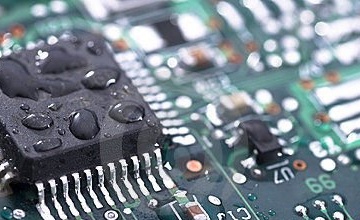
The author of Instructables, nicknamed TahsinK, talks about a simple splash protection method for printed circuit boards. To do this, he uses a finished product called Silicone Modified Conformal Coating from MG Chemicals. Such a bottle, as in the picture, will cost $ 20, the funds in it are only 55 ml, but it is spent quite economically.
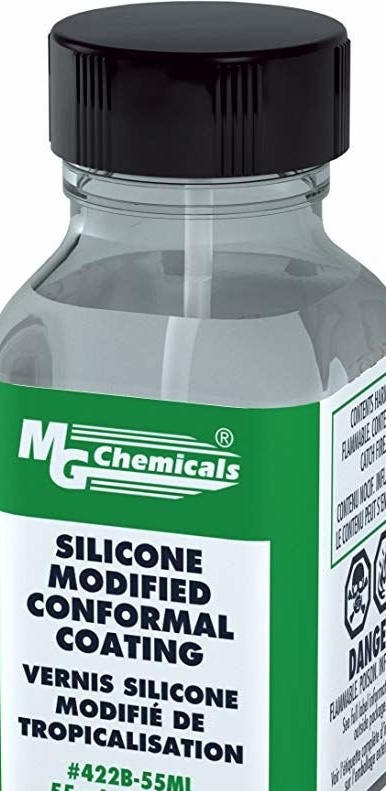
Isopropyl alcohol is still needed. Perhaps you already have one for washing flux from circuit boards.
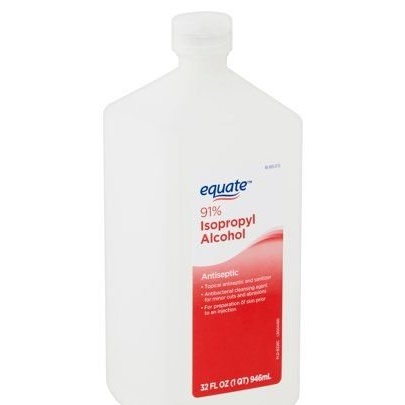
It evaporates quickly and leaves no residue. But it must not be allowed to get into temperature, pressure sensors, displays, etc. It makes no sense to apply a coating without pretreating the board with such alcohol - it will fall off, and you will scold the manufacturer of the product because it is "so expensive and useless." By the way, the same applies to many types of glue: it does not hold not because it is bad, but because the surfaces are not fat free.
The master collects a little money from the bottle on the brush and slowly puts it on the board. It starts from the center, then gradually moves to the edges. Something like this, our wives paint nails ... oh, nails.
You cannot apply too quickly, and it is important to make sure that the first coat is not too thin. Do not cover pads, springs, connectors, etc. - everything that should NOT be isolated. You can put the counterpart in the connector during processing, it will not allow the tool to get into contacts. You can make sure that everything that is needed is covered, and everything that is not needed is not covered, you can use an ultraviolet LED.
Let's watch a video about how the master applies coating:
The coated master dries with a gentle stream of air at room temperature for ten minutes. Until the product is completely dried, you can not touch it. When dried, the coating shrinks slightly. Having gained experience, you will learn to determine exactly when to stop drying. Two boards are shown in the photo, only one coating is applied, on the second it is already completely hardened:
The same thing in the video:
Coated circuit boards, along with the motors they control, are tested with soap suds:
If the coating is broken somewhere, in the appropriate place you can patch it with the same tool, not striving for excessive thickness.When heated, it softens, so you can change failed components on the board by soldering, and then also restore the coating where it was broken. Splash protection does not provide tightness, that is, it protects only from splashes, and not from immersion in water.