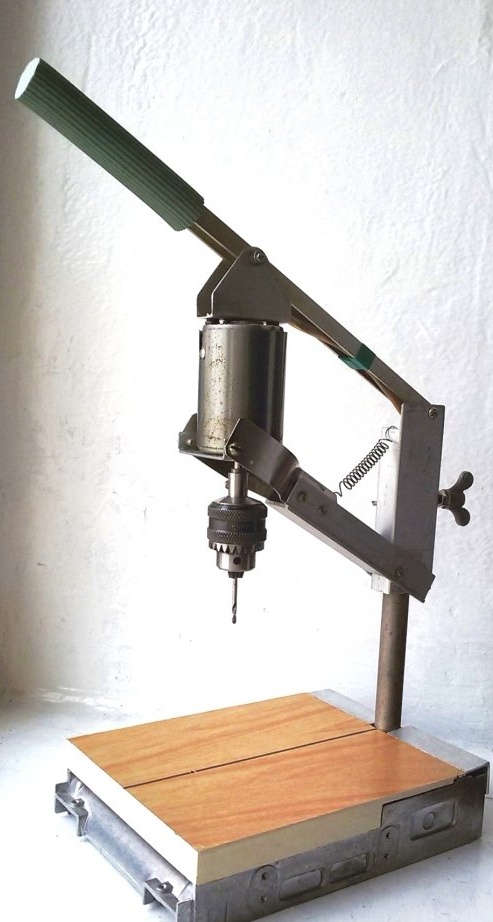
It is proposed to make a small drilling machine of a very simple design. For its manufacture, the pattern parts will not be required - precise guides, rolling bearings, moving mechanisms. If in your household there is a small instrument motor with a drill chuck on the shaft, then you can start work. We make the machine from improvised materials. Billets for components will not be difficult to find.
Design Features.
This machine is easy to manufacture, but has some limitations. Its design is designed for drilling holes up to 10 mm deep. The capabilities of the machine in drilling diameter and the material being processed depend on the characteristics (power, shaft rotation speed) of the electric motor used.
A limitation in drilling depth is associated with the design of the drill drive suspension. The device is based on a hinged parallelogram. Two vertical, equal in length and opposite links parallelogram, this is the electric motor and the base of the suspension. The remaining two equal and opposite links are the connecting elements. As you know, in this design, the opposite links will be parallel at any rotation of the links of the parallelogram. Therefore, the common axis of the electric motor and drill (in the exact manufacture of parallelogram elements) will always be parallel to the axis of the fixed stand and perpendicular to the machine table.
For reference, a rhomboid is a parallelogram in which adjacent sides have different lengths and the angles are not straight.
Setting up and working on the machine.
The position of the connecting links parallel to the table will be taken as the zero position. When machining a part on a machine, to increase accuracy, the location of these links should approach a horizontal position.
In this case, with the axial movement of the drill from +5 mm to -5 mm (10 mm stroke) from the zero position of the links, the radial offset of the drill (in the rhomboid plane) will be 0.08 mm. This amount of displacement will be at a link length of 150 mm. In practice, this displacement is imperceptible, and will not be critical for the tool and the hole being machined.
When drilling printed circuit boards, even with a brittle carbide tool with a diameter of 0.8 mm, the offset of the drill on the board with a thickness of 2 mm will be 0.003 mm (3 microns). Compare the given value with the offset and position of this drill when processing boards manually.
Setting the machine to the size of the part, in height, is carried out by quickly moving along the machine rack manually, the suspension base and fixing it with a thumb screw. The height of lifting and fixing the base of the suspension is visually determined by the risk of the zero position (plotted on the base of the suspension - the last photo) when touching the part with the tip of the drill. When drilling various boards with a thickness of 1 ... 3 mm, a readjustment in height is not required.
Additional design advantages.
The ability to install large-sized boards (with an increase in the overhang of the drill, the accuracy of drilling increases).
When releasing the handle, at the end of drilling, the motor with a drill under the action of the spring quickly goes up and back a considerable distance, freeing up the processing zone of the part.
In the highest position, you can conveniently quickly and safely change the drill.
I think that the above characteristics speak in favor of the manufacture of the proposed machine. The time spent on the manufacture of this machine design pays off in a good mood from the exclusion of breakdowns of expensive and scarce drills.
1. Applicable materials and details.
Electric motor and mechanical or collet chuck.
Pieces of a metal sheet with a thickness of 1.5 ... 2.0 mm.
Aluminum profile hire, pipe.
2. Making a table of a drilling machine.
First of all, you need to decide on the table of the drilling machine. Its size, rigidity and strength will determine the accuracy and ease of use. There are many different table designs. In the given version of the machine, the case of the CD player, which has long been waiting for its secondary use, is used. Rectangular case with dimensions of 145 x 200 mm, cast from aluminum alloy. It has low weight, a rigid structure and flatness along the periphery of the lower part of the part, which gives good stability to the future product. In addition, this part requires virtually no additional processing. For these reasons, the casing was taken as the basis of the machine table.
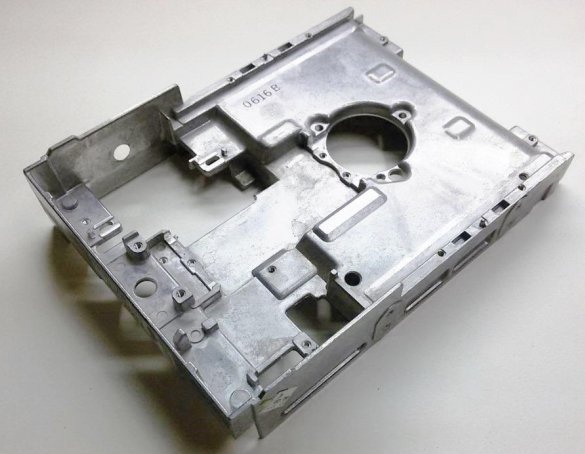
One of the short walls (in the photo on the left), in the middle, has a hole for the M8 bolt, which automatically determines the installation of the machine rack there.
As a rack, you can use rolled metal or a pipe with a diameter of 18 ... 25 mm.
The structure under consideration used a thin-walled steel tube with a diameter of 18 mm, which made it possible to simplify the method of fixing it to the table.
We select a bolt with an M8 thread and a head, the diameter of which fits tightly into the hole in the tube (it may require some refinement of the diameter). Screw the nut onto the bolt and press them into the tube. The stand is ready. It remains to fix it on the table with a second nut.
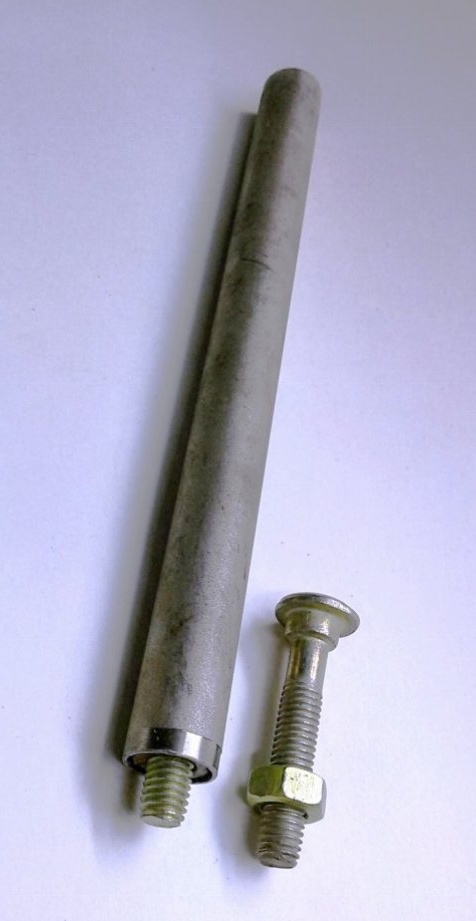
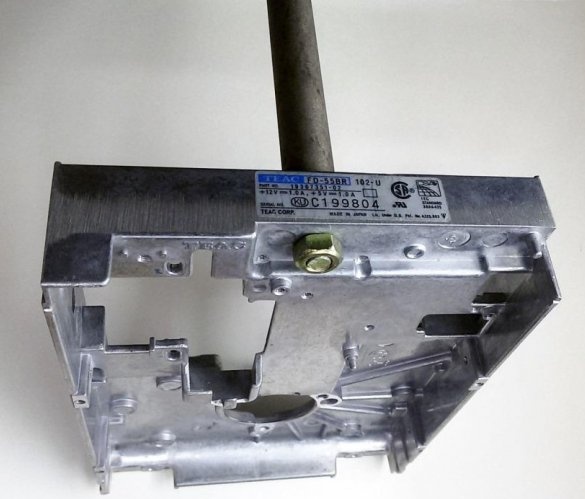
On the upper part of the table we fix the countertop cut from the laminated chipboard along the contour of the workpiece body. In this case, the machine stand will be additionally sandwiched between the wall of the housing and the countertop. In the future, on the free sides of the rack we fix the lining of an aluminum square. All this will provide the installed rack additional rigidity.
In the process, we check and, if necessary, adjust the perpendicularity of the machine stand to the table.
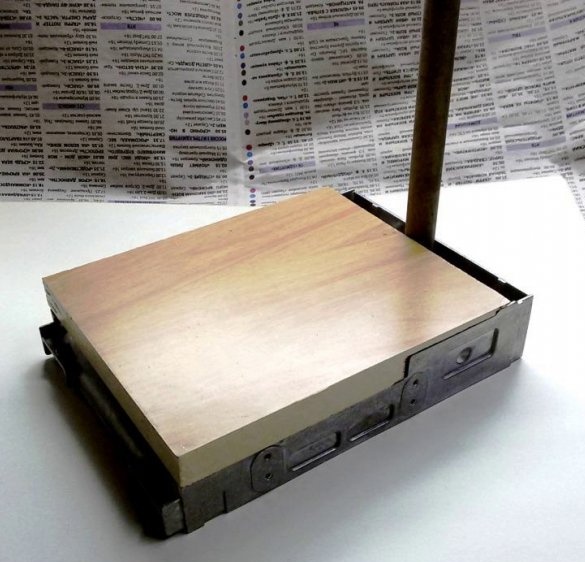
3. Making the base of the suspension.
The suspension base is necessary to install the articulated parallelogram mechanism on the machine stand. It serves as an integral part of the rhomboid, fixes it on the rack, at the desired height and at a selected angle from the edge of the table. Shaped aluminum profile (18 x 40 mm), which previously served as a furniture door handle, was used as a blank for the suspension base.
In the middle of a section of the profile, about two electric motor lengths, we drill a hole and cut an M6 or M8 thread under the fastening screw. We check the reliability of the suspension base installation on the machine rack.
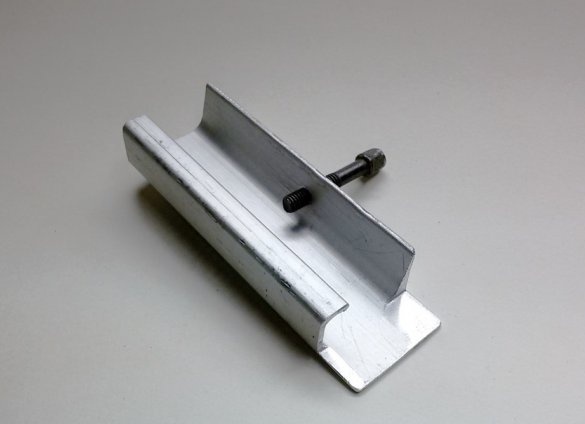
Manufacturing a mechanism for mounting an electric motor
4. Lower engine mount.
For the proposed drilling machine used a DC motor with permanent magnets DC 24V, 0.7A.
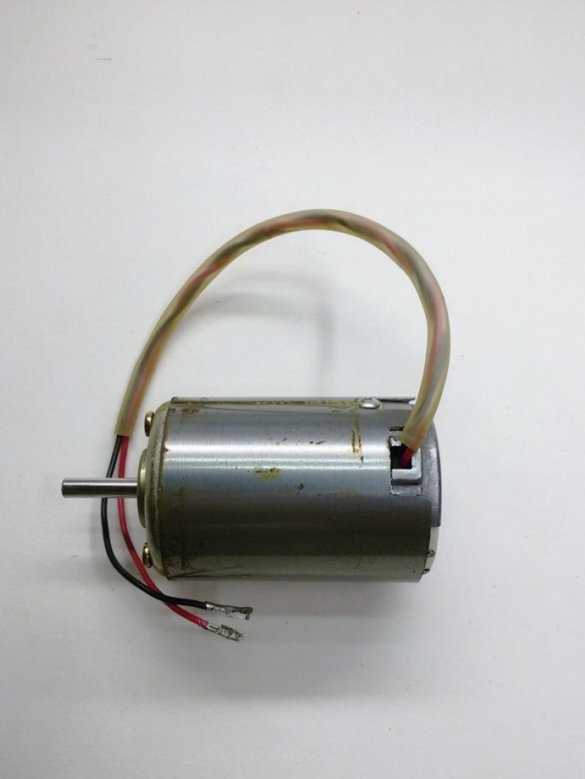
We begin the production of the articulated parallelogram with the main link, consisting of an electric motor and its fastening elements. The dimensions of the engine used may be different, as well as the location of the mounting holes. Therefore, the dimensions of the fasteners are not given.
From a steel sheet with a thickness of 1.5 ... 2.0 mm, we produce the lower engine mount. In the side shelves of the support, drill coaxial holes and cut the M4 thread into them. Install the engine mount with two standard screws.
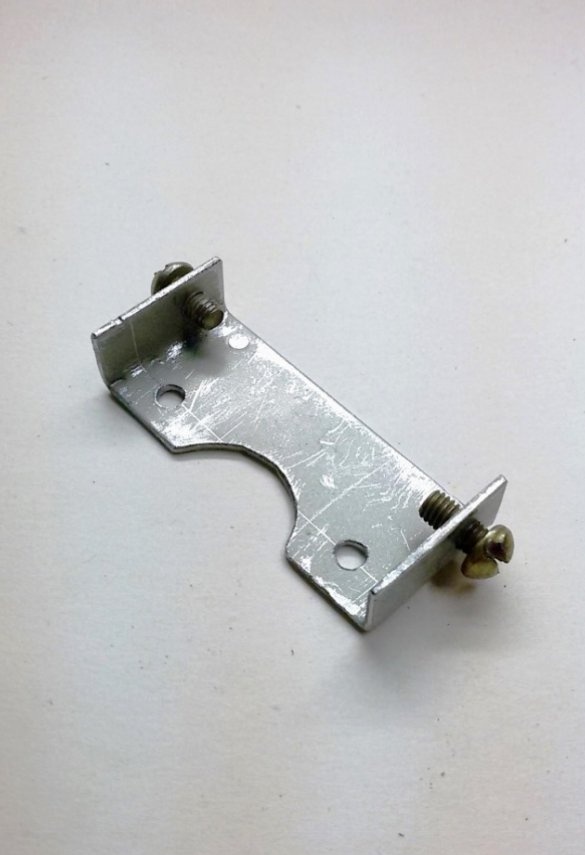
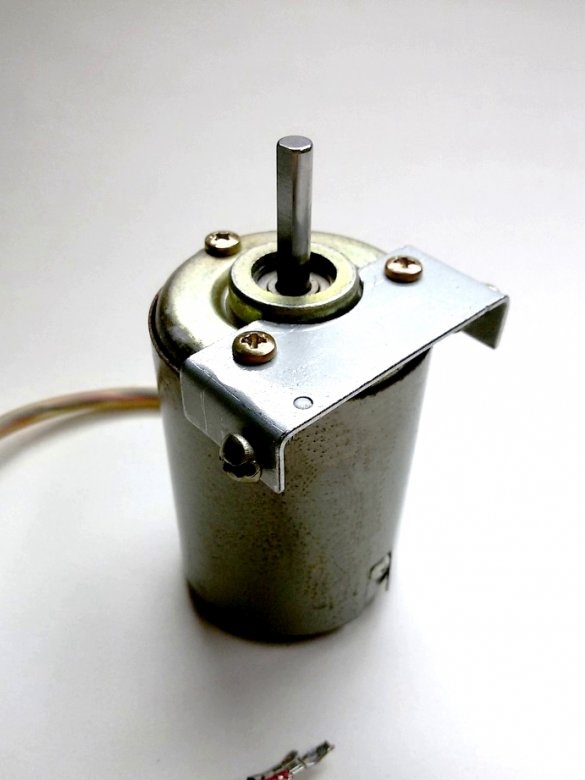
5. The bottom link of the parallelogram.
We will make the lower link of the parallelogram from the rolled aluminum available at hand. For example, in the proposed design, a U-shaped aluminum profile (20 x 20 mm) was used, which was previously used in the manufacture of windows.
To connect the lower link with the motor support, from a steel sheet with a thickness of 1.5 mm, we produce two mirror-made transition elements. They are rigidly connected to the link profile with two screws (rivets).
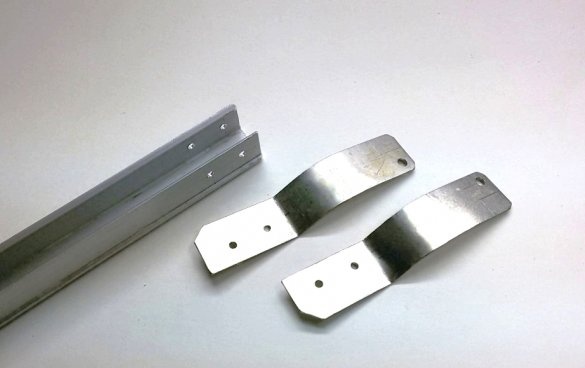
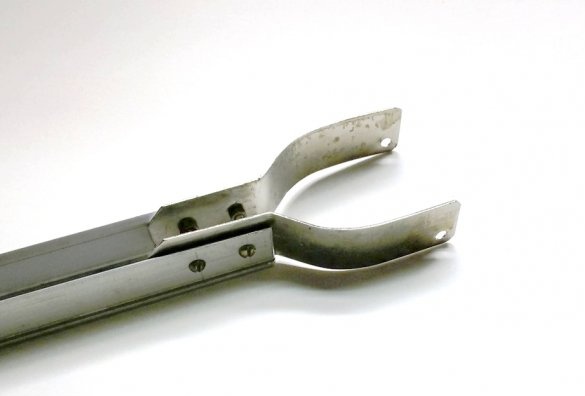
6. Lower link with motor support
The length of the lower link is determined by the size of the manufactured table. In this design, this length (the distance between the axes of the mounting holes) is defined as 150 mm. Mark the holes for connection to the base of the suspension and cut the profile to the desired size. If necessary, on the cut side of the profile, we form the width of the groove for a tight connection in width with the mating base of the suspension. We drill along the marking coaxial holes.
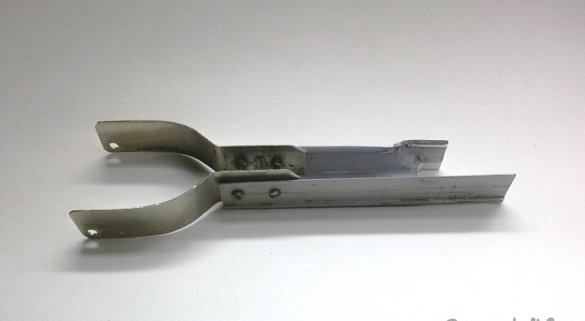
We assemble the lower link with the support of the electric motor. Using the M4 screws, we attach the lower link to the motor support, ensuring free rotation in the connection. The location of the hinge hole in the lower link, behind the engine, is dictated by the maximum possible increase in the length of the link, therefore, increasing the accuracy of processing.
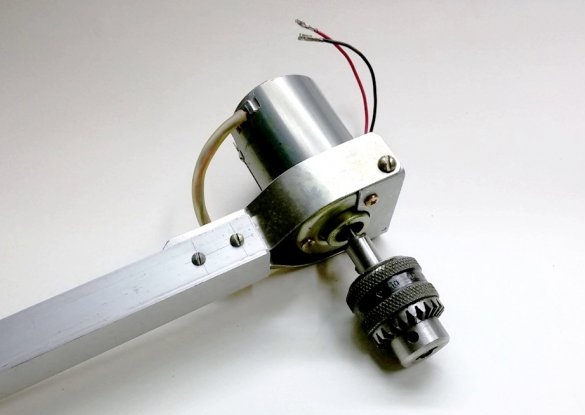
7. Upper engine mount.
From a steel or aluminum sheet with a thickness of 1.5 ... 2.0 mm, we produce the upper engine mount. The design of the part will depend on the location of the attachment points on the existing engine. Install the upper engine mount.
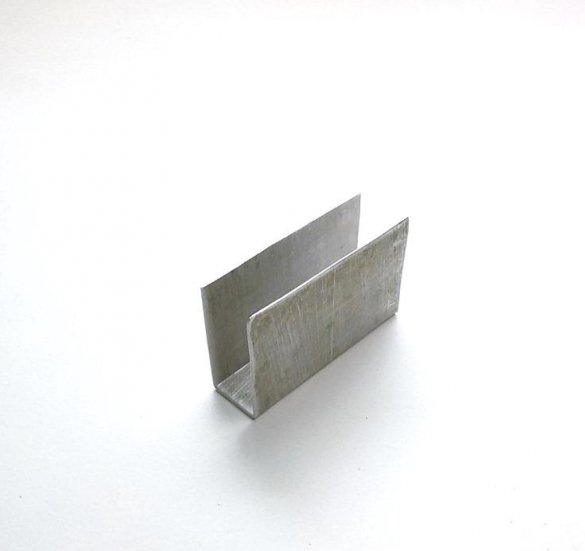
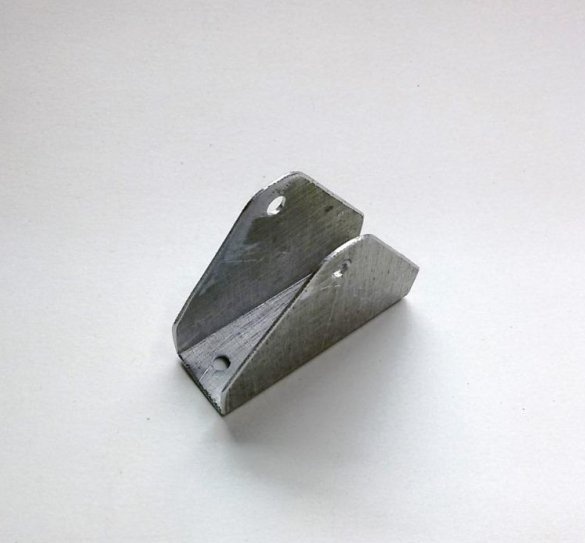
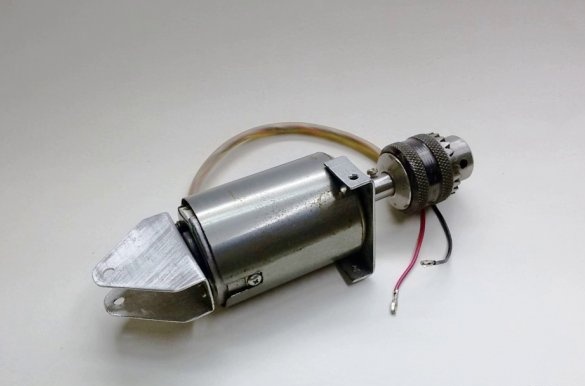
8. The top link of the parallelogram.
The upper link of the parallelogram is also made of rolled aluminum. For example, the proposed design used an H-shaped aluminum profile (12 x 16 mm). Mark the workpiece of the upper link. We transfer the distance between the axes of the mounting holes of the manufactured lower link on the workpiece of the upper link. Drill holes for marking. It is desirable to double the length of the workpiece of the upper link relative to the working size of the link. We will use the free end of the profile as a handle for feeding the drill, which will reduce the force of the hand by half. A piece of plastic tube can be put on this part of the workpiece.
The distance between the axes of the mounting holes and their location on the motor supports, we transfer to the suspension base. In other words, in the manufactured parallelogram, the lines connecting the axes of the mounting holes on the engine mounts and the suspension base must be equal and parallel.
To fulfill this condition, in the manufactured machine design, a part of the profile is cut out on the basis of the suspension (in the upper part).
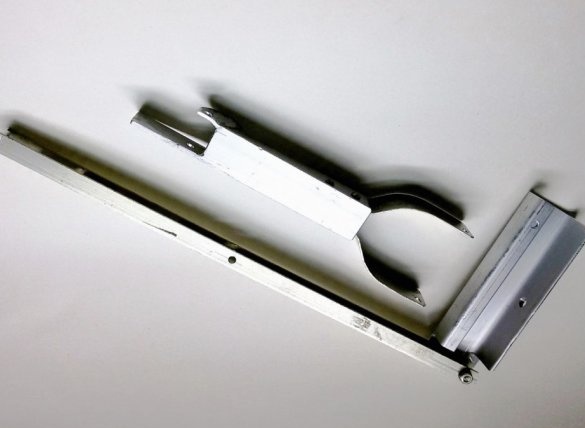
9. Assembly of the articulated parallelogram - rhomboid.
We assemble the rhomboid, install it on a rack and check the mechanism in operation.
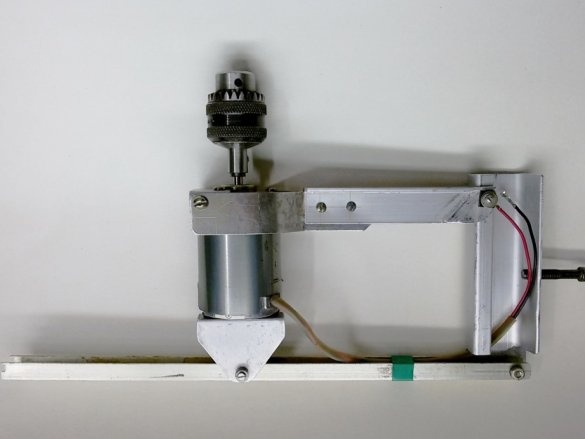
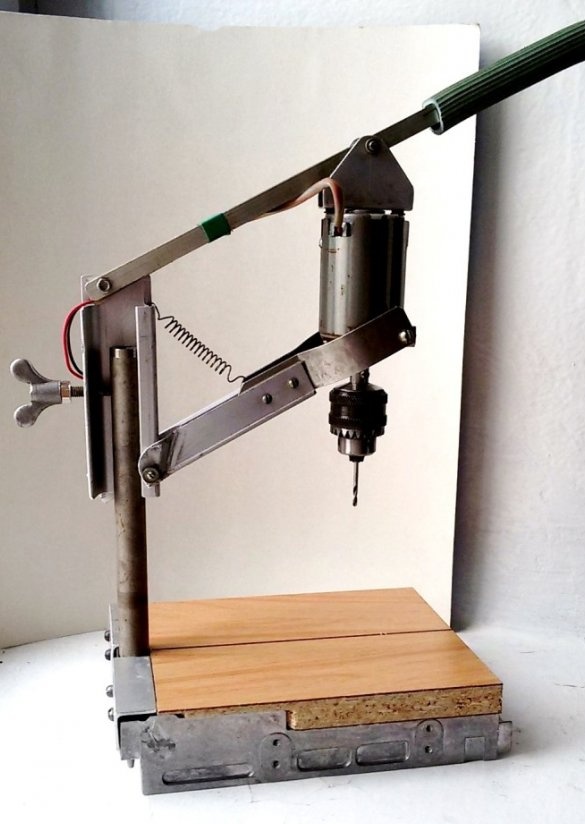
10. Mechanism accuracy control
perpendicular
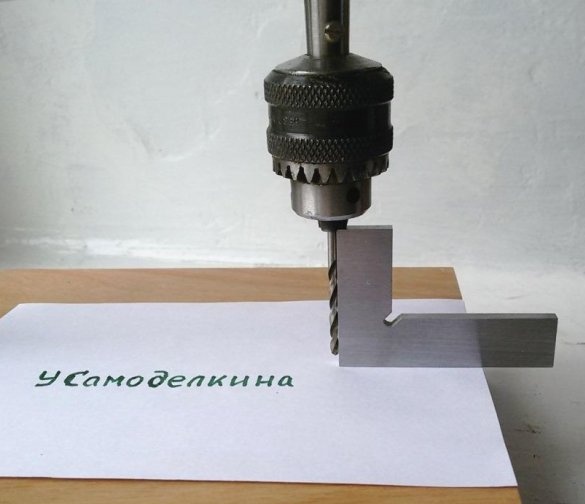
for drills with a stroke of 10 mm
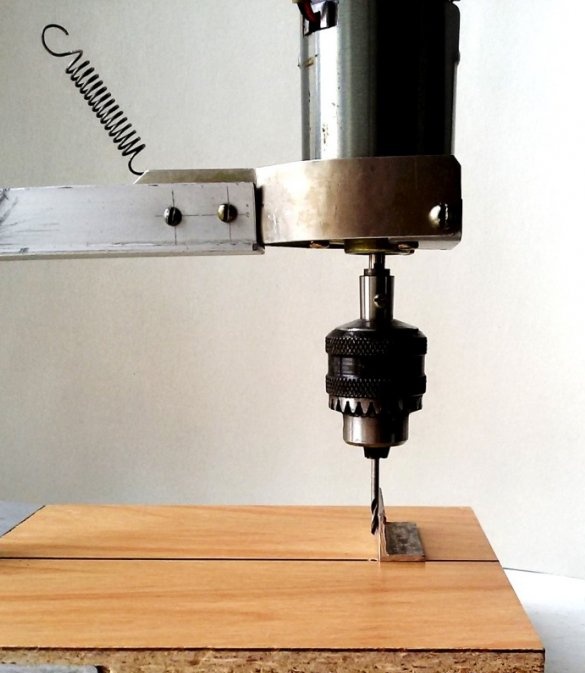
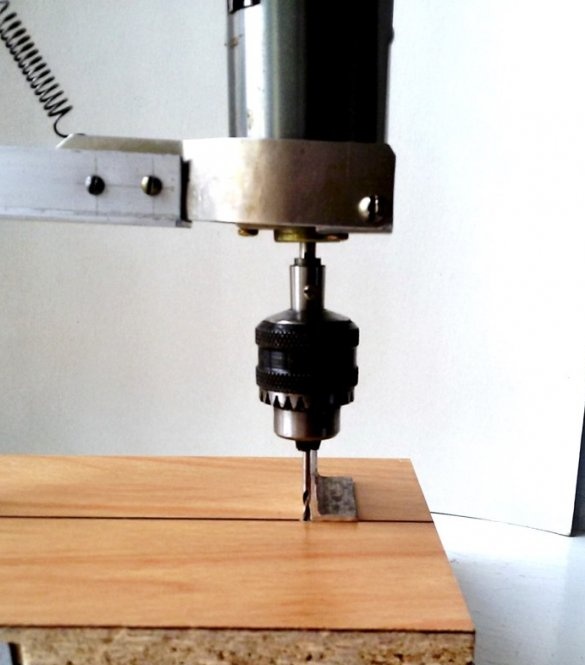
under load.
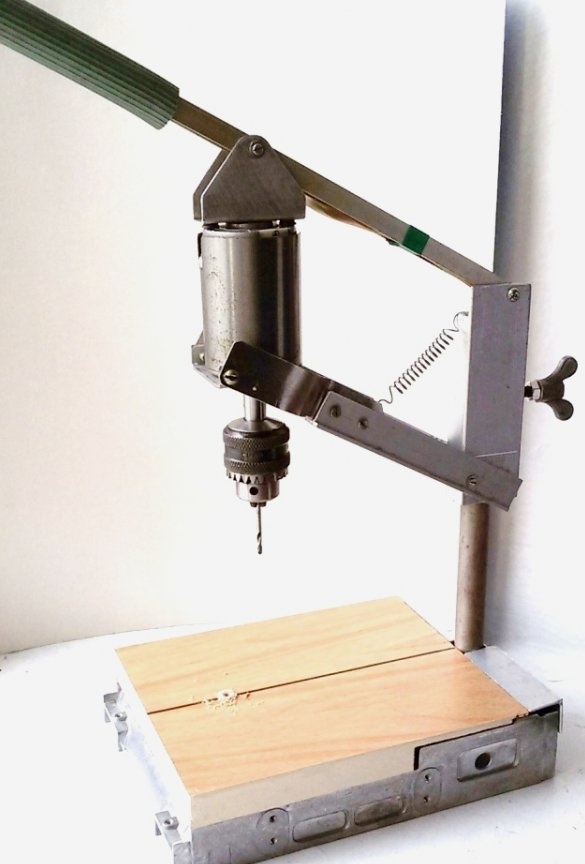