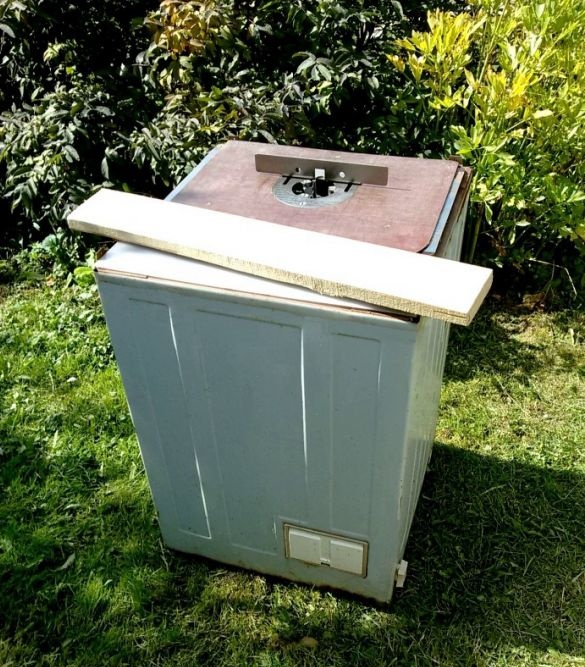
For several years (1997-2003), in the Sarapul Electric Generator Plant, in terms of manufacturing consumer goods, a multi-purpose universal power tool kit, Universal, was produced.
The set, as the main element, includes a two-speed 600W MVB-2V electric drive. The electric drive can be used independently (like a drill when installing a drill chuck) or as a drive in other electrical devices and assemblies.
Depending on the tasks of the consumer, a set was made on the basis of a universal electric drive, which was equipped with various nozzles, devices and accessories.
Various sets of “Universal” power tools were intended for transverse, longitudinal and figured cutting, planing, milling, turning and drilling of various materials - wood, wood materials, plastics and other materials. They were also used for cleaning, grinding and polishing a variety of materials, sharpening a tool during woodworking and other works. All nozzles work only with the "Universal" electric drive.
Kits of household universal power tools “Universal” based on MVB electric drives and nozzles were made in the form of functionally complete sets laid in cases, convenient for transportation and work. Delivered to consumers in the form of functional sets, as well as individual nozzles, devices and accessories.
Since in those years, the choice of inexpensive household power tools for sale was very limited, Universal kits were bought up and used by amateurs to perform a variety of household tasks.
On some sites and bulletin boards, wagon kits are offered today.
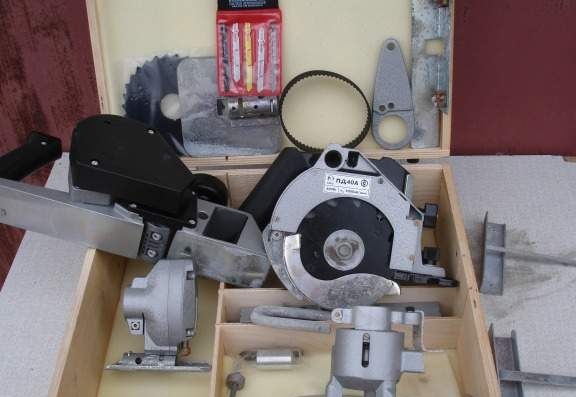
The multifunctional UN-20 set allows you to assemble from the elements included in it: an electric drill, an electric saw with a circular saw, a hacksaw electric saw (electric jigsaw), an electric planer, a milling device.
The kit includes:
- a two-speed drill (electric "Universal" MVB-2V), power 600 watts;
- PD40A circular saw - the diameter of the saw blade is 130 mm, the angle of inclination is 45 ... 90 degrees, the cut depth is 40 mm;
- Planer RB60A - planing width 60 mm, planing depth: with a laying of 1 mm - 0.5 mm; with gasket 0.5 mm - 1 mm; without gasket - 1.5 mm;
- milling device ФПР20 - maximum milling depth - 20 mm; three cutters in a set - 8.10.16 mm;
- V36 vibrator;
- a hacksaw (jigsaw) PN40;
- RD4 gearbox - designed to reduce the speed by four times;
- Drill chuck with key.
Universal electric drive "Universal" is a collector electric motor with a built-in two-speed gearbox. Designed for use in working with nozzles, to perform a variety of operations on metal, plastics, wood and wood materials.
Electric drives MVB-2V, MVB-21A, MVB-21 (ERCHV) have an output end of the spindle with M12x1.25 thread and a landing neck with a diameter of 36 mm for attaching nozzles and accessories of the Universal station complex.
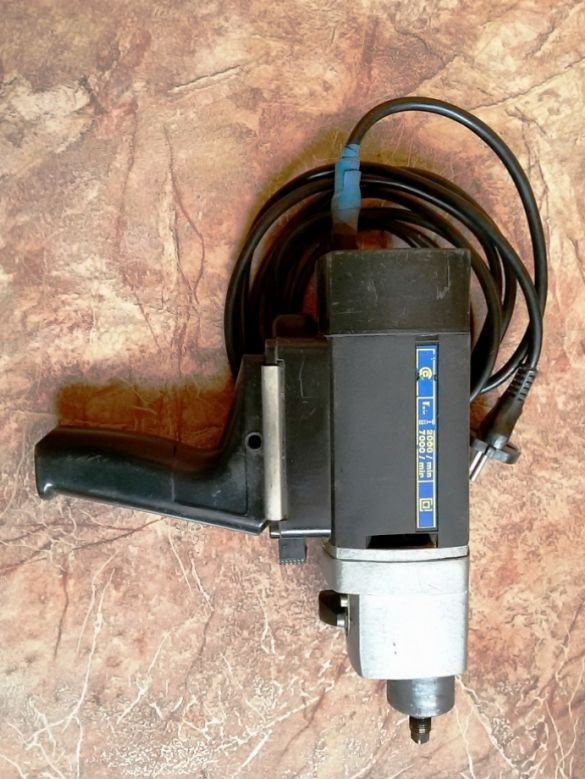
Technical characteristics of the "Universal" electric drive
Parameters \ Type MVB-2V MVB-21A MVB-21 s (ERCHV)
Mains voltage, V. 50 Hz 220 220 220
Power, W 600 650 650
The frequency of rotation of the output shaft at idle, rpm
smooth adjustment
1st speed 2000 2000 0 ... 2000
2nd speed 7000 7000 0 ... 7000
Power cord length, mm 3000 3000 3000
Overall dimensions, mm 255х76х101 255х76х101 255х76х101
Weight, kg 2.5 2.5 2.5
If we return to the impressions of 20 years ago, it irritated the frequent need to reconfigure from one device to another and the small performance of derivative units.
Of course, the drive itself is not bad - compact, has two speeds with speeds of 2000 and 7000 rpm (or smooth adjustment) and good power with its dimensions.
But, for example, in the assembly with a planer, the instrument had an abominable weight balancing. The drive is mounted on the side and strives to outweigh it, it is difficult to hold the planer horizontally. In this case, you need to plan, and the working width is only 60 mm. Similar problems were when working with a circular saw and a jigsaw. The small reference area of the table of the milling device, with a significant height and weight of the drive, made it difficult to obtain accuracy and geometry of processing.
But some time passed and the first branded power tools began to appear. Work with them no longer tuned to work with Universal, and he was a thing of the past.
However, the "Universal" tool is quite working, and these shortcomings are noticeable when working with it, only as with a manual power tool. When these sets are installed in a stationary position, the situation changes. It turns out a compact and relatively powerful mini-machine for the intended processing of materials. Therefore, the owners of an antique, but working Power Station wagon should remember it.
Output characteristics of the device:
Milling depth - 0 ... 35 mm
Cutter diameter - 2 ... 20 mm
Milling device manufacturing
1. We check the completeness and performance of the milling nozzle FPR-20 (see photo).
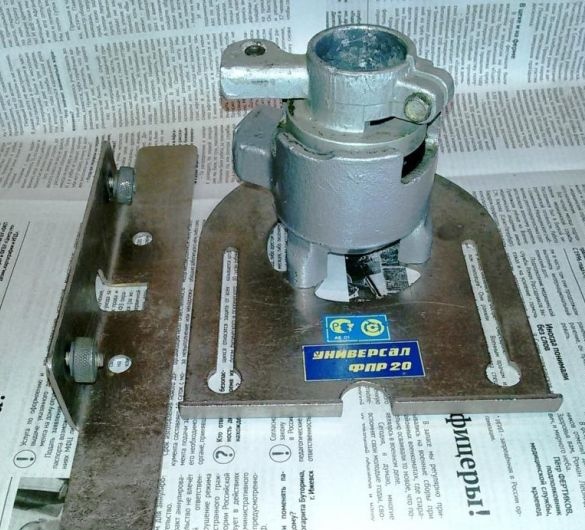
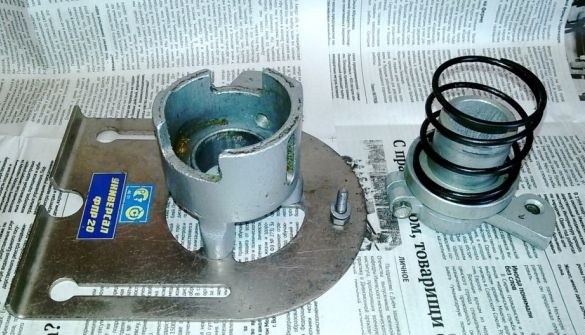
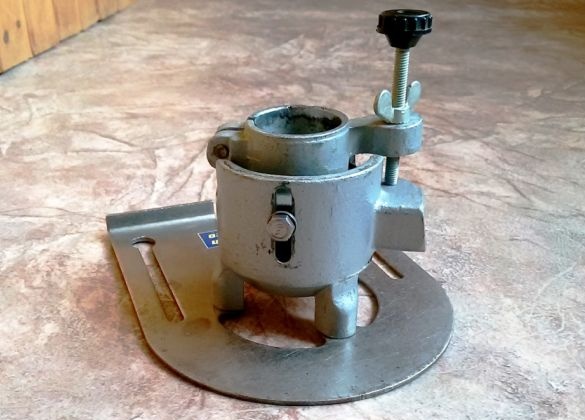
2. Check the availability and sharpening of the cutting tool received when picking the purchased set. According to the documentation, branded cutters are screwed onto the output end of the drive spindle with a M12x1.25 thread. However, finding an additional cutting tool of this design or expanding its range is currently very problematic. If there is such a tool, we prepare it for operation and fix it to the output end of the drive spindle.
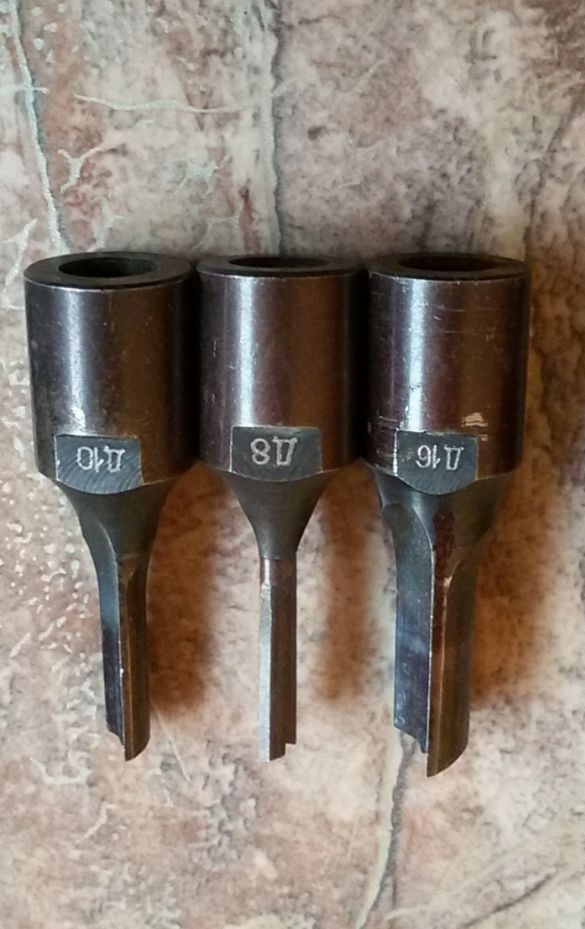
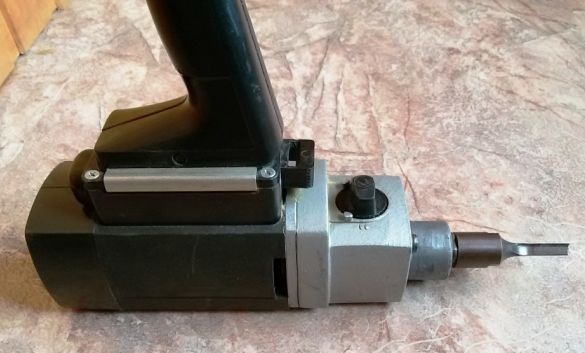
3. To expand the characteristics of the milling device, we will manufacture (order turning and heat treatment) a transition collet chuck for installing typical end mills with a cylindrical shank.
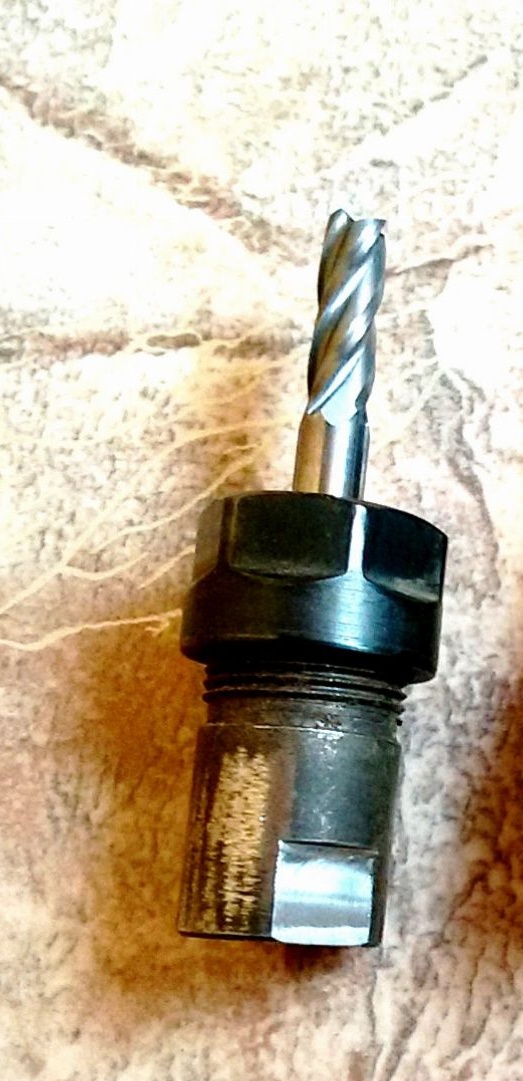
The seat of the collet chuck corresponds to the output end of the drive spindle and has an M12x1.25 thread.
On the opposite side of the chuck, the inner cone is machined to fit the widespread purchase of ER32 collets. For example, the 9PCS-ER32 kit contains 9 interchangeable collets from 2 to 20 mm. https://en.aliexpress.com/item/9PCS-ER32-Precision-Spring-Collet-Set-2-4-6-8-10-12-16-18-20mm.
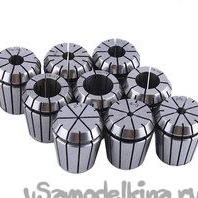
On the outside of the cartridge, the thread for the purchased collet nut is machined.
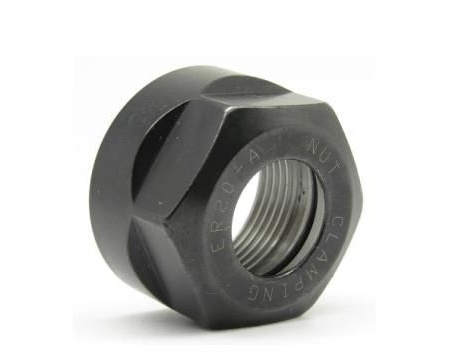
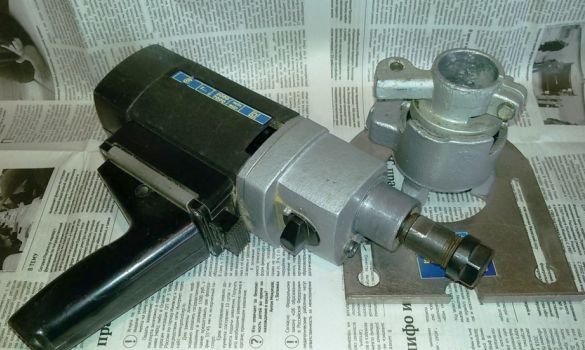
4. We assemble the “Universal” electric drive, a special milling cutter from a set or a collet chuck with a standard milling cutter of the required diameter, a milling nozzle ФПР-20.
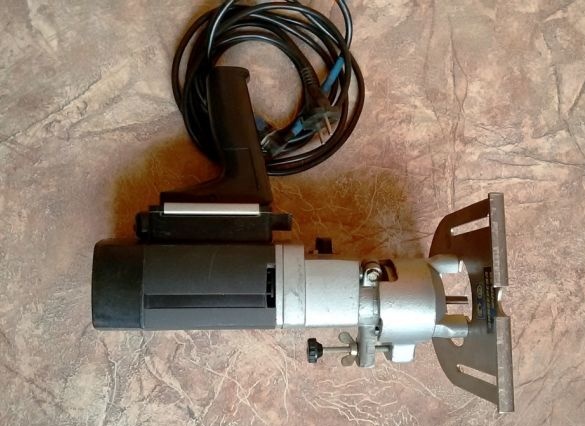
5. We make a table for the milling device. The table material selected is the available plastic (similar to getinaks) sheet 600 x 400 mm in size, 8 mm thick. We mark and cut out in the sheet a window for installing the cylindrical part of the milling nozzle, grooves for adjusting and securing the support, a groove for the existing bend of the edge of the table.
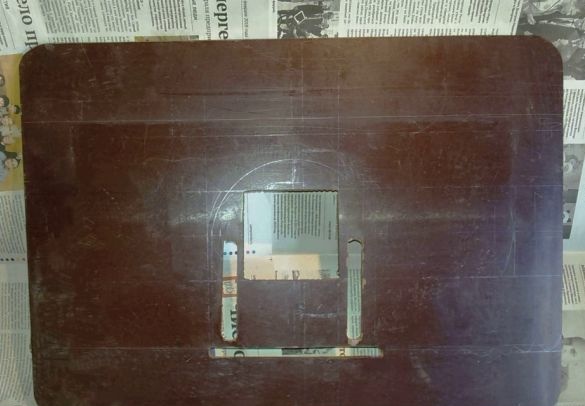
6. Install the milling nozzle on the table. By adjusting the sizes, we ensure the correct location of the nozzle and the free movement of the heads of the screws securing the supports. By editing, we change the angle of bending of the edge of the table of the milling nozzle from 90 to 45 degrees. In the future, this bend will serve as a support for fixing the milling nozzle on the table of the device.
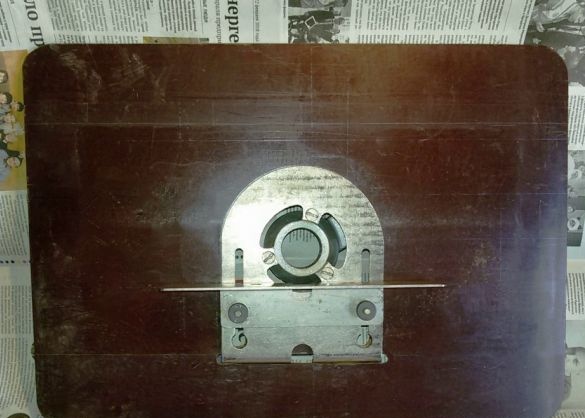
7. Pressing the milling nozzle with the bend to the wall of the groove, in the table of the device, we fix the nozzle using the M5 screw with a recessed head.
8. According to the thickness of the table of the milling nozzle, we select a sheet of PCB with a thickness of 3 mm. We mark and cut out a window in the sheet, according to the size of the table of the milling nozzle.
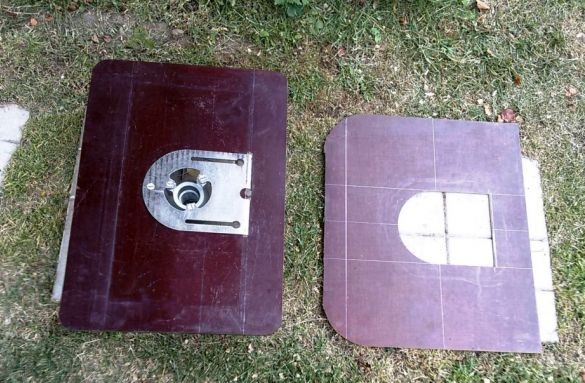
9. Install and connect the table sheets with M5 screws. The plane of the nozzle table must coincide with the table plane of the milling device. The top sheet of the table is shorter than the bottom by 20 mm on each side, for installing metal measuring lines there. They will be necessary when processing long parts and replacing the standard support with another support - along the length of the table.
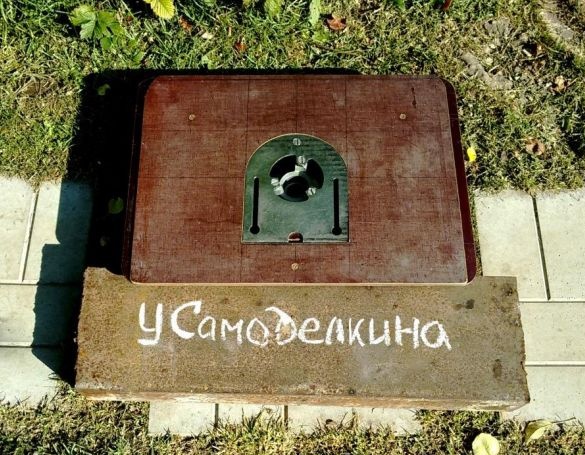
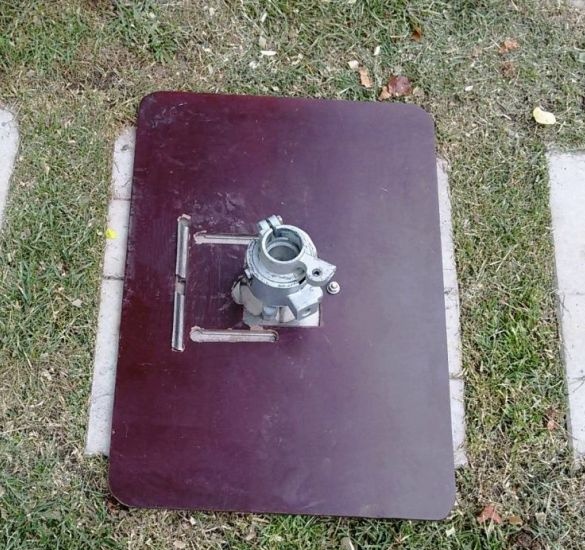
10. We assemble the milling device completely.
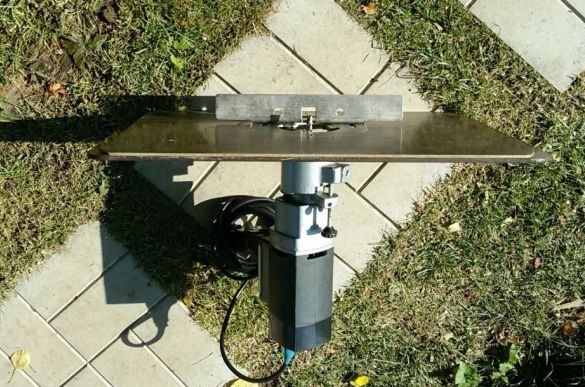
11. As the case - the stands of the milling device, in the author's version, used the case of a former washing machine. This box-shaped case has a small weight, sufficient rigidity, ergonomic height, two wheels and handles to facilitate the movement of a mini machine, a box to accommodate an external electrical power wire. Inside the case, in the future, a vacuum cleaner will fit freely.
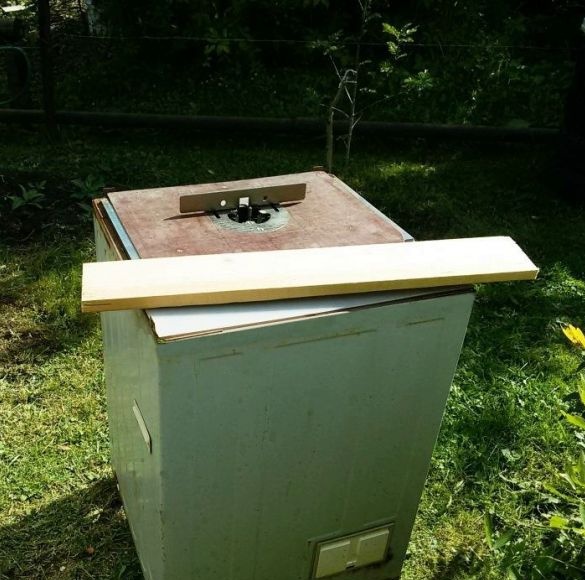