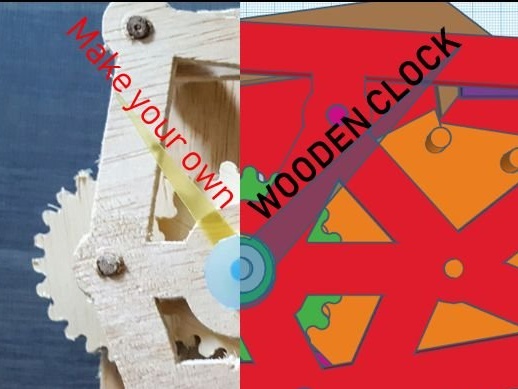
In this guide, the Wizard will tell us how to design and make a watch with a mechanism of wood. For the manufacture of such watches, the master used the following
Tools and materials:
-Plywood;
-Fasteners;
- dowel;
-A thread;
-Drill;
- CNC milling machine;
-Nadfiles;
-Sandpaper;
- Joiner's glue;
-Scissors;
-Screwdriver;
-Hacksaw;
-Bottle;
-Computer with software;
Step One: Design
The master made the entire development of the clockwork in the Tinkercad program. Tinkercad is a free and easy-to-use application for creating 3D models and turning them into a real product in a simple, fun and intuitive way.
It all starts with choosing the right shape. There are several ways to do this, Basic Shapes (basic shapes) and Shape Generators (shape generator).
Basic shapes are primitive shapes (Boxes, Cylinders, Spheres), these shapes can be combined with each other to create almost anything.
Shape generators allow you to quickly create complex shapes. You can find springs, curved text, gears.
Going to B> ALL> Shape Generators, you can change the shape. Place the mechanism on a work plane. To change the properties of a gear, click on it in the pop-up window. You can change the pitch, height and number of teeth.
Some figures need to be combined. To do this, you need to place the shapes in the correct order. To resize, you need to select the cylinder, then click the white square on one of the bottom of the cylinder and change its length and width. The white square at the top of the cylinder will change its height.
Using alignment, the master will align both parts in the center.
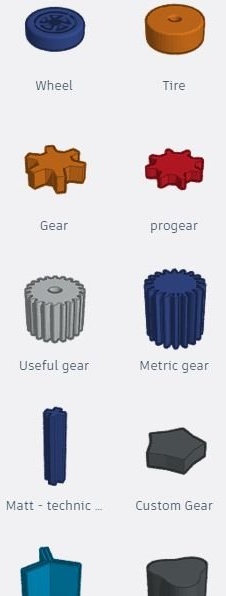
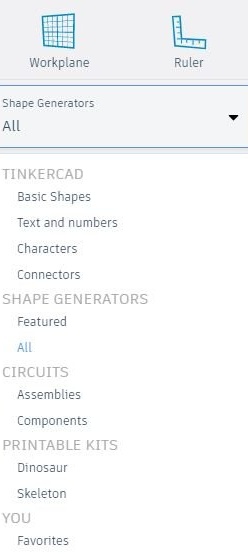
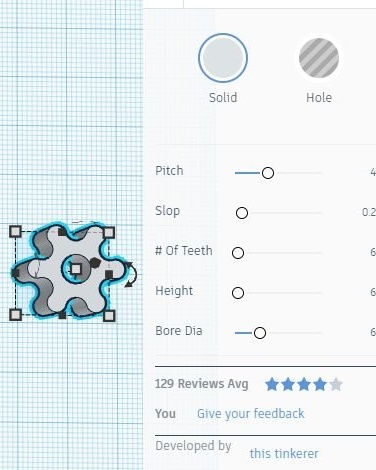
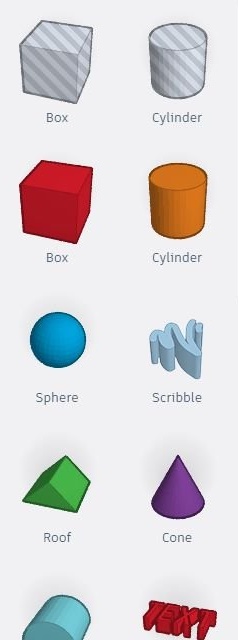
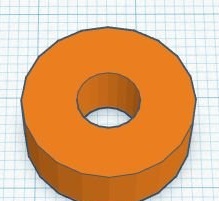
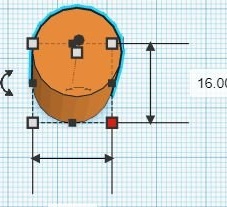
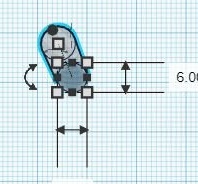
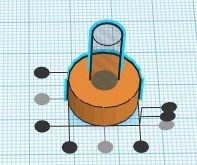
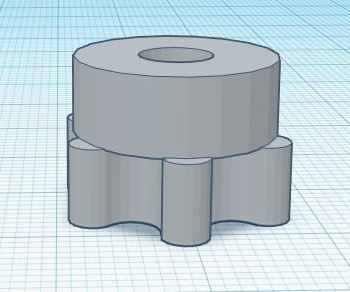
It is necessary to calculate the gear ratio and direction of the gears. You can do this manually or use the gear calculator. Then we need to create the remaining gears and form the gear train. The dimensions of the mechanism can be seen in the photos.
Further, the master designs the pendulum mechanism.
Develops a mechanism case.
Now it remains to export model for CNC machine.
You can download the file.
Step Two: Cutting Parts
Parts can be cut manually or using an CNC machine. The master cuts partially on the machine, and finalizes manually.
Arrows cut out of polypropylene.
Step Three: Build
After about 3 hours, all parts are ready for assembly. Gears checked, then glued with wood glue to the axles. The hole of one of the gears turned out to be weakened and the master had to redo it.
Step Four: Calibration
Now that the watch is assembled, you need to calibrate the pendulum so that the watch works efficiently.
The master winds the thread and ties the load to the end of the thread. Next, you need to install two levers at the desired angle and tighten the screw.
It remains to establish the hands and, if desired, the dial.