Previously, I used an electric emery based on a 50W single-phase motor, but its power was not enough for normal operation. At hand was an old three-phase electric motor with a power of 370 watts, on the basis of which a completely working electric emery was obtained.
Materials:
- electric motor 63V4U2, 370W, 1410 rpm;
- MBG0 capacitor 10 μF x 600 V;
- MBG0 capacitor 4mkF x 500 V;
- junction box for wiring;
- nozzle on the shaft under the grinding wheel;
- start button;
- wires;
- chipboard plate.
Instruments:
- soldering iron, solder, flux;
- electric drill;
- jigsaw;
- drill.
Assembly Instructions for the device:
The backbone of the electric ejector will be a three-phase asynchronous explosion-proof motor 63V4U2 with a power of 370 W and a rotation speed of 1410 rpm.
In my apartment there is no three-phase power supply, so I will connect to a single-phase network using phase-shifting capacitors such as MBGO.
The electric motor power will drop to 60-70% of the nominal, but the rotation speed will remain almost nominal. In fact, the motor begins to work as a two-phase.
I have three wires coming out of the electric motor, i.e. the stator windings are connected by a "star", so the capacity of the working capacitor is calculated by the formula:
Cp = 2800 x I / U (μF),
where I is the current consumed by the motor (actually consumed value),
U is the supply voltage.
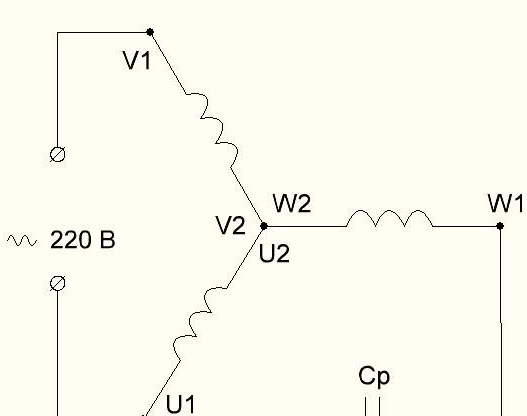
This is how the connection looks in the terminal box
The difficulty lies in the fact that under load and at no load current through the windings flows different, which means that the capacity will need to be selected experimentally for a specific load. If the capacity is more than necessary, the motor will overheat during operation, if less, it will not start or the start of the motor will be unstable.
In my case, two 10 uF and 4 uF capacitors connected in parallel allowed me to start the electric motor without any problems and not to reduce the speed when loading on the shaft.
When using one working capacitor at 10 microfarads, the electric motor was started every other time. Therefore, the capacitance of the working capacitors of 14 microfarads is optimal in my case. The calculated data of Ср also indicated a close result.
As working capacitors, metallized paper or film capacitors can be used (MBGO, MBG4, MBGP, KGB, MBGCH, BGT, SVV-60). The permissible voltage must be at least 1.5 times the voltage of the network.
If six wires come out of the electric motor, then the stator windings of the electric motor can be connected with a “triangle”. In this case, the efficiency of the electric motor will increase in comparison with the “star” winding connection scheme.
In this case, the capacity of the working capacitor is calculated by the formula:
Cp = 4800 x I / U (μF)
In practice, for every 100 W of electric motor power, it is necessary to add 7 microfarads of working capacity, but again, the optimal value is selected experimentally depending on the outgoing conditions.
When starting three-phase electric motors with power up to 1 kW in a single-phase network, as a rule, it is sufficient to use only a working capacitor Cp. If the electric motor power is higher than 1 kW, it is also necessary to use a starting capacitor Cn, which will work when the electric motor starts. To change the direction of rotation of the motor shaft, it is enough to throw one wire of the working capacitor to the other end of the stator winding.
The electric motor got me without a cover, so I had to close the hole with a textolite sheet, having previously provided for the output of the ends of the windings and the fastening of the junction box for connecting the electric motor.
I placed the capacitors and the power button in a separate case and attached it to the chipboard plate
I ordered a nozzle on the shaft for the abrasive wheel under the motor shaft with a diameter of 12 mm, with a seat Ø32 mm.
I use an abrasive wheel with a diameter of 125 mm, a width of 16 mm. Designed for preliminary and combined grinding, sharpening of the cutting tool.
The electric motor was installed on the chipboard plate and bolted.
The sanding pad is made of a steel strip 3 mm thick and bolted to the chipboard plate.
Conclusion
Electric emery has enough power for sharpening drills and processing various parts, respectively, the work was done not in vain!
In the future, I will add protection against abrasive particles flying during processing of the material and, possibly, install a second abrasive disk on the back of the electric motor, because the place on the shaft allows.
Well and most importantly - observe safety precautions and your crafts will delight you and others