
I had such a technical rarity. Given for the occasion. 1968, the brilliance, like all products of that time, resembles either a mine or a grenade, a sort of “military” both in essence and in execution. However, it’s you who haven’t seen an old domestic vacuum cleaner - the one, as a whole, a clean land mine, is scary to approach. But we must pay tribute to our ancestors, faith did not allow them to make glands with a specially limited service life. Execution sometimes, sometimes, disappoints, but was designed for centuries. To recall at least grandmother’s refrigerators - all kinds of “Minsky”, “Morozki”, “Dnipro” and “Yuruzani” there, have been working like cute for half a century. In a word, in our one-time age, such fossils cause tenderness and nostalgia for something stable and reliable.
But it's not about nostalgia. A small and convenient source of compressed air, although not of great pressure and flow rate, is nevertheless in demand in the workshop. It is very convenient to use it to “energize” the etching process, printed circuit boards or other copper glands. The process itself with running reagents stretches for hours and is very slow if there is no removal of the etched products from the surface of the piece of iron or the board. One of the good ways to remove them is to agitate the solution in the cuvette in one way or another. The presence of a miniature compressor solves this problem simply and economically. It is enough to put the compressor outlet hose into the container with the pickling solution and fix it there, near the bottom, so as not to pop up. You can hang a small weight on the tip of the hose or install a spray like an aquarium. It is only necessary to remember the resistance of the materials in the etching solution. The only inconvenience - the pickling solution must be in a sufficiently deep vessel otherwise, it will work poorly. The advantages are significant - cheap, in comparison with other methods and especially specialized chemical mixers, the multipurpose device is easy to adapt to any other desired location, minimum size and mobility, only the tip of a silicone hose immersed in an aggressive pickling solution is very resistant to various kinds chemicals. Useful word, contraption in the workshop. Again, it’s unpleasant when whatever mechanism nearby does not work.
The device, by the way, is the simplest, in the manner of an electric razor or of the same water pump like a “baby” or “Aquarius” - an electromagnet with an open, spring-loaded magnetic circuit. A certain working mechanism is mechanically attached to the moving part - a pump, for example, of two valves. When you turn on, the alternating magnetic field of the network, the same notorious 50Hz, distort the moving part, and that already does some work. Advantages include extreme simplicity and, as a consequence, overall high reliability.
What was used in the work.
Instruments.
Soldering iron, of course, with accessories. Power, watts, that way for forty. Instrument for radio installation and small locksmith. Building or special hair dryer for working with heat-shrink materials. To check the integrity of the circuits, a multimeter was needed.
Materials
To restore the compressor, they needed a coil of suitable sizes from the inductor, adhesive tape, nylon ties. Thermotubes for isolating soldering spots. To restore valves dried up from old age, I needed a piece of soft rubber or hardened silicone sealant. A piece of soft tube, a piece of wood, came in handy. A bit of solvent like acetone or 646. Cotton rags.
The restoration began with a revision - dismantled the compressor to atoms and examined, among other things, it was just interesting to stick your nose. Well, it is, everything seems to be in order, however, almost all the gum hardened from time to time and who turned into a solid lump, who simply crumbled. This is primarily about valves. He got the hang of it and cut out two elastic gaskets with scissors from the hardened silicone sealant. Set in place of the petrified. They had to be scratched beforehand and the residues removed, where mechanically, where acetone. Fortunately, the body of the pump itself is made of carbolite, is screwed in two parts, you don’t have any latches and other mischief. In a word, I put things in order here.
A piece of rubber tubing with a metal tip was turned on at the compressor outlet — it led air from the valve block inside the compressor housing to the outlet. The native tube was also pretty cracked and was replaced with a single, silicone, directly from the carbolite block. The air supply hose “to the consumer” turned out to be non-removable, but this does not cause any inconvenience.
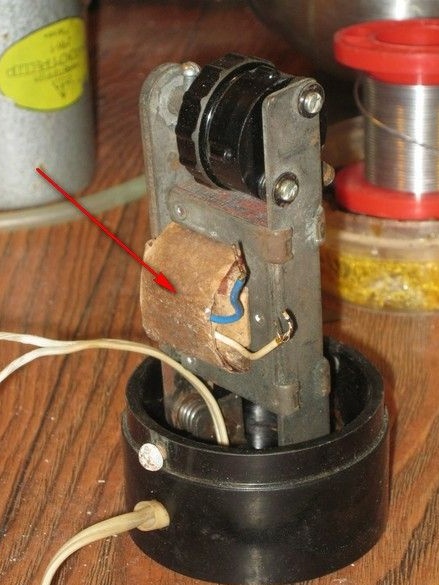
The next trouble was a break in the coil of an electromagnet. I tried to rewind several thousand turns of the thinnest wire, in search of a break, I really did not like it. The lightest effort and the wire breaks, after three or four breaks at the very beginning of the work, and the rewinding was carried out on, albeit an impromptu but winding device, where measures were taken to easily rotate the coils and the absence of their jamming, we had to look for another way.
Rummaging around in my supplies of transformers, I found what I was looking for - a whole (operable) inductor from some tube radio, with a very similar coil, only the thickness of the set was a little more. Having disassembled the core of the throttle, he tried on a coil to the compressor magnetic circuit. What can I say - almost "Victoria", a little wider, respectively - hangs a little, but it is easily eliminated with a wooden peg.
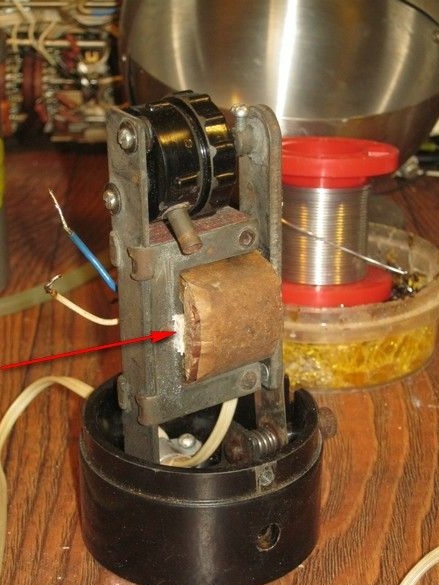
The inductor coil was wound with a slightly thicker wire and, accordingly, created a larger alternating magnetic field in the compressor core. The spring of the anchor could not cope with it, the anchor rattled on the magnetic circuit. I had to find a way to reduce power without rewinding the coil - I used the reactance of the capacitor. On alternating current, any capacitance has reactance, and, unlike the active one, heat is not released on it (reactive element), which is extremely nice - quenching resistors in such applications are mercilessly heated. The only significant drawback is the strong dependence on the load. But in this application, the load is constant and the method is applicable and convenient. To calculate or simply determine the capacity of the quenching capacitor, there are simple formulas and even more simple nomograms, however, in this case, it was easier to choose the capacity in practice.For reasons of reason - now, without any resistance of capacitors, the power of the electromagnet is maximum, all that is added to the circuit, the power will weaken. It is required to select such a condenser in order to slightly weaken the magnetic field, but so that the air flow pumped by the compressor is sufficient. It was possible to pick up three times - the classic "plug", like mortar. Metal film capacitors K73-17, at 630V. Of the two connected in parallel - I recall, while the capacity decreases by half (with the same capacities), the working voltage is the same.
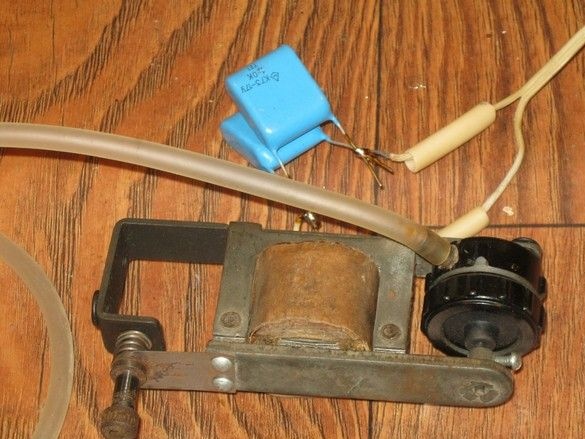
Having let the compressor work in such a “wide open” form for some time (remember the reliability theory - 90% of breakdowns occur during the first hours of operation of the device) at the maximum armature amplitude and in the other modes, I was convinced of a smooth adjustment of performance. The temperature of the coil did not exceed "room".
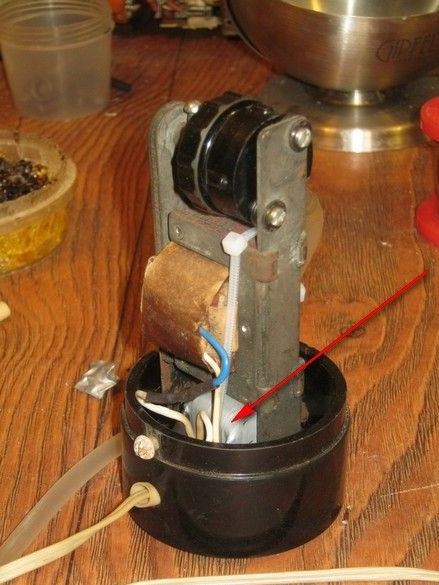
A set of quenching capacitors insulated with adhesive tape was rather conveniently placed in a sort of “basement” of the structure; in addition, the capacitors were fixed with a nylon screed to the structural elements. The compressor was placed in the housing.
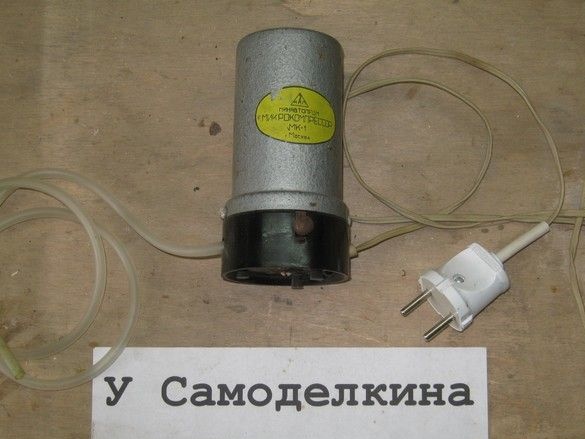
The broken “old-mode” plug has been replaced with a suitable one, to modern outlets, in the tail of the plug, on the wire, a piece of thick-walled silicone tube is dressed - a preventive measure, from bending and damage to the wire in a characteristic place. The compressor is tested assembled and hired and staffed.