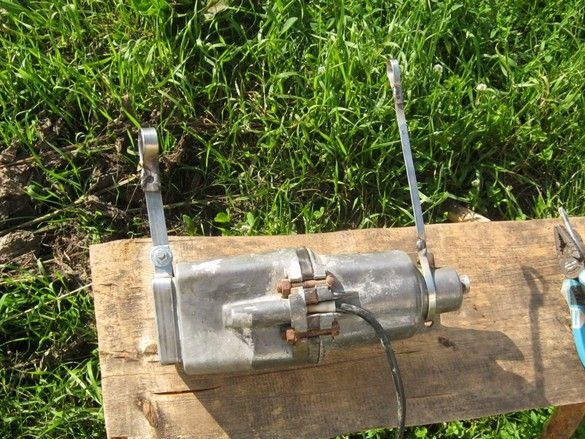
Equipping the winter version of the water supply system from our own spring, I had to pay attention to the pump with the nearest communications. The pump is factory vibrating. Some improvement, or rather, adaptation to their own needs, its installation in an existing small capacity and a standard suspension, and I would like to offer the attention of the venerable public.
Prelude
The vibration pump is a wonderful gizmo - the simplest maintenance-free, highly reliable design with a minimum of moving parts, a completely underwater working position (good cooling, does not freeze in winter). Low probability of electrical breakdown (per housing). Simple design provides moderate cost. The characteristics of the pump cannot be called outstanding, but they cover most of the needs in the farm.
The pump is an open-core coil connected to the network. An alternating magnetic field distorts, with a network frequency, an anchor mechanically connected to an elastic membrane. Water is sucked through two valves and is supplied to the outlet pipe.
The pump coil is filled with a compound in the wide bottom of the pump housing. For normal operation of the pump, it must be immersed in water for cooling. It is worth saying here that there are pumps with an upper water intake and a lower one - the latter are convenient only for work involving pumping water. In other cases, pumps with an upper intake of water are preferable - they can be suspended in less deep containers, wells - less trash is sucked from the bottom, moreover, it is more convenient to operate such a pump - it will not be able to pump water out of itself and burn out.
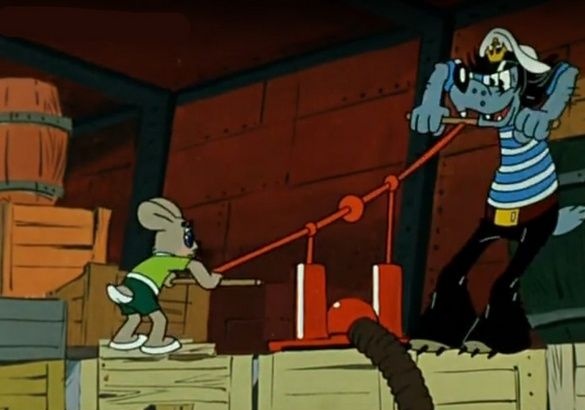
Formulation of the problem
Our source is a spring with a container for water intake. Capacity, represents a dug piece of a ceramic reclamation pipe with a concreted bottom. The depth and generally the size of the tank is small, it is located, although on our site, but in a kind of lowland, in winter it is covered with snow, it’s difficult to go to the spring at this time of year for inspections, preventive repairs, and repairs.
A small volume of water tank and all-weather work require well-known measures to prevent freezing of the water supply. We made our batch water supply system, completely drained between the work.The terrain also contributes to this - the spring is pretty much lower than everything else.
Our main pressure pipe is insulated and buried in the ground, but what about. There was only a small area left above the ceramic container with water. The pipe should be molded so that any of its length was directed downward, towards the drain of water. At a shallow depth of the "well", comparable to a large pan, the standard installation of the pump - a vertical suspension, although possible, leaves an uncomfortable "not drained" hose ring above the surface of the water (freezes).
For a convenient, "merged" installation of the pump, we used its non-standard suspension - horizontally. At the same time, a plastic pipe and a piece of a transitional silicone hose are formed by a sort of descending half-ring that fits perfectly into our container. He molded a plastic pipe, heating its individual sections with a building hairdryer. It is not necessary to bend one place at a large angle - folds are formed that reduce the pipe section, it is better to make several small bends. A silicone hose is installed for vibration isolation and ease of maintenance. Compared to garden irrigation, it does not harden in the cold (in cold water) and allows you to pull out the pump for inspections without wriggling a hard plastic pipe.
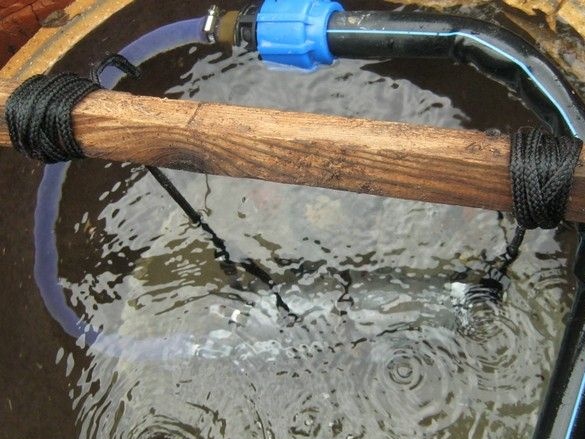
To take advantage of the “upper fence”, the pump in the water column is located like a swimmer - with his head slightly higher.
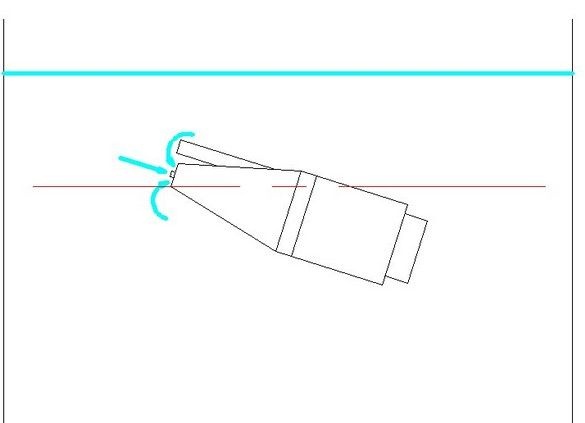
In the event of a water outage (for example, a blockage in the supply pipe), the pump coil will still remain in the water.
Pump suspension
The standard suspension of the pump is made in the form of two tides-ears on a silumin body and involves only vertical installation. Moreover, the inner part of the ears is rather rough and during operation of the pump (vibration) frays short suspension ropes, even if they are reinforced with thermotubes, as suggested in the instructions.
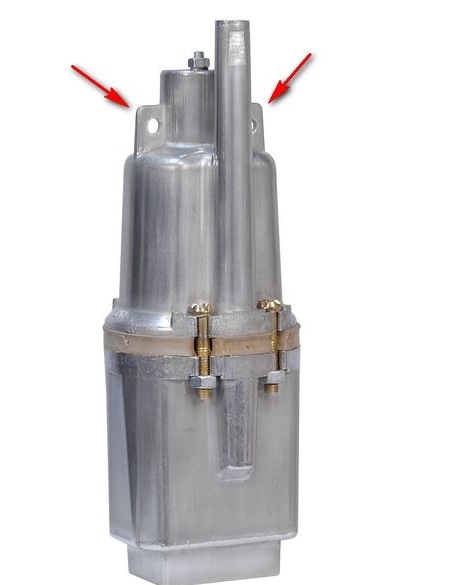
Probably, with a long rope suspension (well, pond), a thick elastic rope softens this effect. It is possible to reduce grinding a little by grinding the inner surface of the holes.
With the desired horizontal suspension of the pump, another suspension point is required at the rear (bottom). She chose a rectangular protrusion at the bottom of the case, it is clamped with a special clamp. Initially, it was a piece of thin steel tape pulled together by an M5 screw. For a screw, a wire ring of 5-6 turns caught on (distribute the load). One of the standard mounts was supplied with the same ring. The rope was not frayed, but the metal parts quickly deteriorated, repairs had to be carried out, including in the winter, digging up snow, working in the cold.
Once, the pump came off the rusted mounts and worked for some time lying on the bottom. With his vibrating body, he nearly "ate" his way out, Count Montecristo a sort of.
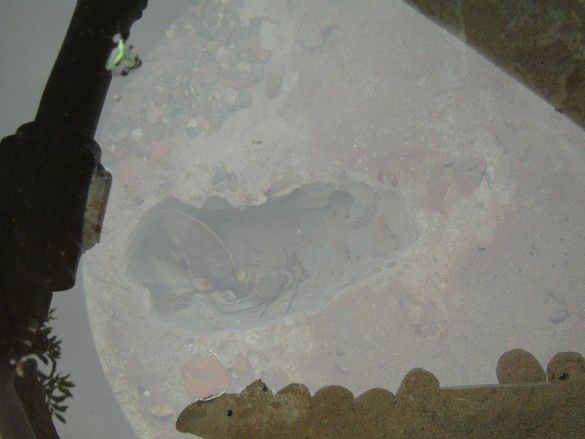
Special stainless steel mounts have solved this problem.
What was used for work
Instruments.
The usual set of bench tools. For cutting sheet steel I used a small angle grinder with an abrasive disk ø125mm. It is highly advisable to use protective headphones and glasses. The marking tool - an alcohol felt-tip pen or a metalwork "pencil" - a scratcher with a sharp hardened nose, a large joiner square, a long ruler. To fix the parts during cutting-welding, several joinery clamps were useful. For welding, a small inverter with accessories was used - cables, a protective mask, leather gaiters, homemade whisking of glassy slag from a small chisel with a handle. It should also include tight non-synthetic clothing and boots. The work was carried out on the street - a good extension cord with a pair (angle grinder, inverter) of sockets came in handy. As always - absolutely necessary, a bit of patience and accuracy.
Materials
In addition to the sheet steel itself, welding electrodes were needed - I used TsL-11, ø2mm, and abrasive wheels ø125mm, 1 mm thick.
Mounts
Affordable was 1.5mm thick stainless steel sheet. I cut out several strips of suitable thickness from it, straightened it, and cleaned the burrs.
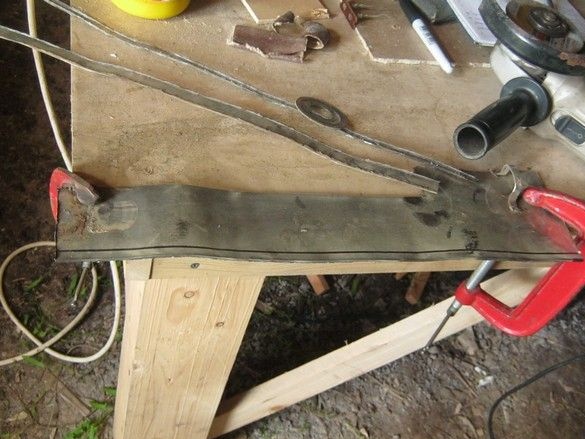
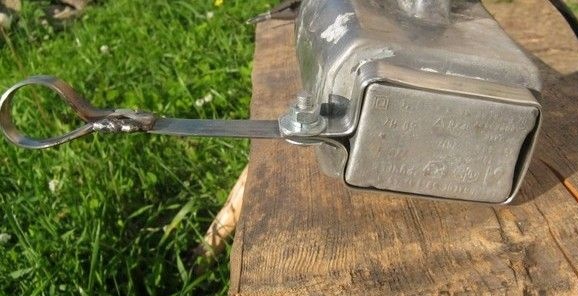
For the rear suspension, from the strip of the appropriate width, I curved the outline of the rectangle, fastened it with a short M6 screw with everything due - a grover, washers, everything. The latter applied - reinforced, or "body". The sticking-out strip, in place of the future eyelet, was carefully polished with several numbers of the skin, to a completely smooth state, and it bent the eyelet, the end of which was fixed at several points by welding. He took a stainless steel electrode ø2mm, grade TsL-11, reverse polarity, current - 40 ... 50A
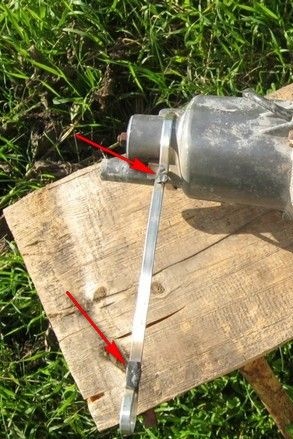
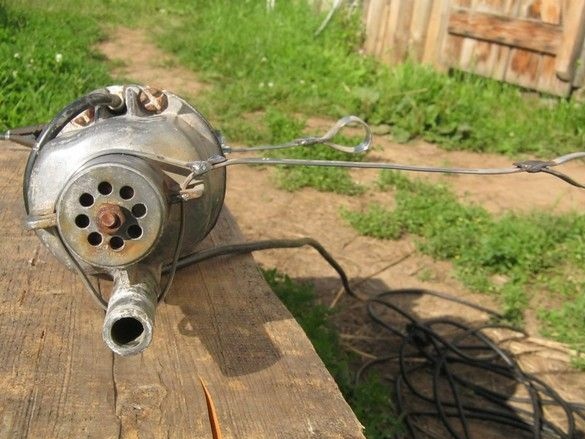
He did the same with the front suspension - he narrowed the strip through the regular ears and fixed the edge with welding, polished the remaining tail, molded it, welded it.
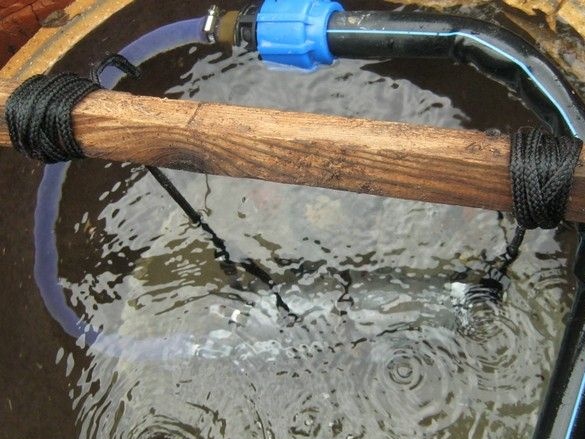
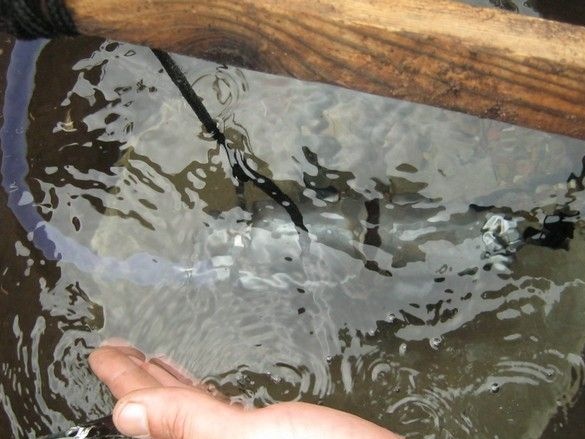
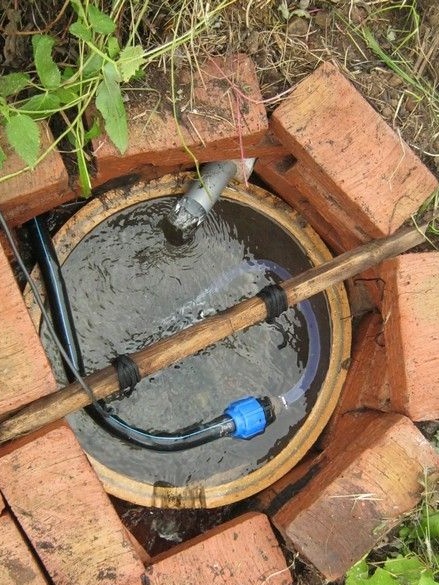
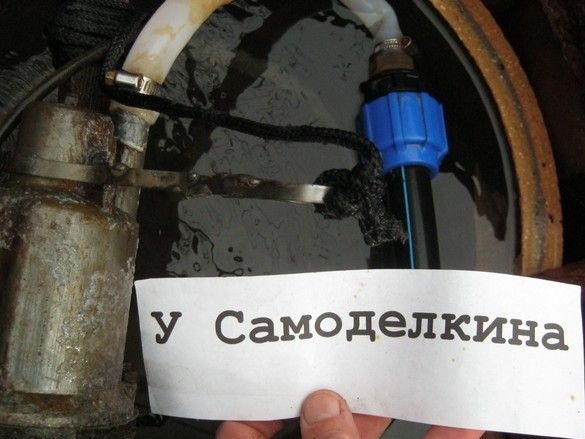
For the last photo I had to climb into the spring, at the same time I made an autumn revision. And it turns out in the captivity chamber, the princess lives with me, now admire what a beauty!
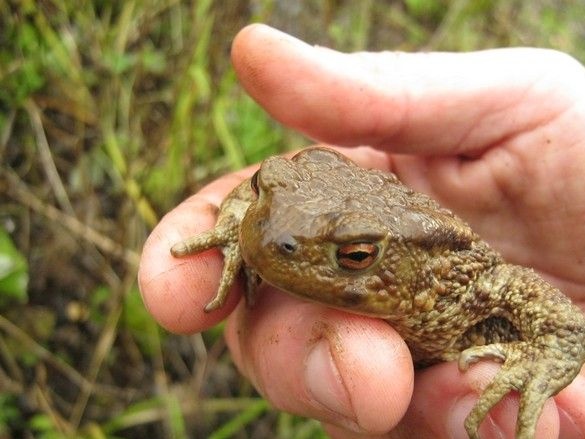
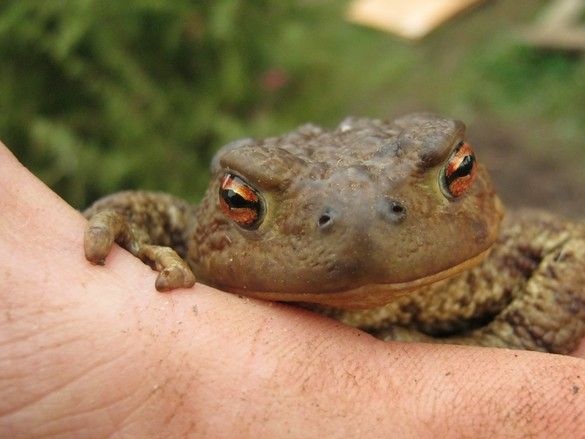
Conclusions in pursuit
The fasteners turned out to be very successful - the ropes do not fray, the glands do not rust. The operation of the pump for more than two years, including in the garden seasons (watering), without any maintenance, confirms the reliability of the design.
For fasteners, you can try to use stainless wire, get a small piece of it, you can by stripping the welding electrode on stainless steel - they are relatively expensive and in specialized stores, often sold by weight - individually. Several pieces, even of significant diameter, are quite moderate.
Practice shows that a vibration pump that constantly works in a system with pressure (a hydraulic accumulator that turns off by a pressure switch) does not last long. Usually up to a year - swam, we know.
The well-known maxim says - a correctly formulated question, contains half the answer - while writing the article, it came up with a good way to protect the ropes from rubbing with a standard suspension - use vulgar thimbles.
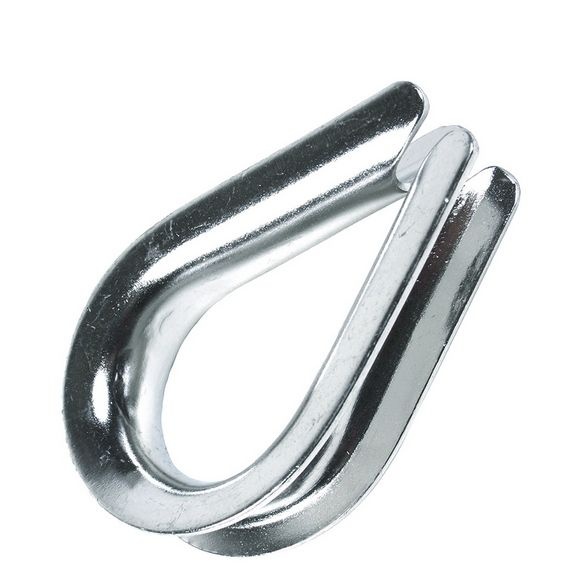
We have such glands sold in hardware stores, along with all sorts of there, eyebolts - lanyards.