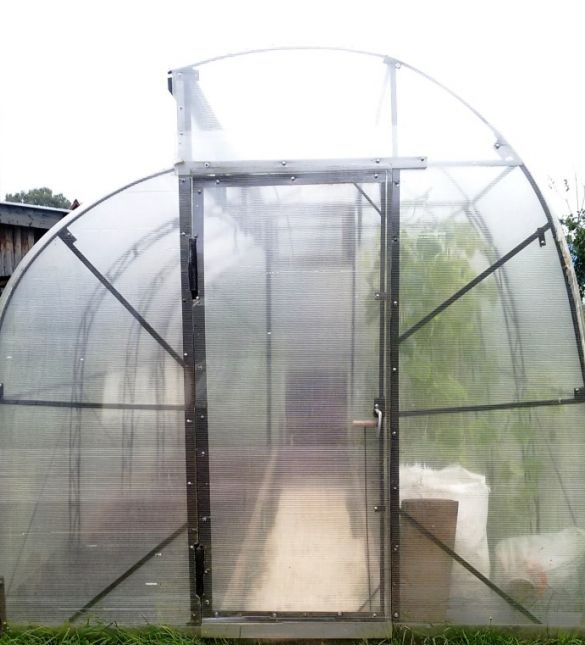
Today nobody argues about the benefits of modern greenhouses made of polycarbonate. The industrial greenhouse has a relatively light construction, easy to operate, quickly assembled and installed. However, it does not always have sufficient rigidity and in a snowy winter it can crush it at the first warming.
The previous Mitlider company greenhouse was made of (very) thin-walled square and rectangular pipes. Its design was considered (according to documents) reinforced, but the strength of the source material did not inspire confidence and in winter, when warming, I had to visit a site to clean the greenhouse from sagging snow.
Therefore, when there was a need for a second greenhouse, I decided to make it myself. The Mitlider greenhouse was structurally selected, its design and ventilation system showed themselves well in past years. In addition, it became possible to practice welding.
As a workpiece for the arches of the greenhouse, I used the available steel strip 5 x 30 mm, profiled for rigidity on the crescent section.
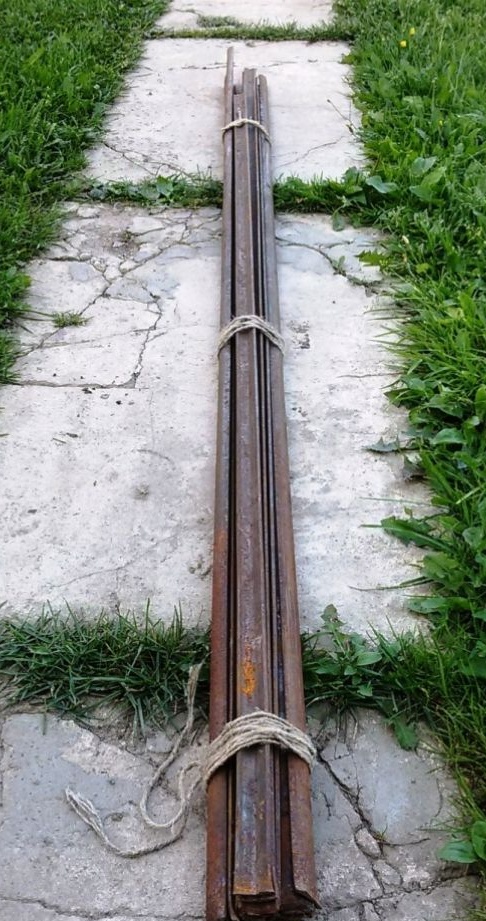
After the manufacture and assembly of the greenhouse, such a design was obtained.
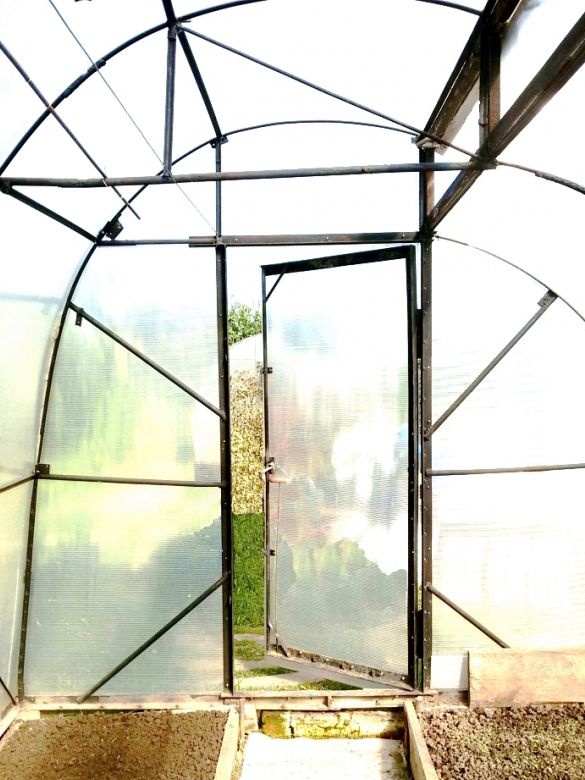
Using a steel strip gave some advantages. This is the absence of problems when bending the arc (as opposed to bending pipes), a simple and reliable connection by welding is possible, and the structure is lightweight. But in the end, after assembling the greenhouse, a drawback also emerged - insufficient rigidity of the bearing arches of the greenhouse. Under my weight on the upper crossbar, the middle arcs are slightly, but bent. Apparently the large length of the arc affected (total length 6 m).
But I did not want to visit the greenhouse in winter to clean it. Therefore, I had to remove the sheets of installed polycarbonate from the greenhouse and begin to finalize the design of the manufactured greenhouse.
If desired, most of the greenhouses can be strengthened and refined similarly to the proposed option.
1. Increasing the rigidity of the bearing arches of the greenhouse. Manufacturing technology.
For each half of the medium bearing arcs (ribs) of the greenhouse we produce arcs - understudies. The material and shape of the double arcs corresponds to the main arcs. The groove of the strip profile on the main arc faces the inside of the greenhouse so that the sharp edges of the strip do not crush polycarbonate. When bending, on the backup arc, we position the groove towards the groove on the main arc.
From the remnants of the strip, we cut for each of the arcs under development 10-12 jumpers 60 mm long.
We position the corresponding duplicate arc parallel to the main one. We distribute jumpers evenly along the arc. We install jumpers in the grooves of the strips, between the main and newly installed duplicate arcs and weld them.
By segments of a bar with a diameter of 6 - 8 mm, we connect by welding, alternately, the opposite ends of the jumpers. As a result, a farm-like construction was obtained. See photo.
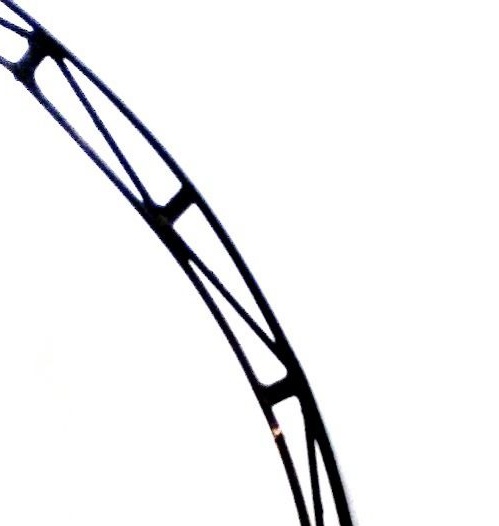
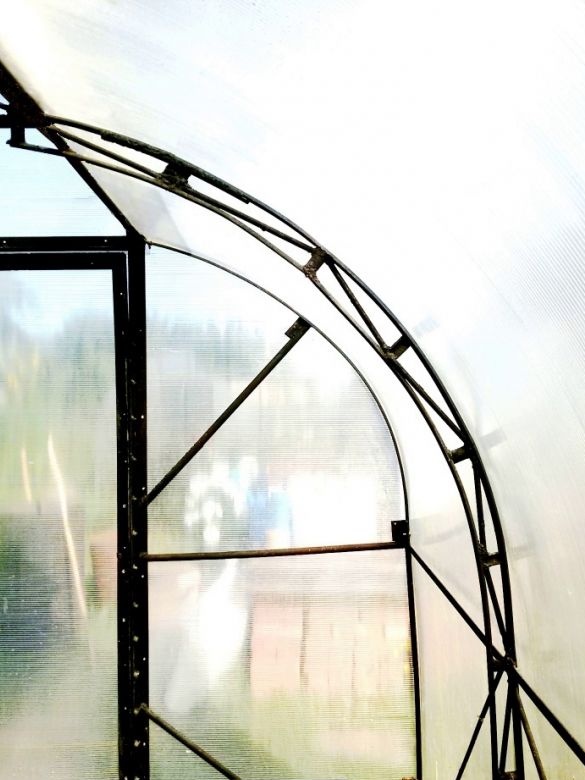
We will repeat the similar work on the remaining halves of the middle bearing arcs of the greenhouse.
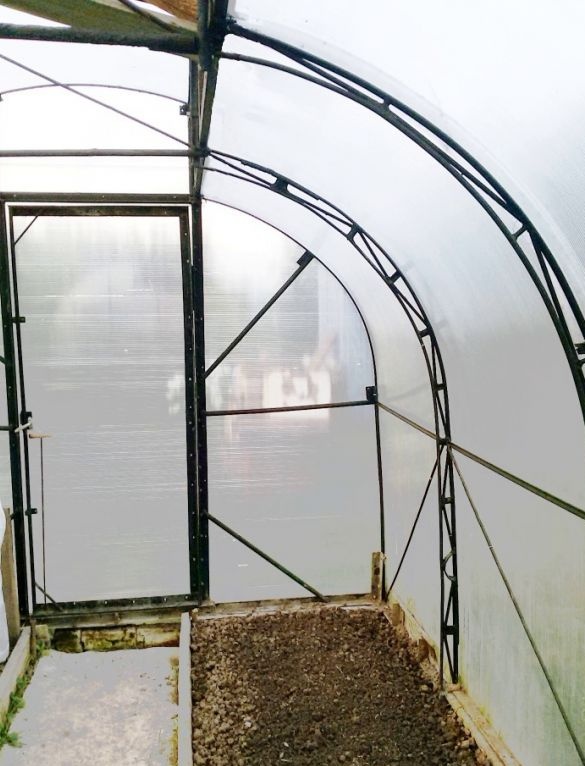
In my case, to refine the design I used the material at hand, I did not use the calculations of sopromat, I selected the sizes intuitively. Significant expenditure of resources and time was not required when finalizing the design, but the strength and rigidity of the greenhouse increased significantly. Under the weight of two people on the upper crossbar, on any of the middle arches, the deformation of the greenhouse is almost imperceptible. The strength of the end walls is provided by additional elements. The longitudinal rigidity of the structure and the protection of the lower part of the greenhouse from being forced through by snow is ensured by diagonal ties from a bar with a diameter of 8 mm. See photo.
2. A device for opening the windows of the greenhouse.
Due to the fact that the windows of the greenhouse are located high under the ceiling, their opening, fixing and closing require their own fixtures. In addition, when closed, the window must be closed tightly and not open from drafts. And in the open state, it is securely fixed and does not close under the influence of wind.
Furniture door hinges help to solve these problems in a complex way, if you install them on the window leaves, instead of window hinges. In the greenhouse shown in the photo, the furniture hinges of the first, all-metal, structures were used. Each hinge has two powerful coil springs. Therefore, two such hinges reliably fix the window in both extreme positions (open and closed), in all weather conditions. This is also facilitated by a very lightweight window frame design.
The window leaf is made of the same polycarbonate as the greenhouse. The frame at the window is missing, except for the upper bar. To it, with the help of screws and washers, a polycarbonate sheet of the required size and two hinges along the edges of the plank are attached. The drowning part of the hinge is located in a blind hole made in the bar. The counterpart of the hinge is attached to a wooden frame common to all window leaves. The material for the window frame and strip is a wooden rail 30 x 50 mm.
Today, there are many designs of furniture hinges, but the principle of operation is the same. Therefore, it is possible to use any, but it is advisable to choose those that have a more rigid spring and a good anti-corrosion coating, since they will work in a humid environment.
from two sections of the profile. One - a pivot arm, mounted on an axis fixed to a suitable support near the window leaf (in our case, this is the upper transverse beam of the greenhouse). The lower end of the lever serves as a handle to open the window. The upper end of the lever is connected by an axis to the intermediate link. To do this, at one end of the link, offset from the edge by 10 ... 15 mm, drill a hole for the axis. We connect the other end of the link with an axis (cotter pin or screw with nut) with a piece of an aluminum square fixed on the window leaf (see photo).
The material of the levers is metal U-shaped sections of the profiles (it is also possible to use aluminum squares), of those found in the household or in a specialized furniture store. The width of the profile shelves is negligible and is limited by strength.The length of the mechanism arms is selected locally, depending on the size of the greenhouse structure. The restriction, on the one hand, will be the height of the bottom point of the handle of the mechanism in the closed position - do not touch the head when passing under it. On the other hand, the ability to conveniently switch the lever to different positions. In the above design (in the photo below), the ratio of the shoulders is approximately 1: 1 (: 1).
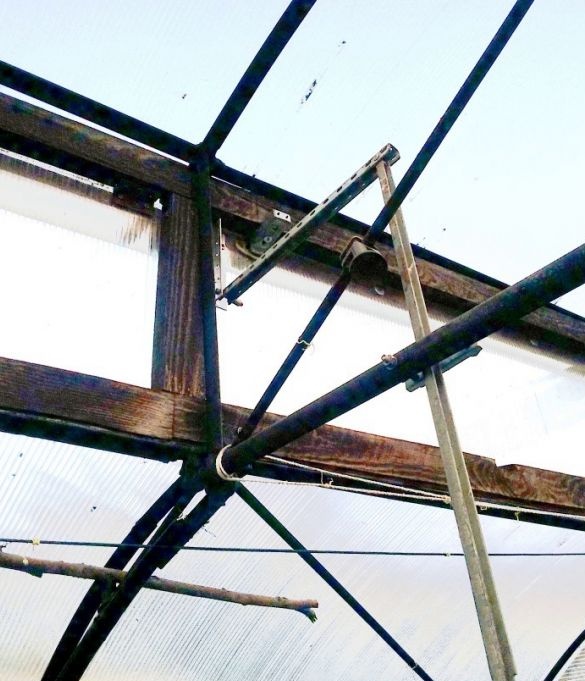
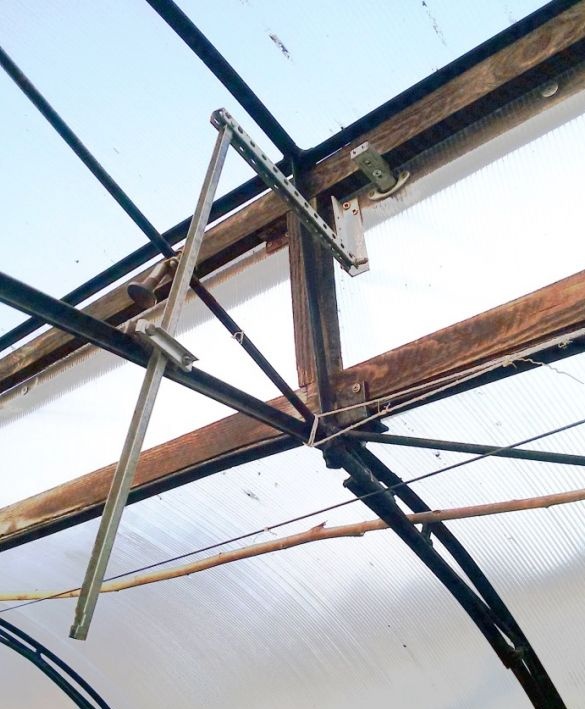
When the vents are fully opened, the levers turning turn to stand in line. With a slight further rotation, the lower pivot arm abuts against the upper link, due to a slight displacement of the axis on it. At the same time, the design becomes stiff under load from the side of the window, and will not allow it to close even under heavy loads, up to breakage. This position of the mechanism is supported by the hinge spring.
When the handle of the mechanism is turned back to “close”, the axis easily passes the “dead center” and the window is closed under the action of the hinge spring. Additional springs in the mechanism are not required.
If it is necessary to partially open the window, we add a movable adjustable emphasis to the design of the mechanism, which pivots the pivoting lever when closing the window. In the photo, it is located on a diagonal screed near the pivot arm.
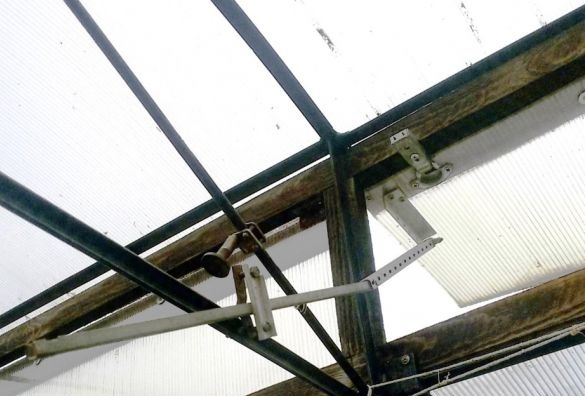
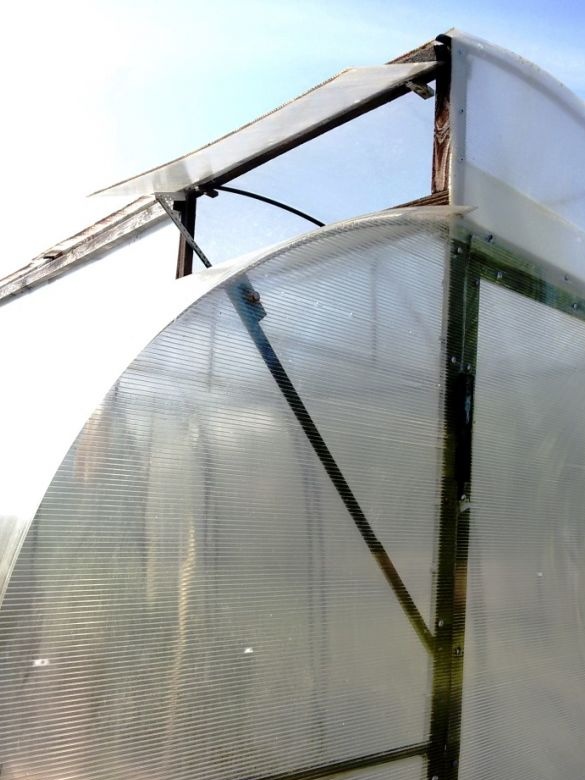
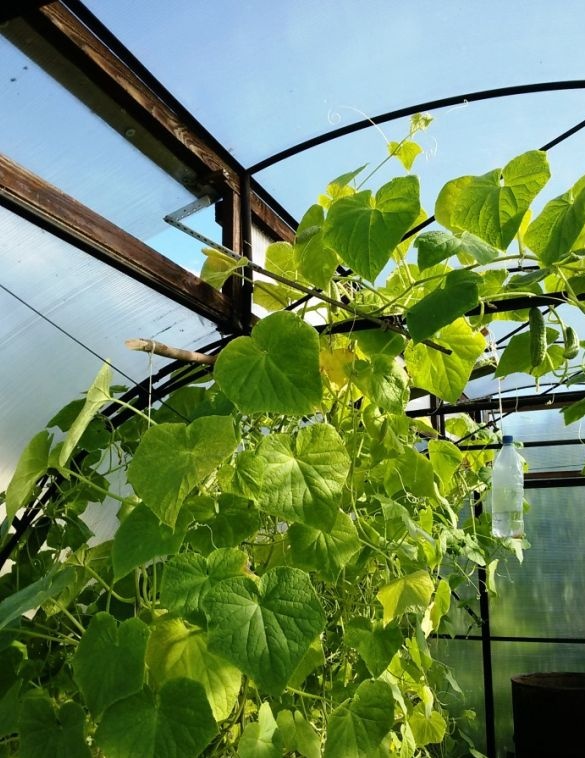
3. Mechanization of opening the middle window
The author's version of the greenhouse consists of four sections one meter long. The window opening mechanisms described in clause 2 are located on two extreme window leaves one meter long. The middle window leaf of a similar design, two meters long, can be equipped with the same opening mechanism or modified to automatically control the temperature in the greenhouse.
Many homemade options for temperature control devices have been described, I propose to make one of them.
The design of the top link of the mechanism and its fastening remains the same. The swivel lever with the handle is replaced with a plate (a piece of board), which is fastened through the window hinge to the bottom of the frame. Under it, we also fix the second plate. See photo.
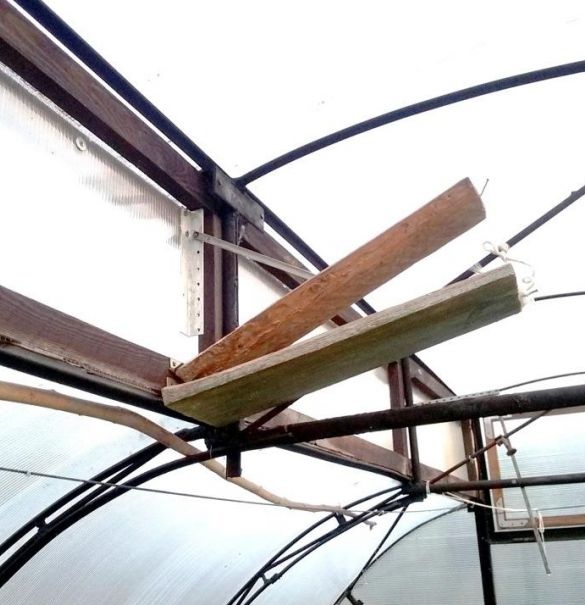
We fix the free end of the bottom plate to the elements of the greenhouse, with the possibility of further height adjustment. To the upper movable plate, axis, attach the free end of the upper link of the mechanism. As can be seen in the photo, in the aluminum squares located on the window and the top plate, there are a number of holes. They are designed to adjust the sensitivity - the opening size of the window depending on the movement of the upper plate. This can be done by changing the location of the axes of the upper link in the openings of the squares.
Having placed between the plates a control element that changes its size depending on the temperature, we will force the window to open when the temperature rises, increasing heat transfer and vice versa.
As a control element, you can use the rubber chamber of the ball or wheel, a thin-walled plastic five-liter capacity and other home-made or proprietary devices.
To exclude the pitching of the ajar window in the wind, an additional load is suspended from the upper plate. It may be a bottle filled with water to adjust weight.
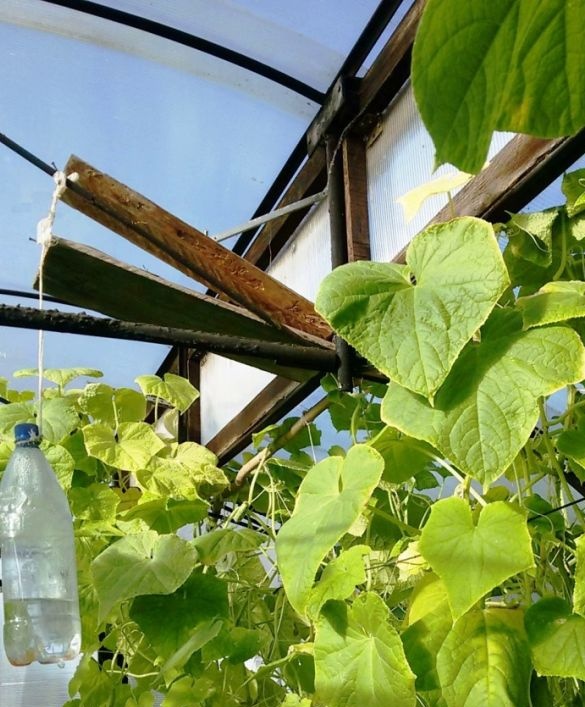
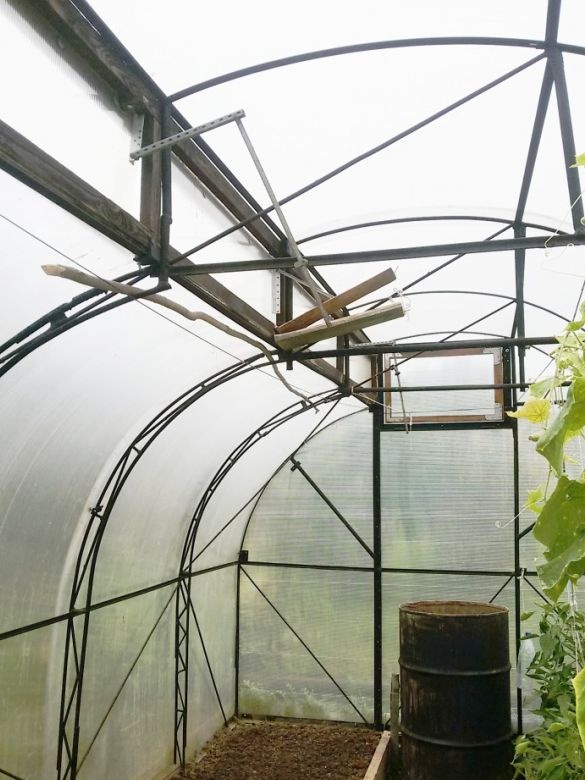