Homemade electric burner fusing oven good for many, but there were two very serious flaws in the existing configuration. Oven even in insulated version had a rather large loss of radiation (at high temperatures), this did not allow the correct annealing of the sintered parts - the glass after the furnace had significant internal stresses. This led to increased marriage. Often, parts burst when soldering (installing them using Tiffany's stained glass technique).
The second point is a great inconvenience, however, of purely organizational meaning. Manual control of the fusion progress manually by timer. At the same time, the operator was tied to the furnace for hours. Having missed an important point, one could easily spoil a valuable workpiece. The use of an inexpensive Chinese-made programmable industrial controller made it possible to neutralize both shortcomings and make the work as simple and technological as possible - I put it on, turned it on tomorrow, took the finished one.
In general, the entire process of fusing glasses must obey a certain complex time-temperature dependence. Often called her
Consider the first reason for previous periodic failures - poor annealing. The low thermal inertia of the furnace is to blame here - the light refractories of the enclosure of the working chamber quickly heat up and cool down quickly, while relieving stresses in the glass requires not only exposure at a certain temperature, depending on the type of glass, but also a very low cooling rate. Not less than (degrees / sec). And when you turn off the heaters of the furnace, it turned out more than (the same degrees / sec). Therefore, frequent marriage. That is, the regulation was carried out manually - turn on / off the oven, turned it on - it heats up at its own pace, turned it off, it also cools down. And if the heating rate (also important) can be slowed down by switching on additional resistance in series with the furnace heater (it is reasonable to reduce the heater power inside the working chamber), then the cooling rate can be reduced only by changing the design of the furnace. Weighting the heated mass.A simple thermocontroller is busy only with the speedy achievement and accurate maintenance of the selected temperature and nothing more. All these your pace, not his task. So there were tensions inside the finished part - sometimes a little touch and a-ha. Moreover, even if you make a thick muffle, cooling will not be uniform - from 550 to ~ 300 ° C, the oven will still cool faster than from the same 300 to room temperature - radiation losses.
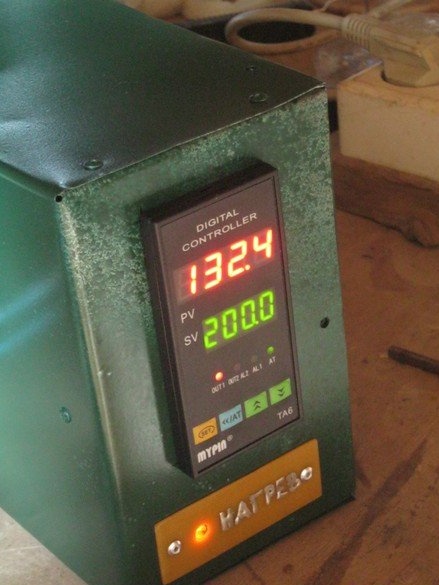
The use of a programmable temperature controller capable of independently maintaining the desired thermal profile inside the furnace, in addition to full automation - changing temperatures at the right time, completely solves the described problem. That is, the rate of temperature change (and its constancy) is set and very precisely controlled. At least those that the oven is capable of providing. Our two main speeds - initial heating and cooling at the end of the process, can be set and regulated to the full extent to the right extent. It simplifies, reduces the cost, facilitates and at the same time expands. Highly.
What was used at work
In addition to the actual furnace to be improved and the new controller, they came in handy - a set of tools for wiring, including a soldering iron with accessories, a small bench tool. For tuning and experiments - a timer, stopwatch, IR pyrometer, home-made polariscope (stress meter). The experiments were carried out with samples of art glass for fusing.
New controller
As the "Big Brother", the Chinese-made Altec-pc410 thermal controller was selected. His main specialization is application in BGA soldering stations. This type of microcircuit has soldering pads, at the bottom, and the microcircuit heats up during installation. From above. This leads to accurate tracking of temperatures and a controlled rate of their rise in order to avoid thermal shock. Unlike many analogs, for example, the popular “furnace” Aries-251, it is not the time for each step of the program that is set here, but the slew rate, which is a more significant and informative parameter for the mentioned soldering. But for working with glass it is also more convenient! In addition, Altec has more memory (programs) and costs more than half the price of domestic. Its disadvantages include a less obvious indication, without a drawn curve with LEDs, the Altec front panel seems more complex, without mimic diagrams, and since fusion stoves are used mainly by young ladies, this is a serious obstacle. However, it is programmed elementarily. Using is even easier.
Connection
Here, the temperature controller, for verification, was connected to a live thread to the old one. Instead of a conventional, single temperature, non-software controller. The controller is not installed in the case as expected - this is only a test of the device’s performance and ideas. In the future, the controller will work with a new, slightly larger furnace, in its box, with a three-phase load.
The control output of the device is connected to an existing thyristor key, and a signal from a K-type thermocouple (chromel-alumel) embedded in the furnace is fed to the input. The device additionally requires two external “Start” and “Stop” buttons. Moreover,.
In the previous version, to somewhat reduce the heating rate, an external resistance, an oil heater of 2 kW, was connected in series with the heater of the furnace.
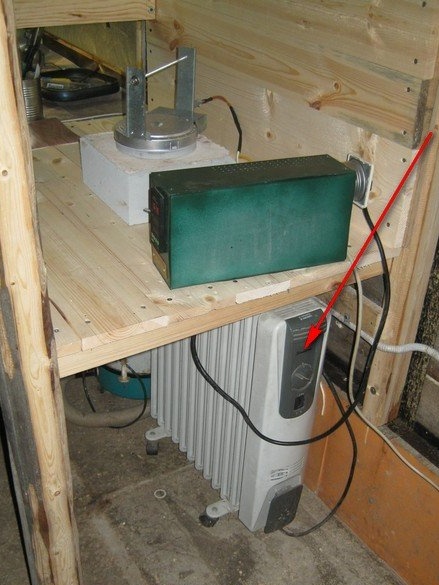
Now you can stop using it - the socket for connecting it has been removed on the back of the unit, the switching has been changed. At the same time, the efficiency of the furnace increases, and to a fair extent, the losses of electricity on the radiator are removed. Everything is in the house.
Programming
It should be understood that there is not one version of the described device - the so-called "Performance", which may well differ in minor details. The general principle, however, is one.
The device is, in principle, universal and should be configured before operation - enable the necessary functions, limit them to the necessary limits, disable unnecessary ones, change some parameters for convenient operation in a specific application.
The device is designed to work as part of soldering equipment. The maximum temperature is 400 ° C. In the factory configuration, the controller operates within these limits.
So. To enter the configuration parameters menu, press and hold for more than 3 seconds.PAR / SET key, find the parameter SP h and set its desired value. In this case, at least 800 ° C.
Thermoprogramming
Everything is very simple here. I will give a visual memo from the front panel of the developed control unit.
That is, the program consists of several steps, each step corresponds to three parameters: L - the desired temperature; d is the retention time; r is the rate of its rise. Yeah - one-two-three, one-two-three, one-two-three ... The rest is obvious.
conclusions
It turned out a miracle as well! Once tuned, the furnace works exclusively without the slightest hassle and is half more economical. Sintering has become a pleasure.
The front panel, with some habit, seemed quite informative and understandable. Even with a cursory glance, it’s easy to understand what point the program is working on.
I really wanted to connect the controller to the computer. There is such an opportunity, but it turned out - there is absolutely no reason. Whim and only. Easy to program without a computer. Once. Then only the necessary program from memory is called. Moreover, all the software (there are several options) for the PC-shnik, also for soldering - up to 400 ° C. Well, to hell with him.
Babay Mazay, November, 2019