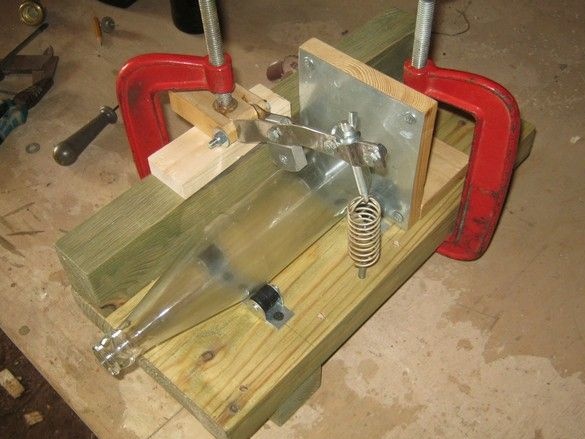
Generally speaking, any vessel is a sacred thing, which is extremely useful in the household. Not for nothing in humans, the task of acquiring dishes was always among the first, without it, nowhere. Each box and dish was treated very movingly, even an unfortunate clay pot, after breaking or cracking, was wrapped in birch bark and used for storage, whatever loose. From which only vessels do not make - wood, ceramics, metals, plastic, and of course glass. In the old clay days, when glassware was blown out, picking up molten glass on a special long tube, it was valued very highly and could hardly be very common. Now, machines are engaged in its manufacture, the dishes themselves are very cheap and common, although much less decorative than her sisters made by hand. Nevertheless, glass is a very decorative material and even for factory "conveyor" bottles, a craftsman with a bit of imagination will easily find application in the household and as elements of his designs or crafts. Moreover, the material, which is actually junk, is practically worthless.
Cutting glass involves applying a glass cutter to scratches in the right place, and then a certain impact on the glass, where a crack forms from the scratch. Applying a good scratch with a glass cutter requires certain skills and knowledge of some features of the behavior of the glass. For example - a scratch should be applied in one uniform motion, it is very desirable not to stop the glass cutter. The scratch should extend from edge to edge of the glass. A second time should not be carried out with a glass cutter for a scratch - the resource of a carbide roller is reduced and a crack in the glass is likely to go crooked. With sheet glass, it is simpler, you only need a good, flat surface and an even block or rail of sufficient length. Scraping an even ring on a bottle with a glass cutter so that its ends coincide is not so simple. Special simple help fixturesallowing the bottle as a body of rotation to rotate without shifting along the axis. Take a look at them.
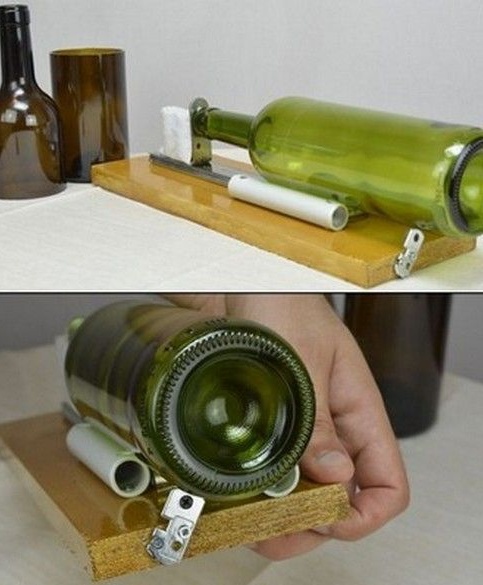
It should be noted a very simple and elegant solution - a cutting head from a glass cutter is one of the pillars of a rotating bottle. Pieces of metal-plastic pipes were used as supports for the rotation of the bottle.The main advantage of this type of cutter, in addition to simplicity, is the possibility of continuous rotation of the workpiece, since both hands are free.
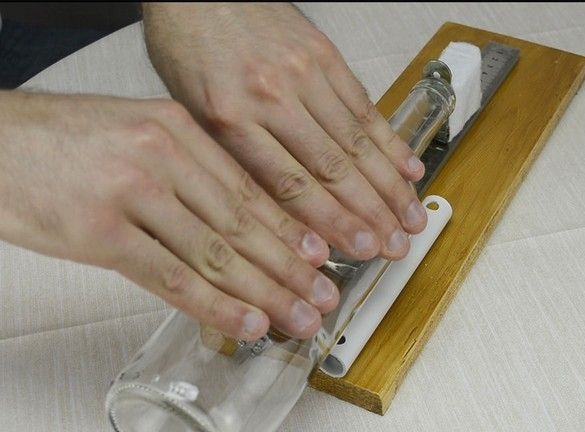
At the same time, a scratch is applied according to all the canons of glass cutting. Of the shortcomings - not universal, it is convenient to receive parts, only a certain range of lengths.
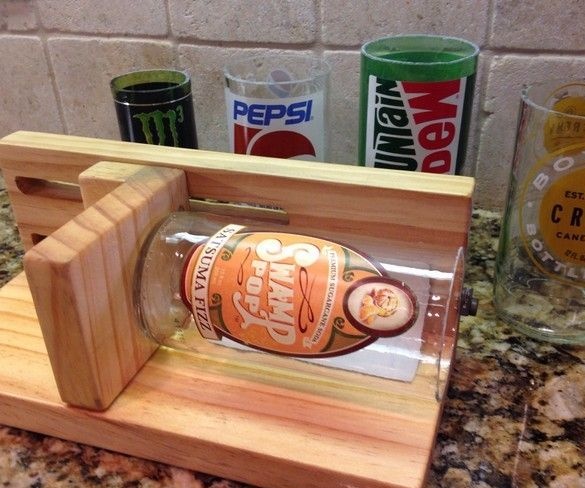
The variation on the theme seems to be very successful - it can be conveniently cut almost anywhere, but slipping over wood is worse. Perhaps surfaces in contact with the workpiece should be trimmed with plastic slippery for glass.
The scheme of such a cutter is good for everyone, but in principle it does not allow you to cut off a narrow neck at the bottle.
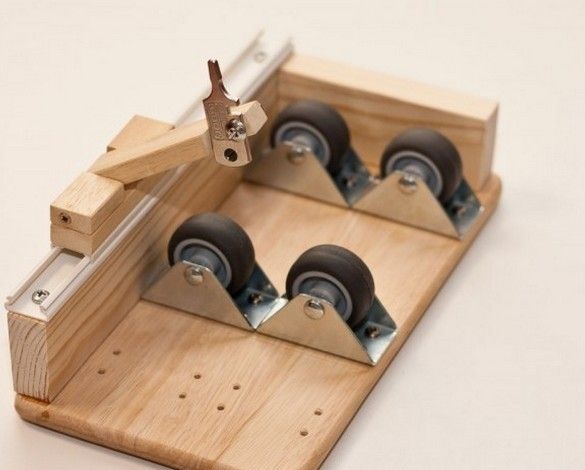
The second common type is with movable glass cutter. The solution is less elegant, we can say “on the forehead” - a rotating part, an instrument is brought to it. Nevertheless, in principle, it allows you to cut absolutely anywhere on the bottle, including a narrow neck.
A good option for such a scheme is a glass cutter holder with a joint. That will allow you to conveniently handle a very large range of workpiece diameters.
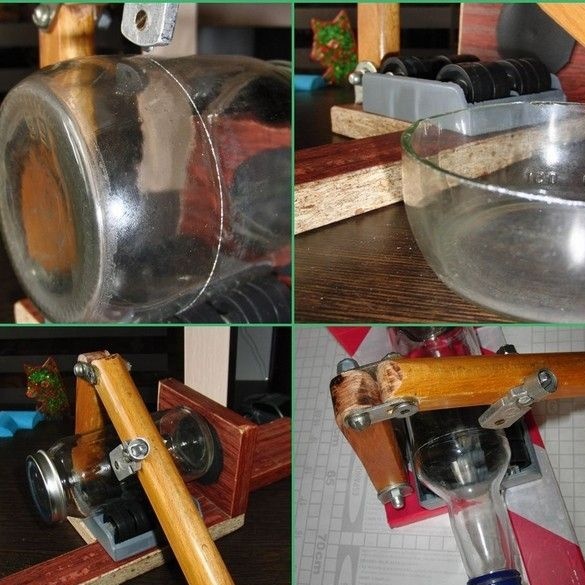
Note that the designer veneered the wooden emphasis with slippery plastic for smooth and smooth rotation.
The cutter is good, but it does not allow you to scratch without interruption, in one motion - one of the hands is busy pressing the glass cutter, and turning even an ordinary bottle, even with a large palm, 360 degrees, without stopping and intercepting, is very difficult.
So, an attempt has been made to develop a bottle cutter that, if possible, combines the advantages of both construction schemes - rotating the workpiece with both hands without stopping, any place of the cut, including on the neck.
To build a universal device, the fastening of the "support" of the glass cutter is selected using a joiner's clamp. Advantages - simplicity, versatility - with the help of gaskets from pieces of plywood or wood, moving the glass cutter assembly along the base of the device, you can place the glass cutter at almost any point on the bottle, almost perpendicular to the surface. The axial stop is also fixed with a clamp.
What was used for work.
Instruments.
For processing wooden parts, a planing machine, a pendulum saw, a drilling machine were used. Brushes and utensils for painting. Screwdriver or screwdriver for self-tapping screws. To process the glands, we used the usual set of bench tools, the same drill, electric sharpener, and a small angle grinder “Bulgarian”.
Materials
A piece of a suitable board, a piece of bar, fasteners. Glue, paintwork, rags. Sandpaper. As blanks were also used - a factory glass cutter and four wheels for of furniture. A piece of stainless steel, a suitable spring, two simple joinery clamps. A piece of roofing steel for the back stop.
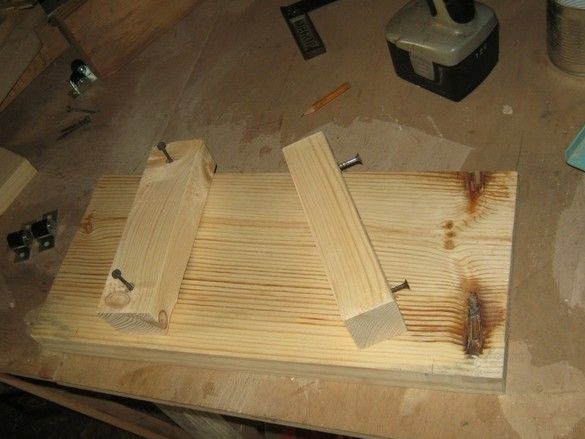
The base is a 50mm board, planed and "put" on its legs - pieces of a 50x50mm bar. Fastened with self-tapping screws with PVA glue.
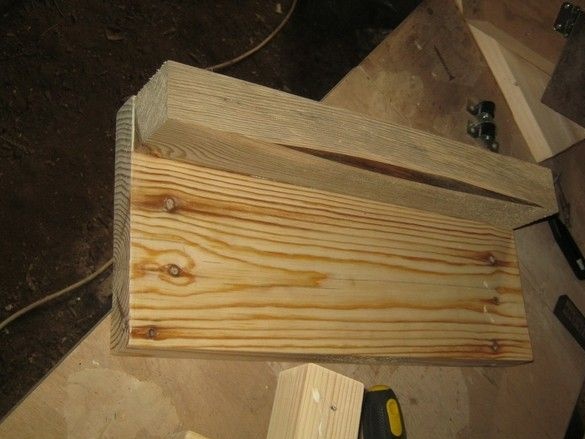
The glass cutter assembly should be slightly raised so that every time you do not have to use a gasket-stand of great height, a long platform along the entire base is made from a piece of block, it is also for glue and self-tapping screws.
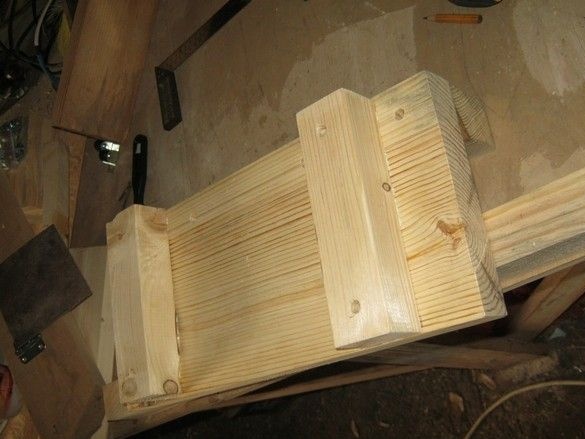
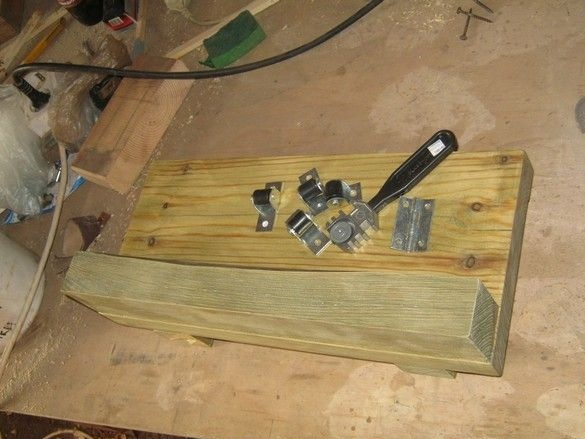
So that the pieces of wood do not become too dirty from dirty hands, he sanded a bit and varnished several layers.
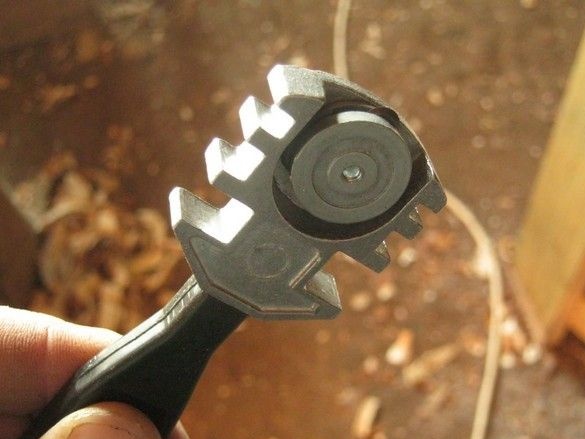
The glass cutter is selected inexpensive, but quite powerful.
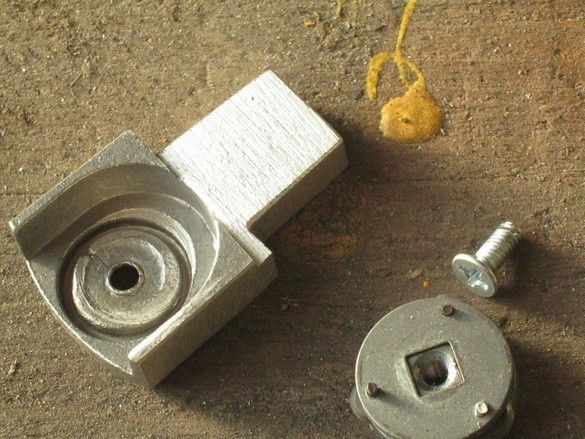
His handle was sawn off, everything superfluous was turned, a platform for fastening was organized.
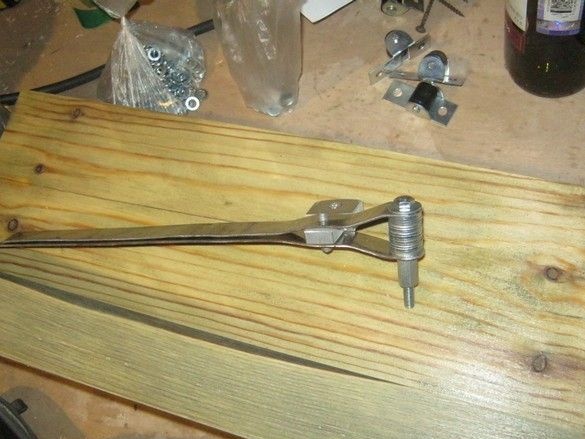
Of two suitable 1.5mm stainless steel strips, the glass cutter mount is curved. A set of washers imitates an element fixed by a clamp to the base, a long “residue” after the glass cutter will be used as a lever, with a spring tension. The glass cutter itself is sandwiched between two strips, a hole for the M6 bolt has been drilled through the entire set. With nut, washer, stopper, as expected.
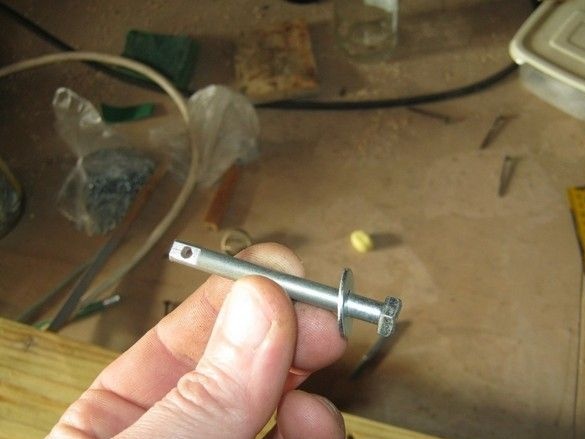
The fastening for the opposite end of the spring is made of a long M6 bolt. The smooth part without thread was cut, files were made with a file for convenient marking and drilling. Marked and drilled hole. The former bolt itself is passed through the base board. Opposite the bottle on wheels, with an interval of 50 mm, a number of holes were drilled, combining the installation of a spring bolt in them with the position of the back stop, you can place the glass cutter roller anywhere in the bottle. To prevent the narrow head of the bolt from picking up a soft pine board, a reinforced washer is put on the bolt.
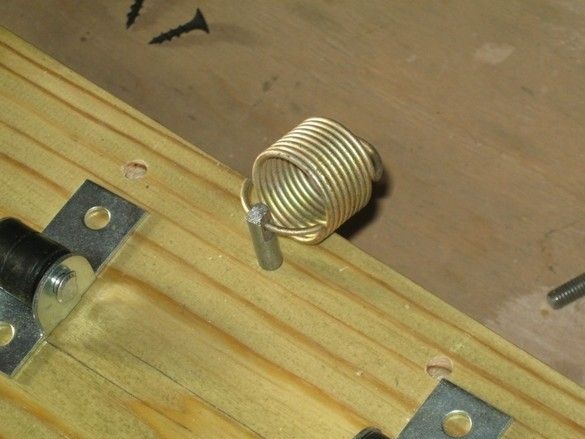
A perfectly suitable spring was found, both size and rigidity, a dream and not a spring. An alternative is a piece of spring for slamming doors, they have different stiffnesses, you can take a obviously stiffer one and bring the force to an acceptable one by etching the spring in acid, such as sulfuric acid for a car battery.
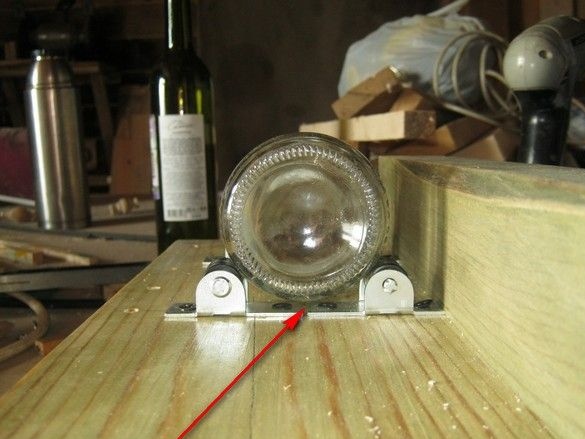
On the base, the rollers from the furniture are fixed with screws, and the distance between the two pairs should be maximum for greater stability of the workpiece, but the thinnest bottle should not touch the "bottom". It is long between pairs - focus on the shortest bottle that is supposed to be cut.
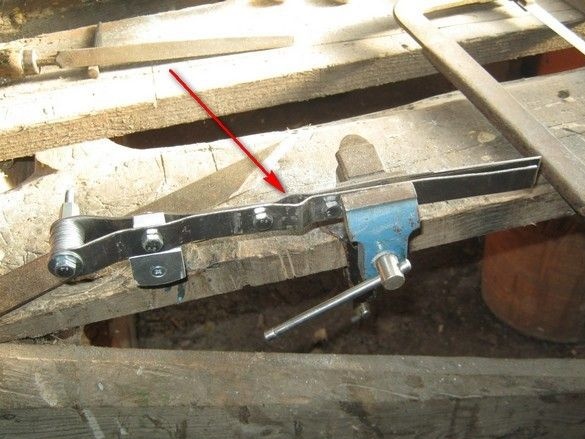
Having tapped on the anvil the shank of the drill clamped in diameter of 7 mm, formed a "hole" for a piece of M6 hairpin with a lamb. Without a piece of paper. To adjust the spring tension. On both sides, fastened with bolts, the same M6, so as not to produce the nomenclature. It was possible and welding. At several points.
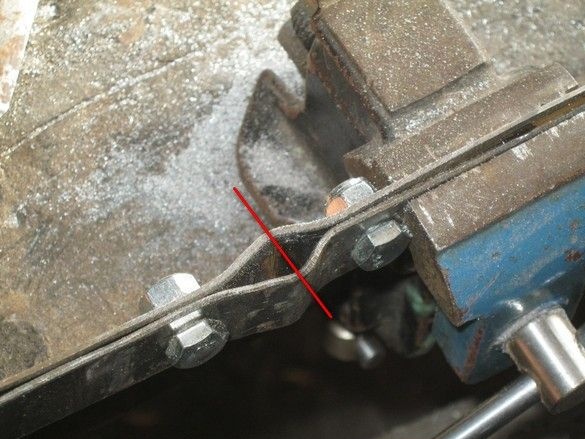
Two strips were selected in the pieces of iron already ready - scraps and not too even so that the washer under the lamb was level, I had to work with a file, aligning the seat for it.
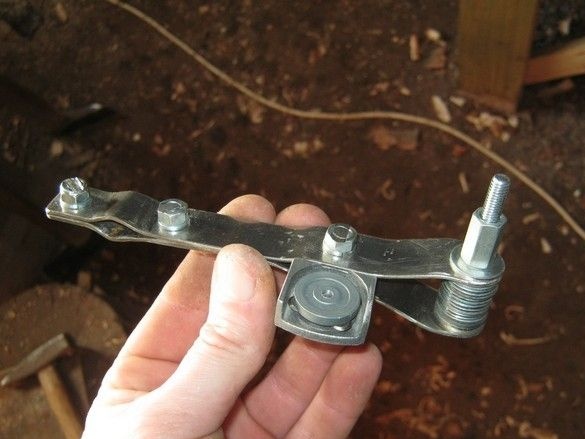
Cut off the excess glands. It's time to think about the standard part of the lever, instead of a set of washers.
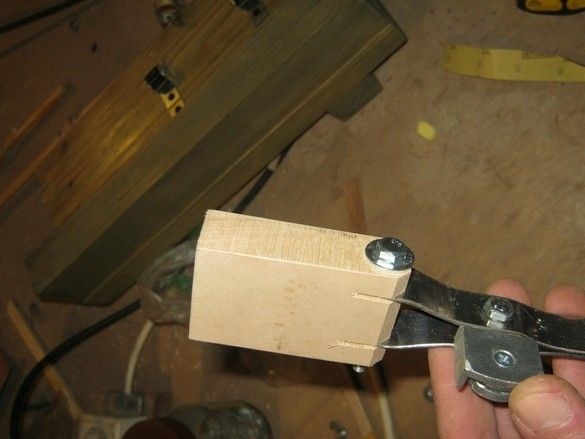
Such a small piece of wood with cuts was born from a piece of birch plank. Saws, to increase the width of the clamped part, so that it is more convenient and less fidgeted.
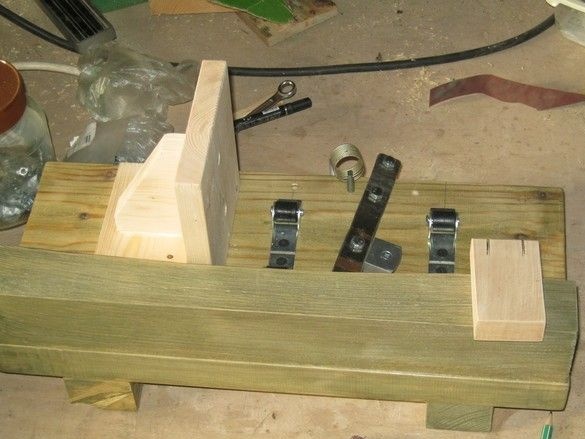
He also made a back rest for the patient from wood, fastened the elements in the same way, with glue and screws, lightly sanded and varnished several layers so that it would not crack from moisture and would not be caught in dirty hands.
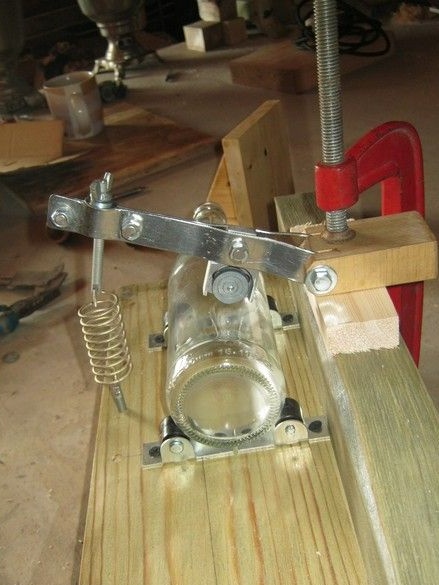
I tried the tensioner in the case, it works and not bad, rearranging it only in a different position is quite troublesome.
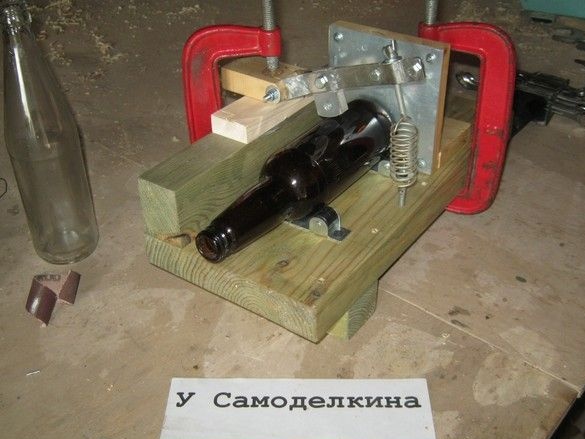
For smoother sliding, a piece of galvanized steel roofing was attached to the working surface of the rear wooden stop. Four screws in the corners. Practice has shown that the device works well without a spring tensioner, it is convenient to use it with a large number of identical cuts.
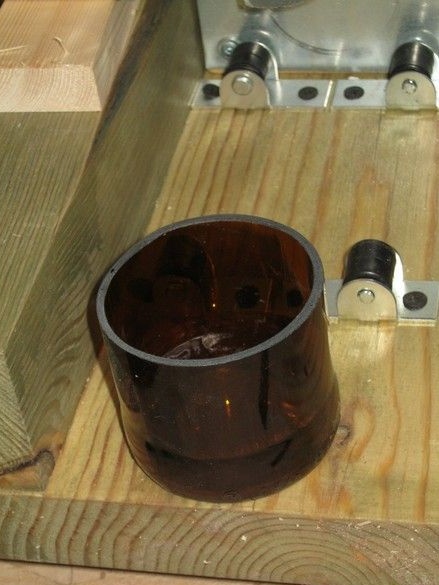
After applying the scratch, the formation of an annular crack should be achieved, best of all this was achieved by local heating with a candle or a small flame of a gas burner and rapid cooling with the corner of an ice cube or by dropping water from a pipette.
The finished cut may have sharp edges, for safe use of the resulting glass, they should be smoothed. Time-consuming, but with ordinary tools, this can be done by rotating the glass cylinder with effort, resting it on a piece of large or close to large, sanding paper on a rag base lying on the table. Under the skin, it is better to put a piece of felt, this will allow you to get a neat, somewhat "littered" safe edges.