Vacuum impregnation is the most effective way to make the liquid creep deep, even into the small pores of the sample. Vacuum technology is not the easiest and most accessible area of life, however, even the simplest device, which creates a very modest rarefaction in a very small volume, can serve as a significant help in home workshop. With it, you can saturate winding products with varnish or compound, deeply stain small samples of wood, and degass the compound before pouring.
- A great way to improve their performance. In the home workshop, impregnation, among other things, also allows with some optimism to use the old winding wire. Particularly impressive is the reduction in “buzz” of sufficiently powerful power transformers rewound or made - they are practically numb. To distinguish by ear their inclusion in the network is very difficult. The only point is that signal transformers (interstage and output in high-quality tube type UMZCH) should not be impregnated. An increase in inter-turn capacitance decreases the bandwidth of their transmission on the RF. Deep impregnation with a compound based on epoxy glue (or diluted glue) also makes it possible to obtain high-voltage transformers. Another way to obtain an impregnated coil is layer-by-layer impregnation during winding, which is much more dreary and unpleasant for the “operator” than the use of vacuum.
It may seem very limited in application due to the small size of the chamber, however, there are several areas where even such an impregnation chamber is enough. For example, wood intended for the manufacture of musical instruments is often soaked (with linseed oil). After polymerization of the oil in the pores, the pieces of wood are much better processed, the risk of chips and cracks is reduced. There is also a very interesting direction of decorative turning on wood - segmented turning. Its meaning is in the manufacture (gluing) of billets for turning from smaller wood billets of different colors (different species). Turning from such a workpiece allows you to get gizmos with a very bizarre pattern.
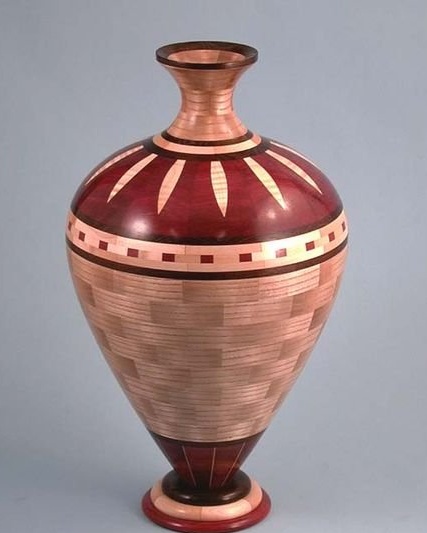
Trees of contrasting to common light wood flowers, are valuable and expensive species of wood.The deep coloring of even small samples of local inexpensive wood will significantly reduce the cost of harvesting, at least at the stage of the first experiments and testing the technology.
A common case in practice is the “forcing” of bubbles from a prepared epoxy glue (compound) before pouring a certain volume. It is used both in technical and decorative castings, no bubbles are strictly needed either there or there.
As a vacuum chamber, a piece of standard glass jar was used. This allows impregnation directly in the chamber without an intermediate tank (fully utilizing the volume of the chamber), while it is convenient to heat the chamber from the outside (water or sand bath). A vessel from a standard glass container is not very valuable, with severe contamination it is easy to make a new one.
As a vacuum pump, a manual plastic similar to a bicycle counterpart is used. It is intended for pumping air from plastic bags with clothes (convenient and compact storage). Kits of this kind appeared on sale (Ali Express), their cost is very low. By the way, such a bag, without any changes, in its original form can be used as a vacuum clip of a photo template for contact printing (image transfer using photographic varnish) This will reduce the flare from exposure under a loosely pressed pattern.
It should be said that there are similar domestic systems. For example, for vacuum conservation. The kit is a special cover with a check valve and a similar pump. The kit was found to be unsuccessful for use due to an inconvenient cover and mainly, overly high cost. On the other hand, if it is necessary to process small workpieces crawling through the narrow neck of a standard can, this can be a good solution.
What was needed at work.
Instruments.
A set of small bench tools, a jigsaw for sawing wood with accessories. A device for cutting bottles (you can do another way of cutting, for example, a thin nichrome wire heated by a current, a diamond disk for a drill). The hair dryer is construction.
Materials
Set (the smallest bag, pump) for compact storage. Silicone sealant, a piece of organic glass of a suitable size, a piece of felt, a sandpaper of medium size on a rag basis. Standard glass jar.
Let's get started.
As already mentioned, if it is necessary to impregnate small things crawling through the neck, it is best to use a ready-made kit for canning, however, the author most often has to deal with larger workpieces. Having removed a narrowing with a neck from a standard glass jar, we get a beautiful vessel. It is of a sufficiently large volume (it is not difficult to find a jar with a capacity of 5 l) transparent (observation), within reasonable limits it is durable and very cheap. Having pounded or chopped it, it is not difficult to make a new one.
In the photo, the camera is made from a trimming can with a capacity of 0.75 L, for impregnating the coils of the rewound transformer TS-180. The coils are placed tightly, while the consumption of varnish to fill the chamber is minimal. The lid is made for universal use, and is suitable for a jar vessel with a capacity of up to 3 liters.
When cutting jars applied bottle cutting tool. The scratch in the machine is applied completely evenly, its edges are closed. To create a crack, a construction dryer with a narrow crevice nozzle was used. The can (bottle) rotates (uniform heating) above a stream of hot air. We warm the place with a scratch. We immerse the warmed jar in a bucket of cold water to the cut level. Sometimes the operation has to be repeated.
The resulting slice is not particularly smooth. A storage vessel with such edges (sharp edges dull) is acceptable, for our purposes, the edge will have to be aligned. For single works, it is not difficult to grind the glass edge manually. To do this, a piece of medium-sized sandpaper on a rag base is placed on a piece of felt (sheet rubber?). The jar is pressed against the abrasive with an uneven edge, it is rotated with pressure. Moisten the skin with water.Rinse the jar and skin regularly from glass sludge. Hands get tired pretty quickly - work is best done with “approaches”. The edge of the felt is better to fix, then you can work with both hands using your weight. Felt holds the skin well by friction.
The lid of the vacuum chamber is made of a piece of organic glass with a thickness of 6 mm. Sheet plexiglass is well sawn with a jigsaw on wood.
The non-return valve is cut from the bag and glued to the lid on top (will be pressed by pressure) with silicone sealant.
A flexible gasket is also molded from silicone sealant. The edge of the can during manual processing does not work perfectly "trimmed", bumps of several millimeters can easily be neutralized by a thick and relatively soft gasket. In addition, the sealant layer is easy to upgrade.
He acted like this - he applied a thick sausage of liquid sealant to the contour of the throat of the vessel, covered it with thin "sausage" polyethylene (silicone does not stick to the film) and pressed it evenly. It is convenient to use a piece of glass. Please note - the valve must be open (the rubber band is removed or ajar), otherwise the silicone will squeeze out with an air bubble.
The resulting layer with a thickness of about 4 mm, after two days of polymerization, showed itself well in testing.
The created vacuum is limited by the design of the pump (the walls are cracking) and the elastic rubber band of the valve. Without extreme loads for the design, it is possible to saturate the transformer coils with liquid (heated) varnish well.
Babay Mazay, May, 2019