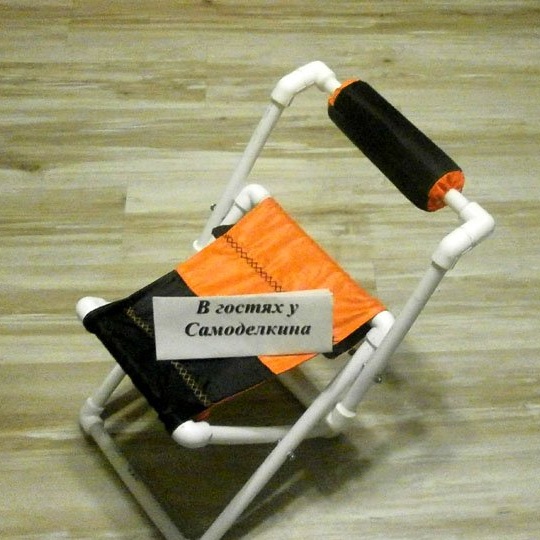
And it all started with a picture that accidentally caught my eye.
But only when I saw similar folding chairs live, two unpleasant remarks arose. They are:
• Above highchairs. And the child will not be completely uncomfortable sitting on them.
• Made of metal. So, it’s heavier than a similar one, only from plastic pipes.
Plus, my hands were scratching something to do. And if so, then we go to create.
So, the basis of the stool, a plastic pipe. Standard, 4 meters long and 1/2 inch in diameter, “twenty” or DN20. Who likes what name.
It needs to be cut into 12 pieces:
• two 25 cm long and two 40 each: they will go one on legs;
• smaller, by 5 cm: 2x20 and 2x35 cm - on the second legs;
• on the contrary, large: 2x30 and 2x45 cm - to the back.
You will also need 12 angles at 90 degrees for this pipe;
8 coupling bolts, those smaller than M4, with only the counterpart;
long (enough for two) M4 screws - from them four studs 25 mm long with a thread must be made;
and a soft seat. I’m always plugged with fabric, so I asked my mother. She cut and stitched a piece with two gates and “clean” sizes of 20 by 30 cm in a few minutes. Without gates, it is longer, about 45 cm.
And then everything is simple. Using a soldering iron for pipes, we collect a rectangle, but in one place we do not solder it.
We put on a rag, and only now we close the structure. We also do it on the other hand. Done.
In the middle, we drill holes with a diameter of 5.5 mm, and with the help of 4 coupling bolts and two studs, we assemble them. They are too long, and under the hats had to put improvised washers - ordinary M6 nuts. One for each bolt.
In principle, the stool is ready, and you can already sit on it.
But it’s not so interesting. Therefore, we proceed to the back. And to make it even softer, we use a piece of heat insulator for pipes.
All the same mother, having seen a stool looming gradually, even sewed a small case on it.
I solder the back (not until the end, the last soldering after putting on the heat-insulator cylinder),
and tighten it. Lace allowances (I used ordinary plastic clamps) were also carefully left in advance.
I screw the back to the structure itself.But the holes for the connections are no longer in the middle, but closer to the edge.
When folded, it turned out just great.
But in the spread out - not ice at all. The back came out long, and it is also far removed from the seat: it will fall over with leaning on it - just spit. No, you need to invent and invent something.
A simple shortening is not the best solution: when folded, it rests on its legs and hangs. Therefore, you need something else.
The idea came by itself - the corners are not under 90, but 45 degrees.
We cut off the upper back almost end to end, leaving a couple of centimeters, and solder the corners to it.
Vertical racks are shortened by 15 centimeters, and also soldered. Done.
We collect again. Nothing hangs anywhere (I deliberately chose such dimensions that the structure when folded was "tightened"), it only became a little thicker.
Then, as in the unfolded form, it turned out just right. The little son of two years old, immediately appreciated the resulting product. It is only necessary to drive away the older brothers from him: they will precisely crush the chair with their weight.
It remains only to go into nature and test it "in the fields."