Our world does not stand in one place, so the most cutting-edge technologies are manifesting themselves in industries where it might seem like to come up with something new! The most striking evidence of this, which can safely be given here as an example, are fuel briquettes. Or as many call them - Eurodroves. This is all the same wood that our ancestors heated, but due to the fact that in the process of briquetting it received some new properties, due to which it can burn with greater efficiency.
To create fuel briquettes do not need any forbidden technologies, space developments, etc. At the heart of the simplest briquetting machine is a conventional press. Therefore, to establish the production of such firewood, with some improved properties in relation to ordinary firewood, is quite real. A fuel briquette is chopped wood, a variety of shavings, sawdust, coal waste and even husk from seeds that are pressed into a specific shape, convenient for storage and transportation. There are also other advantages of this type of fuel. Here is some of them:
Increased combustion temperature and correspondingly higher heat transfer. Since briquettes are compressed under high pressure, they accordingly have a higher density, which allows them to burn longer compared to fuel of the same volume. Briquettes reduce the amount of soot and ash. And much more.
That's about such a machine, which do it yourself made by the author of the YouTube channel MikhalychTV or with his own hands and will be discussed in this article.
To work, you need:
welding machine
Bulgarian
drill with drills of different diameters
Step 1.
The author proceeds with the manufacture of loading bins. For this, a square profile pipe is used. 4 workpieces of the required size are sawn off, in which places for holes are first screwed up, and then the holes themselves are drilled in all all the workpieces from all 4 sides. After this procedure, the surfaces are sanded both internally and externally. Further, all the parts are welded, pre-placing between them a wire with a diameter of 6 mm. This is necessary so that during the pressing of the fuel mass moisture can freely come out of it.In order to prevent the mass from loading up the inter-capacitance gaps, plugs from the same wire will be welded there.
Step 2
4 metal strips are cut, which will play the role of a skirt on loading containers. They serve as limiters so that during loading the fuel mixture does not fall out of the containers. After the author makes the bottom for containers. It must be opening so that the resulting briquettes can be easily and conveniently removed from the machine. A plate is cut off, which is reinforced on the sides by stiffeners from a profile pipe or corners. This is an important point since this part of the machine will bear the entire load during the operation of the press. Holes are also made in the bottom. A swivel is made to open the bottom.
Further, the author makes the so-called pistons, which will go inside the loading containers and compress the mixture. To do this, 4 pieces of a profile pipe are welded to the plate, at the ends of which are welded pads, the size of which is the diameter of the loading containers. These pads will press on the mixture and press it. The top of the piston group is reinforced by angles. A hydraulic jack will be installed on it.
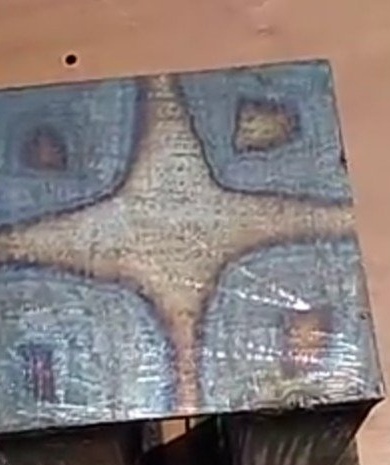
Step 3
The author begins to assemble the manufactured parts into a single whole. The bounding skirt and machine supports are welded to the base. The bottom is put.
Step 4
Stops for a hydraulic jack are welded to the base of the machine. The jack itself is mounted on the cover of the piston group and on the transverse crossbar to which it is fixed using angles to a movable bolt connection. The long handle on the side helps in lifting the jack and piston group for filling the fuel mixture. Of course, this is very inconvenient both in terms of loading and in terms of operating the machine. Nevertheless, the idea is quite interesting and workable.
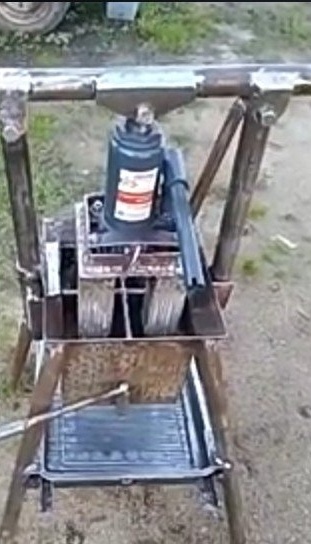
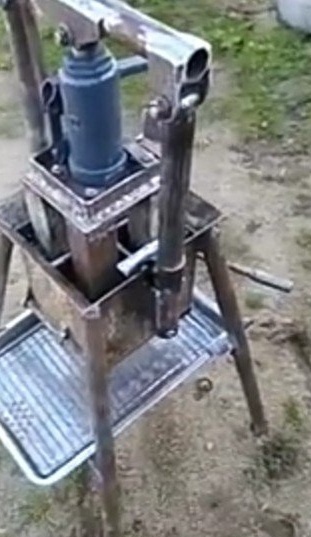
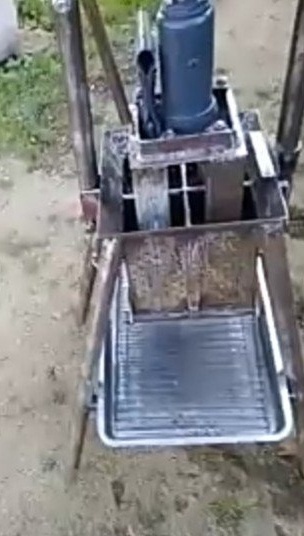
Here, according to the author, the result of this machine. Loading more or less mixture, we get briquettes of the size you need at the output.