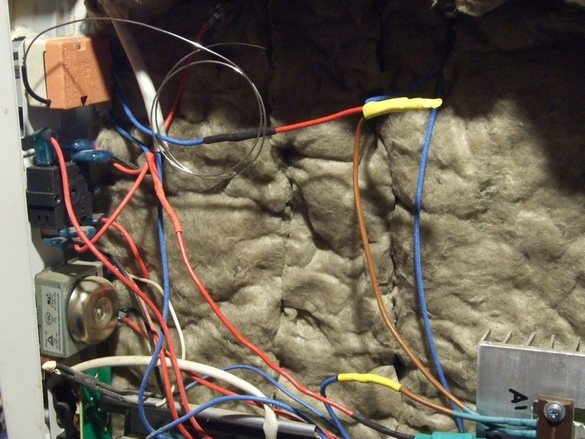
We are surrounded by a wide variety of household appliances, a fair amount of which is associated with electric heating. These are electric water heaters, various air heaters, irons and kettles. In the vast majority of them, temperature control is carried out by a simple mechanical thermostat. Here, the bimetallic plate begins to bend when heated (different KTP - coefficient of thermal expansion, metals) and switches the power contacts. Modern household appliances are designed for modern haste - its heating elements are very powerful so that the device works quickly without delaying kind and honest people. As a result, the thermostat contacts have to switch a lot of currents, and this is an arc, burnout and welding of the contacts. Practice shows that failure of such a (mechanical) thermostat is a very common cause of a malfunction. In fact, a thermostat is an inexpensive component and is almost an expendable item. Its cost is low, replacement is usually simple. Another thing is whether it will be possible to find such an element. It could be removed from production for a long time, it can be rare with expensive and long shipment from afar and so on. Finally, the failure of the right thing can be critical for the livelihood of the household, especially in areas remote from stores.
An easy way to greatly increase the life of a standard thermostat of a heating device is to supply it, to strengthen it with an electronic key. The simplest and cheapest is the key on the triac. Modern electronic components are cheap, have high parameters and small size. In most household appliances, there is quite a place for several additional elements and a small radiator.
Consider this kind of modernization on the example of an electric oven.

The oven has four direct heating elements with a maximum total power of 1.6 kW. Two electric burners on the roof of the appliance - a compact emergency cooking option. The burners are controlled separately by electronic key.On the side of the oven’s working volume there is a narrow metal compartment with controls - a thermostat, timer, work switch, electronic burner thermostat. The standard oven thermostat is the simplest, not even having a remote sensor. In fact, it responds to temperature in the instrument compartment.
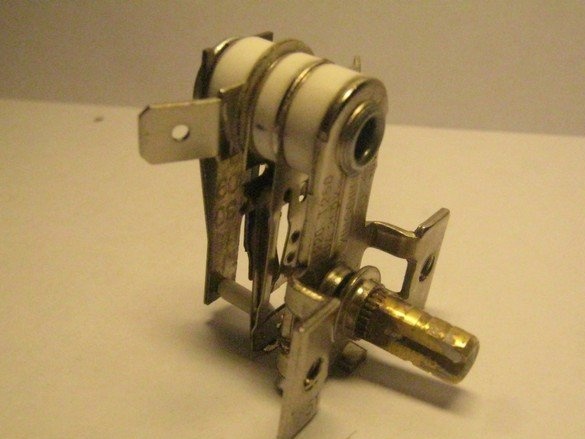
After the standard thermostat failed, it was replaced by an analogue in a ceramic case with an external sensor. This made it possible to increase the accuracy of setting the temperature and reduce its stick out.
What was required for work
A set of small bench tools, electric drill or screwdriver. Tool kit for electrical installation. When working with heat pipes, a construction hairdryer with a narrow nozzle is convenient. Useful IR pyrometer, engraver.
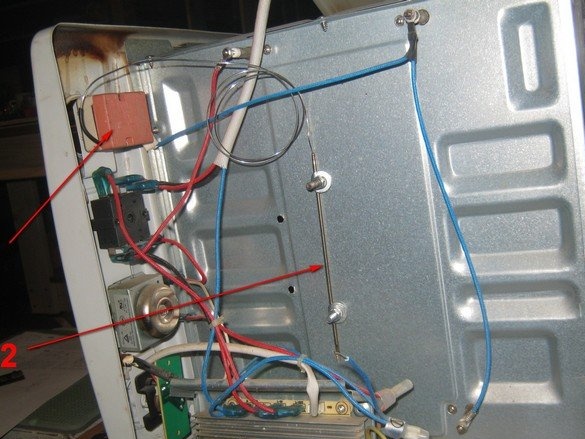
The schematic diagram of the refinement in the electrical part is given below. It can be seen that the triac role now plays the key, the contacts of the thermostat K1 now work only as a sensor. They are significantly unloaded. The current passing through them is reduced to 100 times (if a triac with a low opening current is used). This drastically increases the resistance of the thermostat contacts, its reliability.
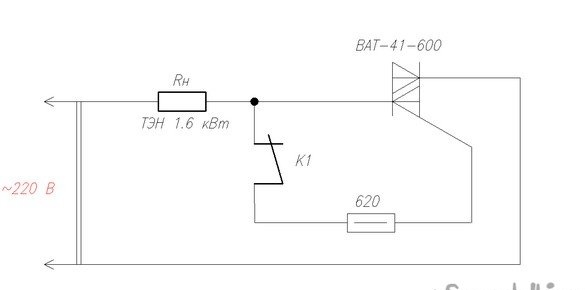
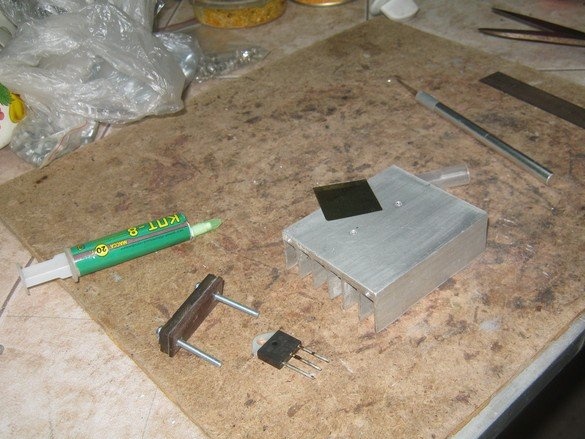
The triac is mounted on a small radiator. In the massive base of the radiator, two blind holes ø2.5 mm were drilled and an M3 thread was cut to fix the assembly in the instrument compartment of the oven. The triac is mounted on the radiator through the mica gasket. Between the mica and the radiator and on the back of the triac there is a thin layer of KTP-8 heat-conducting paste. Surfaces with paste are slightly ground. Mechanically, the triac is pressed against the radiator by a plate of thick PCB with two long M3 screws. On the reverse side are nuts with split lock washers. The conclusions of the triac before installation are tinned.
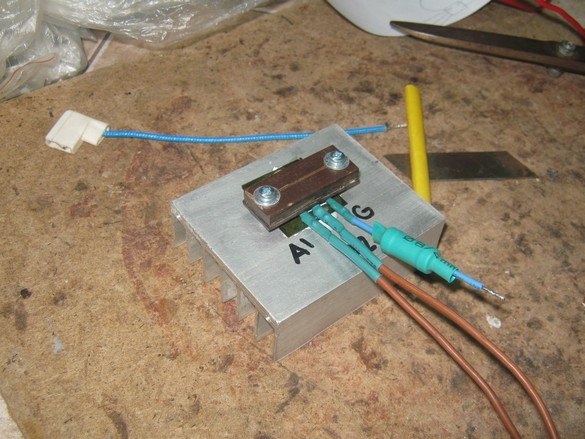
It is more convenient to immediately install a device mounted on a heat sink, and solder wires on the table. With some allowance, I see. 2 W MLT, 1 kOhm soldered to the control electrode. All connections are thermotube insulated. The findings are signed with an alcohol marker.
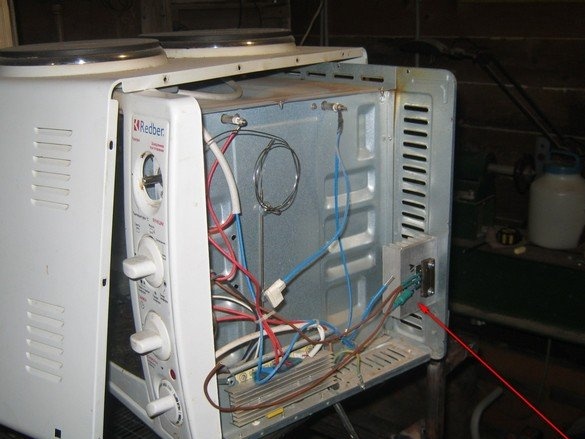
On the back wall of the instrument compartment, I marked and drilled holes for mounting the radiator. Screwed it with two short M3 screws with grovers. Yes, the upper U-shaped casing with the hobs installed is connected to the main part by a wiring harness. We definitely did not want to mark the terminals and their mates or sketch the connections. Good access to the instrument compartment, without shutting down, was obtained by turning the P-casing 90 ° around the vertical axis. Having placed scraps of a thick board under the burners so as not to short-circuit uninsulated current-carrying parts, it was possible to turn on a device for checking operability and running.
A simplified approach is clearly visible in the oven - the working space is not thermally insulated in any way, only an unstable (ventilation window) air gap between the inner tin case of the oven and the outer casing. Achieving the desired temperature - due to the excess power of the heaters blocking heat loss. In the instrument compartment, in the absence of thermal communication with the workspace, a simplified thermostat could not work. Now, it is permissible and even necessary to insulate the inner case. This will save a fair amount of electricity during subsequent operation, will allow the outer casing to heat less, the elements in the instrument compartment will work in light temperature mode - longer, more reliable.
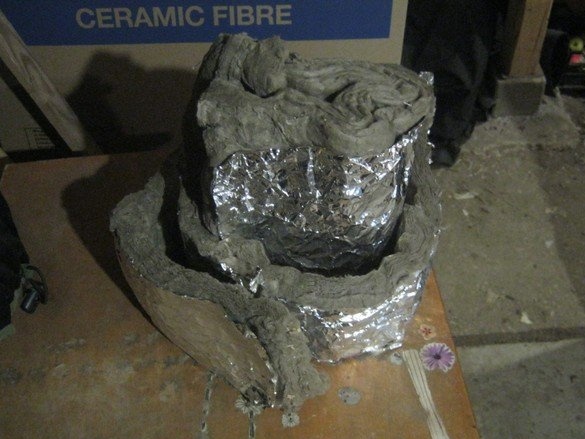
For thermal insulation, scraps of foiled basalt wool were used, although it would be better to take basalt cardboard - it pours less from it, when laying there are less chances to get hurt by glassy particles. Cotton wool was laid in strips, foil to the inner body of the oven. Cutouts for protruding elements were cut with a sharp knife in place. The thickness of the basalt mat and the installation of the oven elements made it possible to reliably fix the insulation with thick rigid wires (heat-resistant insulation).
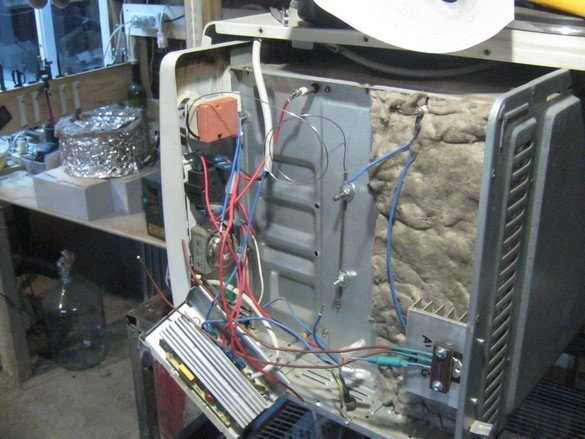
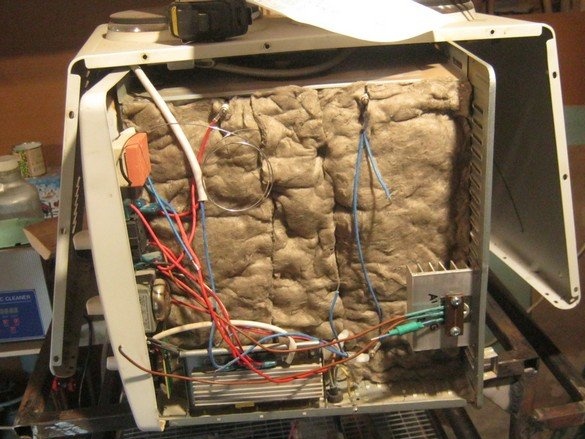
Thermal insulation of the most complex wall - the instrument compartment is made of three strips. The sizes of the strips were cut out with some margin and inserted at odds.
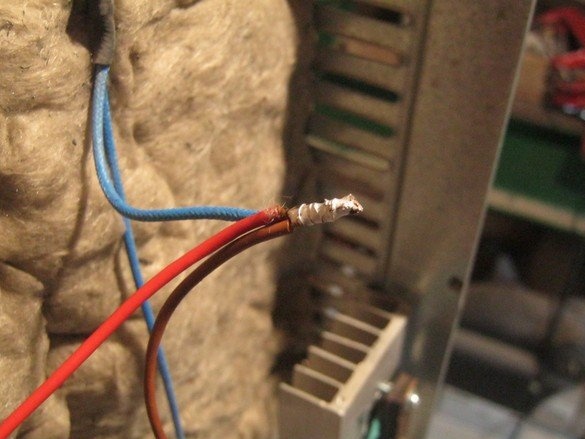
New connections were carried out by soldering. The most difficult moment is three powerful wires connected at one point.Each wire is stripped from insulation over a length of ~ 20 mm, the cores are twisted in the direction of the coil, the stripped end of the wire is tinned. Three prepared ends are wound, fastened with a thin tinned wire and carefully soldered. The place of soldering, when using non-wash fluxes, is isolated by a thermotube.
After checking the installation, you can make a test run.
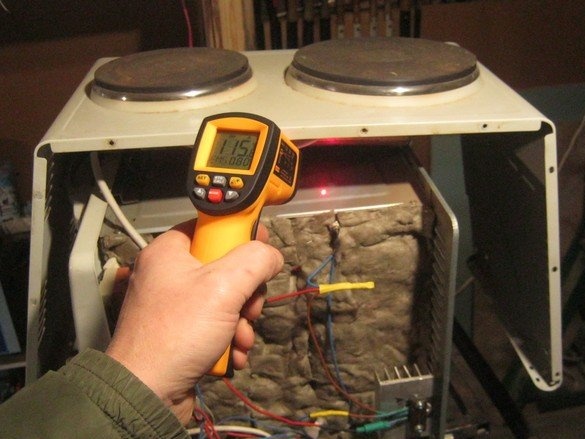
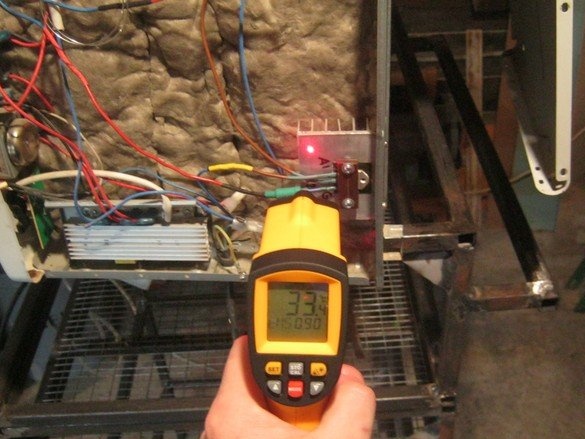
At a temperature outside the wall above 100 ° C and the operation of all the heating elements, the temperature of the triac radiator is low - a little warm and nothing more. It is clear that in a closed compartment and during prolonged use it will heat up more, but there is a margin.
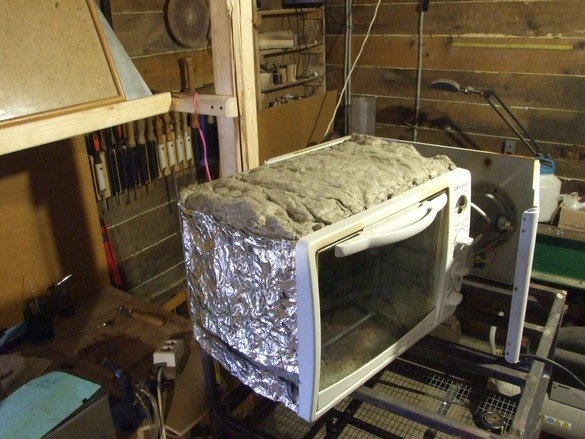
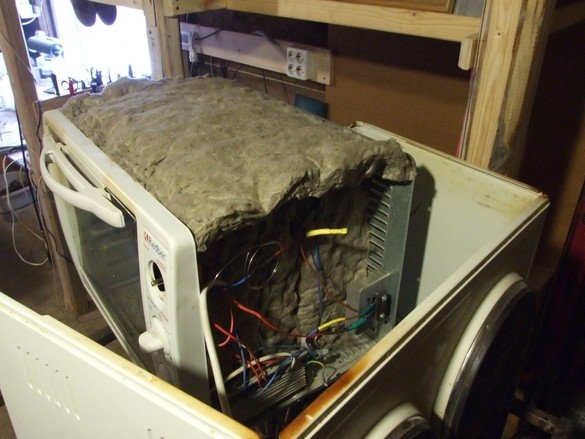
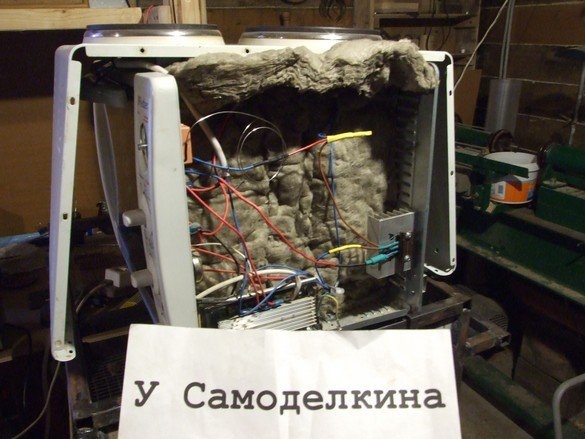
All relatively empty compartments were filled with basalt wool. Unfortunately, the bottom and back wall of the working volume do not have double walls, for their insulation, more significant improvements would have to be made.
The outer casing is installed in place, the oven is assembled, its performance is checked.
The thermostat is standard and re-installed, have a different graduation. In the new kit, there was also a graduated pen, the markup with which was transferred to the previous twist. For reasons of appearance.
The old numbers are painted and wiped off pretty much. Removed their remains with a fine sandpaper. He made point marks on a plastic handle in the form of indentations with a small boron ball, the numbers were engraved with a makeshift engraving cutter from a fragment of a 3 mm drill. Depths filled with black asphalt varnish. After drying the varnish, I cleaned off the excess on top with a fine sandpaper. The result was a contrasting abrasion resistant pattern.
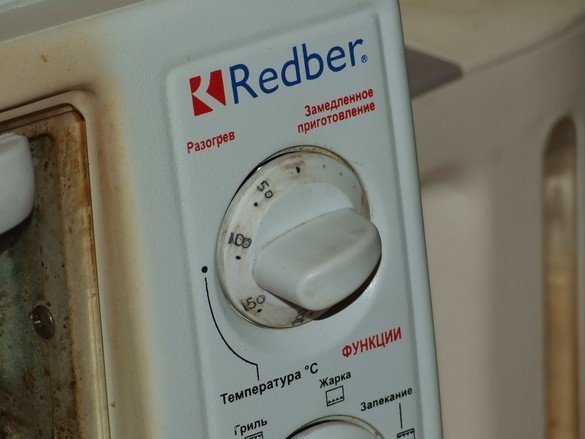
Conclusions, ways of development
Actually, it remains to say that a number of thermostats, humidity meters and other temperature controllers with load switching by an electromechanical relay can be subjected to similar amplification.
Babay Mazay, November, 2019