Today for many, the topic of profile bending in home conditions for several reasons.
First of all, this is the manufacturing cost and lead time. Oversized delivery is a separate matter.
Secondly, accurate sizing is much easier right at the installation site.
And the third. On such an instrument, if desired, you can even bend curls with a variable radius.
The author chose the most common scheme, with a roller on a hinge and a hydraulic jack.
The body was welded from the scraps of the 20X40 pipe and a powerful channel.
The author has simplified the pressure rollers to the maximum:
The outer bearing ring in this design is the clamping surface.
Draw shaft.
To make it, I sketched a sketch and ordered it from a turner.
The cost of the shaft is about a thousand rubles.
His scheme.
The author had to purchase the following:
Bearing units for 204 bearings - two units.
Bearings 204 - four pieces.
Hydraulic jack. Hardware and fasteners.
Hairpin M20
with washers 22X37 and 22X56 mm.
It performs the function of a shaft.
Large washers serve as limiter flanges.
With their help, there is no need to use side stops.
At the same time, it remains possible to change the geometry of the pinch rollers for various profiles.
It is enough to collect the necessary sandwich from the washers.
All finished welded blocks are interconnected without welding.
This is done on bolts, so that there remains the possibility of displacement relative to each other.
From the first time, the design of the machine turned out to be quite successful.
The arc is symmetrical and even.
The process of its manufacture does not require special physical efforts.
With each pass, we slightly jack the right side of the machine.
This reduces the bending radius of the profile.
The lever is made of 3X40 strip.
Hand pen from an ancient meat grinder.
The mounting location of the lever to the shaft in an unassembled form.
Here are the actual drawings.
Most likely not drawings, but diagrams, but the author tried to depict the necessary dimensions as clearly as possible.
This is a successful and author-tested design.
It ensures a smooth passage of the profile through the rollers and gives the correct arc shape.
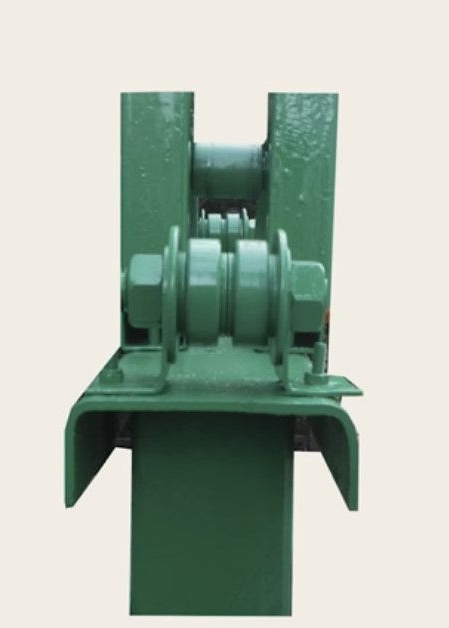
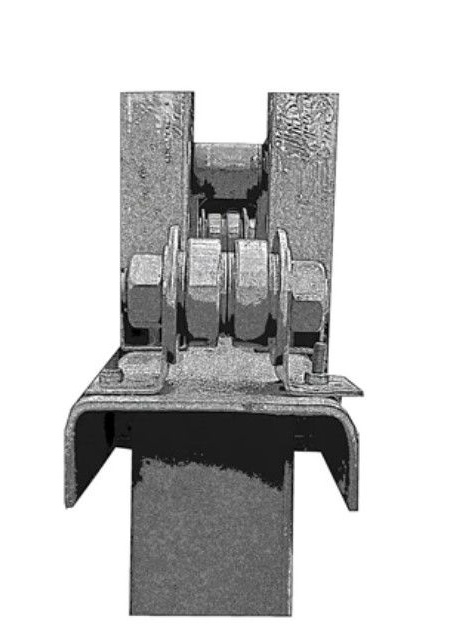
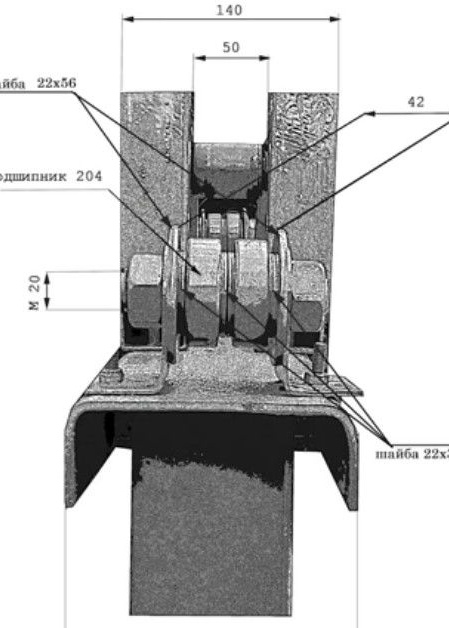
It should be remembered that at 240mm from the edge of the workpiece, the profile remains straight.
The straight section is highly visible at small workpiece radii.
For the manufacture of arcs of small radii, a margin of 25 cm should be left, which can later be cut off if necessary.
The design of the machine allows you to expand your creative possibilities.
For example, it is possible to produce not just arcs, but to bend a profile in different directions, and not only in one plane.
To do this, just squeeze the shaft, rotate the profile by 180, or 90 degrees. You can also change the clamping mechanism itself. By installing clamps for pipes of different diameters - the same machine can easily bend pipes.
Definitely, you should optimize the clamping system near the jack, providing it with a ruler. Then do not have to guess with the radius of the bent part!
Many thanks to the author for the work done and the drawings provided.
It’s a pity the process of creation is not filmed, but the people are rugged. And for those who bend the profile on their own, they are completely friends with welding and drawings!
Posted by Evgenich, video by the link