This tube amplifier is designed and built from the ground up. This is a very long project, and it took a lot of time and patience from the author of this project. Let's analyze all the pros and cons of this homemade together with the author.
IMPORTANT! This device has a deadly voltage inside. If you do not know about high voltages and electronics, then it is not advisable to repeat this homemade. Otherwise, you do this at your own peril and risk! It is not recommended to delve into the device with electronic lamps while it is on!
Step One: The Idea itself
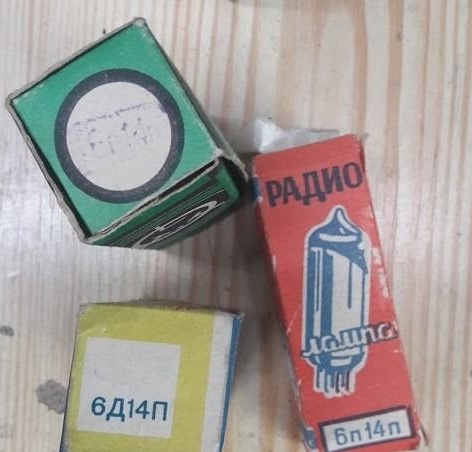
Several old lamps were found in a box in the house of grandparents. It was decided to make a low-frequency amplifier based on them. Other semiconductors in this homemade product were not used in principle. I had to conduct a study to find out how these tube amplifiers work.
Step Two: Circuit and Components
Designing the circuit was probably the most difficult part of this project. First, a list of the tubes that were available was written, and then, based on them, a schematic diagram of the project was drawn. A push-pull stereo amplifier with tone controls, phono and aux inputs and some VU meters was designed. EL84 c lamps were required, and for other steps it was decided to use simple double triodes. The lamps quickly ran out and had to order new ones.
Then the time came for another difficulty: an output transformer. A cheap transformer was not easy to find. But after a little search, in the end, the transformer was found on one popular bulletin board. The transformer is designated as NASS II-12 in the diagram. “NASS” means “Not A Single Semiconductor”, II means push-pull and has a total of 12 legs.
Step Three: First Test
The chaos on the table above is the assembly of components in the air.
Two conventional power transformers are used here in series as an output transformer, just to check if everything is working. Everything seemed to be in order, and now it's time to find a power transformer. An old transformer was lying in stock and the author made an attempt to wind the transformer himself. However, after disassembling, rewinding and testing, I had to, abandoned the idea ... Therefore, one transformer was taken from the old radio, thinking that everything would be in order. But this is not so. But more on that later.
Step Four: Product Housing
The material for the case was to be aluminum. Brushed aluminum front, top and back plate. Hand made of some solid wood. Unfortunately, the author had to abandon the aluminum top cover because resources were limited. The front and back were made of a three-layer material (two sheets of aluminum and one plastic between them). The top cover required strong and durable material, because it had to withstand the heat generated by the lamps and withstand the weight of the main transformer. Therefore, the decision was in favor of the PCB. This material has a brownish color, it is relatively durable and easy to work with.
Important! It is necessary to electrically shield the entire housing and connect it to the ground at only one point in order to avoid ground loops. In this case, aerosol glue and a thin aluminum radiator were used.
The front and back panels were designed in SolidWorks to see what the amplifier looks like. After that, a drilling machine was used to make the necessary holes for the connectors, fuses, switches, potentiometers and volume meters. Fine sandpaper is used for a good surface finish. After that, transfer foil for label printing was used, which was coated with a layer of shiny and transparent coating to prevent letters from erasing over time.
First, the upper panel was installed for a test landing, and then the necessary holes were drilled.
Step Five: Amplifier Wiring
In order for the top panel to withstand transformers, the structure was reinforced with sheet metal. After that, wiring was started. This is the most time consuming procedure. First, the bolts are attached to the transformers and pipes, and then the necessary components are soldered. The tone control module needed additional shielding because it picked up noise from the environment. Therefore, it was installed in a metal box.
Step Six: Final Assembly, Problems, and Specifications
Thus, everything was collected. After the test, it turned out that the main power transformer had problems with a very high current, it was very hot. After about 30 minutes, he reached temperatures above 90 C. This was above his optimum working temperature. Even after installing a small fan inside the case, it did not work to lower the temperature. Therefore, I had to install another 6.3V transformer inside the case. This solved the heat problem of the main transformer.
Another problem was the very high noise level. This is likely due to ground loops that were accidentally left in the circuit.
Therefore, the inevitable modernization of this amplifier.
In the end, despite the small flaws of this amplifier, according to the author, it sounds great!
This amplifier can deliver a RMS value of 15 watts per channel without any noticeable distortion. It consumes about 10-15 watts from the network when idling and about 100 watts when operating at full power, transformers.