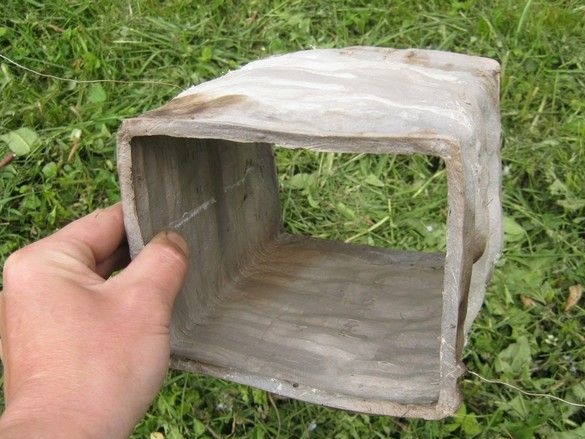
Very often, in the descriptions of various stoves, the manufacturing process of the most important and crucial part - the muffle, is either neglected, or they touch on this topic in passing, or the information is frankly untested. And meanwhile, this is the heart of the muffle furnace, on which many of its parameters largely depend. Muffle materials are not often found on sale, they are often expensive.
The following describes an experiment in manufacturing a muffle for a glass annealing furnace (maximum 600 ° C). An oven with this kind of muffle can be used in glass-blowing, lampwork. The volume of the muffle is about 4 liters. Heater made of nichrome wire of the "internal" type - the spiral is walled up in the thickness of the walls of the muffle. The task was to make the most inexpensive efficient design suitable for practical use.
So. As a material for the walls of the muffle, a mass consisting of talc mixed with liquid glass was used. The heater is a nichrome wire. As a primary thermal insulation - a thick asbestos cord. The main thermal insulation in the furnace is assumed to be foam. Consider some of the features of these materials in a similar application.
The first thing you should pay attention to is water glass and nichrome. Of the important - liquid glass is slightly electrically conductive in the melt from about 650 ° C; it actively dissolves furnace refractories from 700 ° C; water glass causes catastrophic corrosion of heaters. It is enough to drop one drop of liquid glass on the heating wire so that it burns out at the first start of the furnace. Of course, when mixing liquid glass with other components (corundum, chamotte, sand, etc.), the damage to refractories from it decreases, but the corrosive effect on the heater remains. This corrosive effect is explained by the high content of sodium oxide in liquid glass (liquid glass is sodium silicate Na2SiO3). Sodium oxide destroys the protective oxide film on nichrome by the reaction:
6Na2SiO3 + 4Cr2O3 + 3O2 = 4Na2CrO4 + 4NaCrO2 + 6SiO2
This reaction actively proceeds from 600 ° C and leads to deep oxidation of nichrome.
With fechral, the situation is even worse - a protective film of aluminum oxide in contact with sodium silicate loses its protective properties and begins to pass oxygen to the metal, which begins to oxidize almost like simple iron.
Asbestos. At 800 ° C, it loses chemically bound water and turns into powder. Therefore, products from it, such as cardboard or cord can work up to this temperature. In addition, fechral should not be in contact with asbestos [2]. By the way, about the loss of water - when using asbestos board or cord at high temperature, calcining, asbestos products become fragile. If it is necessary to disassemble the asbestos thermal insulation, you should let it lie down for a day or two. Asbestos is saturated with water vapor from the air and becomes soft again.
Foam concrete. It is a building material for general use. With a not very strong surface, it withstands 600 ° C and up to this temperature, it is an excellent heat insulator.
Refractory coating of talc-liquid glass, in itself is operable up to 1000 ° C [1].
So, at the desired temperatures (up to 600 ° C.), The listed materials can be used.
The manufacturing technology of such a muffle is described in [1] for miniature high-temperature tube furnaces and involves winding the heater on a collapsible blank, coating, drying, removing from the blank and drying, finishing and supplying the finished muffle with thermal insulation. Below, according to the proposed technology, an attempt is made to manufacture a muffle of a fair amount - slightly less than 4 liters.
What was required for the manufacture.
Instruments.
To make a blank of wood, I needed a carpentry tool, a screwdriver. Container for mixing the components of the refractory mass, rubber spatula for its application.
Materials
In addition to liquid glass and talcum powder (baby powder), we needed - thick paper, twine, paper tape, packing plastic film, some fasteners. Finished spiral of nichrome.
First of all, I picked up a blank for winding a suitable size. She became a box in which before experimenting with the manufacture of clay muffle. To give it “easy folding”, twisted the walls with self-tapping screws through a layer of newsprint, this prevented the adhesion of the lacquer layer. If the blank is made specifically for winding in the described manner, there is no need to cover it with varnish. After assembling the side walls, I screwed the ends of the box, and removed the screws on the side walls. As a result, I got a box that is dismantled from the ends.
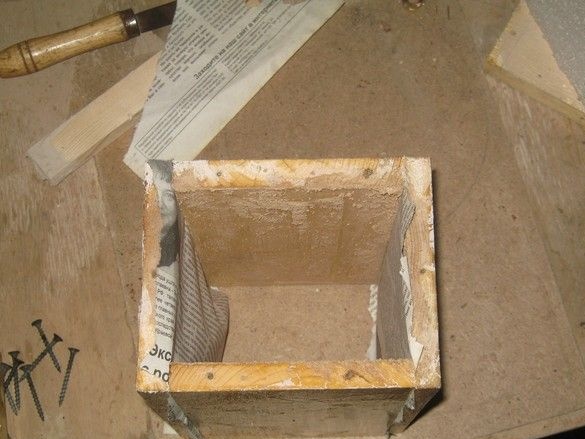
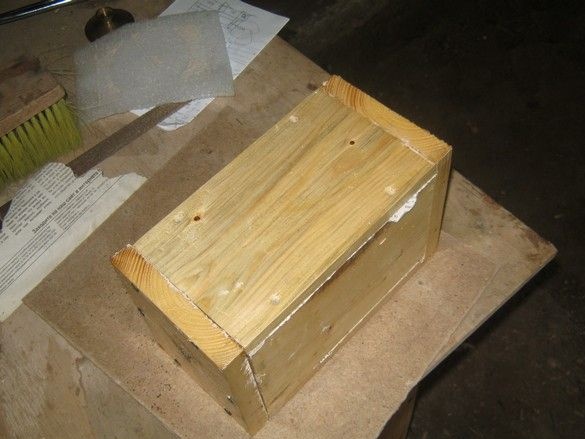
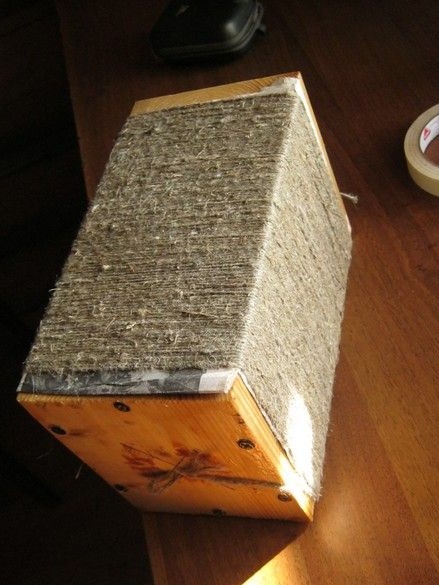
The next step is winding the rope. Tightly, turn to turn. The simplest twine was applied. The ends were temporarily fixed with several brackets from a construction stapler. At the ends, so that you can dig out later. I made a layer of “waxed” paper on top of the rope winder - I applied the packaging from a pack of printer paper, fastening the ends with paper “masking” tape.
Heater wire preparation. Nichrome is a very expensive thing and to acquire it with coils so that the farm has a number of diameters, in case of need for a heater - it is unprofitable. It is also not always possible to purchase several tens of meters of the required diameter. As a possible option - look for ready-made heating spirals and use them. Below in the photo, the local version is a severe Chelyabinsk spiral. Note the moderate cost and availability of a number of different capacities in the store. Even lower is a series of iterations for turning a spiral back into a wire.
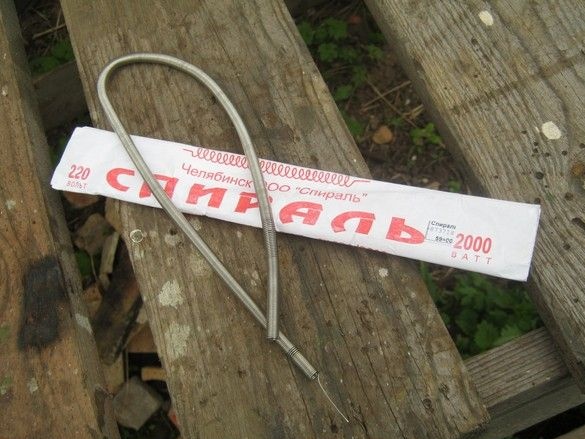
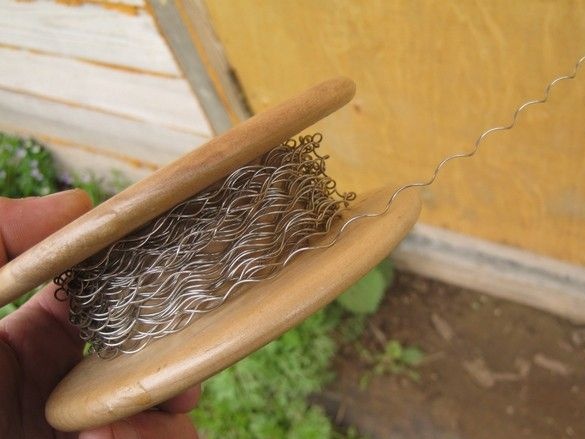
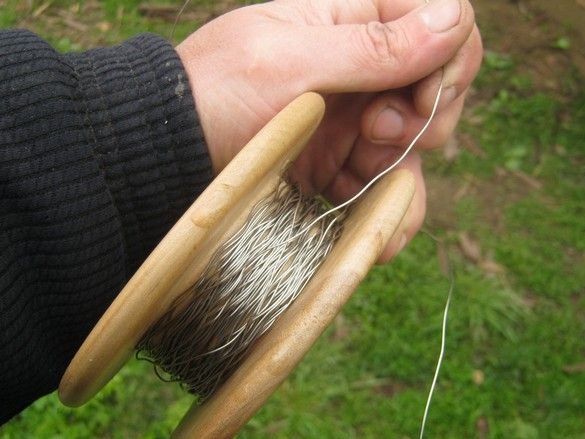
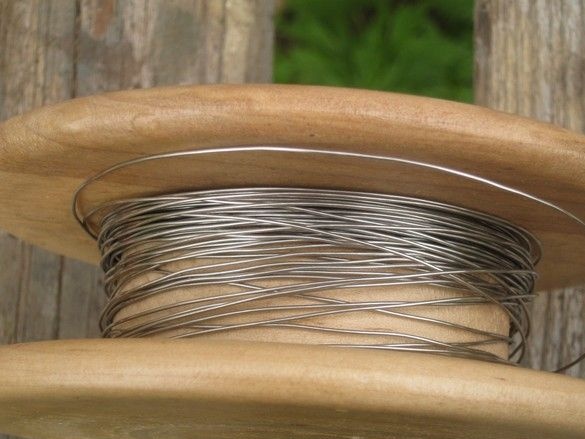
The end of the bent wire was tied to anything massive and held out, squeezing rags through a lump. In this case, ensure the free rotation of the free end of the wire around its axis. The last few edits - through a series of videos.
The wire is prepared, it turned out about 13m. The power of the heater depends on the size of the muffle [2] and in this case a little redundant - the heating rate will be slightly higher than optimal. Received 13m divided by the perimeter of the prepared blanks - received the number of turns that will have to be wound, it is small, which greatly simplifies the task. Divided the length of the winding (muffle) by the number of turns - got the winding step.In this case, it came out equal to about 8mm - we walk, you can wind it with your eyes closed.
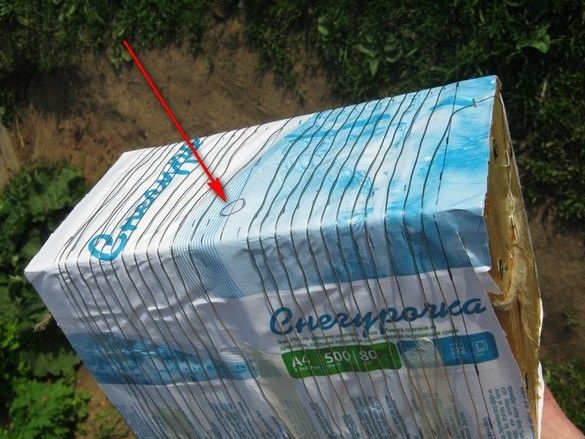
I decided to stick a thermocouple into the side of the muffle - this is a very concise design, you can use a relatively short, rigid (in a ceramic or steel casing) thermocouple without compensation wires, directly to the terminals of the thermal controller. In place of the thermocouple hole, the winding of the heater is “pushed apart”, the place allows. By the way, for uniform heating of the ceramic muffle, sometimes winding is done with a variable pitch - denser at the edges, less often in the middle. In order not to lose a place for a thermocouple after coating, I scored a small clove in the center.
After winding the heater, he made the sides so that the edges of the finished muffle were even. For this, I used slats wrapped in thin “sausage” polyethylene. Secured them with carnations. The slats rested on an empty space under the paper to align them, reeled up a little of the same twine on the void.
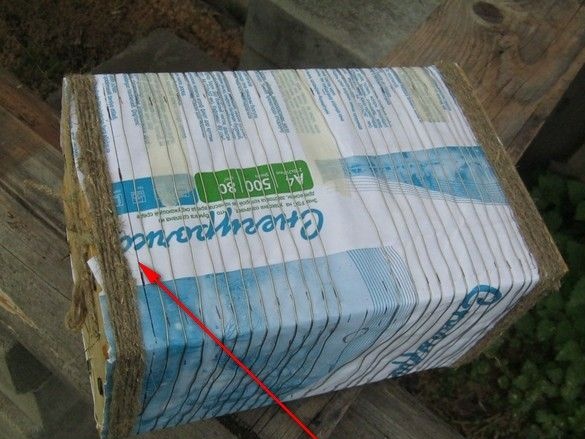
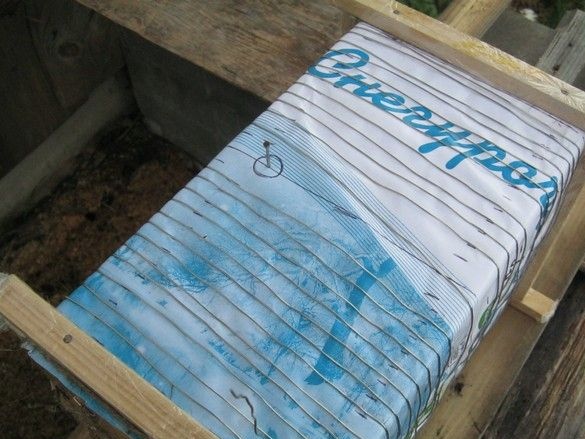
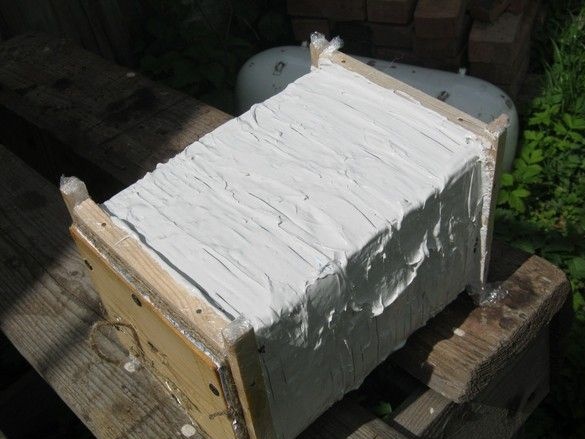
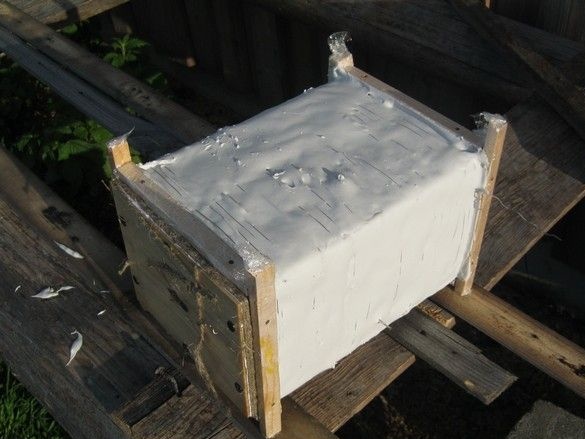
The coating was in two layers. It was carried out with a rubber spatula. The mass itself was prepared from liquid glass and a pharmaceutical baby powder - there was no pure talcum powder. About ¾ glass of liquid glass and 5 bottles of powder of 40 g each were spent on one layer. Powder with stirring was gradually added to a portion of liquid glass until the consistency of thick sour cream. The resulting composition was applied on all four sides, dried horizontally, occasionally turning over. The coating turned out to be very viscous and practically did not drain.
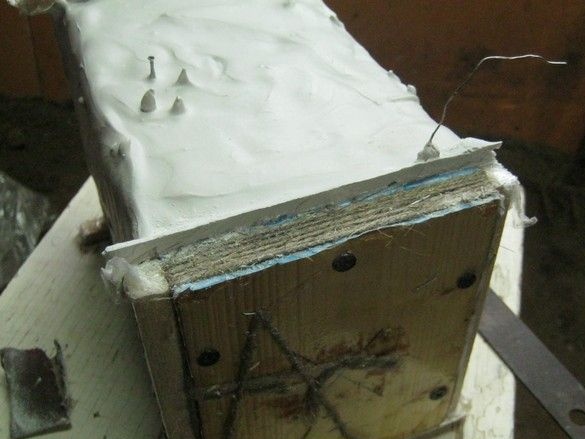
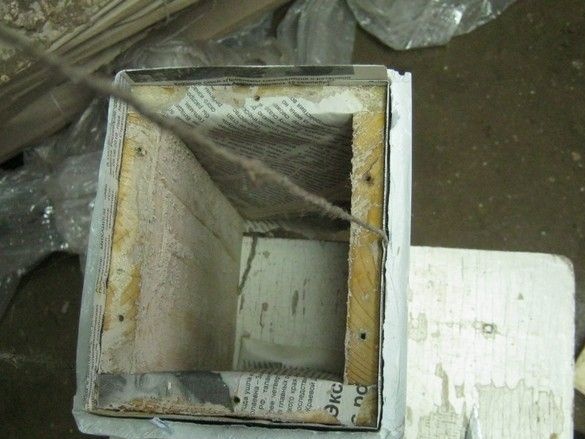
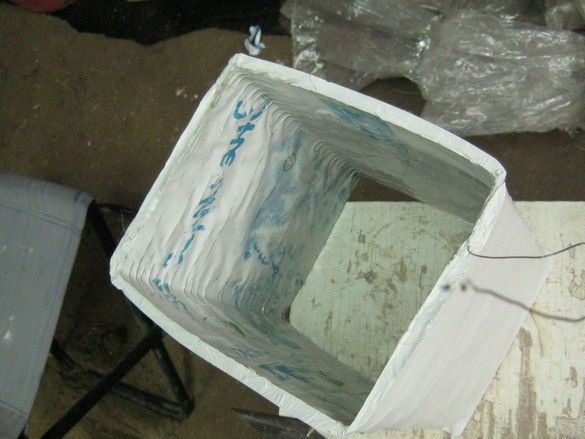
After hardening of the coating of the muffle, he began to disassemble the blanks and remove the muffle. Carefully poked the sides, wrapped the ropes under them. He removed the end walls, and began to rewind the rope between the muffle and the blank. Here an ambush awaited - firstly, the rope was rather rough, its thickness was not particularly equal, often the remains of small slivers were woven into the rope. The worst thing was at the corners. In the end, in order not to damage the muffle, the rope was left alone, and the wooden base was simply carefully knocked out in pieces.
The muffle was not so dry and durable. In the absence of a bottom, lying down, he strove and, if not formed, then come closer to a parallelogram. But after a night spent standing, a little "swam".
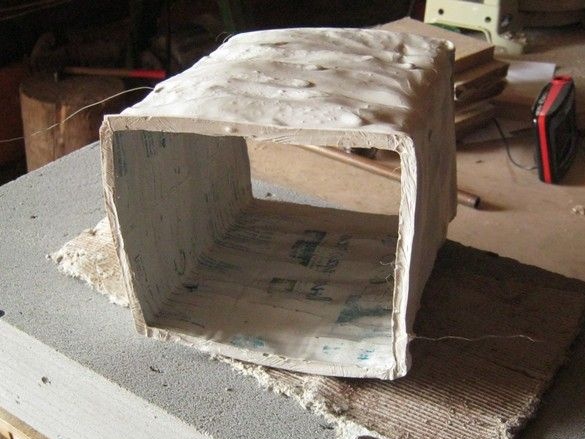
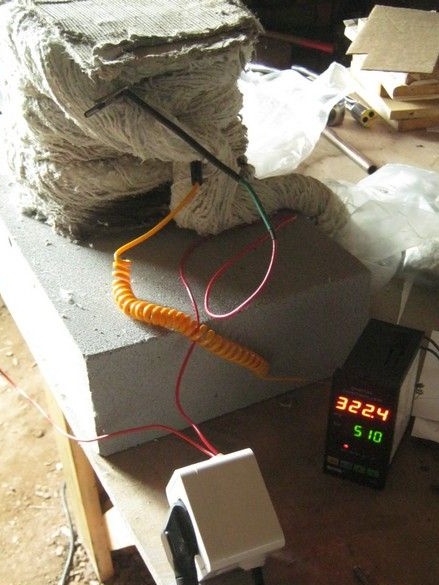
After several days of drying out, I started to turn it on. The muffle put upright on a piece of asbestos cardboard, all this, on aerated concrete brick, wrapped on top with "primary" thermal insulation - a thick asbestos cord. Covered with several more pieces of asbestos cardboard.
I made the first connections through a 1.4kW iron connected in series. The iron reduced the current, its temperature regulator after heating turned on for 5 ... 10 seconds. About once a minute. The result was a very gentle warm-up - in 3 ... 4 hours, the muffle was heated to 300 ° C. After several days of gentle drying, a 4 kW heater was switched on in series. Things went more fun. Above 400 ° C, starch from baby powder started to burn out, and the process had to be transferred to open air.
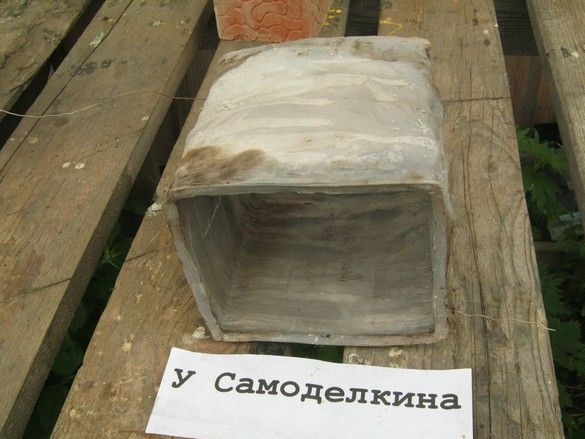
The result is a muffle with very light rigid walls, similar to ceramics. With a slight tapping, a ringing is heard.
In general, the experiment was considered successful - it was possible to make a muffle for the glass annealing furnace, with a working temperature of up to 600 ° C. The costs are minimal. Running materials. For safer use, after drying completely, apply another coat of coating from the inside. Dry similarly. If necessary, a muffle with a bottom can be made similarly.
Work on the bugs.
First of all, you should find pure talc - burn it for a very long time and is unpleasant. The form should be made more rounded, with smoothed corners, then there will be no difficulties with unwinding the rope. With the size of the muffle, I got a little carried away, however, the desire to use the finished form justifies me.For molds and linings it is better to use a dry piece of hardwood and other natural materials - then the initial drying can be done by switching on, carried out directly on the mold, this will save you from deformation. Moreover, you can try to burn out the form - the ignition temperature, for example birch, is 330 ... 350 ° C. At the same time, there is no need for linings and a rope. Since the muffle will not experience mechanical stress upon release, this method is well suited for the bottom version.
1. Brower G. (1985) Guide to Inorganic Synthesis. T.1. Chapter 9 High temperatures.
2. Home-made electric muffle furnace.