Today I want to tell you and show you how I made a large-sized homemade cone for a drill, or a drilling machine, which is convenient to process metal pipes from the inside, removing the weld, or slightly increasing the inner diameter.
Recently, making parts of a lathe on wood, I again faced with the need to insert a section of one pipe into another ... I say "again" because when working with metal (profile, or round pipes), I often had to apply such solutions . And each time there was a need to remove the weld inside! After all, the pipes are mostly welded. And, if the seam is practically not visible from the outside, it is always inside. Sometimes (quite rarely), shining through a section of pipe with a flashlight, and carefully examining it from the inside, it was possible to select a section with a weakly defined seam ... But this is rare. Basically, I had to clean it. And this is that work!)))).
I tried different ways ... And a round file ... And it is the same, only without a handle, clamped into a drill.)))). (The latter method, by the way, is quite effective, but now, it kills a file very quickly.)))))
This time I felt sorry for both my hands and the file))). So I made a temporary device from a piece of round timber (some unfinished part that I picked up in the waste at a metalworking enterprise):
Having glued the pin with double-sided tape, I wrapped it with sandpaper:
This allowed me to process a short piece of pipe from the inside, holding my tool in the chuck of a drilling machine.
So, as a temporary solution, it might be useful to someone).
But just as temporary .. (In a fire, as you know, and .... a well-known body -
Branzboyd!

But there are many shortcomings in this design. The main one is that under the sandpaper there is a soft layer (double-sided tape), because of which it does not “scratch” very well, and if pressed tightly, it easily breaks through, being pressed through by the protrusions of the weld. And changing it is quite problematic ... Yes, and the direction of rotation must be controlled and can not be changed, because if you glue it “in the joint”, then the sandpaper breaks. Therefore, we have to "overlap".
And since the processing of longer pipe sections was waiting for me, I began to think about creating some kind of permanent tool for such work. The various cones available on the market did not suit me, first of all, because they were short. And, if they are more authentic - then, usually, of a large diameter. I need to "climb" into the pipes ...
..A prototype of my future creation was a grinding drum for an engraver:
Here is something, but bigger and more authentic, I decided to come up with. Looking ahead, I will say that I succeeded.
And here is what I needed for this:
1. Emery cloth on a fabric basis.
2. Plastic tubes from fax paper.
3. Trim stud M10.
4. Bolt M10. (Not necessary. You can use the same hairpin.)
5. Cutting steel pipe DU-8.
I began by making removable work items. Initially, I was supposed to use an emery cloth, so I began to think about how such a "mass and unnecessary" can be used to make the base of grinding drums. I remembered the plastic tubes of fax paper.
(I don’t know, I’ll explain. The fax machines use special paper, which is sold in rolls. A roll is wound, for some reason, not on a paper sleeve, but on a composite plastic tube. When the paper runs out, three such tubes remain in the compartment:
In every office they are thrown in large quantities.))). I, as a "sick master", collected a package of such tubes on the table, although I had no idea what they could be made of.)))) And finally, I came up with ...
I tore the abrasive cloth on a fabric basis into narrow tapes:
He tore, not cut. I would probably not be able to cut along very evenly. Therefore, making a small incision, then simply bursting. So it breaks very evenly parallel to the warp threads.
In order to make it more convenient to work, I put the tube on a piece of metal pin:
(Do not pay attention to the "stencil".))) I painted something before this.))))
Then he smeared the tube and the skin with glue. Clay took the first suitable one. Once I bought a cheap “to be” cheap at a fixed price store)):
Giving them a little dry (as written in the instructions), I wrapped the tube tightly in a strip of hide:
And fixing it, left to dry:
I’ll tell you what I fixed.
I noticed that the tube fits very tightly into a piece of twenty polyethylene water pipe:
I cut a piece of pipe and cut it along:
Then he realized that, even when cut along, it is difficult to fit on my pipe.
Even smooth. And I definitely won’t wear it with an abrasive .... Then I cut this “clip” into many narrow rings and used it to fasten sandpaper in a pair of these:
In the meantime, the glue dries up, I started manufacturing the drum shaft. Earlier, I picked up a piece of a metal tube DU-8 in scrap metal. My plastic tubes fit tightly on her. So I decided to make a drum out of it.
The tube got "reinforced." Its inner diameter was a little more than eight mm. (Apparently, this is a piece of the old gas pipeline. Remember, before these came from gas cylinders on the street?). :
I made an incision at the end of the tube:
Then he cut off a piece of the required length and cleaned it:
The pipe will play the role of a drum. But to clamp it in a cartridge will not work in every drill. After all, basically, the cartridges of household drills have a working diameter of 10, or 13 mm. Therefore, you need to make a shank of a smaller diameter. For this, I used an M10 hairpin trim:
At one end of it, I made several longitudinal grooves to the depth of the thread with a grinder:
Then, with a heavy hammer, he hammered into the tube about two-thirds of its length.
And at the other end of the tube (cut) I cut the M10 thread:
Due to the cut, the thread was cut in a smaller diameter than is required for it. The tap simply unbent the tube to the missing millimeter fractions.
After that, I took the M10 bolt and slightly sharpened its end:
Twisted it into a tube:
And cut off:
Then, with the help of a angle grinder, he made a slot for a flat screwdriver in the end of the cut bolt:
Turned the resulting cork. The surface of the drum, in order to prevent the smooth plastic tube from slipping on it, I scratched along the metal sheet from the reciprocating saw:
This leaves very deep scratches with sharp edges.Now, even if you just put the tube on, it is almost impossible to turn it around.
When the glue had dried, I, using a knife, evenly cut the ends of the sandpaper on the tubes:
All! Dress the tube on the drum:
And screw in the cork. She wedges the tube on the drum:
As practice has already shown, such a cone much better copes with welding seams inside the pipes. It will also conveniently process (expand and grind) holes drilled in metal.
I have a lot of fax paper tubes. (Yes, and collect them in the office as they appear, I will be all the time))). It’s very easy and quick to glue sandpaper on them - I watched about thirty pieces of it while watching a feature film, with “re-coffee shops”. So far I only need rough ones to grind the seams. And you can do it with a finer grain size, to clean up inaccessible places. And, even, paste over one tube with felt - under the GOI paste. So, the tool turned out even with more functionality than originally intended.
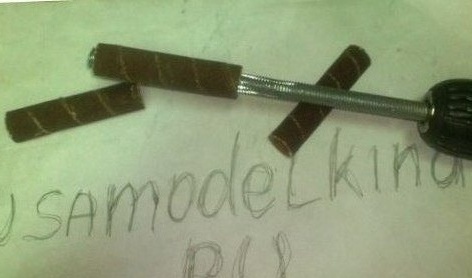