I would like to share one of my simple idea. Homemade useful to those who solder a lot and worry about the condition of their lungs.
It's no secret that breathing various fumes emitted during soldering is not very good for your health. You can argue for a long time on the topic: the more harmful it is to breathe the evaporations of flux or solder, which flux is less harmful: rosin or glycerin. I think many will agree that it is better not to breathe any of the above. I know 2 solutions to this problem: hoods and hoods using various filters (for example, coal). I did not consider the option with filters, as there are questions regarding the quality of the filtering. There is an option with a hood to the street. I did not want to make any massive pipes for the outflow of air to the street, I wanted to have some kind of compact desktop version, which, if necessary, can be quickly put away in a cupboard.
I came up with a simple idea: to solder by the open window on the windowsill / balcony, and use a compact and powerful fan to extract it. For the cold season, the option, of course, is not very suitable (although I still manage to solder, dressing warmer), but for other cases it’s quite working. I could not quickly find ready-made desktop fans that were compact and powerful enough (either too bulky, or the power was small). I also wanted a lamp. Therefore, I decided to make such a fan myself. It looks something like this:
Pulls perfectly:
Process of creation:
I did not immediately come to the current version. At first I tried the usual 120mm fans for computers. Traction was clearly not enough. I decided to make a home-made fan from the collector motor from a screwdriver, a screw from a computer cooler and cabbage cans:
In general, everything worked, the thrust was excellent. The engine was too powerful for this purpose. An adapter for 2 Chinese amperes was clearly not enough, the power supply was very hot. The screw was fastened to the motor shaft using the clips from the mounting clamps for the chandeliers
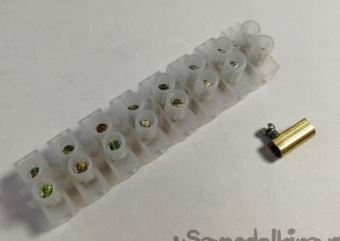
The fastening was extremely unreliable, which led to the screw coming off the shaft and breaking the case. Only then I realized that the right solution is to use a collet chuck.
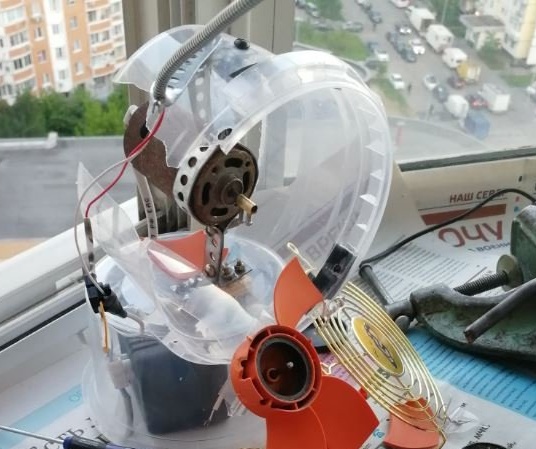
The idea came to my mind: to look for more powerful 120 mm fans for servers. I found one on Ali and ordered it. It pulls, of course, not as much as a home-made one, but also quite worthy + current consumption of only 0.6A.
The stand was also made more accurate, and also added a protective grill to the fan:
After that, he placed switches in the case and painted the base black with matte primer from the spray can.
Later he replaced the grill with a more open one.
As a luminaire, I used a 4-watt LED matrix, purchased on Ali. The matrix is very hot, so a radiator is needed. Also added a small fan to the radiator. He fastened everything with iron clamps, screws and rubber rings cut from a bicycle chamber.
The lighting was good, you can solder at any time of the day, everything is clearly visible.
All parts are connected by wires - mounted mounting.
For stability, I placed a counterweight from an iron plate wrapped with tape in the base (for insulation just in case).
Inside there is a lot of free space, there I store a 12 V power cord with a cord when I put the fan in the cabinet.
List of used parts:
• Powerful 120mm x 0.6A fan. Standard 0.1-0.2A are not suitable, because very weak.
• Power supply 12V 2A (Chinese), in fact 1.5A
• The lamp on a flexible leg from FixPrice (used only a leg)
• LED matrix 12V 0.3A
• Small aluminum radiator
• Small 40mm 12V fan
• Plastic first-aid kit from Auchan (case - base)
• 2 switches (for fan and lamp)
• Electrolytic capacitor 16V 2200uF
• 10k resistor
• Ceramic capacitor 10mkF
• Socket for power supply 5.5 x 2.1
• Iron corners and strips for installation
• Fan grille
Device Diagram:
Explanations according to the scheme:
The scheme is quite simple, but there are some subtleties. An electrolytic capacitor is added to the common input. When the main fan starts, the current consumption sharply increases, which leads to unstable lighting operation (up to the point that it goes out for a second). Capacitor solves this problem. So that after turning off the capacitor does not remain charged, a 10k ohm resistor is soldered to it in parallel.
Also, a 10 uF ceramic capacitor is soldered to the input of the LED matrix to stabilize the matrix power and protect against interference that a small fan can create.
In general, I am satisfied with the project. It’s quite simple to quickly deploy everything on the windowsill and is also easy and quick to clean. The experience of creating home-made fans (from collector engines and cabbage cans) was useful to me for creating a model of a radio-controlled boat with a propeller, but this is a completely different story ...