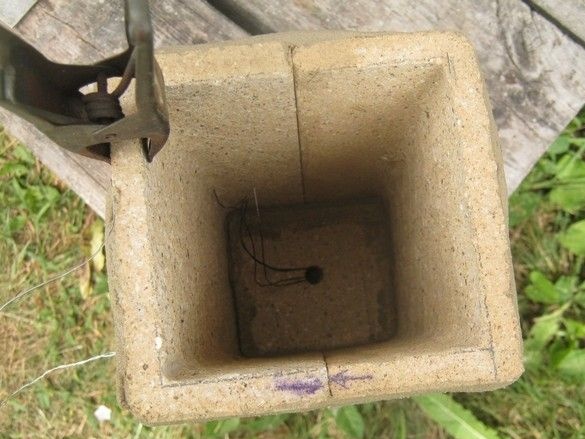
The most complex and crucial part of a high-temperature muffle furnace is, in fact, a muffle with a heater on top of it. For the manufacture of the furnace muffle, metals and ceramics are used. Metals make it possible to achieve a particularly uniform temperature distribution in the working volume of the furnace - in some cases (for example, annealing glass devices) this is very important. Ceramics are often used.
For special laboratory furnaces that operate with small volumes of substances, ready-made ceramic tubes are often used, and it remains only to wind and fasten a wire heater with high-temperature coating. Having equipped the miniature muffle with a casing with thermal insulation, we get a ready-made special furnace. For large volumes of the working chamber, craftsmen use a ceramic tube from a powerful rheostat as a muffle. Making a furnace is similar. In a more general case, the muffle has to be made on purpose. To give birth, so to speak, in agony.
Indeed, the independent manufacture of a ceramic muffle, as a rule, causes difficulties - pottery, just at first glance and simply implies a lot of nuances, and working out the technology is a long-term business. In addition, a dried muffle requires roasting at a high temperature, which is also most often difficult to implement, especially for muffles, no matter how large the sizes.
I propose a “dry” method of making a muffle that does not require special equipment or ceramist skills. The main part of the muffle is a box of two U-shaped parts, each of which is sawn from refractory (fireclay) brick. The wall thickness is about 10 mm. The advantages of the method are obvious - fireclay bricks - factory-made refractory, extruded, calcined, all as required by the charter. The thermal conductivity of fireclay is considerable - much higher than ordinary clay bricks, which is why it is forbidden to lay furnaces out of it - the external walls quickly and strongly heat up, and the furnace becomes fire hazard. Fireclay in wood-burning heating stoves is used only for lining.
When using fireclay bricks as a blank, a whole layer of tasks related to ceramics is removed, which, as a rule, becomes a stumbling block and a gravestone of a conceived design.Cutting bricks, angle grinders with a diamond disc is a much more common skill. In the end, you can practice using cheap clay bricks. The muffle turns out to be quite a decent size - more than 4 liters.
What was used at work.
Instruments.
The protagonist of this action, of course, was an angle grinder with a diamond disk, popularly a “Bulgarian”. Drilling holes in chamotte (for a thermocouple) - a perforator in the drilling mode with a conventional drill. A small hammer came in handy. Be sure to use safety glasses, preferably headphones or an ear plug. Dishes for water. Extension cord (street work).
Materials
Three fireclay bricks. Water.
So.
In the beginning, it should be said that fireclay bricks are sawn much worse than clay bricks, sometimes with ringing and sparks. Water helps a lot - when sawing, keep a bucket of water next to the bucket and, after any small cut, water the workpiece with water. This, among other things, washes away dust and chamotte pieces, which allows you to better see the place of work. But best of all, soak the brick for several days in water. This makes processing easier by an order of magnitude - chamotte is sawn almost as easily as clay brick; periodically watering the place of cuts at the same time will also not hurt.
Power angle grinder and, accordingly, the diameter of the disk. On the one hand - a large machine allows you to wield a large disk, which is convenient to make deep cuts. On the other hand, a small one, with a ø125mm disk, will allow working in some places with one hand (not with deep cuts), it is better to control the tool in case of a likely jamming of the disk. But you have to dodge. Yes, we remember that the “Bulgarian” is one of the most dangerous tools - unlike the others, it has absolutely no emphasis and you should only rely on the hardness of your hands and the corresponding skill - be careful. Yes, the processed brick should be fixed, at least from horizontal trepidations, well, at least with several slats pinned to the desktop.
Marking can be done both on dry brick and after soaking.
I give a sequence of my own actions, for a tool with a saw blade diameter of 125 mm.
A few cuts to the middle of the brick to the maximum possible depth. At a distance of 5 ... 7mm from each other. It is better to cut so that the marking line is outside. The brick turns over and the actions are repeated.
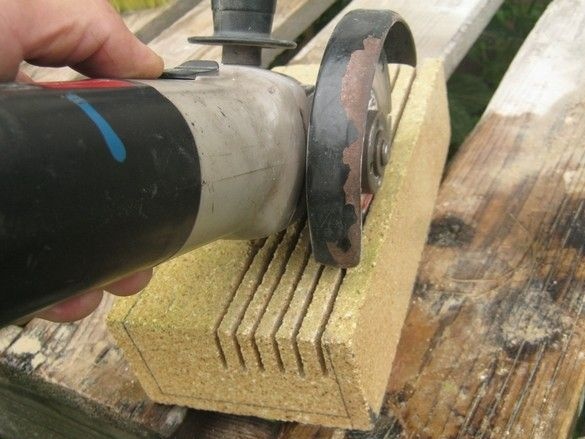
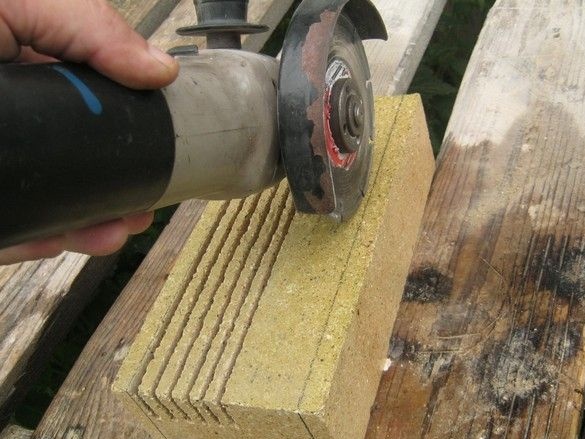
After completing cuts, the brick blank should be washed with water and proceed to core removal. He wielded the lever - the key to the angle grinder went well, but it was also possible with a hammer. The tooth closest to the left wall, therefore, is not worth breaking - the outer wall is slightly thicker than the one being broken, you never know, it is better to carefully with a hammer.
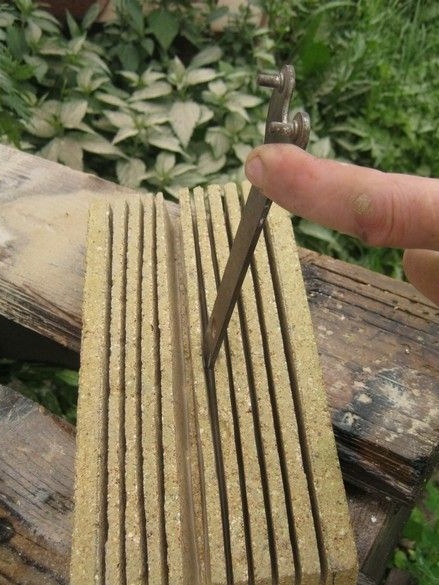
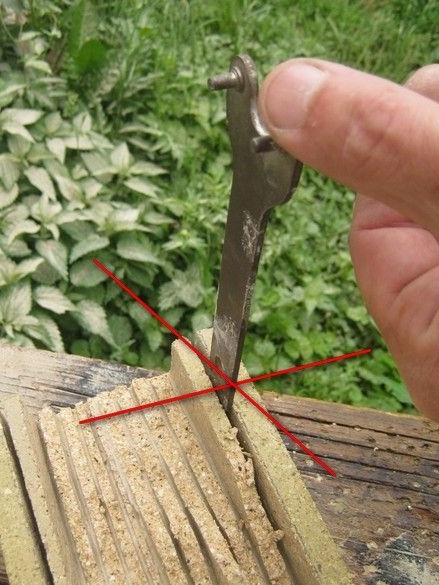
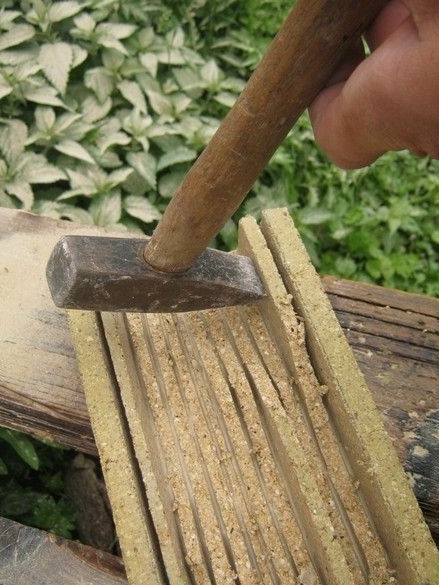
We wash the debris, fragments and saw through the second tier, in the same way. Alas, the gearbox body of the machine does not allow to get to the middle, it has to be cut with oblique cuts. Here, a lot of dust (and in soaked brick - rather dirt) and small debris is formed at each cut, so you have to water it every hour.
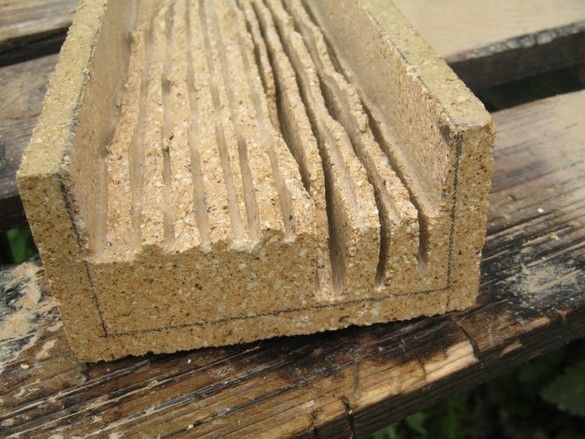
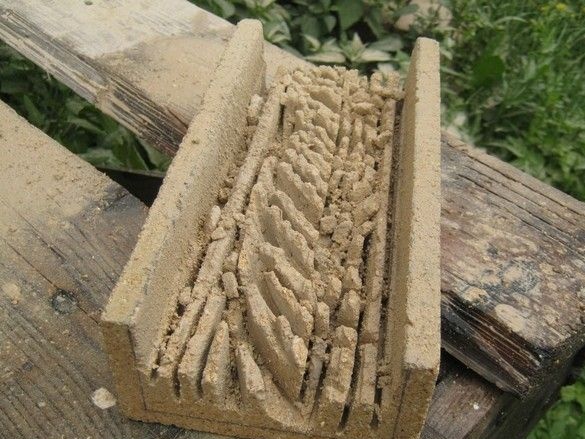
After knocking out the teeth, there are many irregularities that should also be aligned, but not with ordinary cuts,
and with long lateral movements of the machine, approximately so that the lateral surface of the diamond disk works. Do not forget about the water.
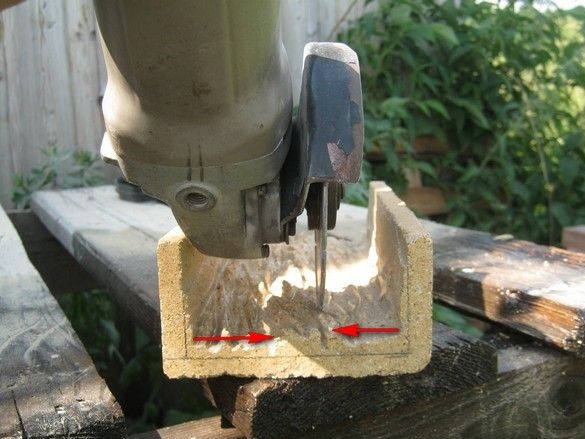
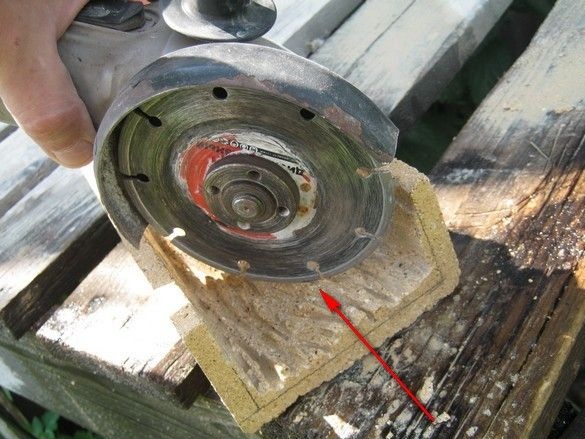
The order, there were thickenings in the corners, they had to be chosen a little differently, and it turned out that there was no way to get into the drive. The problem was solved by replacing a worn-out disk with a new one - the missing 5 ... 7mm was enough.
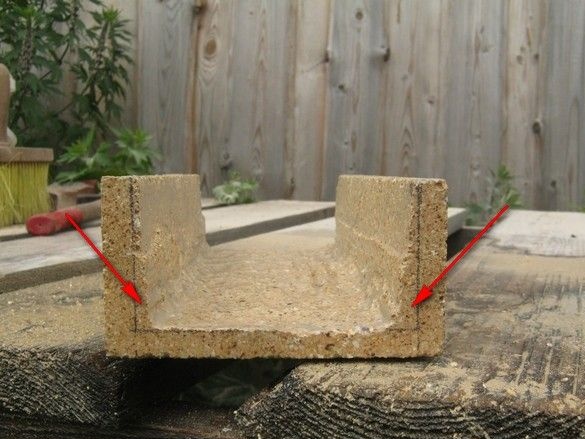
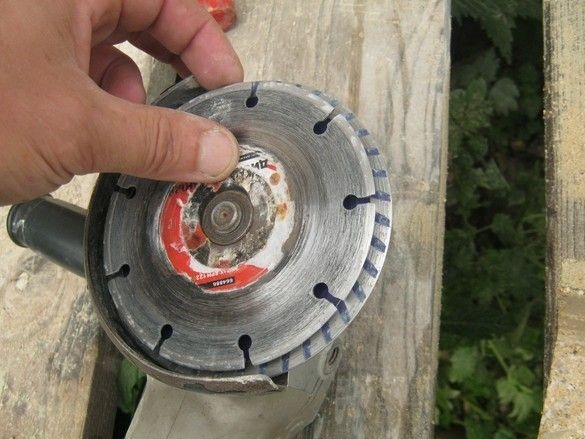
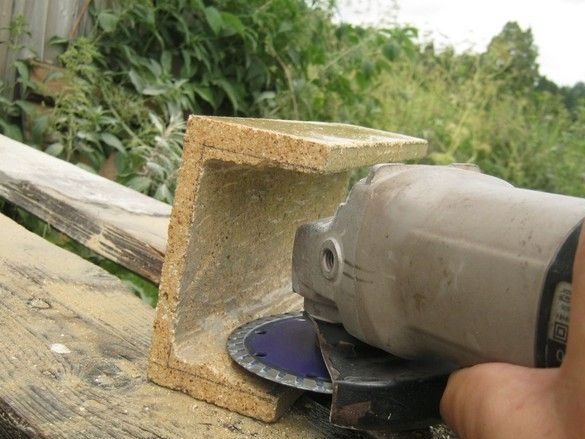
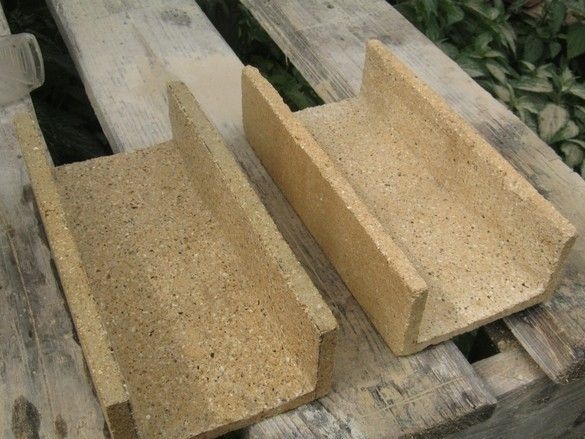
After such exertions, to cut the bottom - a trifling job - a plate about 20 mm thick was sawn out of brick, a “quarter” 10 mm deep was made around the perimeter. At these 10mm, the bottom is inserted into the muffle body.
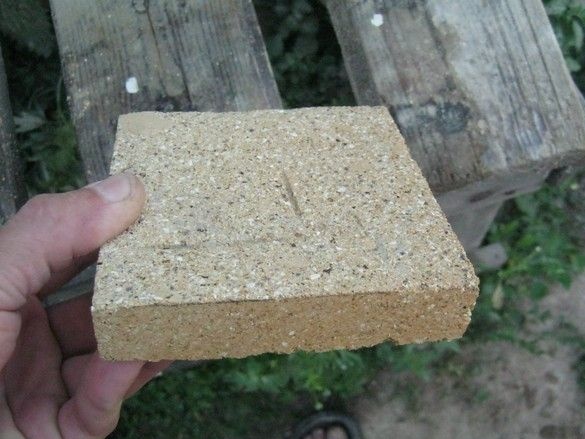
An ø10 mm hole was drilled in the bottom for a thermocouple. As already mentioned - carbide drill (drill).
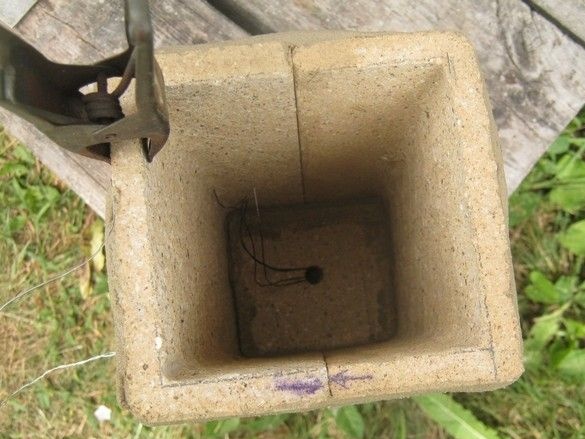
Here was applied the composition for laying refractory bricks "Terracotta".
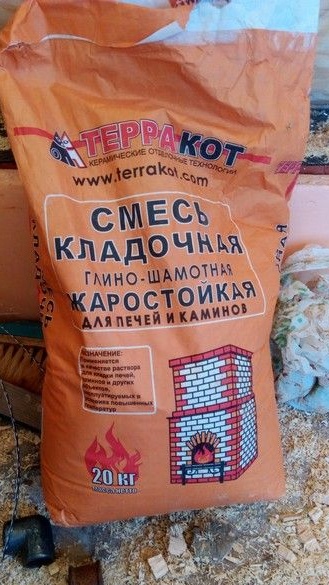
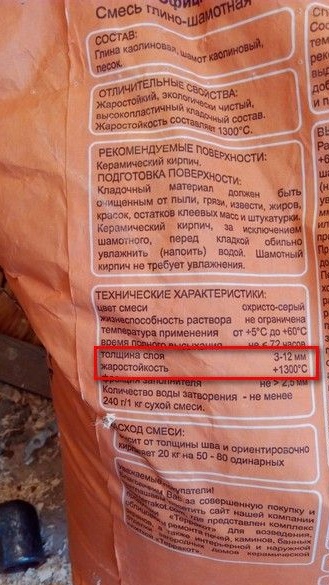
A 12 mm layer without cracking is likely to make the muffle from this composition alone.
The mixture diluted with water is very convenient in work, it was necessary to use it for laying fireclay lining in a wood-burning stove.Here, the bottom of the muffle is installed on it, the mixture is also used to coat the heater. The U-shaped halves did not stick together - there would still be a crack during heating-cooling, in addition, the halves were pulled to death by tight winding of a wire heater. In fact, the bottom also did not have to be glued, a tight fit was enough. The bottom seam also later cracked, but what about.
Conclusions, general remarks
The cut-out, which seemed more terrible than the aspirations, was not at all burdensome, but with careful soaking (for several days) of bricks, and somewhere a pleasant pastime. The muffle turned out, by the standards of high-temperature furnaces, of quite decent sizes. If necessary, a smaller volume (a specialized furnace, for example for lampwork), you can take one "channel", blocking it with a plate.
The temperature of application of the muffle when using a nichrome wire heater is up to 950 ° C, and when using fechrales, it is slightly higher. In the latter case, it should be remembered that contact of fechral with asbestos is not permissible.
There is no special cover in this muffle - it will be made of asbestos cardboard, in the manner of a door miniature oven.
The work described above by an electric tool with cutting-drilling bricks, significantly reduces its resource - abrasive dust, commutator motors. It is very useful, after such work, not to be too lazy to blow the grinder drills with compressed air, even without disassembling them, through regular openings in the case.
In the photo, a muffle with a heater and asbestos winding, extracted for inspection, after a month of operation.
