For manufacturing, I needed the following basic ones (I write “basic” since if you start describing the entire tool, the list will be long, boring and boring) materials and tools:
1. Chinese clockwork
2. A piece of penoplex the size of a sheet of A4 paper. 30mm thick
3. 0.5mm thick aluminum sheet
4. Steel wire ø0.3mm- 3m
5. Cardboard
6. Acrylic paint
7. Epoxy adhesive
8. Baby powder
9. Very sharp knife
10. Hand-held jigsaw
11. Sandpaper
12. Soldering iron
13. As they say at the end of the credits for the film “and others” ... and another instrument.
I think there is no need to describe the clock mechanism, neither the Chinese nor I did anything new there.
Watch case.
On the Internet, we find the image we like, download and print it on an A4 sheet, then use carbon paper to transfer it to penlex.
Cut the workpiece along the contour with a thermal cutter.
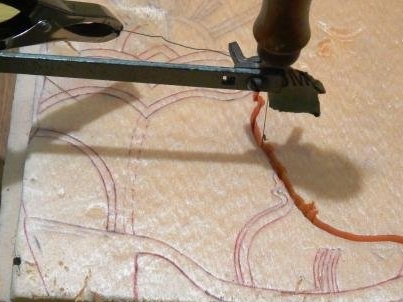
"The craziest device"With the loud name" thermorezak "is an ordinary hand-held jigsaw, still of Soviet manufacture, on which stands" c 1 p ", in which instead of a file a nichrome wire is clamped (through a piece of sandpaper for insulation), connected to an adjustable power source.
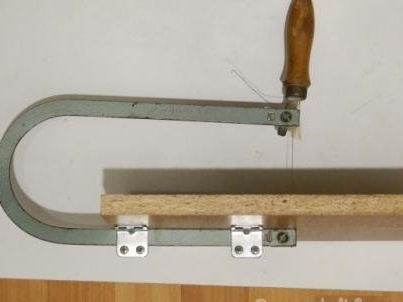
We give the workpiece roundness to the workpiece with sandpaper and grind the largest recesses of the picture (marking the boot, lower joints of the cut)
To give strength to the case, we glue it with epoxy paper napkins.
For a long time I fumbled with a picture on the bootleg, it did not work out what I wanted. As a result, I evened it with a putty made on the basis of epoxy resin and baby powder as a filler
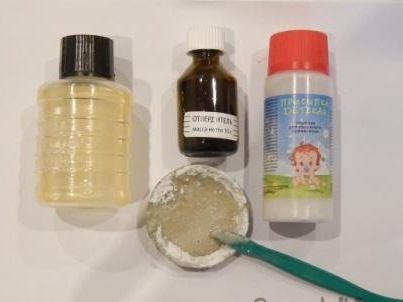
I pasted a picture cut out of cardboard, and then primed with white acrylic paint.
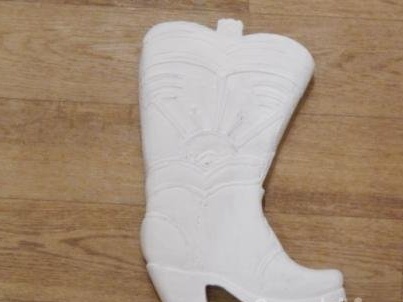
Painting to simulate the skin was done with acrylic paint using a sponge, and the result was very similar.
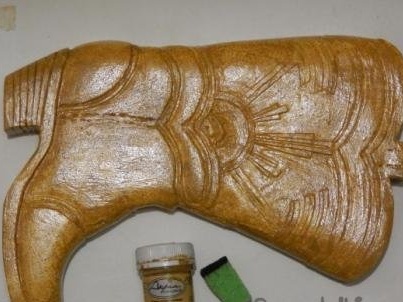
Recesses and seams are shaded with a marker to tint scratches on of furniture. This photo is not particularly noticeable, but after the third or fourth processing, the contrast has become much brighter.
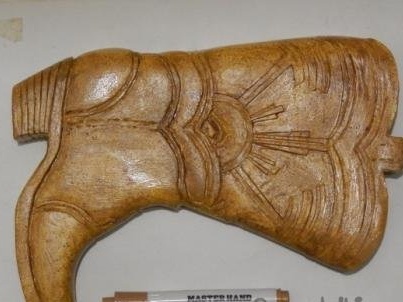
To set the clock mechanism for marking, I cut a niche.
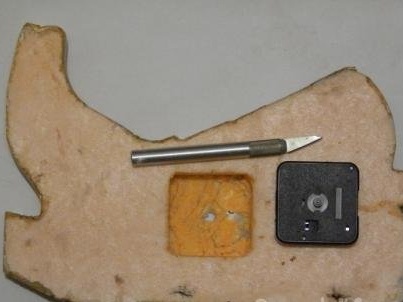
As the saying goes, “come after a good thought”, it was possible to cut through this niche right at the first stage, and then simply glue it on the front with a sheet of paper, then you would not have to carefully, so as not to damage the thin putty film, to pick out the extra foam.
The mechanism itself is sealed with glue used for ceiling tiles. It is impossible to use glues, the solvent of which is used in acetone, it will corrode penoplex instantly, well and accordingly it will ruin everything irretrievably.
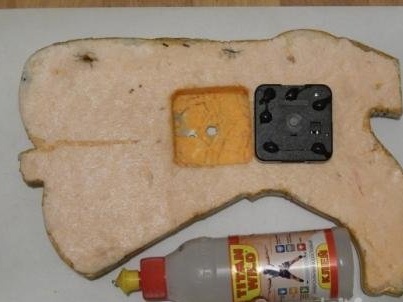
The arrows, as mentioned above, are made in the form of stilettos. We also download the drawing from the Internet, print it in two copies and glue half a millimeter thick aluminum sheet onto the base.

I took aluminum from the reflector of a burnt LED spotlight.
We use ordinary stationery scissors to cut along the contour of the part, then fold them together and punch holes in both at the same time.
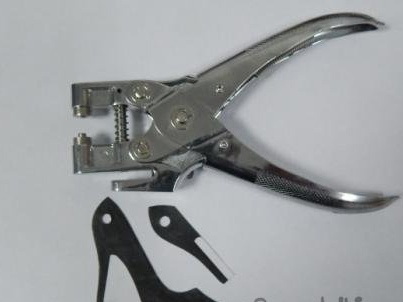
At first, I just wanted to stick the shoe details on the regular watch hands
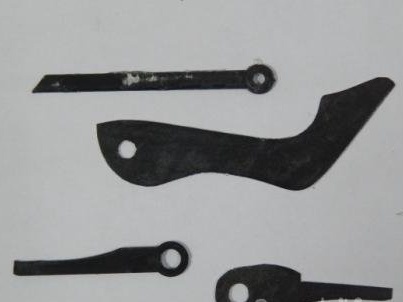
Then he decided to use only the seats of the regular shooters, pasting them into the holes of the new shooters.
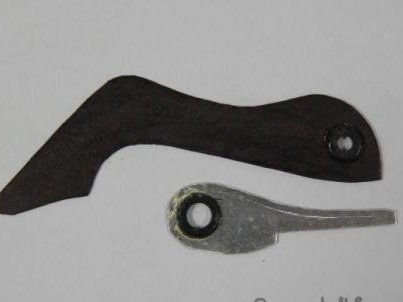
Moreover, in order to reduce the gap, it was necessary to glue the sleeve at the bottom of the watch, and the arrow at the top of the minute.
At first the dial was not supposed at all, according to the location of the hands, and so it’s clear how much time they show, and behind the bulky dial the pattern will be lost. But yielding to the customer’s requests, I had to dodge a little, and here’s what happened in the end:
To create a strong and at the same time transparent base, it was decided to use a thin steel (copper too soft for such a diameter) wire, laid in a flat spiral and soldered in the places where the numbers are attached.
On a sheet of cardboard I drew four concentric circles (initial radius 85mm) with a step of 5mm, divided into twelve parts and used this drawing as a template.
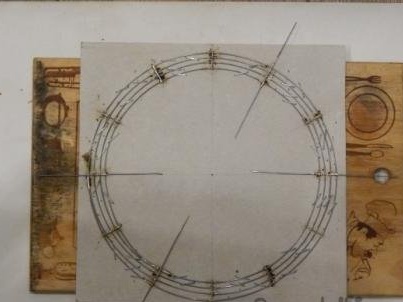
As you can see in the picture, when laying the wire in a spiral, I pinned it with a stapler to avoid displacement before soldering.
The result is this design:
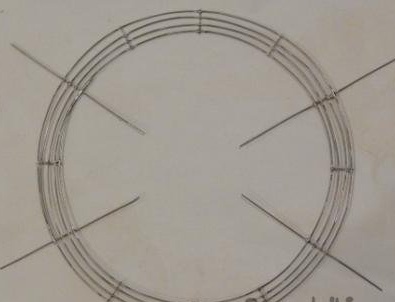
Long parts, subsequently bent at right angles to the plane, serve to fasten the dial to the watch case. Excess solder is removed with a file. Since an active flux was used when soldering (“soldering acid” is written on the bottle), the product was washed with a strong soda solution and painted black.
The numbers are again printed on a computer, the font is Harrington, size 100, then pasted onto cardboard
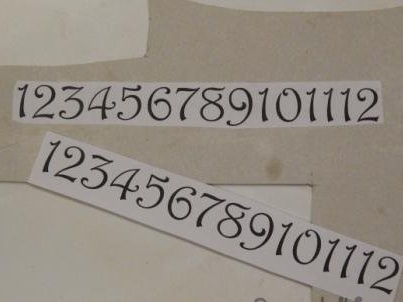
They were cut with a thin and sharp knife for stencils and like a stencil, and painted in golden color
.
Guided by the soldered marks, we paste the tsifiri.
We do not install the finished dial on the case, but with a certain gap (about 5 mm), which makes it as if airy, not covering the picture. This is how the watch looks at its final place of registration.