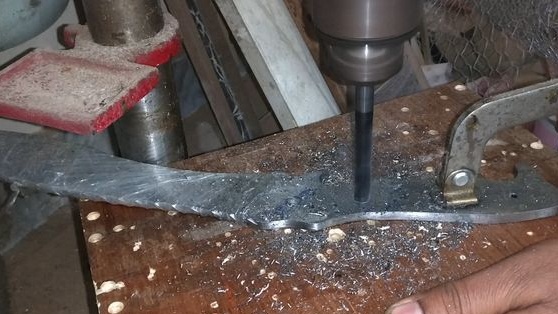
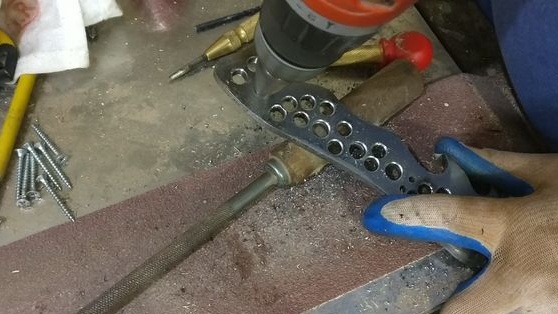
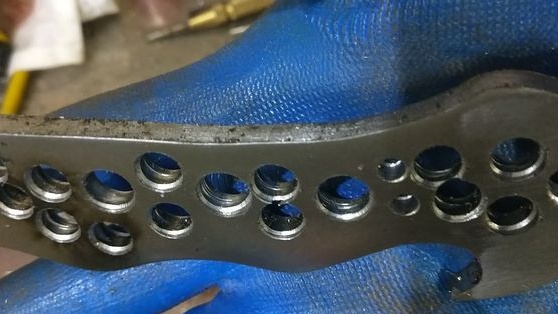
Step Nine: Hardening
The next step is the hardening of the knife. The master determines the degree of heating using a magnet. After heating, lower the knife into the oil. First, the butt drops, then the blade. After quenching produces a vacation. Heats the knife for 45 minutes and allows to cool in the air.
Step Ten: Grinding
After cooling, the knife polishes it. It uses sandpaper with grain from 60 at the beginning, to 1000 at the end of grinding. The last stages of grinding are carried out with water. Then polishes with paste.
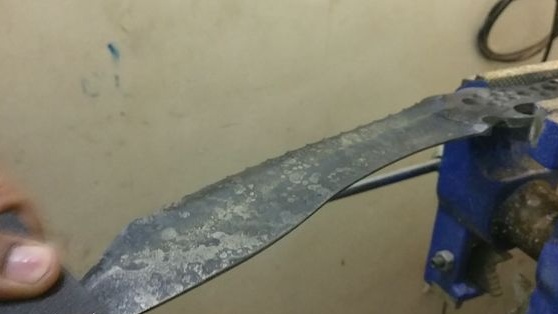
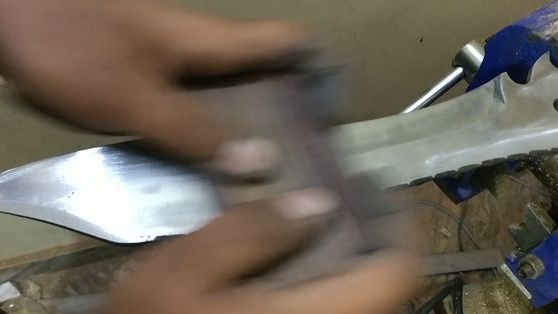
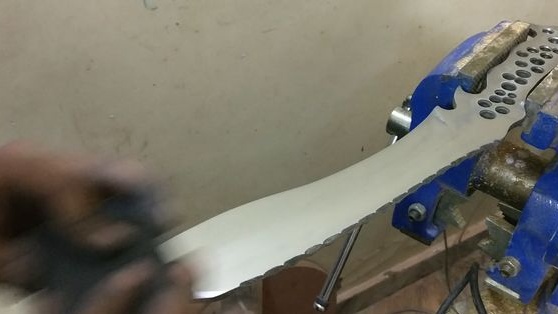
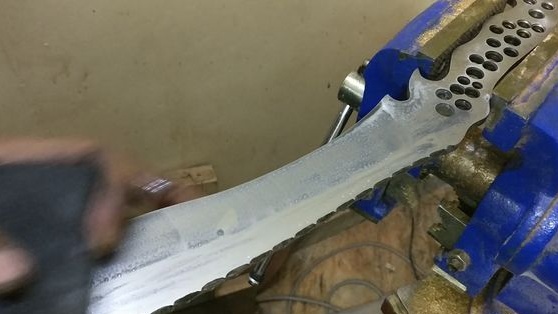
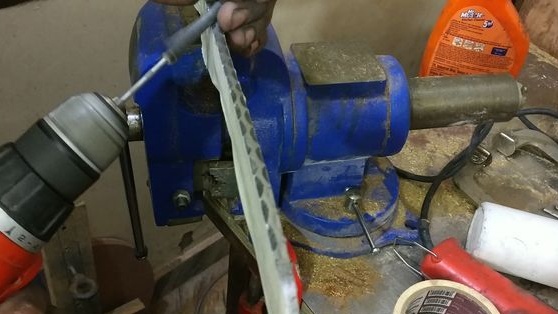
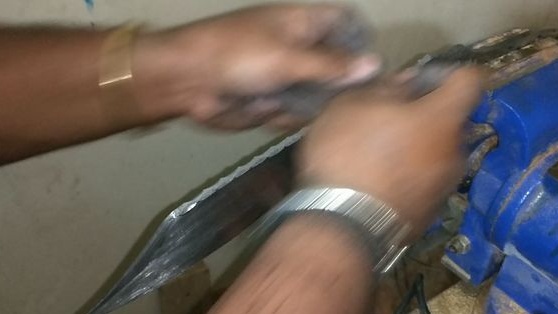
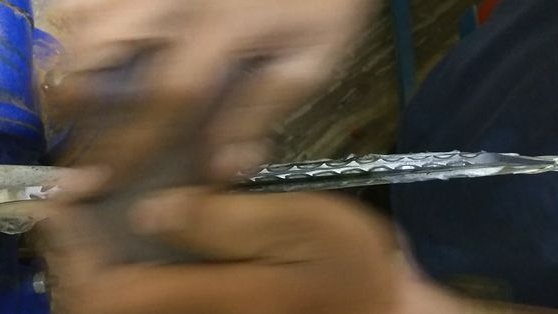
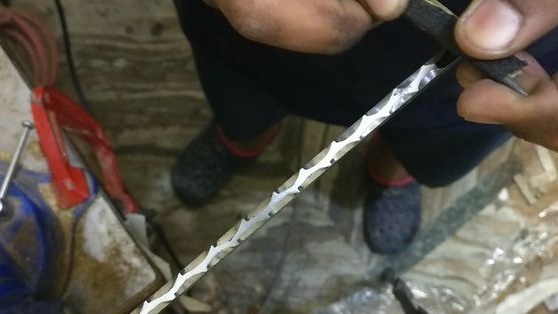
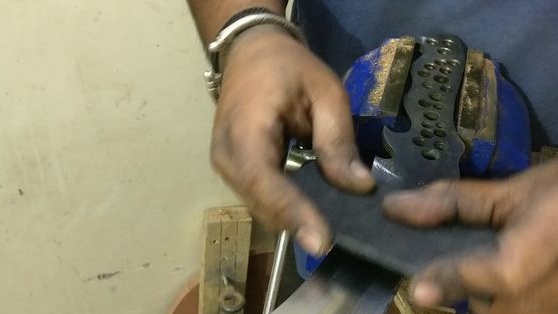
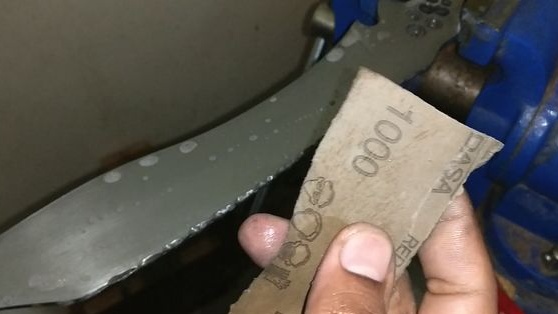
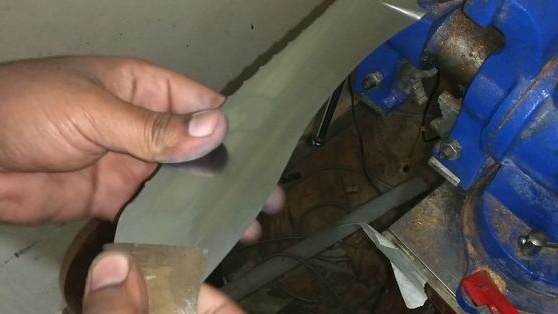
Step Eleven: Installing the Handle
To lighten the weight in brass, drill recesses from the back. Sticks on Micartu linings. It processes the edges of the linings to achieve symmetry. Adhes pads. Glues mosaic pins.
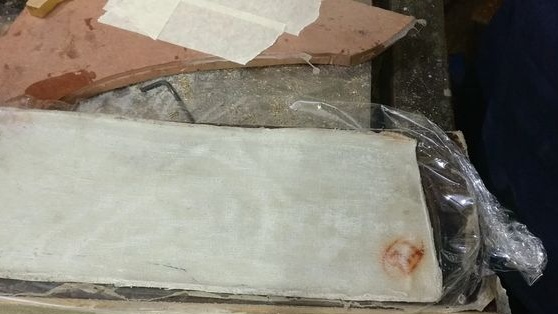
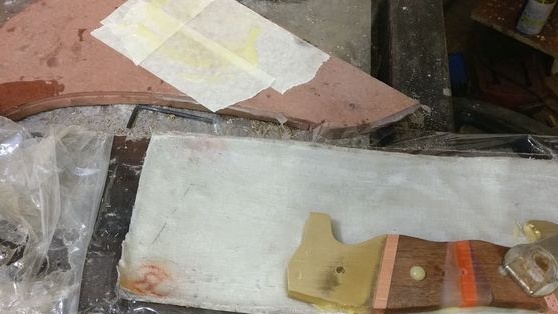
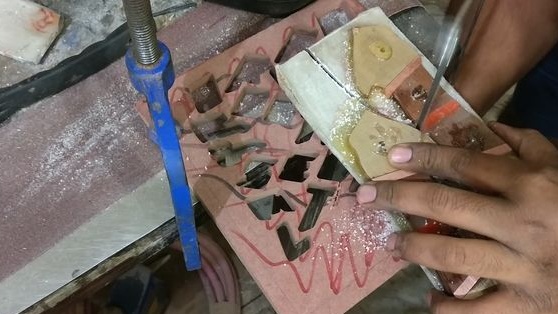
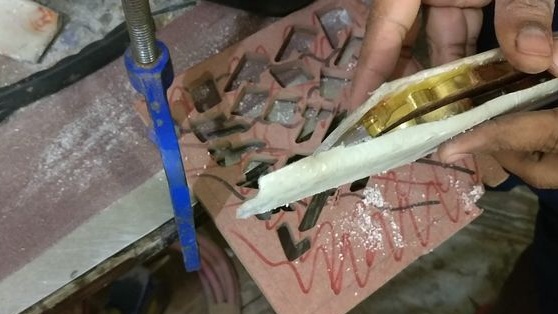
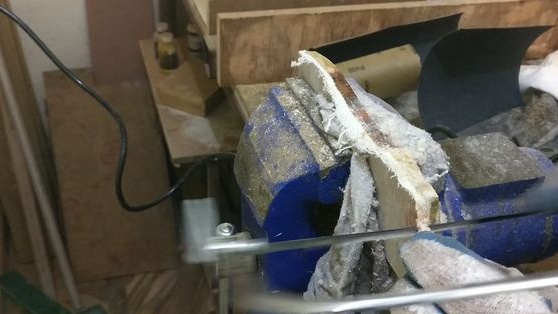
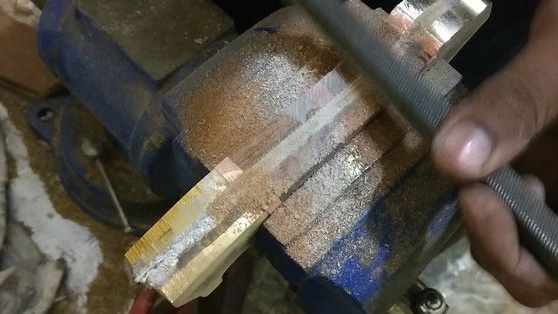
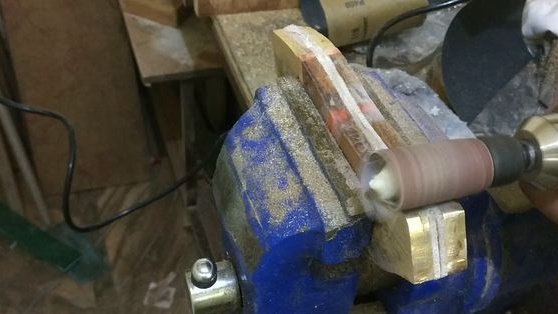
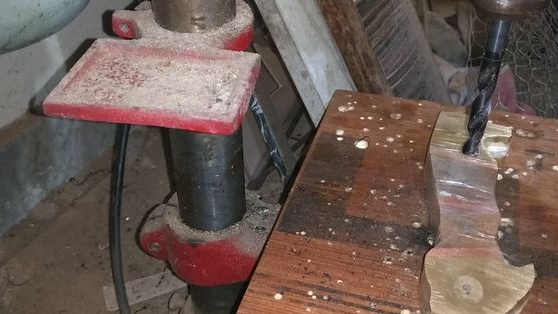
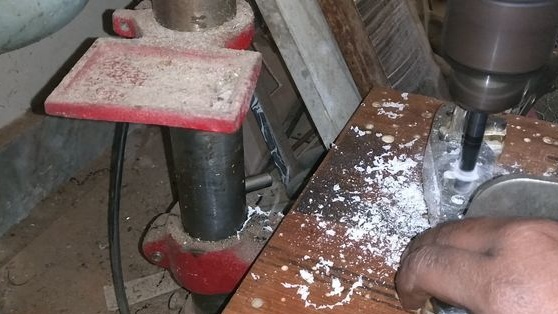
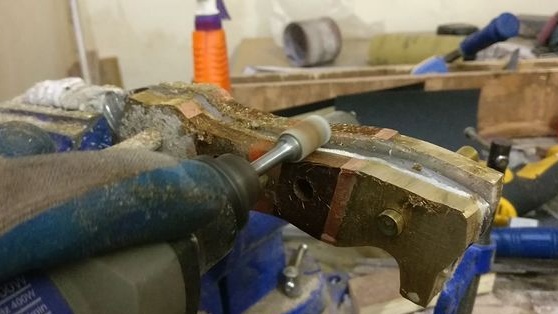
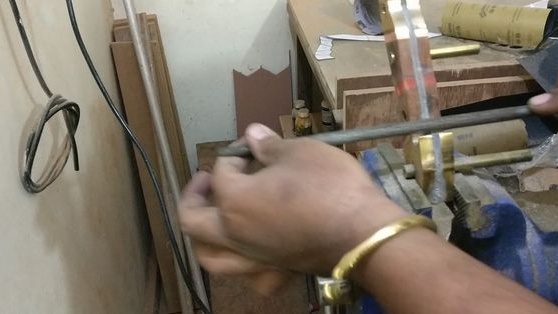
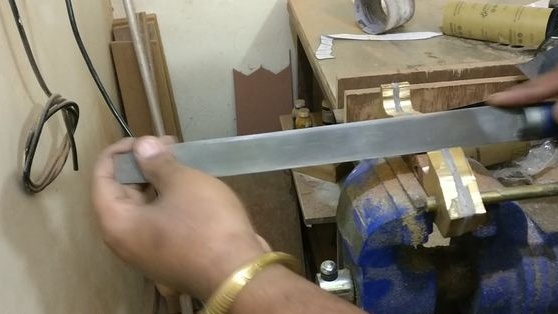
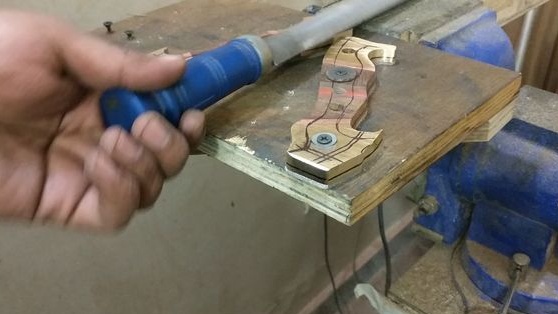
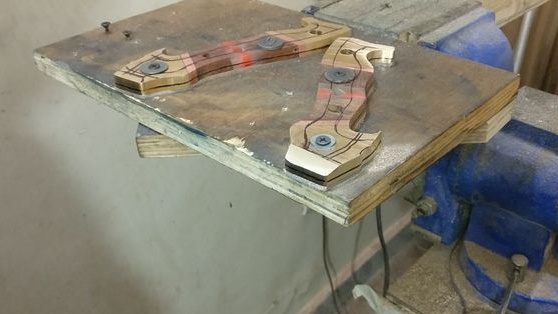
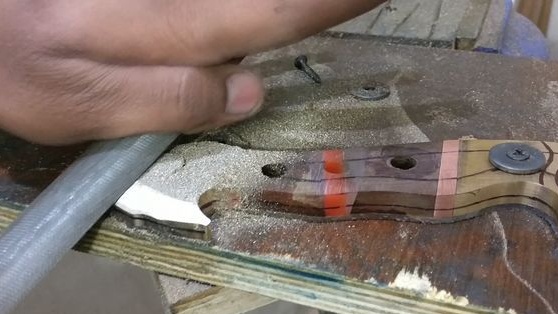
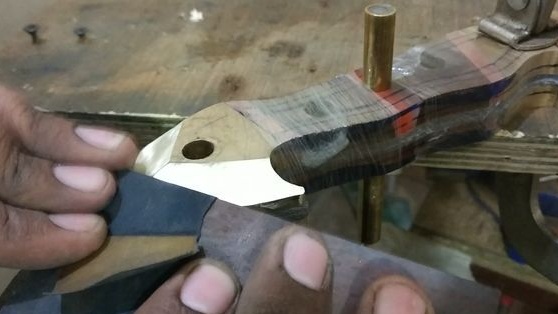
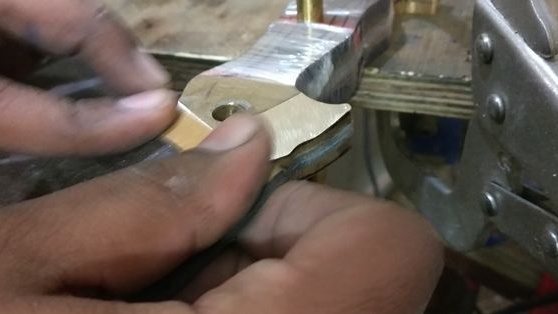
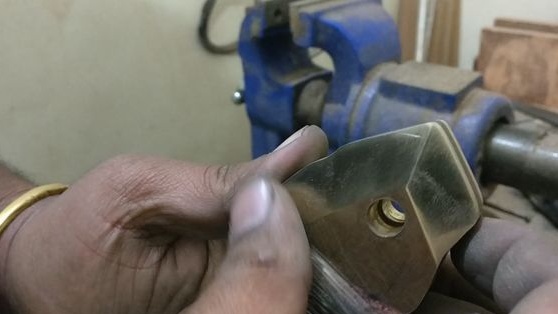
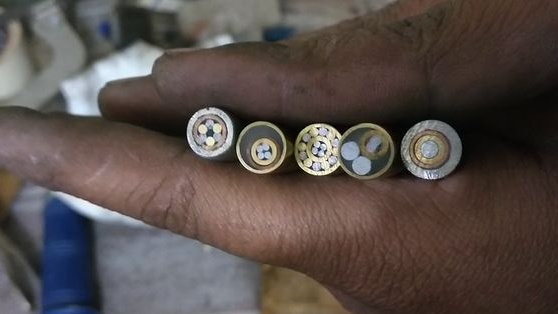
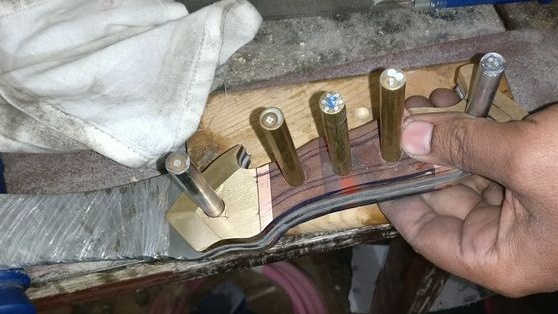
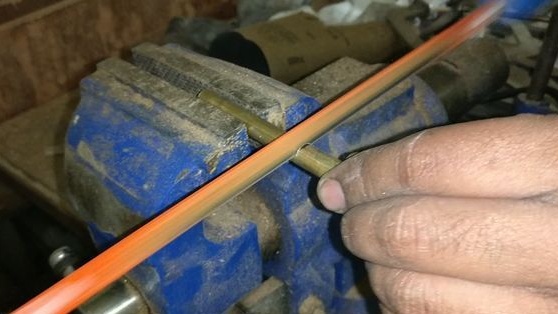
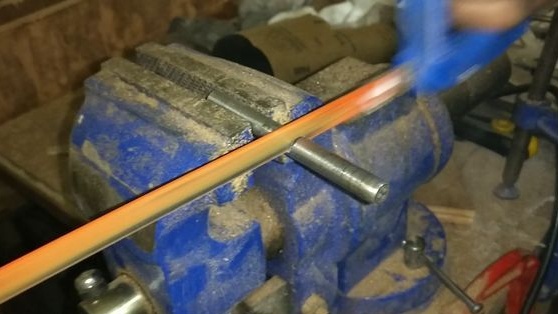
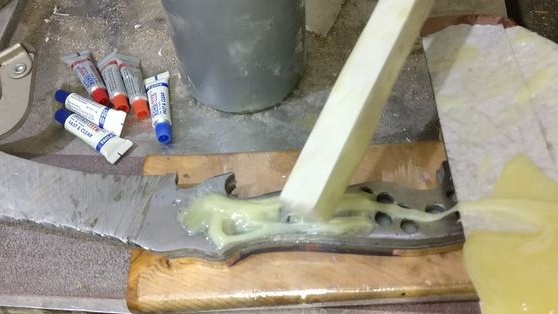
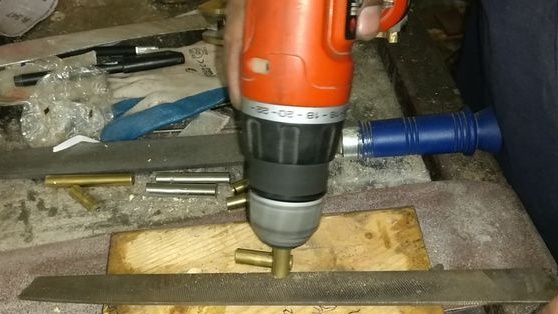
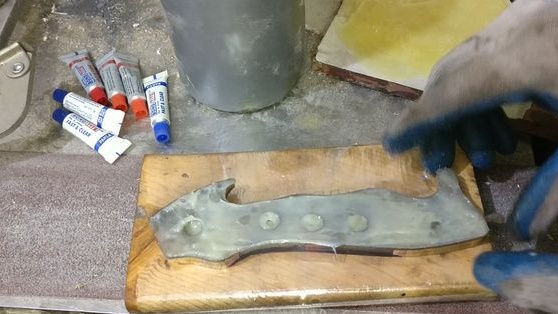
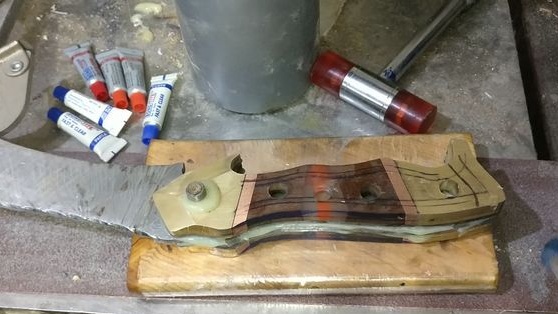
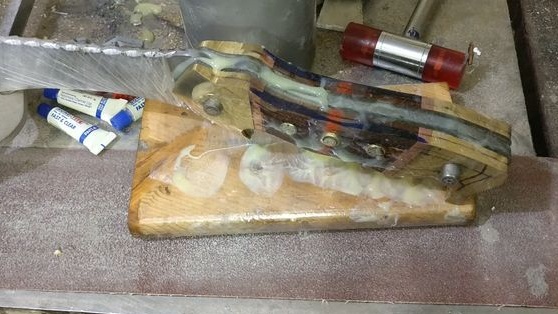

With the help of an angle grinder and a file, it displays the shape of the handle. Grinds.
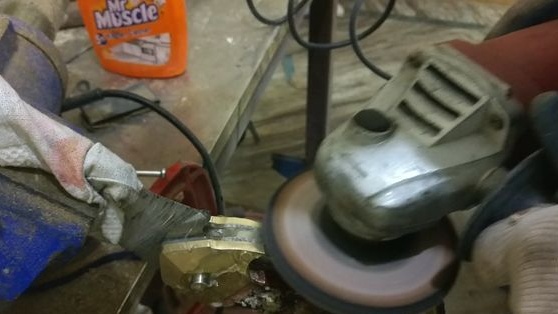
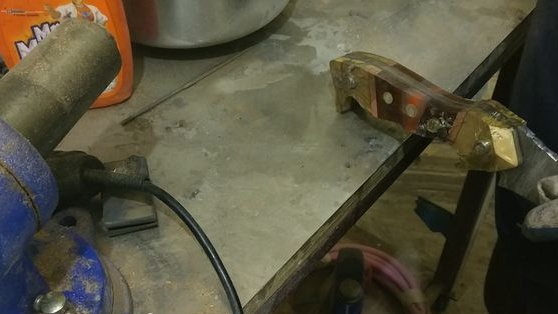
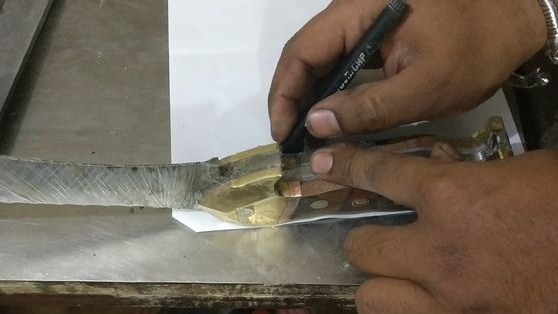
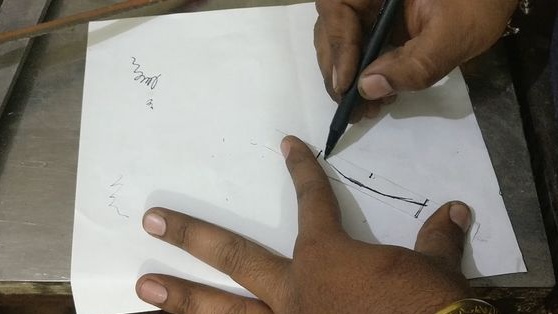
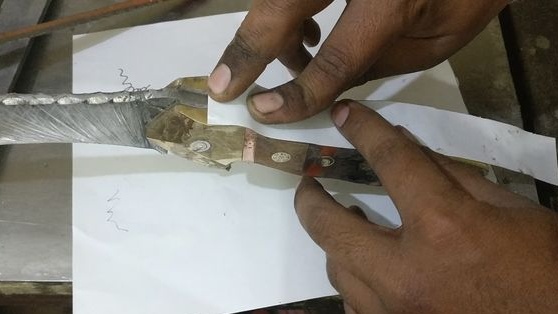
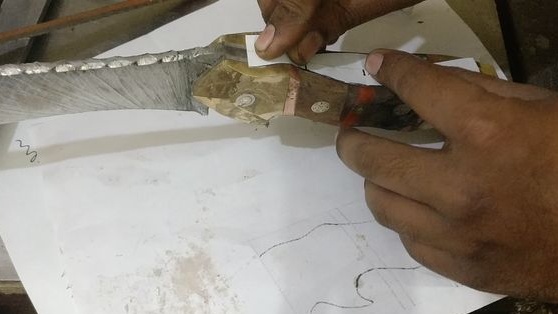
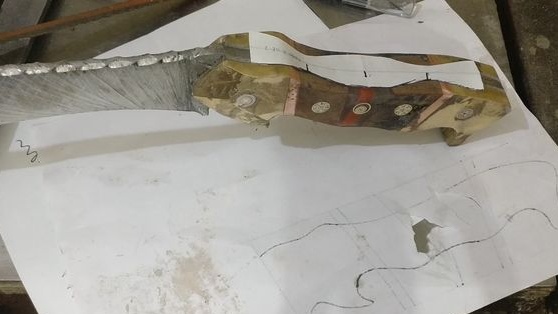
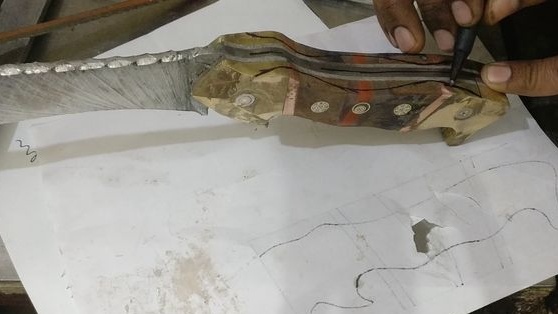
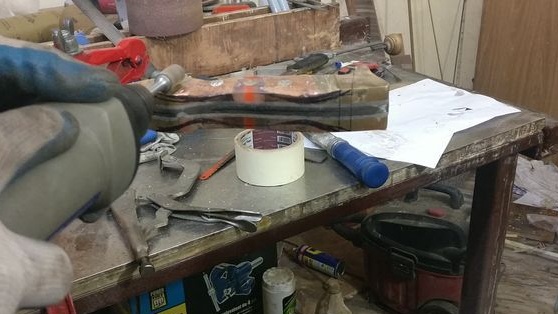
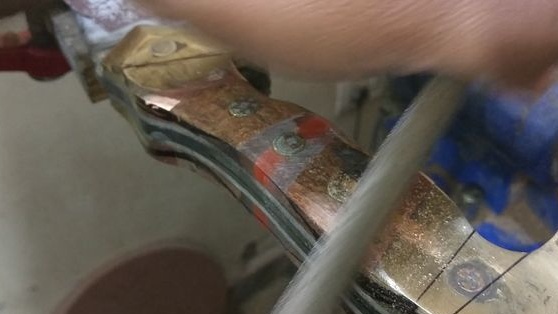
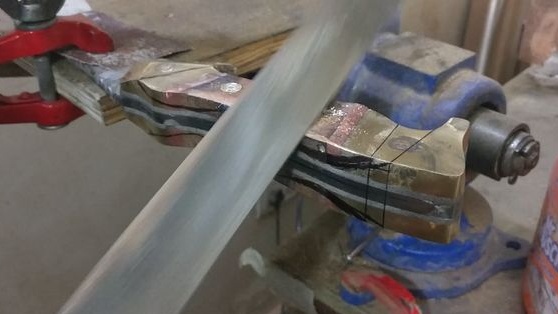
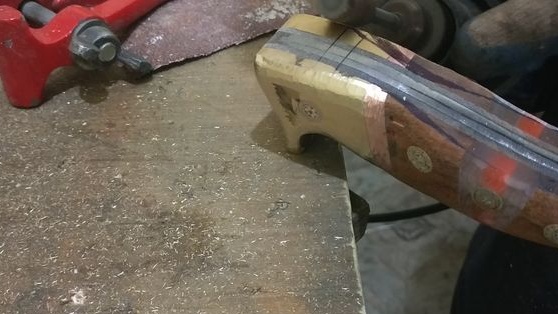
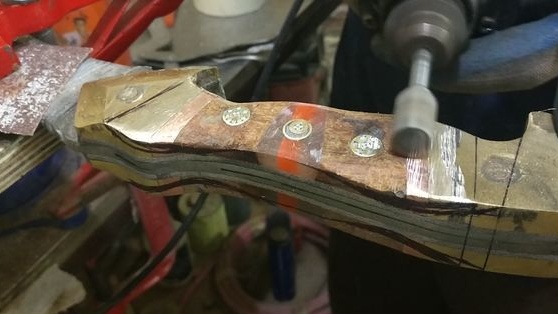
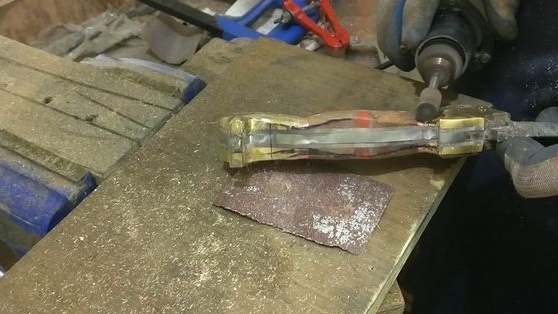
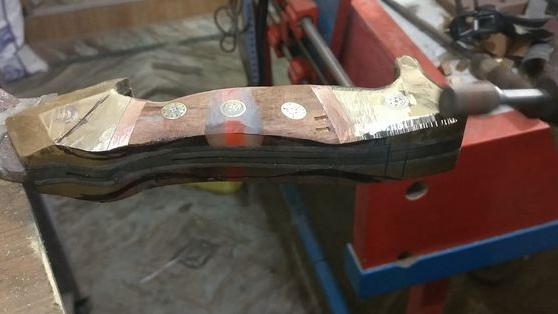
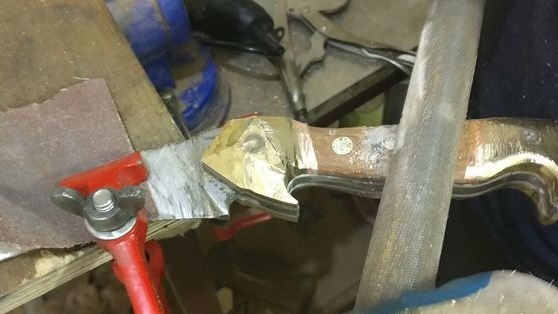
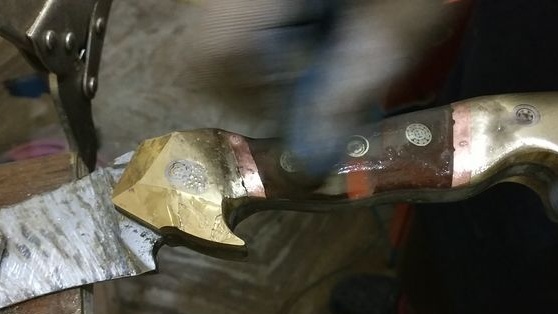
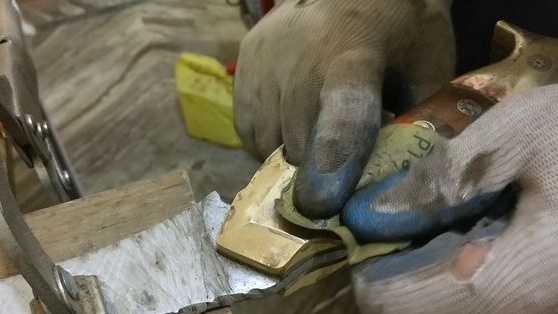
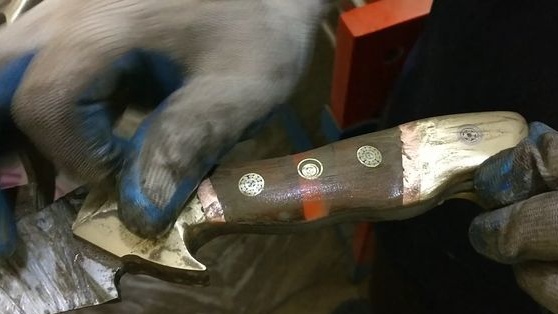
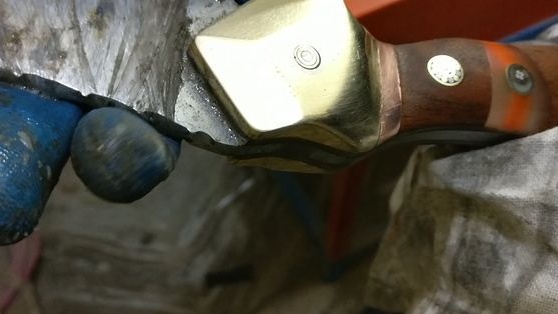
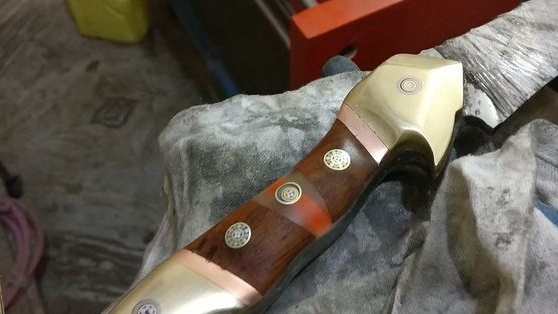
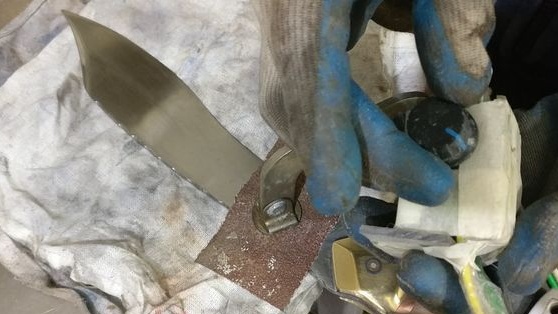
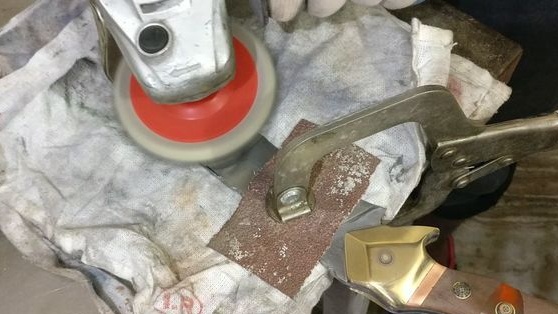
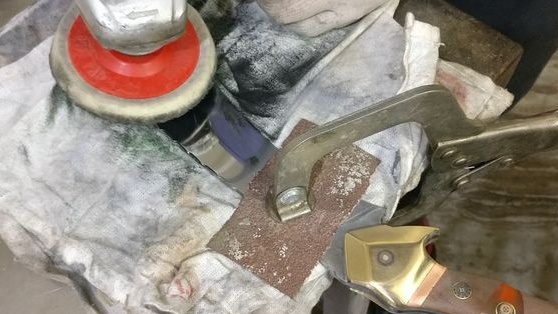
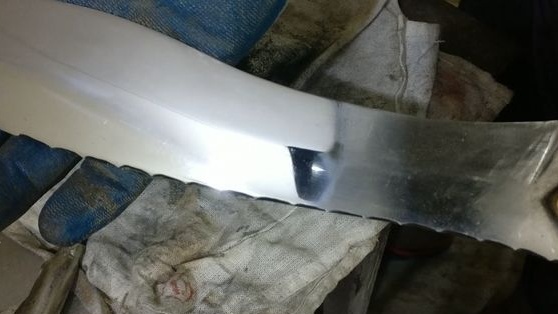
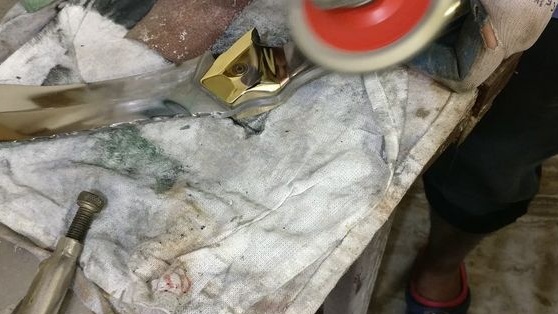
Step Twelve: Sharpening
Pastes over a knife blade with masking tape. Sharpening produces on a 800 bar, wet. 10 times one side, 10 the other. And so 15 approaches. Then brings the blade to the leather belt, 30 sets.
The knife is ready.
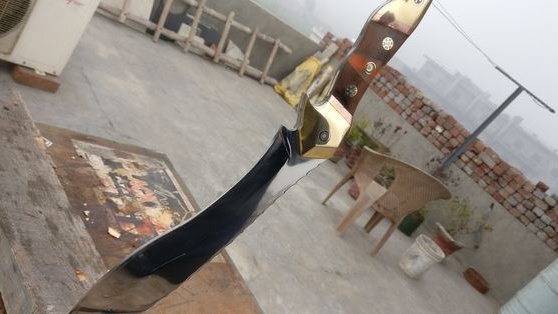
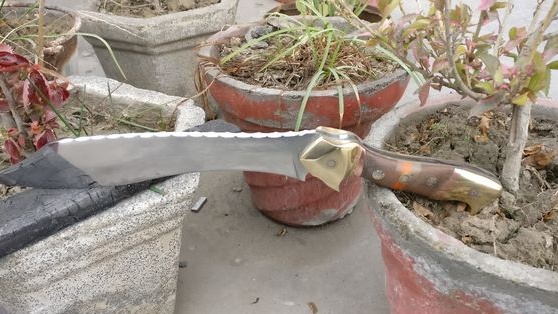
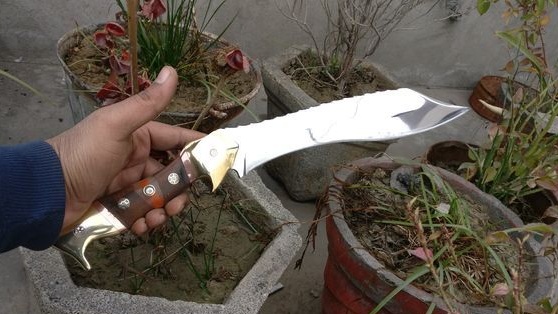
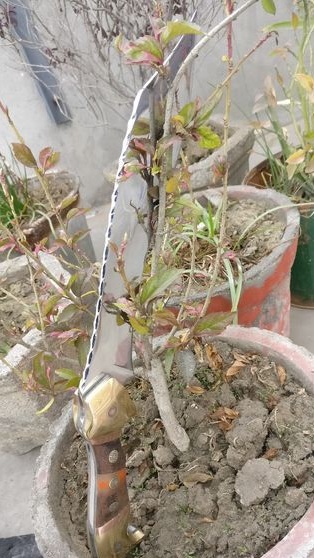
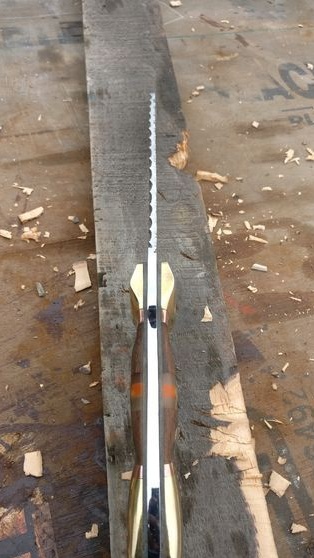
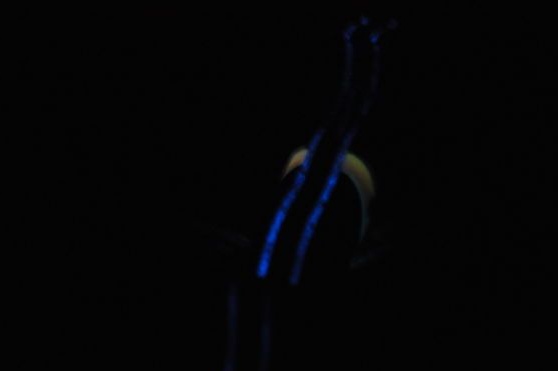
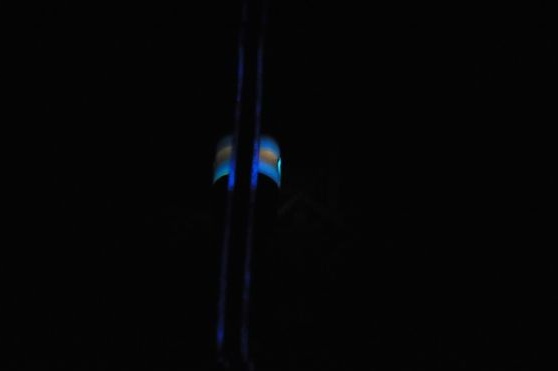