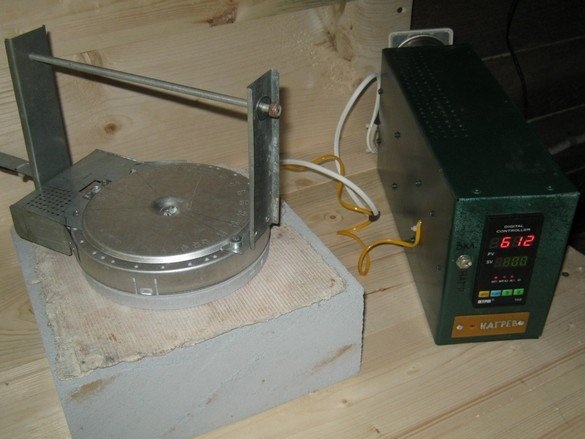
Fusing, (eng. Fusing from fuse - sintering, smelting) is relatively newfangled needlework and as it is now, it was born in 1990. Apparently, the manufacture of a “sintered” stained-glass window became possible with the advent of stained glass with equal KTP (coefficient of thermal expansion). It is done like this - on a glass base, a pattern of colored pieces of glass is laid out, and their edges, in most cases, do not require precise adjustment and processing, enough glass cutting and special nippers. The assembled preform is placed in a special furnace and heated to the temperature at which the glass melts.
The resulting stained glass window looks very peculiar - smooth rounded edges, each element resembles a sort of melted candy. With a bit of artistic ability, we get very interesting gizmos. Moreover, here you can apply a whole arsenal of techniques - use metal foil, sawdust, wire, stencils for them, cloisonné enamel techniques, apply firing paints on glass and ceramics, chemicals giving bubbles inside the glass. The fusing furnace also allows molding of flat glass - bending. Ready-made gizmos can be combined using "low-temperature" methods, in large stained-glass windows. In a word - an abyss of opportunities for creativity.
Colored glass, with the same CTE, like many materials for fusing, are expensive, however, the most expensive article in mastering this technique is, of course, the furnace. A furnace for fusing glasses is rather unusual, its shape is dictated by sintering technology - a flat table, on which it is convenient to lay a glass sheet-blank, a hinged lid with heaters. In general, it resembles a suitcase, on some, there are even fasteners.
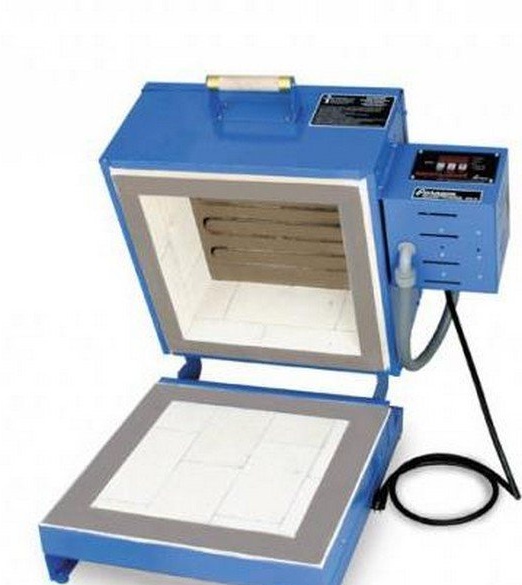
Muffle furnaces - with a heater on top of the muffle chamber, are not used - after heating the glass to the melting point, the product should be cooled quite quickly to the annealing temperature, while the ovens are often slightly opened. A quick drop in temperature in the muffle is difficult - the thermal inertia is too high, and it is inconvenient to lay the blanks in the chamber.
Furnaces for fusing, there are very different sizes, respectively - capacities. With heaters of a small stove, home wiring can very well cope.
Glass sintering “for not expensive”.
You can try yourself in this interesting business without spending large sums - for starters, there is an original version with Ali Express - special crucibles for the microwave. It is a refractory crucible with graphite coating on the inside. The coating is heated in microwave waves and heats the glass with radiation. There is one virtue, but a fair amount - cost. At the time of writing, the crucible cost 2-4 thousand rubles. depending on size.
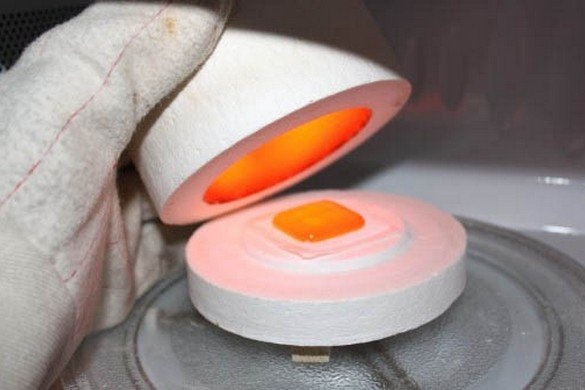
The disadvantages of such a simple option, as usual, are mass. Temperature can be controlled only visually, "by eye", controlled annealing to relieve internal stresses is impossible. Small size - only for jewelry, the inability to use metals. As a rule, having experimentally selected the sintering mode and having consumed the glass fragments included in the kit, the occupation and the crucible are thrown.
A specialized electric furnace, of course, is much more perfect, however, the smallest - 200x200 mm, costs 35 thousand rubles. Of course, only refractories, a controller with a thermal profile, quartz and ceramic tubes for heaters, assembly again ... Having a workshop or garage, a bit of metalwork skills and experience with electricity, it’s quite possible to assemble such a furnace yourself, spending less than half the cost of materials , but what to do horseless-garageless residents of the "concrete jungle"?
Idea.
The idea of an extremely simple and inexpensive fusing furnace of “intermediate” characteristics belongs to comrade "Ilya MSU", from the metal forum. The oven is small in size, but it is already possible to bake the glass, much more serious than the ring-brooch-pendants in the microwave. You can use wire, foil and the entire arsenal of fusing techniques. Electric resistance heater in the cover, thermocouple with a simple temperature controller. Low, even for an apartment power, the ability to manufacture in the kitchen from widespread inexpensive parts, elements. The design does not contain specialized high-temperature refractories.
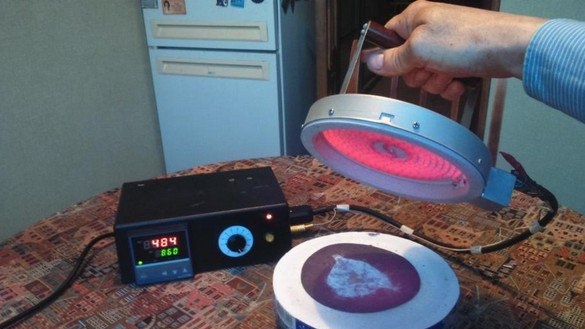
As the top cover of the suitcase oven, a part from an electric stove with a glass-ceramic surface is used - a burner. It has a metal casing lined with fibrous refractory, in which special protrusions of the heater tape are formed. The burner is complemented by a handle and a thermocouple connected to a simple controller. As a base, a flat can filled with plaster was used.
Own version of a simple burner stove.
I got two second-hand burners with an internal “working” diameter of 140 mm, with a mechanical thermostat in a metal case (there are options with a quartz tube).
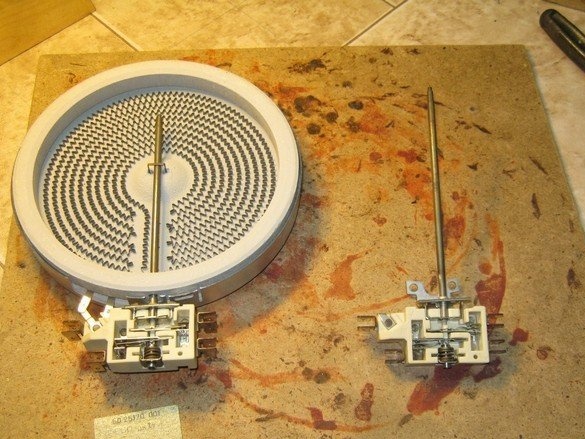
What was used at work.
Tools, devices, equipment.
A set of ordinary medium-sized bench tools, a jewelry jigsaw with accessories, a small angle grinder, a screwdriver or an electric drill. A set of wiring tools, a 40 W soldering iron for wiring, larger - 60 ... 80 W - for structural soldering. Marking tool. Useful tool for installing blind rivets, building hair dryer.
Materials
In addition to the burners themselves, they needed sheet asbestos, foam concrete bricks, wires different, a thermocouple, thermotubes, nylon clamps. A ready-made control unit for a muffle furnace was used (or a controller + solid-state relay + radiator + case). Extinguishing resistor of suitable power (oil heater). A bit of galvanized steel fasteners.
The thermostat contacts of the burner were forcibly closed and soldered, tin-copper solder to the output terminals, wires in silicone insulation were soldered. Next to the thermostat, a hole was drilled into the internal cavity, a chromel-alumel thermocouple (type K) was introduced, from a multimeter. To the probe of the standard thermostat, the thermocouple attached several turns of nichrome wire.
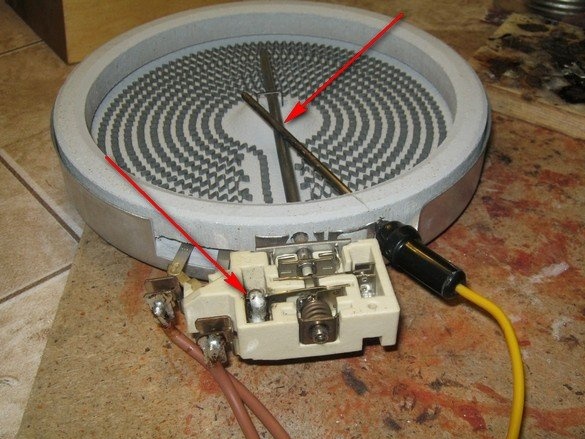
Tin cover - in fact, it turned out to be the most difficult element of my furnace. It is soldered from the “roofing” galvanized steel 0.5 mm, solder tin-copper (the melting point is higher than that of lead solders). Flux - soldering acid (zinc chloride), soldering iron 60 watts.Complex parts were sawn with a jewelry jigsaw, straight cuts - with metalwork scissors. Curved lines were marked like this - the piece of iron was put in the right place, and with a pair of compasses, with a needle in the center of the burner, I drew the necessary radius for the arc.
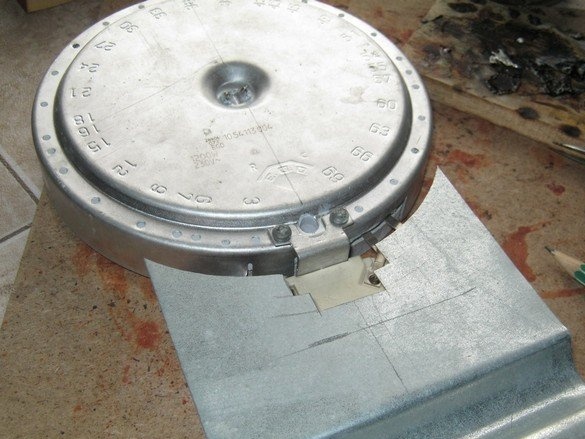
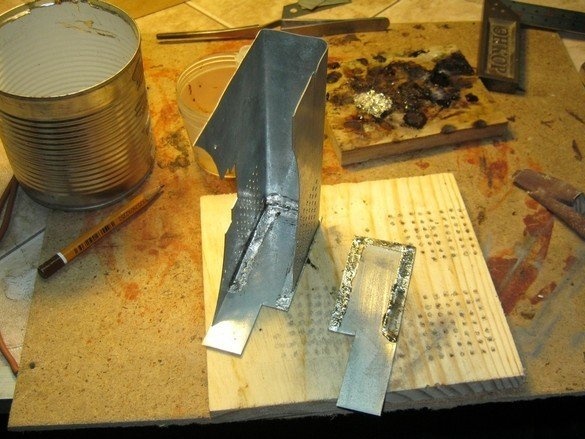
Soldered from the inside, mainly for aesthetics. Opposite the “knife” terminals of the standard burner thermostat, with wires soldered to them, made ventilation holes (above and below) on the casing so that they would be cooled by an air current and the solder would not melt.
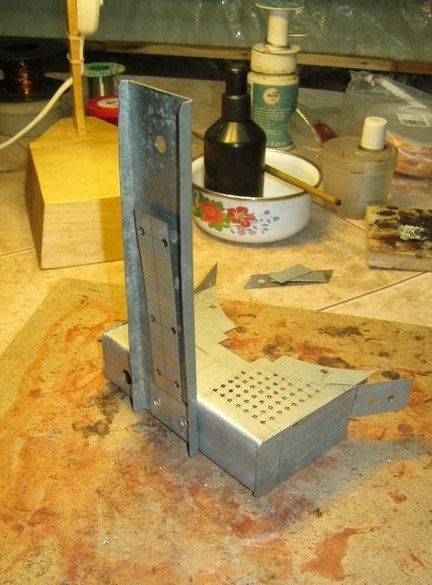
Over the edge of the casing, I decided to hook and one of the brackets for the handle, with the same fasteners, pinned a wire holder. Tin pieces fastened with aluminum blind rivets.
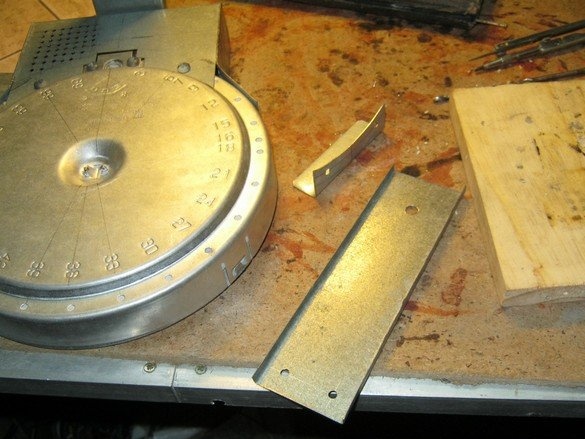
The front bracket for the handle was mounted on a regular casing and consists of two tin parts. It is fastened to the casing with short self-tapping screws, the connection between themselves is riveted.
The outer part.
The burner heater, with a power of 1200 W, is too powerful for baking glasses - the heating rate is great for such a small volume, the glass does not have time to evenly warm up, the workpiece crackes. To eliminate the drawback, the heater's power had to be reduced - to turn on a powerful resistance in series with it - an oil heater at half the power. At the same time, on the burner heater, the voltage drop is exactly half the network voltage - 110 volts.
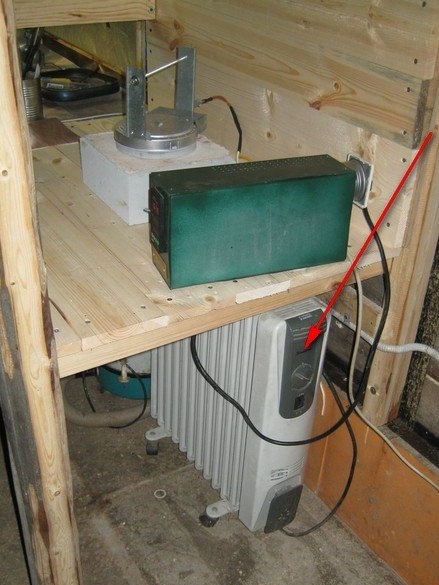
Controller for controlling the furnace. A socket for connection and a screw terminal block for the furnace heater are mounted on its rear wall. The thermocouple is connected directly to the controller.
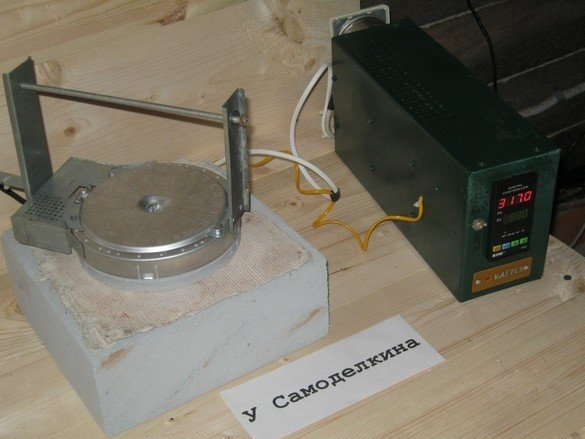
The lid of the furnace is on a refractory basis - asbestos sheet, under which half of the brick is made of foam concrete. Nearby, it is worth keeping the same fire-resistant lining - on it, if necessary, you can put the hot tip of the "open" furnace.
Sintering.
When sintering glasses, two main temperatures must be maintained - the beginning of glass melting (710 ... 800 ° C depending on the type of glass) and the annealing temperature (500 ... 600 ° C depending on the type and size of the workpiece). Initial heating occurs as smoothly as possible (within reasonable limits, of course), after which the temperature quickly drops to “annealing”.
Typically, the process is controlled by a programmable controller "with thermal profile." Here, a simple controller is applied, maintaining one temperature, and they are switched, manually - a semiautomatic device. Upon reaching 800 ° C (~ 30 min.), The furnace lid is ajar, 500 ° C is set on the controller and the product is annealed for 1 hour. After that, the furnace heaters are turned off, and the product cools down with the furnace to room temperature (~ 1 hour). Small sizes of glass allow you not to fear small inaccuracies in the process.
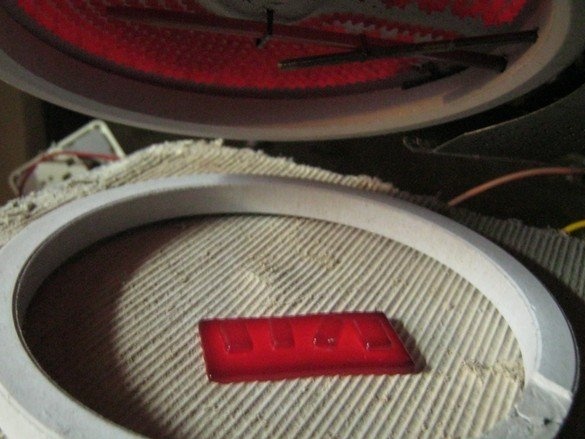
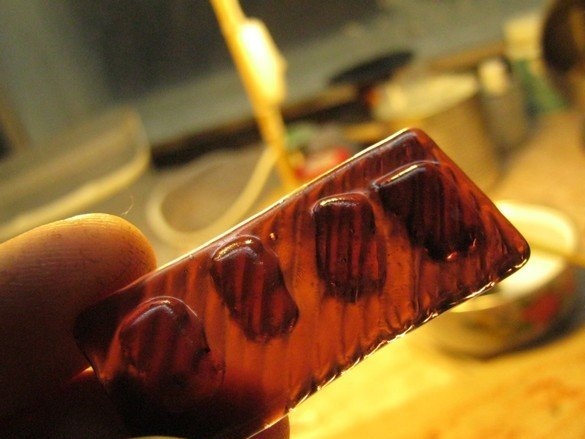
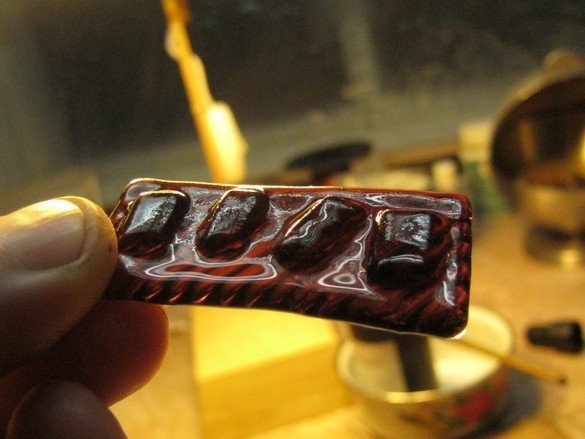
Well, the first experiment is quite successful - the glasses fused, but not to a flat surface, the sample did not crack - the temperature profile for this type of glass should be considered successful. Let’s try to be more meaningful.
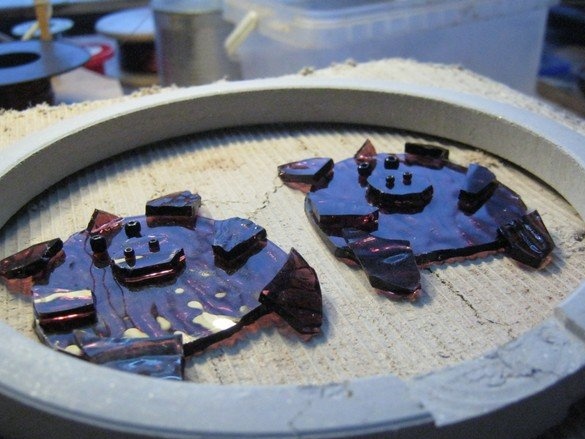
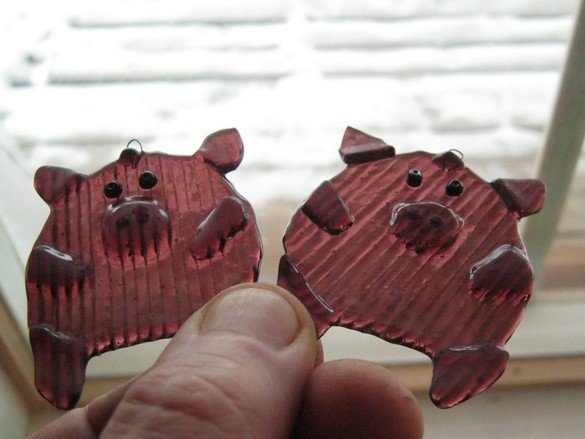
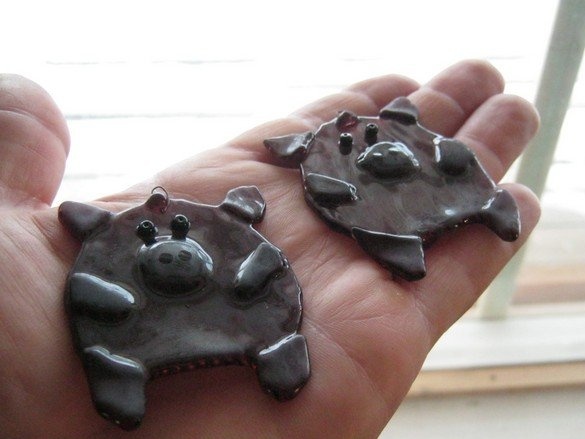
Two beasts, hmm, quite in the spirit of the day, like Olympic bears, at one time ... Here, as an experiment, two varieties of beads were fused, copper wire, glass was melted not only “lap” but also practically “end-to-end”. Beads (glass with a different KTP) and copper wire (all the more) should be very small (diameter, cross-section) relative to the main glass, then the resulting stresses will not destroy the product.
Babay Mazay, December 2018