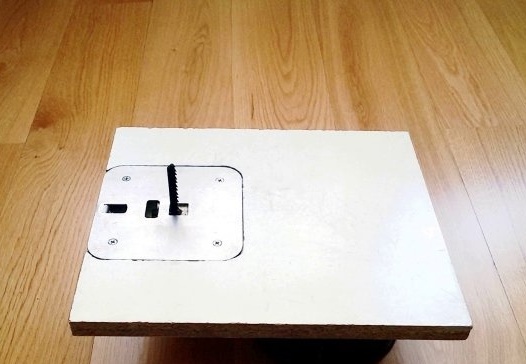
On the basis of the "Universal" electric drive and the file - a hacksaw PN-40 from the Universal set of the UN-20 model it is proposed to make a stationary device for working with a jigsaw.
The domestic multi-purpose universal power tool kit Universal was produced for several years (1997-2003). In those years, it was rather difficult to find an inexpensive household power tool for sale. Therefore, “Universal” kits were readily sold out and used by homemade art lovers for a variety of household tasks. On some sites on the Internet, Versatile kits can be purchased today.
Kits of the Universal universal power tool, on the basis of unified electric drives of the MVB and a different set of nozzles, were completed in the form of functionally complete sets, as well as separate nozzles, devices and accessories. The buyer acquired the set he needed, depending on his needs and wealth.
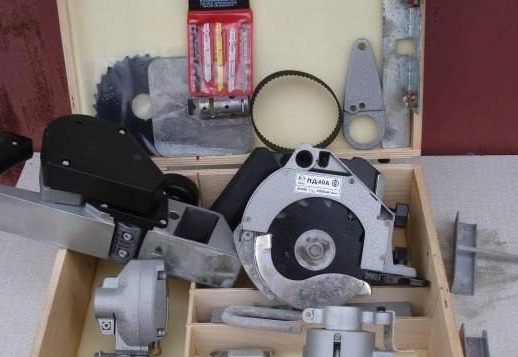
Universal power tool kits were used for linear and figured cutting of sheets, drilling, planing, milling and turning of wood, plastics and metal. They were used for grinding and polishing a variety of materials, sharpening tools and other works. The multifunctional UN-20 set made it possible to assemble from the tools included in it: an electric drill, a hacksaw (a jigsaw), an electric saw with a circular saw, an electric planer, a milling and turning device.
The basis of the Versatile kit options is the MVB electric drive with a power of 600 ... 650 watts. The “Universal” electric drive consists of a collector electric motor powered from a 220 volt network with a built-in two-speed gearbox. It is used in working with nozzles and cutting tools included in the kit. It can also be used independently (for example, as a drill, after installing a drill chuck) and as a drive in various mechanical devices.
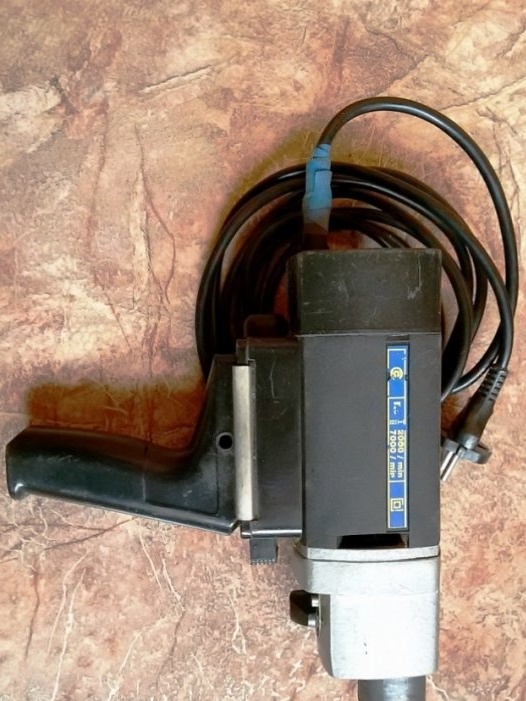
The unified electric drive MVB has varieties - MVB-2V, MVB-21A, MVB-21. For installation and attachment of nozzles and accessories from the “Universal” kit, the electric drive has a cylindrical neck with a landing diameter of 36 mm. At the output end of the spindle there is an M12x1.25 thread for securing the cutting tool and accessories. And to drive the assembled setup from the set, there is a square of 8 x 8 mm.
Technical characteristics of the "Universal" electric drive:
Parameters of the MVB-2V MVB-21A MVB-21
Power, W 600 650 650
1st speed, rpm 2000 2000 0 ... 2000
2nd speed, rpm 7000 7000 0 ... 7000
Overall dimensions, mm 255х76х101 255х76х101 255х76х101
Weight, kg 2.5 2.5 2.5
From the entire “Universal” set, for our homemade we will choose the set “saw-hacksaw (jigsaw) PN40” and the two-speed universal “MVB-2V” electric drive with a power of 600 watts.
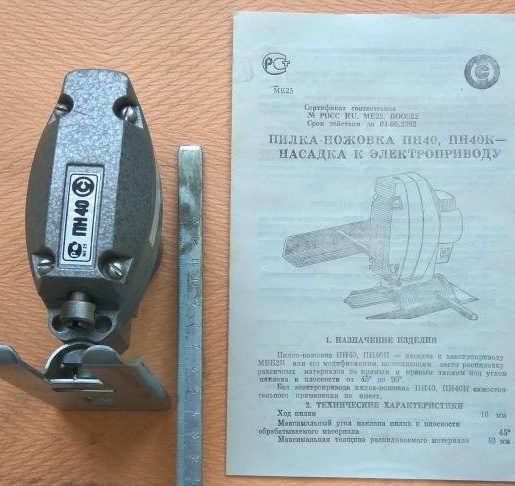
The PN40 jigsaw kit includes a dynamically balanced jigsaw mechanism (a crank mechanism that converts the rotation of the drive spindle into reciprocating saws), two tables - a jigsaw base (narrow and wide) with a rotation mechanism (+/- 45 degrees) and fixation in installed position, adjustable stop for sawing in size.
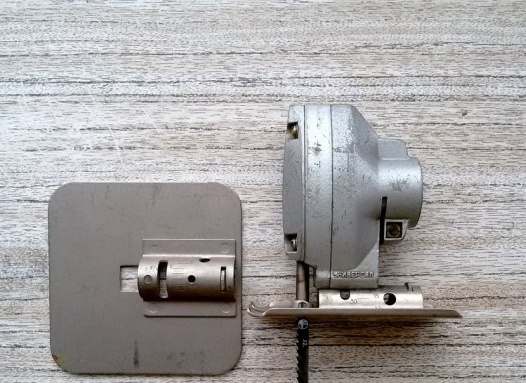
After the practical use of the specified jigsaw in manual execution, the pros and cons of the device can be noted. The "Universal" electric drive is manufactured efficiently - it has been working smoothly since that time, compact, two-speed (rotation speed 2000 or 7000 rpm, model MVB-21 has a smooth adjustment of speed), has good power with its dimensions.
After assembling the drive with a jigsaw mechanism, the center of gravity of the tool moves back. A small reference area of the table of the device, with a significant overhang and weight of the drive, worsens the accuracy and geometry of the workpiece.
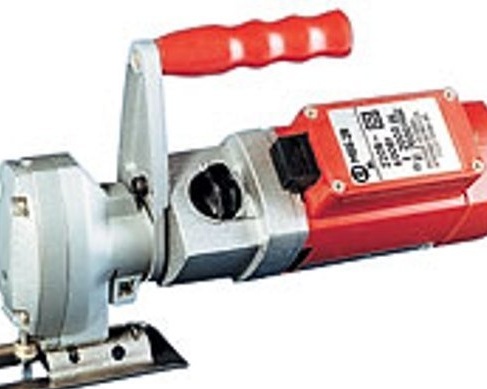
In addition, the disadvantages of the jigsaw design include the lack of additional support for the hacksaw, which limits the amount of feed during cutting, dimensional accuracy during operation and determines the rapid wear of the guides of the working jigsaw rod.
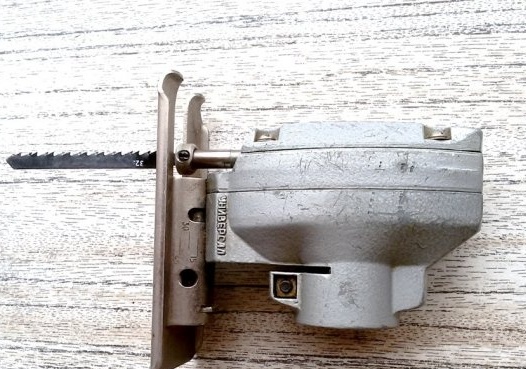
Currently, the choice of power tools for sale is unlimited, and working with it is much more convenient. Therefore, working with Universal does not suit consumers anymore.
Nevertheless, the “Universal” tool is quite suitable for work. These shortcomings are reflected during manual operation. When fixing the tool to a stationary position, the situation changes markedly. This results in a small, but relatively powerful and miniature machine for processing materials. In this regard, the owners of a working antique power tool "Universal" again should remember about it.
In the manufacture of a stationary hacksaw electric saw (jigsaw) based on the "Universal" electric drive, we get the following weekend device specifications:
Thickness of the processed material (max) 60 mm
(depends on the length of the mounted file)
Type of tool universal
(purchased at any tool store,
depending on the processed material)
Processing modes are set manually
Making a hacksaw (jigsaw)
Due to the location of the rod, in the lower position, close to the jigsaw table, there is no place for the location of the hacksaw support (see photo above). In this regard, to eliminate the aforementioned drawback, we will place the support outside the jigsaw structure. To reduce friction losses, we will make a support in the form of a freely rotating roller. To increase the accuracy, we will adjust the gaps in the support to a minimum. The roller will have a groove with a triangular profile, for supporting the hacksaw from three sides. This roller support will be placed between the large and small jigsaw tables, in the thickness of the table of the machine being manufactured. The machine table will be made of laminated chipboard, and the existing jigsaw tables will be fixed opposite each other, on both sides of the plate. This design will slightly reduce the machine's ability to maximize processing thickness, but in this case, the benefits will be significantly higher than the losses.
1. Finalization of a large table for a jigsaw.
In the smaller part of the supporting cylindrical surface, with the help of a angle grinder or a hacksaw, we cut two grooves. The first cut will divide the cylindrical surface in half, the second cut will discharge and free the resulting halves to the base of the plank, for free formation of the base of the support.
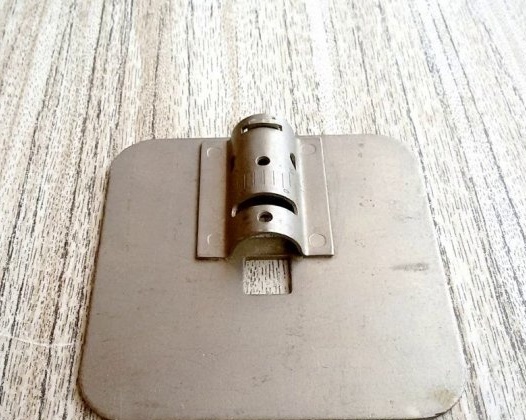
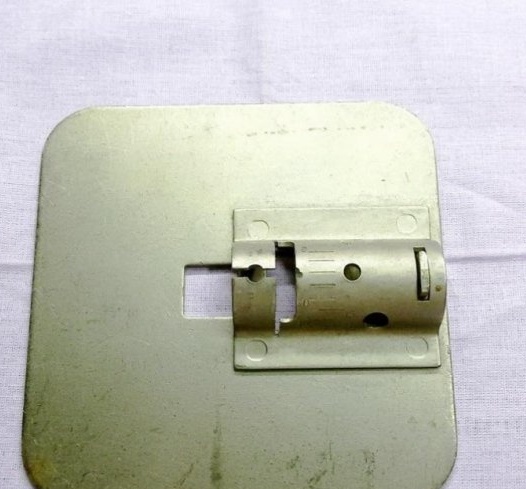
2. The choice of parts for support.
For the manufacture of a freely rotating support, we select or manufacture a pair of parts - a rotation axis with a diameter of 4 ... 5 mm and a roller. The roller mounted on the axis should rotate freely, but not have tangible radial pitching. In the given design, the diameters found in the hardware of the steel hardened roller and the axis from the spring drum of the disassembled mechanical alarm clock were well matched. To fix the axis in the device, one end of the axis (or both) must be threaded.
3. The formation of the base for support.
Using a bench vise and auxiliary tool, from the obtained halves of the cylindrical surface, we form two vertical walls of the groove for the support roller. The size of the groove determines the length of the roller.
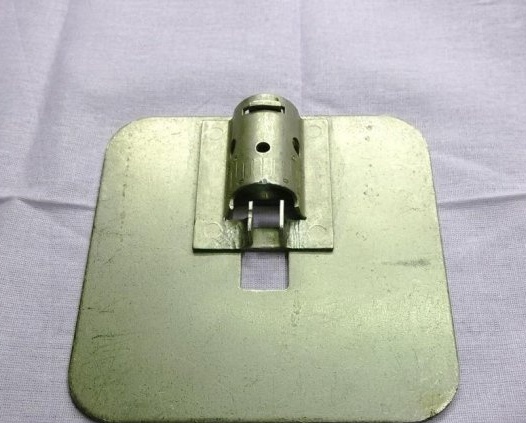
4. In accordance with the diameters of the axis of the roller, in the walls of the obtained groove, drill holes.
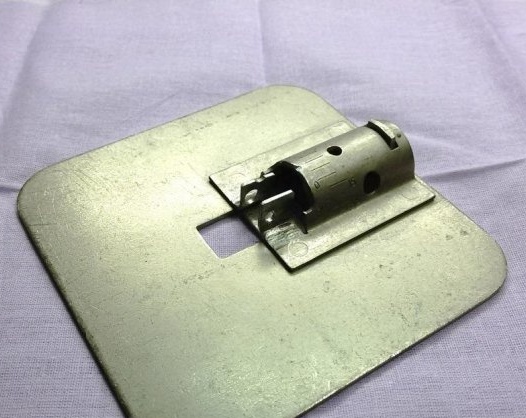
5. Assembly of the support.
We install the axis in the base of the support. When assembling, we install a support roller and a washer on the axis to adjust the clearance (if necessary). First, we perform an incomplete fitting-fitting with control and adjustment of the gaps. Then we collect it finally. A clearance-free connection of the axis with the base of the support is desirable, due to an exact landing hole or a connection with a slight interference fit. Fix the axis with a nut and a split spring washer. Since the axis was clockwise, the nut turned out to be a windup wing nut from the alarm clock. We remove the nut plate (little space) and get the desired nut with a slot.
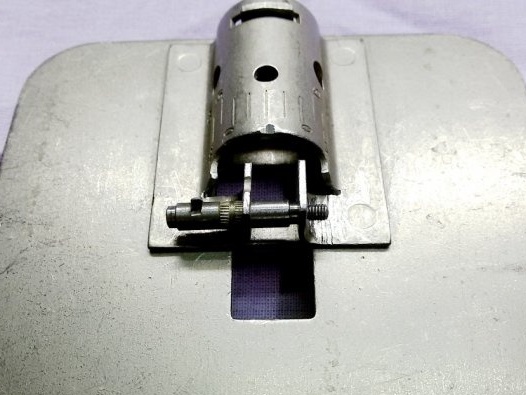
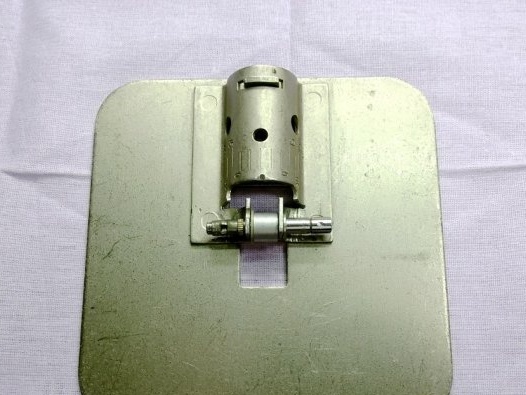
6. Machining the guide groove.
We mark on the roller the location of the guide groove for the hacksaw. It runs along the centerline of the table and the window under the tool. With the help of an engraver and an abrasive cup tucked into a cone, in a marked place, we process the guide groove.
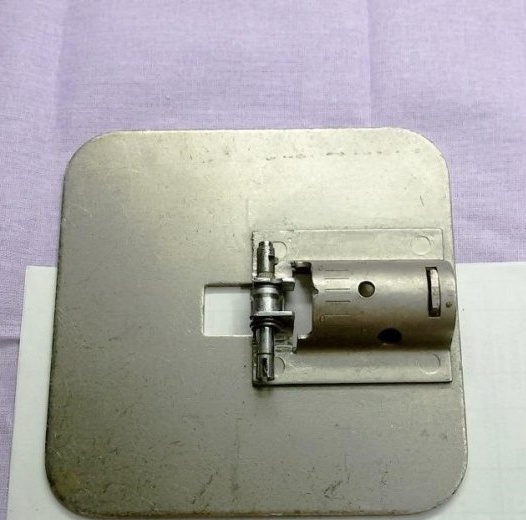
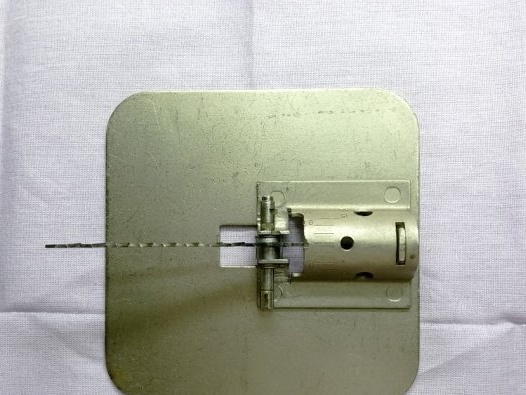
7. Making a table for the machine.
For the manufacture of the machine table, we use a laminated chipboard plate of the required size for the design of the machine.
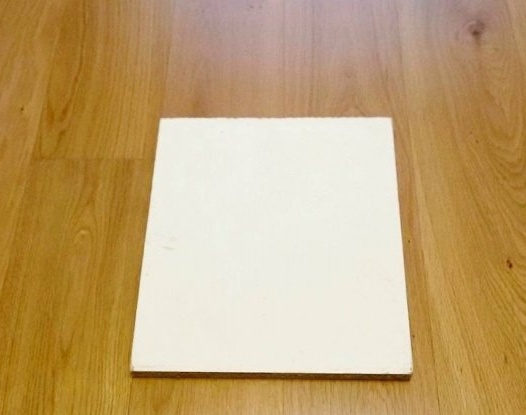
Mark the location of the desktop jigsaw and the position of the tool (hacksaw). We drill a hole under the tool. Using a milling device, according to the markup, we process a decrease in the thickness of the jigsaw table (2.5 mm). Cut the discharge to locate the mechanism for turning the jigsaw table.
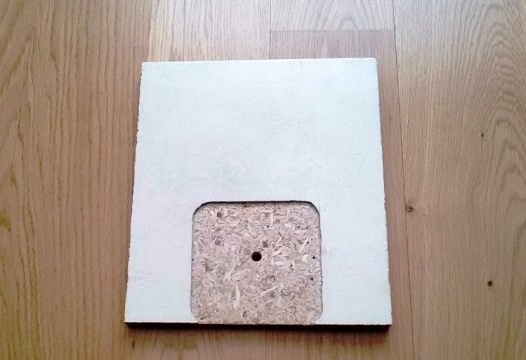
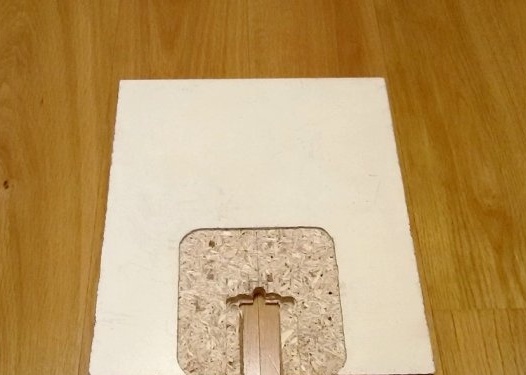
In the working table of the jigsaw, we mark and drill 4 mounting holes with a diameter of 4.0 mm. We make a countersink of the holes for arranging the screw heads flush with the surface of the table. We install and fasten the desktop of the jigsaw with screws.
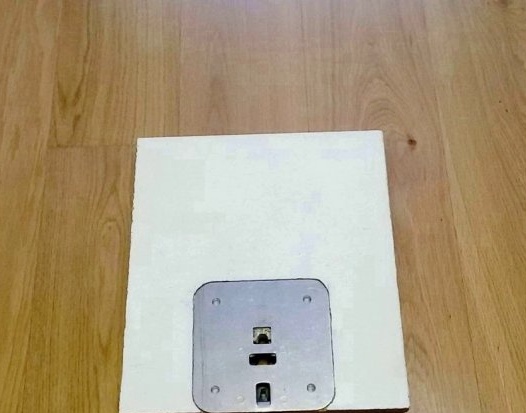
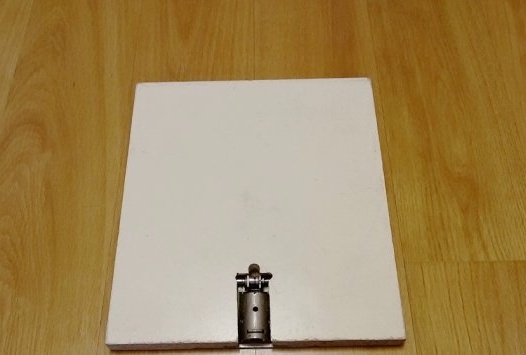
8. Final assembly of the hacksaw.
We mark and drill fixing holes with a diameter of 5.0 mm in a small jigsaw table. We verify the location of the jigsaw mechanism relative to the installed desktop. We fix the jigsaw mechanism on the underside of the machine table. For fastening we use screws with a diameter of 4.0 mm with a flat lower part of the head. This will allow, if necessary, to make adjustments to the position of the tool within small limits.
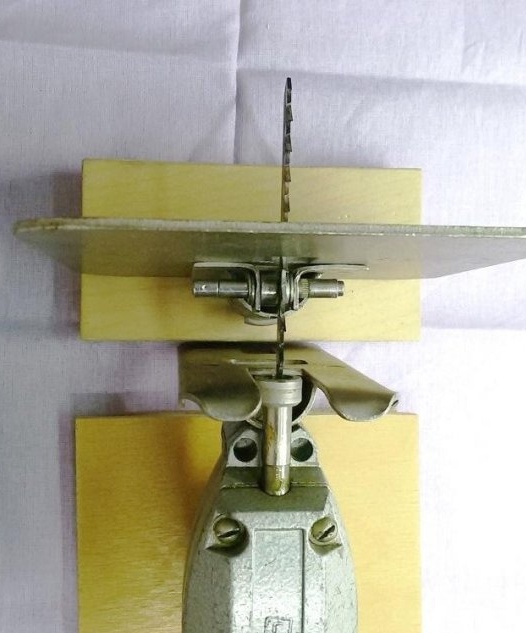
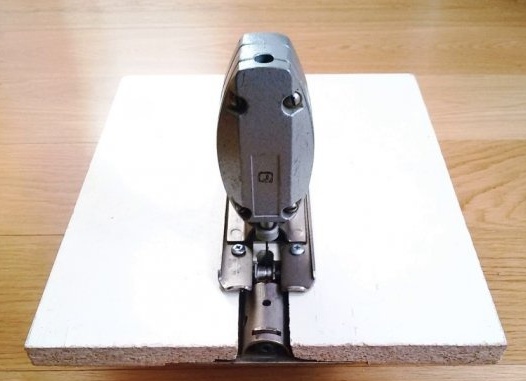
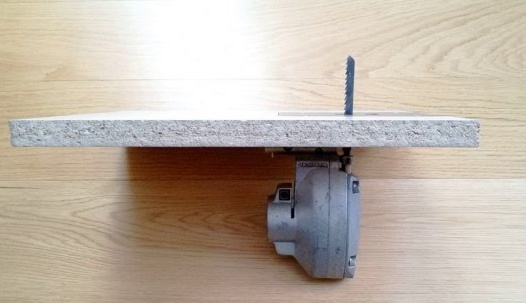
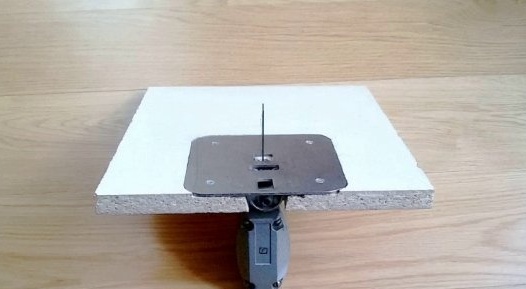
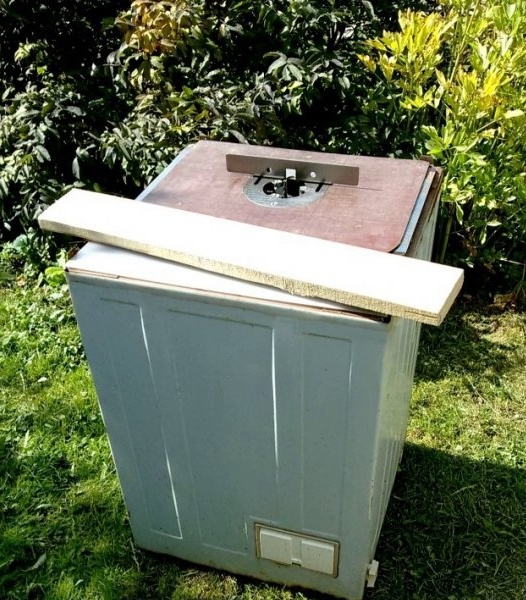
On this, I consider the manufacture of a hacksaw machine (jigsaw) mechanism complete. Warm days will soon begin and the manufactured device (as necessary to use a jigsaw) will take its place on a kind of machine bed. I use the body of a former washing machine as a bed. It has sufficient rigidity, ergonomic height, places for mounting the table, a switch and a box for storing the power cord. The previous home-made work is already working on this bed - a milling device based on the "Universal" electric drive