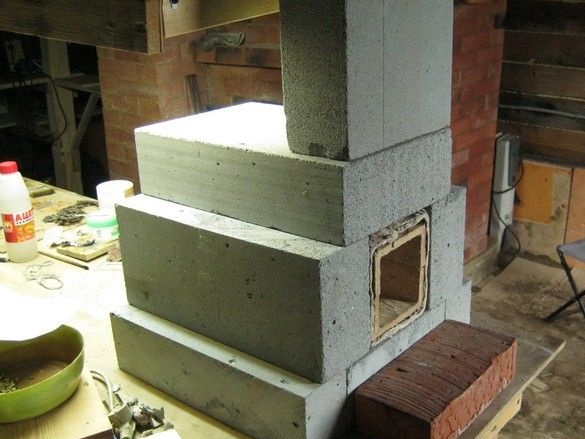
The problem of heating to high temperatures often confronts the master - it can be heat treatment of metals in plumbing, smelting non-ferrous metals for the disposal of scraps or art casting, calcining materials, carrying out reactions at high temperatures. In the glass-blowing business, a high-temperature furnace is also an indispensable attribute - after processing the glass, annealing is necessary to relieve internal stresses, otherwise, the product is highly likely to break.
Glass annealing, as a rule, occurs at temperatures not exceeding 600 ° C, this allows the use of common, non-specialized materials, which greatly reduces the cost of construction. The following describes the manufacture of a prototype of such a furnace. Its muffle is made (sawn) of two refractory fireclay bricks, the heater is a nichrome wire (aligned spirals - spare parts for electric tiles), the main insulation is foamed concrete in the form of ready-made blocks. The design also used materials - a little asbestos cardboard (intermediate insulation compensating for the expansion of the muffle), heat-resistant masonry mixture for furnaces (for coating the wire heater).
The most expensive part of the furnace was the temperature PID controller with AliExpress - a control unit was assembled on its basis.
What was used at work.
Instruments.
For sawing foam concrete bricks, a hand saw was used. Drilling holes in foam concrete (heater leads) - drill bit for metal. To weld the heater leads, a small welding inverter with a graphite electrode was used, but you can get by.
Materials
In addition to the finished muffle, four foam concrete blocks were used. A bit of asbestos cardboard, nichrome wire, a mixture of refractory masonry, related trifles.
Heater
Made of nichrome wire. Power is calculated by methodology. The easiest way is to take a ready-made heater - a new (old fragile) spiral from the electric stove at the appropriate power. The spiral is leveled, its length is measured and according to the geometric dimensions of the muffle, the number of turns and the winding pitch are calculated. The faces of the muffle are marked (step) with a pencil and the heater is wound.To fix the winding pitch and generally sprawling turns, the heater is coated with a refractory composition. “Terracotta” refractory bricks were used here, pay attention to the characteristics.
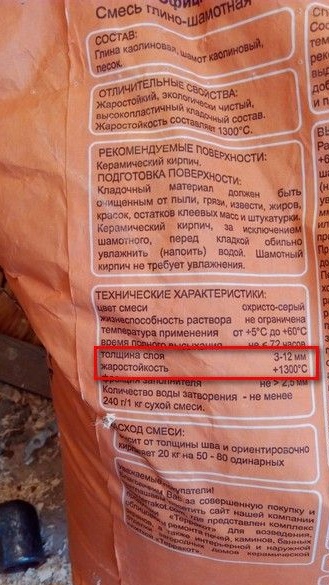
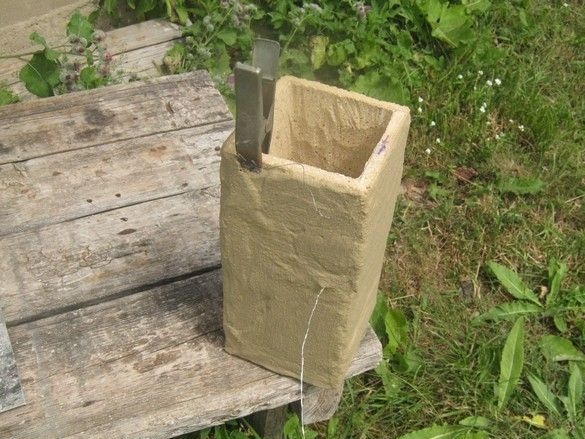
The thickness of the coating layer was about 5 mm, an additional output in the middle of the muffle is medium. Two windings from an electric stove were wound, the winding pitch was about 4 mm. Winders are connected in series. It turned out a lower power value from the recommended range for this chamber volume - something around 300 W / l.
Heater Leads
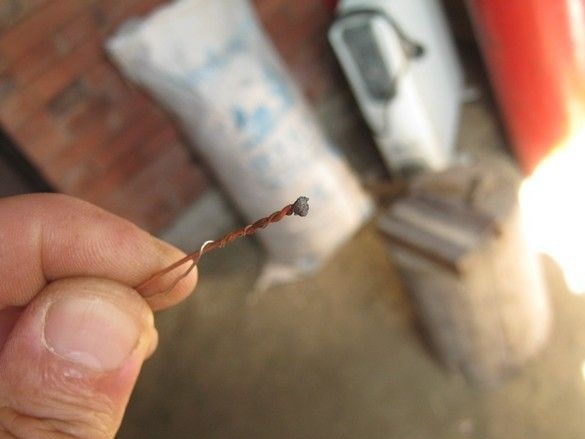
The heater's short leads (nichrome) were welded to the copper wires with a welding inverter adjusted to the smallest current - about 10A. Graphite electrode, from a failed galvanic cell. Flux - dry borax or a solution of borax in water (option - in boric acid).
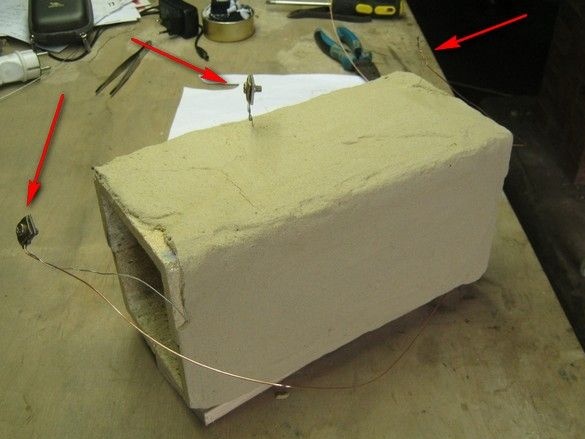
Additionally, the twisted part of the wires was bent by a loop and clamped in part of the screw terminal.
Test, furnace prototype
For testing, the muffle must be thermally insulated. The first option of thermal insulation was whipped up - from a thick asbestos cord. A muffle was wrapped in several layers. The temperature was controlled by a thermocouple (type K or chromel-alumel) - at the beginning, standard, which is part of the multimeter, then connected to a makeshift control unit based on a temperature PID controller.
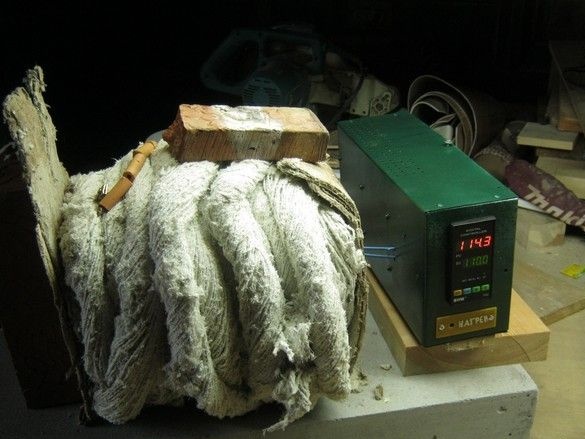
I got a rather short thermocouple - about 300mm. In the photo - its ends are passed through the wall of the control unit and connected directly to the screw terminals of the thermal controller. The muffle and the control unit had to be arranged in a T-shape.
It is better to carry out the first start-up very gradually, so as to smoothly evaporate all the moisture remaining in the materials - it worked like this - heating to 100 ° C, holding for 3 ... 4 hours, 200 ° C, another 2 hours, 300 ° C - 2 hours, and so on.
During the tests it turned out an unpleasant moment - the asbestos cord is “asbestos” only conditionally - on the outside it really had asbestos strands, inside, it was something like cotton wool. All this begins to smoke and collapse at temperatures above 400 ° C, while the “correct” asbestos works up to 800 ° C. It was this cord that let me down when testing the previous muffle - from talc with liquid glass.
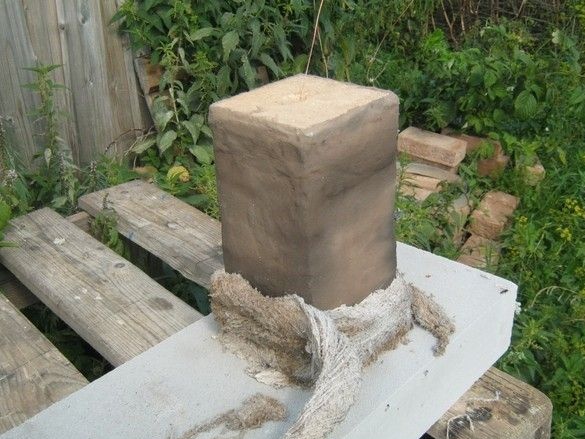
The cord that started to break down removed, at the same time, it was possible to assess the damage to the clay coating of the heater. She was in very good condition, there was one unfortunate crack. As a test thermal insulation, it was decided to use foamed concrete - Yuri Nikolaevich Bondarenko - a scientist, glassblower, astronomer in correspondence, advised to use thermal insulation from foam concrete crumb - it works cheaply and confidently up to 600 ° C. He uses such a heat-insulating backfill for cylindrical ceramic (ceramic pipe from rheostat) and metal muffles.
Since my muffle is with straight walls and corners, it was decided to use whole blocks of foam concrete. Among other things, this made it possible to add, without gluing, from fitted blocks a prototype of a muffle furnace. This makes it possible for some time, resigning to inconvenience during operation, to use the furnace in order to assess the rate of destruction of a material not intended for such temperatures. At the end of the trial period, conclude whether it is worth making a metal frame with a door and an opening mechanism.
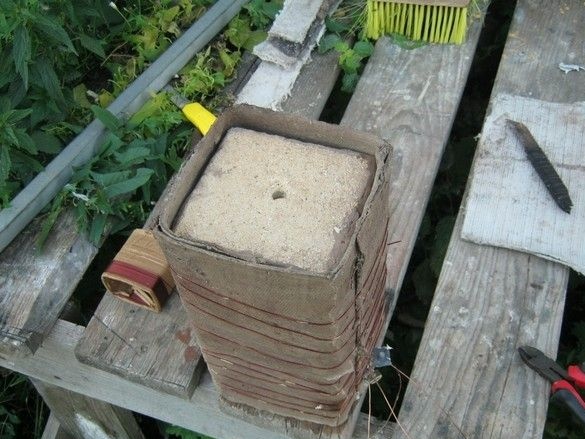
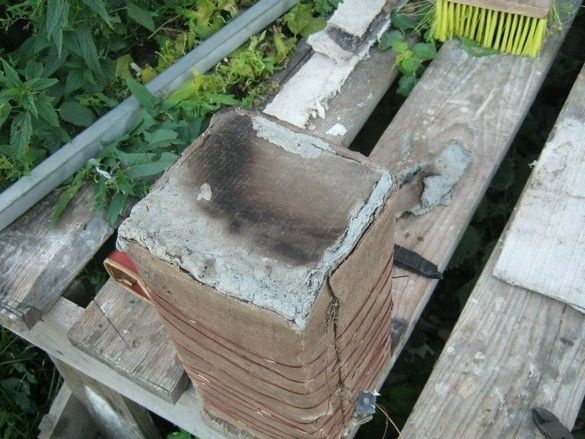
On top of the refractory coating, wrapped the muffle with several layers of asbestos cardboard. This is a very good, inexpensive material, around which the most complete hysteria is unfairly inflated. You don’t need to be afraid of it, you need to respect some of the features of working with potentially hazardous substances and materials. In this case, do not breathe asbestos dust regularly. Any operations on the formation of asbestos cardboard, it is better to carry out, after wetting the material. Having soaked it well, you can practically fashion the necessary details from asbestos. Here, old, second-hand asbestos, of two varieties, was used. Until completely dry, the insulation is fastened with a brace of copper wire.
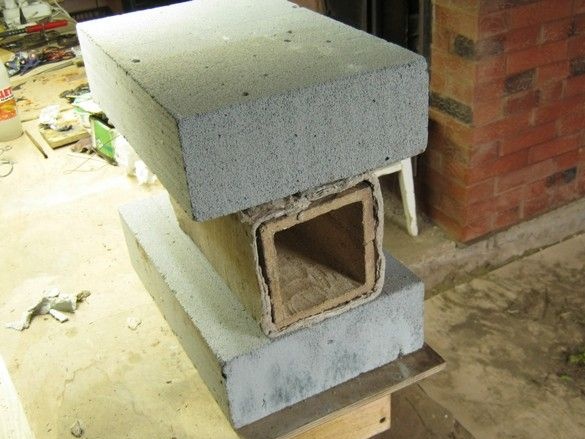
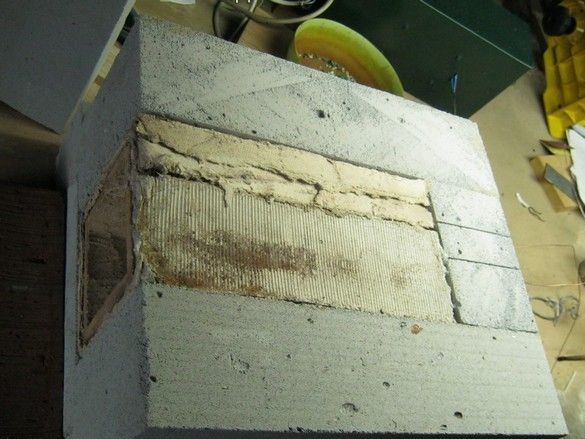
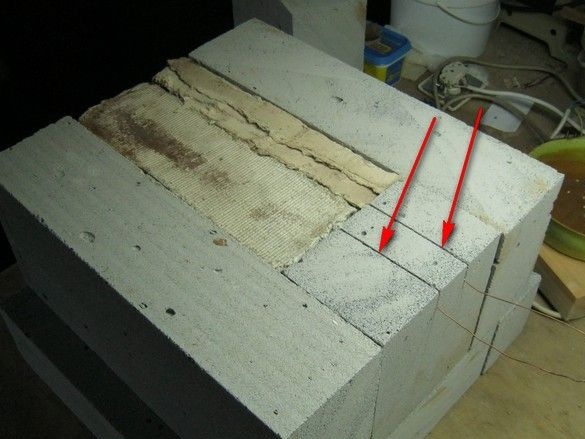
On the end brick, behind, two cuts were made for the copper leads of the heater and a hole was drilled for the thermocouple.
Thermocouple
On Ali Express, a set of three K-type thermocouples was purchased. Shellless, made of thick wires, in special ceramic "beads" with two channels in each. Each thermocouple is about 300mm long. It is rather inconvenient to use them without special “compensation” wires. In order not to wait for a long delivery, I made them, wires, from an extra related (also K-type) housing thermocouple from a multimeter. It is inexpensive and made of very thin flexible wires. The “tester” thermocouple has already been used several times in different places, as a result of all its evolutions, it has significantly shortened, it was necessary, reluctantly to use another rigid one, freeing it from ceramics.
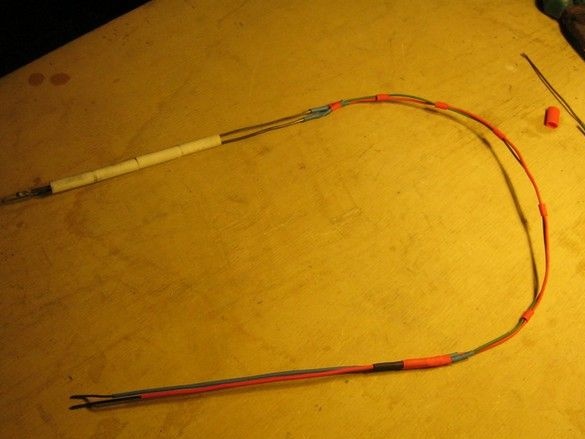
It turned out a miracle as well - the hard end is conveniently and securely clamped in the controller terminals, the soft center allows you to position the control unit in the desired position. Thin wires are embedded in thermotubes, all connections are made by welding according to Bastanov (“300 practical tips”), as well as heater leads - 10A, graphite electrode, drill. Do not forget to connect the wires “in the same way” - chromel to chromel, kopel to kopel. The easiest way to do this is to weld a thermocouple from each pair (at the same time to practice) and connect it to the controller, mark “+” and “-”.
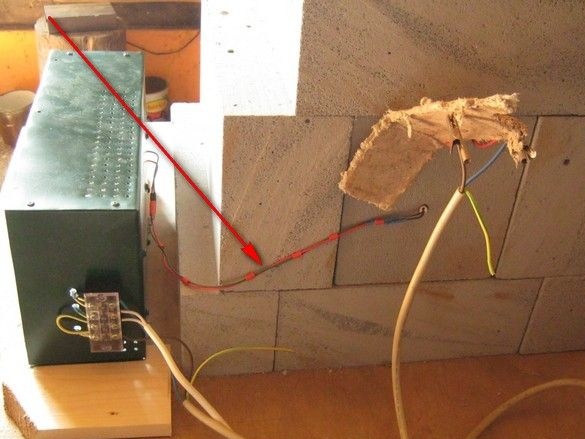
Conclusion, conclusions, errors
The stove in this form was used a little more than a month, almost every day. Compared to the photo, a gap of 40 ... 50 mm was arranged between the bottom of the oven and the table, and for ventilation - moisture was evaporated from the porous foam concrete blocks at the first start-ups. The furnace is simply placed on two wooden bars - at a working temperature of 550 ° C, the outer walls were heated very moderately - not higher than 40 ° C for many hours of operation. Damage to thermal insulation is also insignificant - on the inner surface of the blocks are shallow cracks. In general, the condition is good, you can make a metal frame.
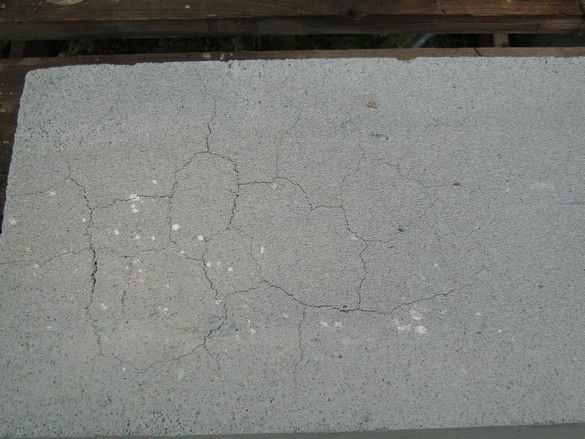
In the photo, the most “destroyed” plate is the top one, it has the only, deep crack, the remaining parts look much better. Thermal insulation was studied periodically and it can be said that its main destruction appeared at the first time of operation, in accordance with the theory of reliability.
As if there were no significant errors, nevertheless, something can be improved. Firstly, the “heating rate” is rather small - the heater power is a bit small. The furnace gains operating temperature, but in two hours with a tail. This was the result of the use of ready-made spirals from electric stoves. There are two of them, connected in series. It can be connected in parallel, but there is no particular need. A low heating rate will make it easier to work with glass, reduces thermal shock, which in our case (the use of cheap general-purpose materials) is very useful. During regular work in the workshop, no inconvenience is experienced.
Heater leads. I must say that the beautiful copper-nichrome compound was never made - satisfactory, but nothing more. Probably the case is in very different materials. Copper-copper or nichrome-nichrome welds much better, and here there is an interesting opportunity - to draw a non-heating output from a heating heater. The conclusion should also be made with nichrome wire, but of a much larger cross section (two or three of which are folded the same). The output resistance will be much lower, it will not be heated, and uniform materials will have to be welded. Well, or do not bother with welding at all and draw conclusions with the same wire as the heater was wound - leave long ends, then close them into ceramic or clay "beads".
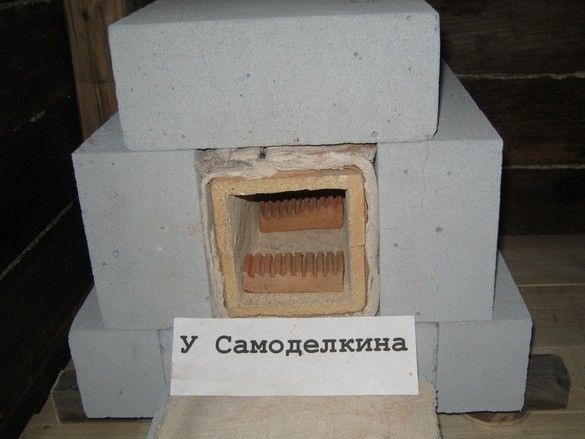