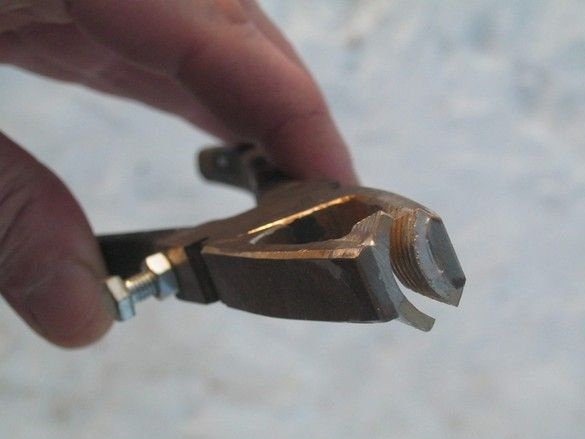
When painting with glass, you can’t do without cutting small elements with curved edges. These can be stained glass elements, works in the “fusing” technique - sintering of colored glass in a special furnace, hot forming of glass.
Glass cutting, both in the case of a straight and in the case of a curved cut, is approximately the same - the first stage, on a clean and dry surface of the glass, a continuous scratch is made from the edge to the edge of the glass in the right place. Faceted diamond or carbide roller glass cutter. The glass surface at the place of scratching is recommended to be lightly greased with kerosene, however, recently glass cutters equipped with a special unit supplying the oil-kerosene mixture from the container in the glass cutter handle directly to the carbide roller have been widely used. In the manner of a ballpoint. Yes, an important point - when applying a scratch, a sheet or piece of glass should be kept on a flat, slightly elastic surface. In glass workshops, for this, a table is traditionally used, the cover of which is trimmed with dense felt. At home with infrequent work, you can use a thick layer of newspapers on a flat surface.
So, a scratch on the glass is applied, an important and very crucial moment comes - breaking the glass. Often, when cutting glass of more or less significant thickness, by lightly tapping on the back of the glass, opposite to a scratch, a crack is formed.
There are also special tools that allow you to exert a "break" force, exactly in a specific place. For example, a ceramic tile breaker, which is part of a portable tile cutter. The ceramic tile is placed on a special edge of the breaker, opposite to the scratches made by the carbide roller, a special emphasis equipped with a lever for greater effort, presses on the surface of the tile, on both sides of the cut - crack! It is done.
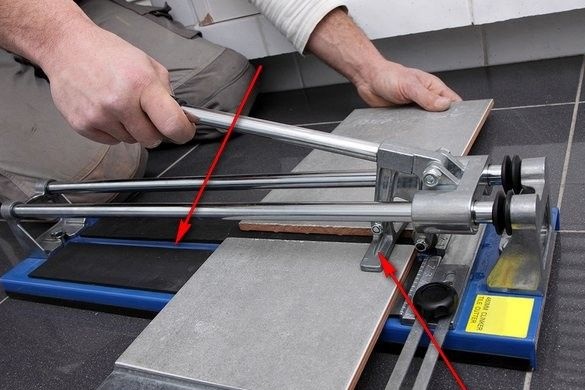
There is also a miniature, pocket-sized version of such a cutting-breaker. Designed for cutting ceramic tiles. It has all the features of an “adult” version - a carbide cutting wheel, a breaker. The cost and ease of use are much lower.
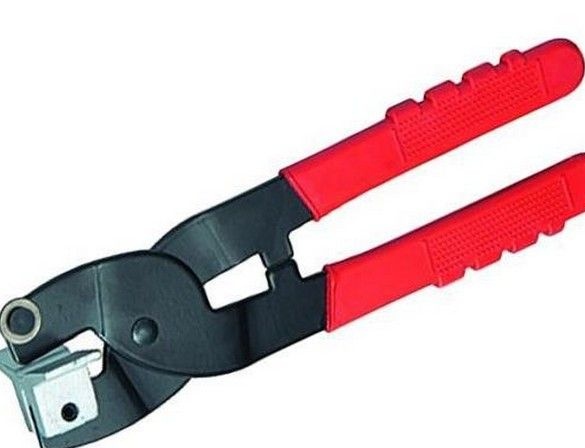
It can be said a prototype.
Let's move on to more highly specialized tools.It is for breaking glass. In the second stage of cutting, a separate glass cutter is used to scratch.
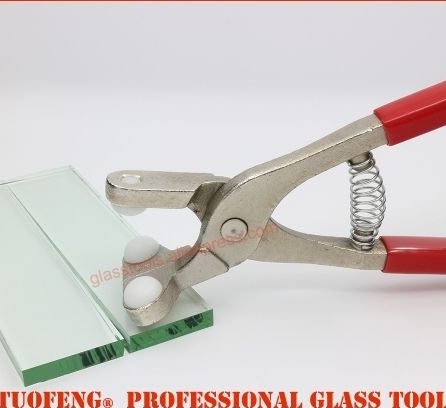
A simple breaker for thick, "display" glass. Powerful design, the stops are spaced quite widely, they are special "navels" made of plastic, it seems, interchangeable. The handles are spring-loaded and independently return to the fully open position. There is no limiter for breaking depth.
Somewhat complicated crackers for thick glass.
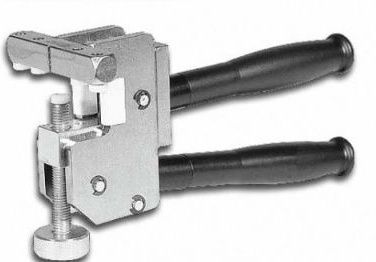
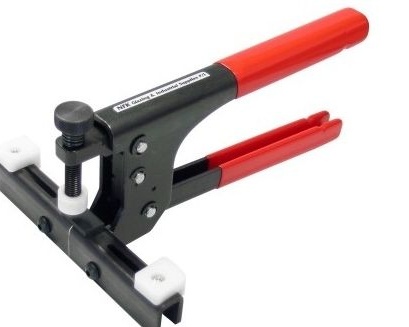
Arranged, slightly differently, the main difference is the lever system in the hinge assembly, which allows to reduce the required effort on the handles - in the questionnaire when entering the glass cutters, you can omit the column "physical training". They cost more than simple, more than an order of magnitude.
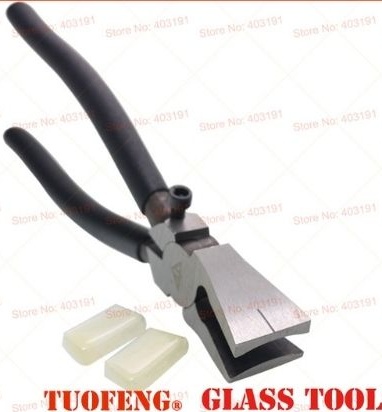
And finally, the most suitable for non-thick (3 mm thick) colored stained glass, a variant of the breaker. Elegant design that looks a lot like pliers. The application of multidirectional force is ensured by the design of the jaws - they are somewhat wider than the usual and curved shape. The tool, unlike the colleague above, does not have a return spring, but is equipped with a depth-of-break adjuster. This is to break the glass, and not crush it into dust. The set includes silicone caps on the sponges so that the iron does not rattle against the glass and does not leave scratches. The caps, according to the reviews of stained glass windows, are frayed quite quickly, instead of them the lips are not thickly wrapped with adhesive tape, paper tape. They also do not work for long, but they are inexpensive and easy to replace. There is a “sight” on the upper sponge.
In domestic, especially metropolitan, stores, such a tool is, not to say, cheap. Inspired by the manufacturer glass nippers from old pliers, I decided to repeat this experience - the breaker design is not sophisticated. The old pliers are over, it was necessary for "this business" to acquire new, inexpensive.
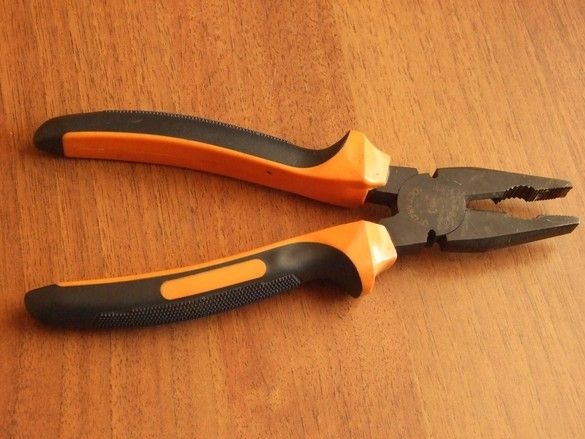
Despite the moderate cost, the pliers turned out to be quite good and for some time they performed their direct, graspingly biting duties. But the time came for the glass, the materials were collected, the tools, mainly also, needed a breaker and was even found on the beloved and dear Ali Express. By the way, at a very affordable price, we must pay tribute to the descendants of Confucius and Lao Tzu. However, there was no strength to wait more than a month for the parcel to reach our wilderness, I had to tackle the file.
What was used in the work.
Instruments.
A set of bench tools, used an electric grinder, a drilling machine, a small angle grinder (grinder) with corundum disks of different thicknesses. Bench vise. Small gas burner for soldering.
Materials
In addition to experimental pliers, solder and flux for burner soldering, M5 hardware, some bronze glands from a box with "plumbing" rubbish.
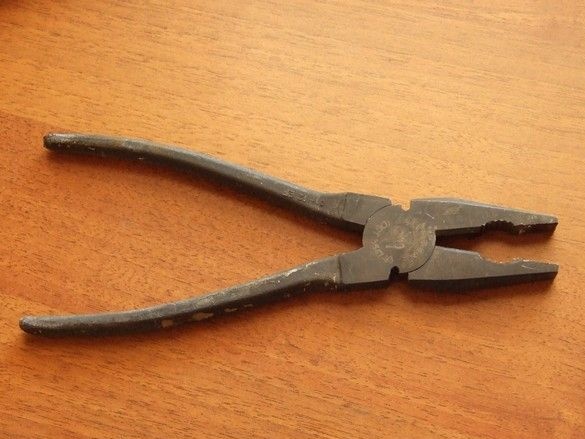
Well, you won’t get away from fate. The experimental pliers were stripped - I cut the plastic handles with a sharp knife, without them, somehow, significantly, hmm ... more elegant. Handles are good for big efforts and here, on thin stained glass, are not required. Then you can put pieces of thermotube of suitable thickness on the handles.
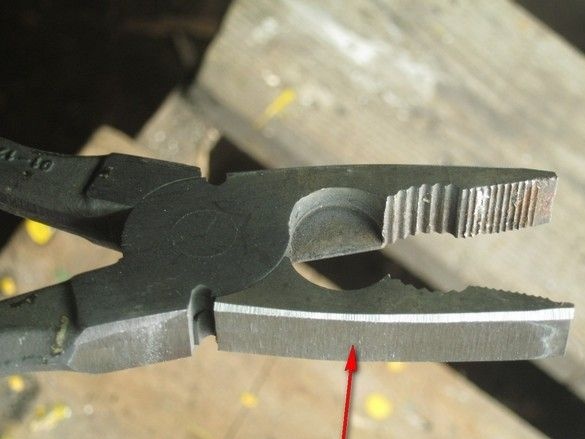
As soon as the efforts applied to the handles are not too great, it is possible to ease the workpiece-flat-nose pliers by draining off all the excess. Outside, these are reinforcing ribs. Stoch them on an emery with a coarse-grained stone, in the end, a little smoothed out a smaller stone.
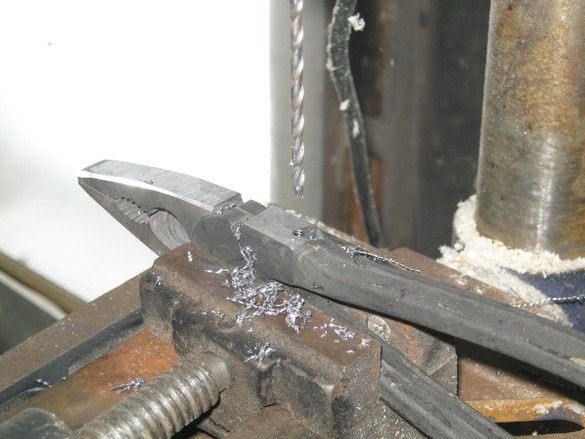
At the same time, on the emery, in the same place, he made a flat area for marking and drilling holes in the handle - for mounting the breaker depth gauge. Nothing complicated - the M5 screw is suitable in length, with a lock nut. I still wonder how easy it is to drill holes in pliers - it would seem that tool steel, but no, is drilled calmly.
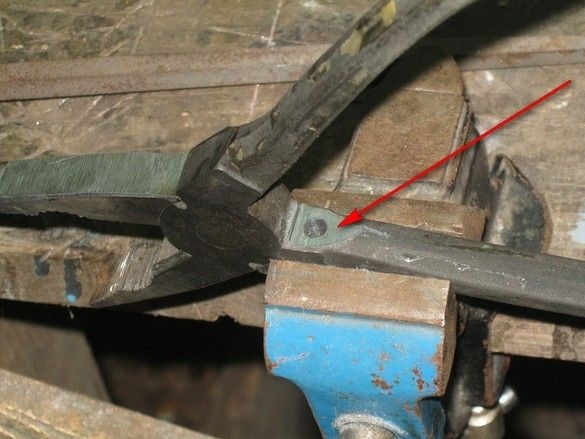
Initially, I drilled a hole for the thread and tried to cut the M5, but the tap went very tight, I was afraid to break it. He slightly drilled a hole and organized a platform with a magic file, where it would be convenient to solder the nut.
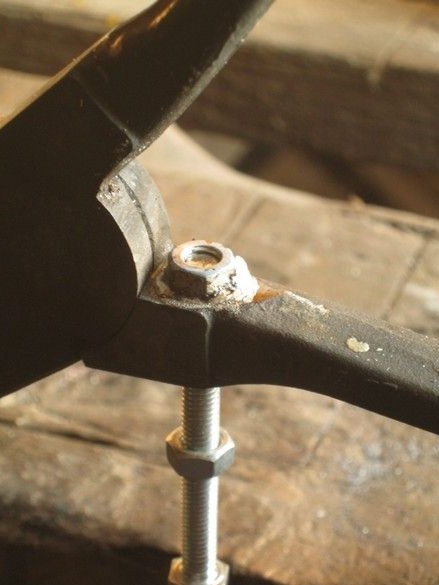
I soldered the nut with a gas torch, carefully so that the solder in the thread does not numb. Residues of acid flux are washed with warm water, a hard brush. It is convenient to use a used toothbrush. Dry the workpiece on the stove (central heating battery is not suitable). Incrusted ugly solder flows can be removed with a file or a medium file.
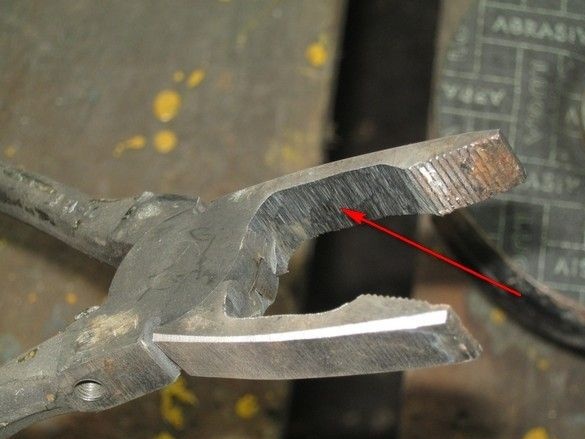
Continued the relief of the pliers. Not a trembling hand, a little "grinder." He gripped one handle in a vice, "the patient open his mouth wider" and trying on, in battle. Of course with headphones and glasses on his head.
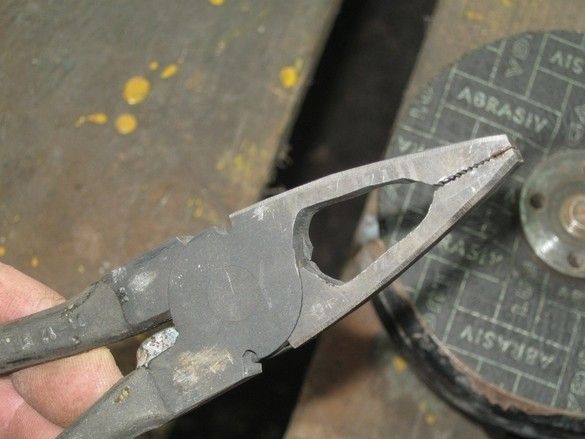
He left it thick on the sides - and less weight and further from the edge you can work. Well, old-mode nippers and notches, on a new instrument, would have looked somewhat inappropriate. The rule of good locksmith tone is to dull sharp edges.
The time has come for curved lips. They should be slightly wider than the pliers (lever) and curved, smiling.
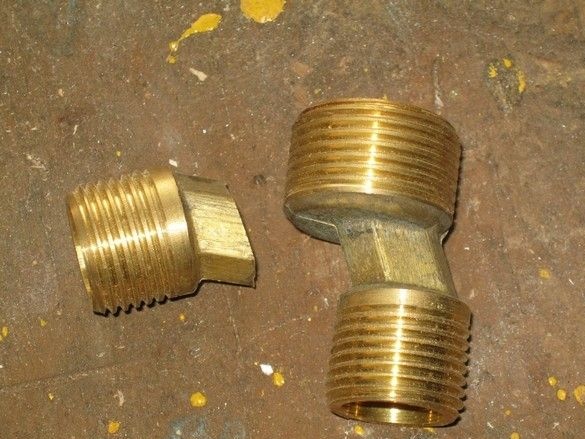
After going through my small pieces of iron, I found such a thing in the “water” rubbish - a water adapter with offset axes, to adjust the center distance when installing “mixers”. Bronze must be assumed.

The smaller cylinder fits nicely into the larger one and is pretty tight. The entire assembly is quite conveniently placed on the lips of pliers. It is decided - we will make sponges out of them. Bronze is well soldered and generally processed, not too hard and is guaranteed not to scratch the glass. True, the thread on the inner cylinder will have to be left - if you grind it off, it will be too thin.
I made blanks of sponges - sawed off the bottoms with a hacksaw for metal, leveled the edges on a small block with medium sandpaper
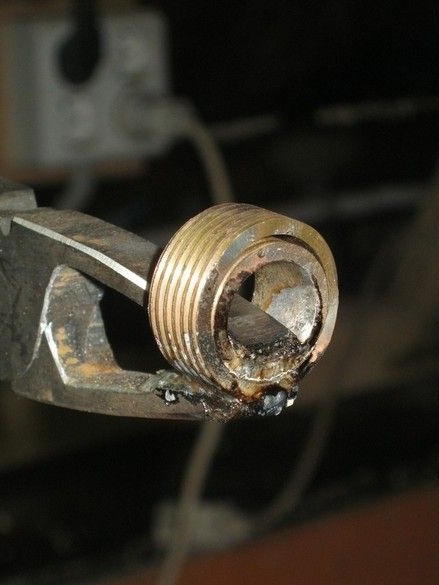
He adjusted the sponges with a “grinder” so that they fit more tightly onto my “omnipotence rings”, cleaned the corresponding contacting surfaces with a sandpaper, smeared it with flux paste and clamped it in the “working” position. He pulled the handles of the former pliers with a rope, by one of the handles, clamped in a vice, in a position convenient for soldering. I lit the burner, warmed up, soldered. Here, too, one should act without fanaticism and prevent excess solder, otherwise he strives to flow where he should not and solder everything to death.
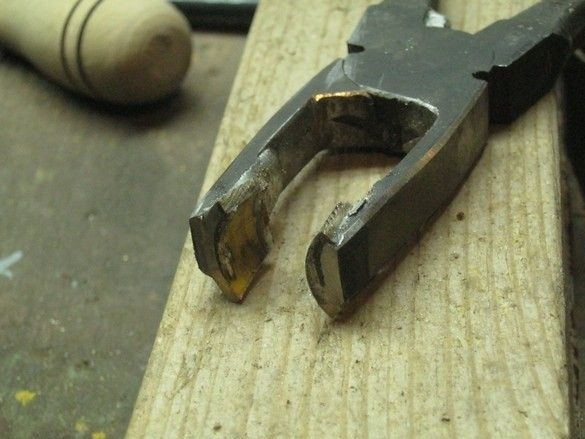
A hacksaw for metal, holding an almost finished tool in a vise, saw off the excess from the rings. Previously, of course, marking them. Scriber, felt-tip pen, nail. We dull the sharp edges, as usual, cut off the excess influxes of solder with a file. We wash off the flux residues with a brush or a toothbrush in warm water and dry it.
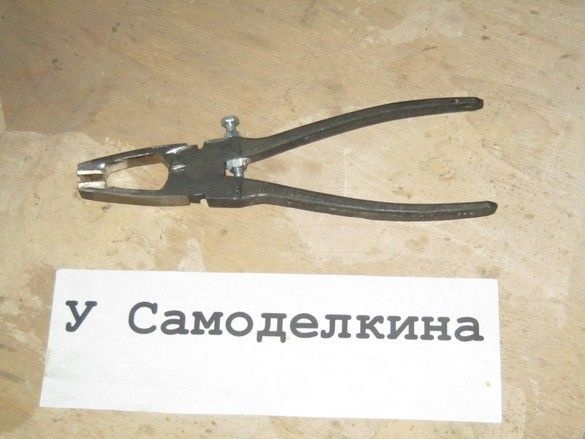
I picked up a screw suitable length, set the stop limiter. I tried on a 3 mm window pane. What can I say - it works like a pretty one. It is very convenient to cut small, frankly small and intricately shaped pieces with a new tool. Yes, in the latter case, the curved cut should be broken from two ends in two steps - the result is more stable and predictable. By pressing the cutter on the cut from one edge, we achieve the formation of a short, a couple of centimeters crack, we repeat the same, from the other edge, it can be a little stronger. Everything, a piece of glass breaks off along the cut line.
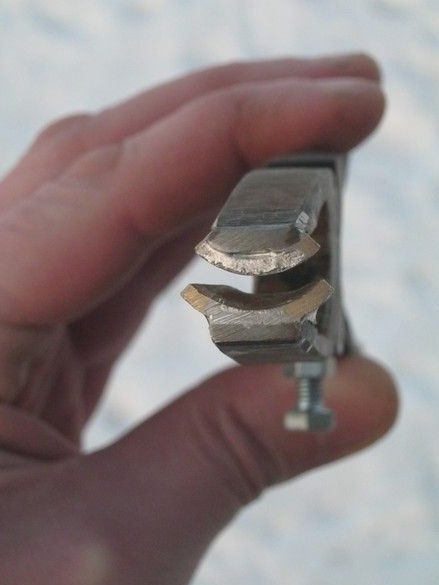
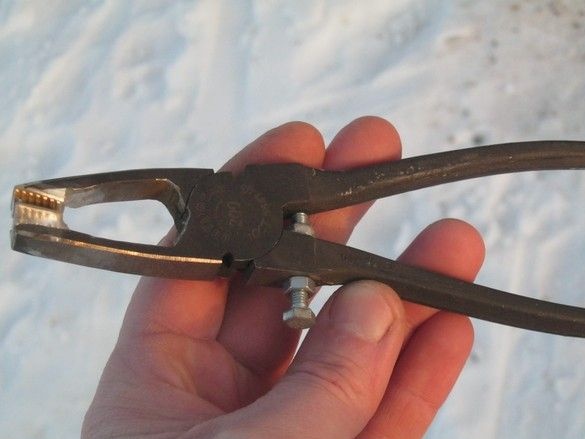