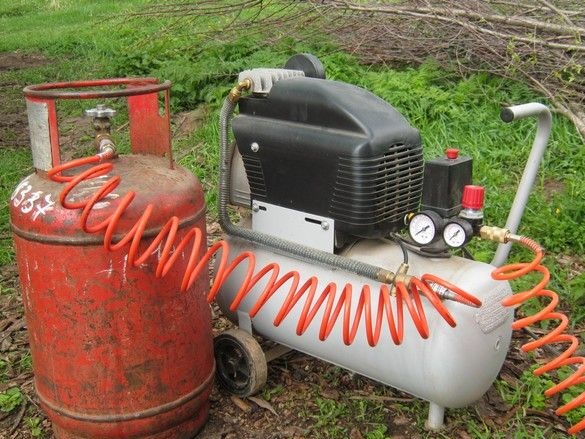
Continuing the theme of equipping a workplace for glassblowing in the workshop, one of the main elements for glassblowing is a special burner. Certain requirements are imposed on it, among the first - a stable flame torch. The burner is fed with a mixture of combustible gas, and among its components, most often air enters. It is clear that its smooth, constant in time flow is required.
In old clay days, air was compressed to supply it to the burner using bellows. Surely today, “When spaceships plow the Bolshoi Theater”, you can find small gas burners like jewelry or dental, with foot furs. This makes sense for portable devices - low weight, non-volatility. Sometimes, in order to obtain compressed air to a small pressure, a water-jet pump is used in laboratory conditions.
For table burners, in particular, used by glass blowers, electric blowers - compressors are now used. Operational requirements for blowers, glass blowers - near the burner, compressed air should be under pressure, 100 ... 150 mm Hg above atmospheric pressure. Air must be supplied evenly and without interruption - the cessation of air supply at the crucial moment of operation can lead to the death of a valuable product. In the case of working with a carburetor, there is a danger of a flame leak into the carburetor and a fire is possible.
First time for experiments with a glass-blower gasoline burnerapplied homemade compressor from the fridge. However, it turned out that he had to turn on quite often, ideally - to work almost continuously. In this case, the pressure will be the most stable. In this mode, a dehumidifier in the form of a box-can with silica gel should be installed on the air intake. Otherwise, moisture from the air will accumulate inside the compressor in the oil. One of the design features of compressors from refrigerators is that an open electric motor floats in oil. Accumulating water will sink to the bottom and can easily cause a short in the windings.
The factory “building” compressor is much more productive. A fairly long work between switching on is ensured by its 24-liter receiver, so it’s more convenient to work. In addition, the compressor of the classic layout is a piston group separately, the engine separately is like nuts and cutlets in the message, and there is no need to drain the incoming air. The factory settings of the pressure switch allow the compressor to automatically pump capacity up to 7 atmospheres, then, analysis by the consumer is through an adjustable gearbox. The very small pressure necessary for the operation of the burner allows the compressor to turn on quite rarely - once every few tens of minutes, depending on the power of the burner. Nevertheless, each of its start-ups adds some gray hair to an unbalanced person - the compressor is quite noisy. You sit in silence - only the flame of the burner hisses slightly, in the hands of curly glass - a kind of frozen music, awe in your soul ... And suddenly behind your back - DRRRRRRRRRRRR !!! Oh mother-my-Soviet-woman. Then even the Zen master will jump on those same one and a half meters.
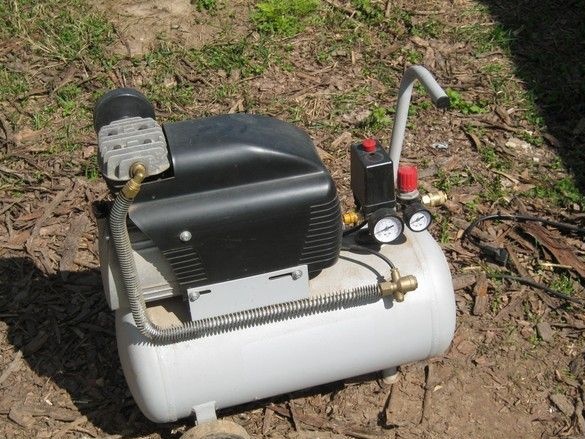
Of course, in the most radical way, it will be to remove the noisy unit in a separate room, in fact, they do so in large workshops. And what do you tell Grandpa Mazay to do in his own, representing a single space? Also, of course, think in this direction, but for now, as a compromise option, you can use a simple way to reduce the number of compressor operations by increasing its receiver.
Generally speaking, compressors of this type (reciprocating, "construction"), can, with the same compressor, but with different receiver capacities, differ significantly in cost. This is connected, apparently not so much with the cost of steel that went to the cylinder, but with the weight and dimensions of the device and, accordingly, the cost of transportation and storage.
During operation, the compressor with a small receiver is good for relatively mobile applications, where its modest dimensions allow convenient movement, it can be powered by a pneumatic tool in the farm or painting, when the length of the available hoses may be insufficient and more convenient to transfer, transport the unit to the place of use . For stationary use, for the same type of tasks, it would be better to have a larger receiver capacity. However, in the aforementioned subsidiary farm, both these and other tasks may arise. Say, in the cold season - stationary use in the workshop, with the onset of the warm, "construction-field" season, is relatively mobile. For example, at a sufficient temperature “overboard”, painting is more convenient to perform on the street, and so on. In this case, the receiver’s variable volume would be convenient — increased in a constant place, even if it would be more cumbersome, “in the field” - staffed. This begs the solution with a plug-in connection to the native cylinder, another capacity.
This is exactly what has been done. As an additional receiver, a household gas cylinder for propane with a capacity of 27 liters was selected. After some reorganization of his gas economy, he remained “on the siding”. It was decided, if possible, not to make changes to its design so that, if necessary, it could be used for its main purpose. For this, standard connecting parts from broken gas appliances were used. Also, it would be convenient to use standard spiral plastic hoses with quick-detachable connectors that automatically lock the channel. This will allow flexible configuration of the equipment. For example, you can use a longer hose, connect several of them, install a cylinder of a different capacity, several pieces through standard “tees” and so on.By the way, if necessary, you can pump compressed air into the container, for example, for use in a place where there is no electricity.
So. What was used in the work.
Tools, equipment.
Structural soldering was used - a small gas burner with appropriate solder and flux is needed. Something to drill, a set of ordinary bench tools.
Materials
In addition to the experimental compressor and the gas cylinder, we needed - standard pneumatic connectors, FUM tape, solder No. 3 and pasty flux to it - from a copper water supply. Standard connecting fitting to the gas bottle.
The place of attachment of the additional capacity, after reflection, was chosen as a plug on the tee. A standard quick-locking pneumatic “mother” will be installed on it. Among other things, this will allow you to disconnect and attach an additional receiver at any time, including under pressure, without loss of compressed air.
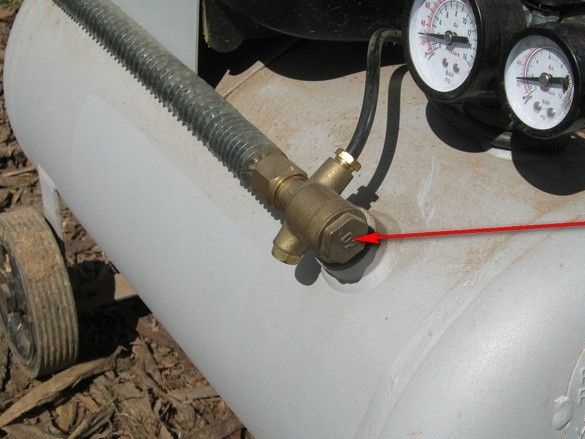
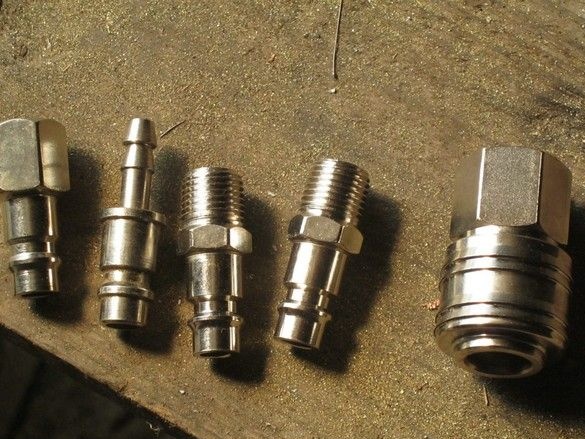
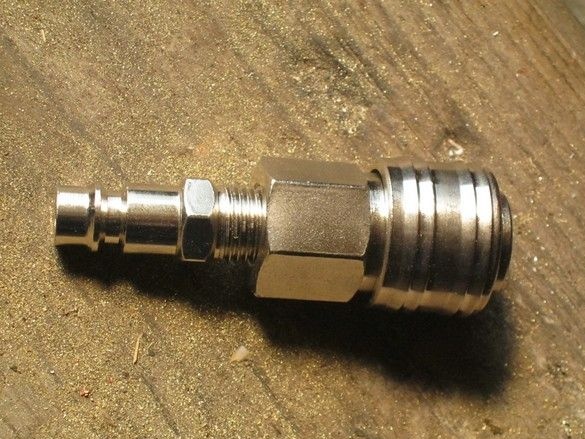
A set of standard fittings was purchased at AliExpress. "Mom" with a female thread. It is impossible to solder it directly - you can damage the rubber seals inside, and disassembling is not so simple. It was decided to use one of several “popes” (the Swedish family?) With the same thread as a transitional part. He is without any gum - you can safely solder.
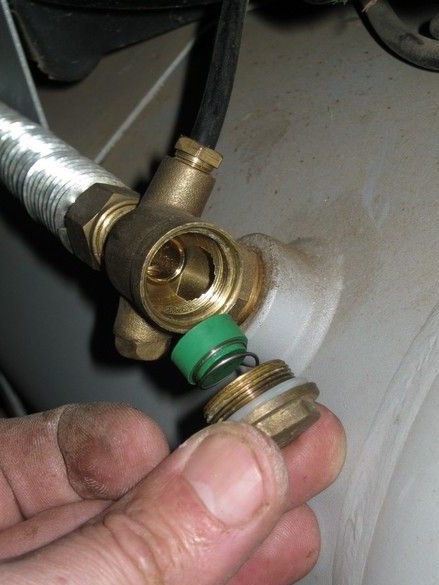
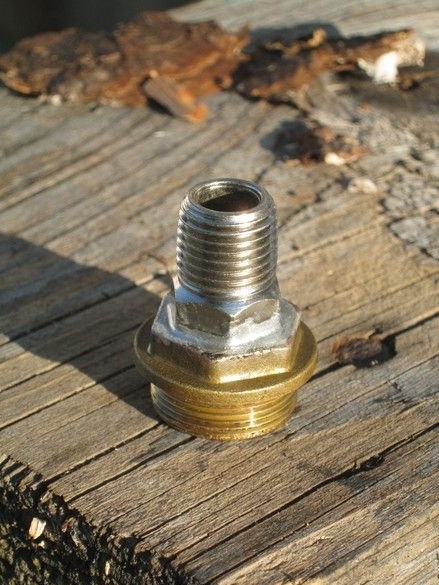
After unscrewing the plugs on the compressor, it turned out that this is not a tee, but naturally a check valve. However, this does not change the matter, you only need to make sure that the soldered “dad” does not stick too much inward and does not interfere with the normal operation of the valve. The silicone gasket and the embedded spring with rubber were removed from the plug. The center was found, a small hole was punched and drilled and wasted with a file, and then with a file to the desired diameter. "Papa" is shortened with a hacksaw for metal, the soldering spots are cleaned. Flux, soldering, washing flux residues with warm water, reassembly. Installation of "mother" on the FUM tape, test with working pressure.
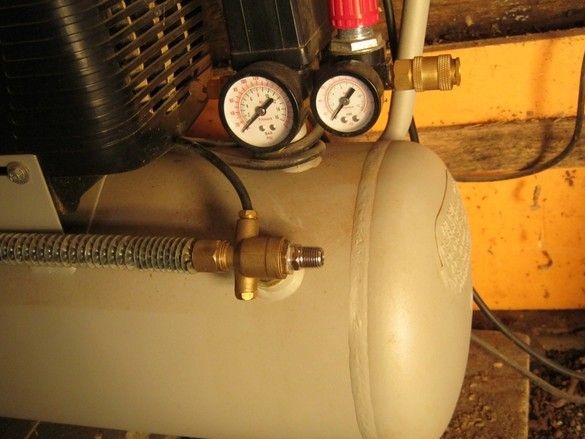
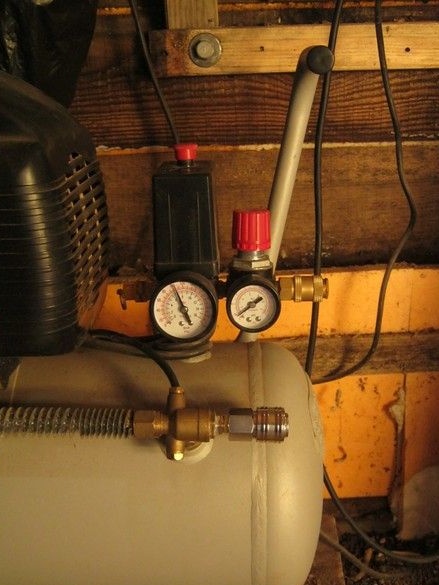
To connect to the system of a gas cylinder without its modifications, you will have to use the standard connecting parts. They were extracted from a failed domestic gas reducer. The fitting was modified for a tight fit with the "dad" from the set. Small file. Well, and as usual - clean the soldering spots, flux, soldering, washing residues. Yes, do not forget to put on the union nut before soldering - it is not removed from the finished soldered adapter - the “turnkey” faces interfere, this is not bad, it will not be lost during operation.
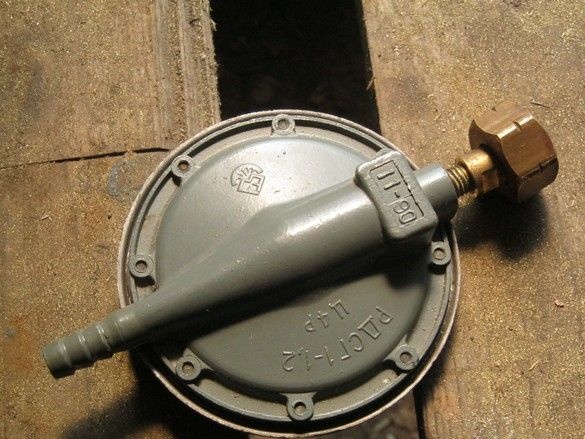
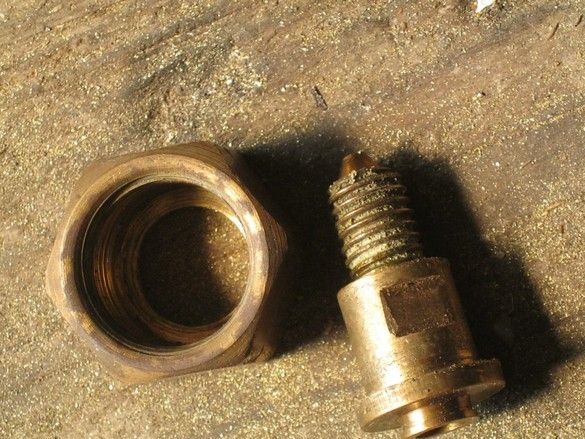
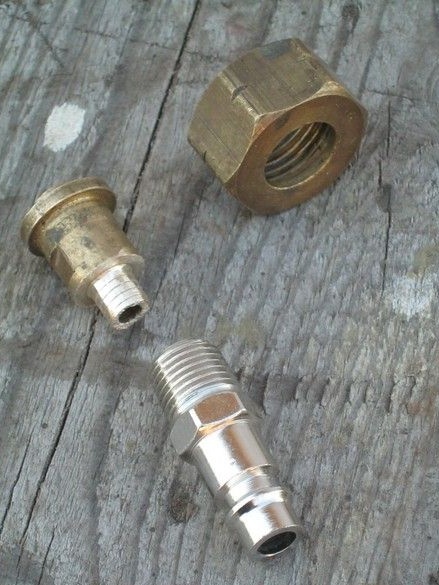
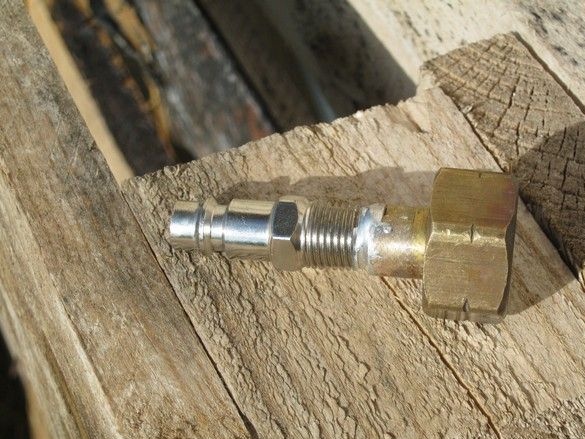

Before screwing onto the bottle, remember to install the rubber gasket. The thread is left. Order, you can combine and try the pressure.
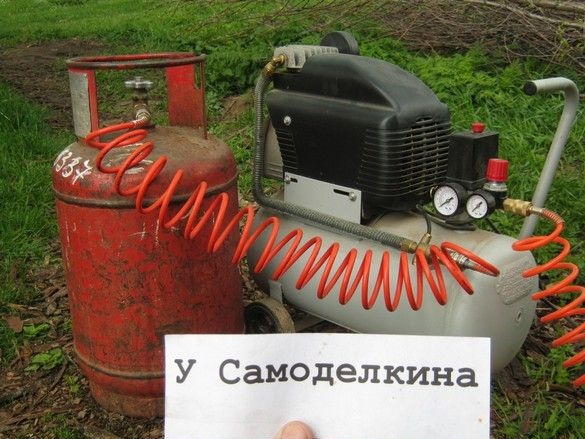
Everything works, tightness at height. It turned out to be true that under full working pressure of 7 Atm. the connectors to the bottle are difficult to disconnect, however, this is not too important. If you need to disconnect the inflated balloon, you need to close it with your own valve, and after reducing the pressure in the standard receiver, everything is perfectly disconnected.