From the article below you will learn how to do it yourself make a toy xylophone. The following description and instructions are taken from the Matthias Wandel YouTube channel.
The master’s two-year-old child likes to beat the drums, so he was thinking about buying him a drum for Christmas. But then he had the idea to do something with a more pleasant sound, so that the sound was not so loud, something like a wooden xylophone.
Necessary materials and tools:
- trim parquet board;
- wooden beam;
- band-saw;
- a pencil;
- small;
- table circular saw;
- clamps;
- roulette;
- PVA carpentry glue;
- stationary belt grinding machine;
- drilling machine;
- Forstner drill;
- self-tapping screws;
- screwdriver;
- glue gun;
- felt;
- punch for felt;
The remaining trim of the floorboard had a good sound on impact, so this is not a bad option for a musical instrument. The master experimented with various ways of fixing them. Rubber bands proved to be the best, and the presence of a cavity under the board significantly improved the sound.
The master even got the opportunity to use the piano tuning application to read readings from the boards, so he became interested in the manufacture and tuning of plates.
But different wooden plates produce different sounds, regardless of size, possibly due to the density of the wood. They are also very sensitive to how deep the neckline is from the back. The cutout significantly reduces the resonant pitch.
After much deliberation and attempts to tune them, the master decided that it was enough to just make a few tablets that would sound good together. Laying them on the bed, they sounded so that they could hear their joint sound.
After selecting the plates, the master needed a box for their installation. The master found out the specific places of the vibration nodes, where hitting them give the least amount of tone and marked these places.
He decided to stick sticks on these marks to find out the geometry. From this data, the master calculated the necessary angle for the joints of the box.
He then made a wooden wedge with the same angle to fit it into the spike cutting template. First, the master cuts the spikes at the ends of the long bars.
He used 6 mm.box connections, but on the workpiece there was an odd number of spikes, so that one wider spike appeared in the upper left and lower right parts of the bar. Asymmetrically. To avoid this, you would have to put the workpiece in the template on the contrary, or center the spikes, or make a box with an odd amount of 6 mm in width.
But it was already too late, so the master decided that he would just make the mating parts asymmetric in the same way.
And matching the asymmetry was a fairly simple solution, all that had to be done was to put the part in the same way for each edge, just as it was done with the other parts.
The clamp of the last short part was quite complicated, so the master used a fastening bolt attached to the back of the box with a wing nut so that it could be clamped in place. The last time he used such a screw when making boxes, so that he already had a hole in the right place in the jig for boxes.
Check for compliance. The spikes enter each other quite tightly.
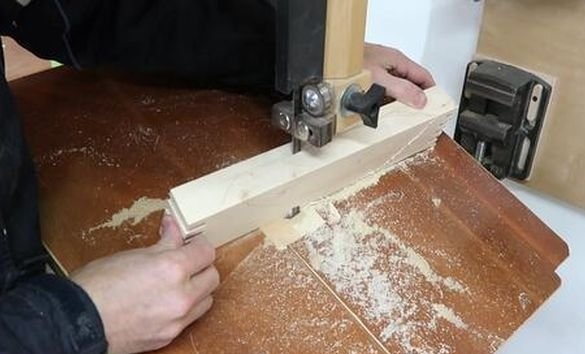
The master decided that he made the box too heavy, so I had to cut off part of the inner bottom of the wider side parts on the band saw.
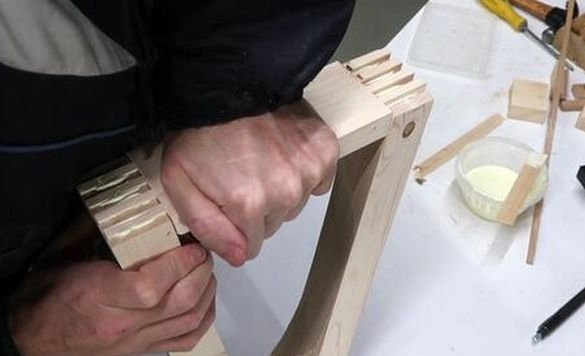
After that, the master glued the parts together.
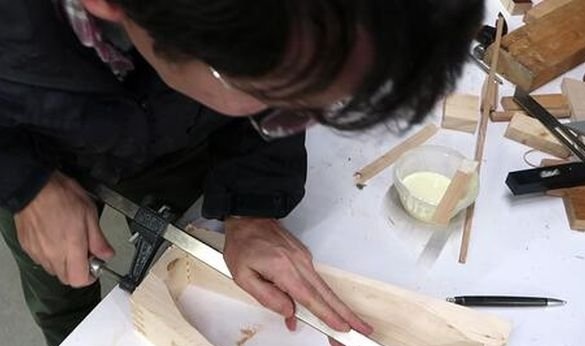
The parts entered each other very tightly, so the master resorted to clamps to leave the parts clamped until the glue dries.
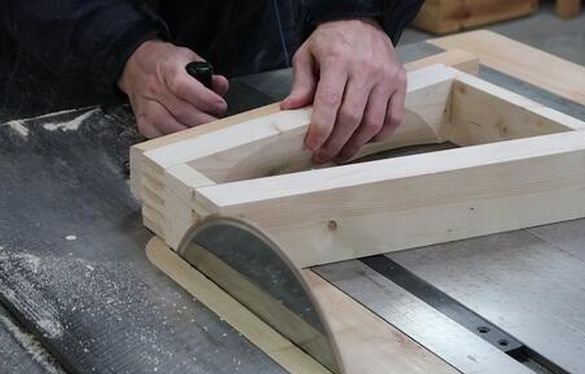
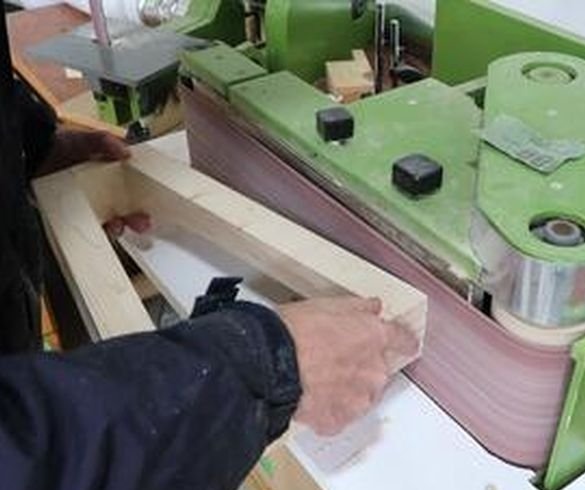
Then the master cuts the box to get the perfect connection. Then he rounded the corners of the box on a belt sander.
When the plates were placed directly on the box, they began to make an already recognizable sound, similar to a xylophone. The master began experimenting with various soft materials that vibrated best, including rubber bands, thin felt and thick wool felt from a woolen pillow.
Thick wool felt sounded best.
Before drilling mounting holes through the plates, the master first noted a dead spot. He adjusted the places where the vibration nodes are located so that the plates lying on the base rest on a dense wool felt.
Then, large holes are drilled and countersinked so that the screws can be flush with the surface and at the same time have a large backlash.
On a real instrument, the plates are mounted using strings that run along the sides, but for a children's toy this would not be strong enough.
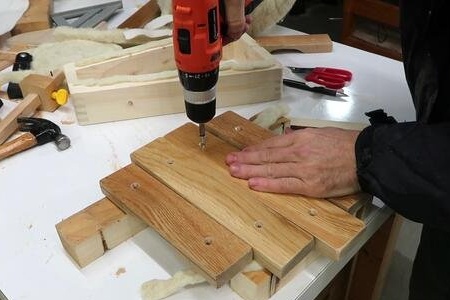
The master hoped that the screws in the vibration nodes, he would be able to freely twist. And even touching the plates with self-tapping screws still get a decent sound. But the self-tapping screw on the plates muffled the sound.
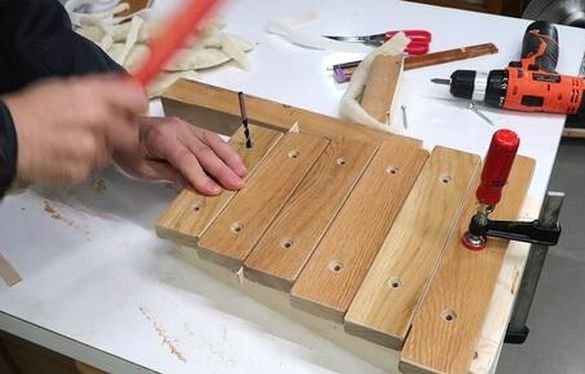
But no matter how the master was going to solve this problem, he knew for sure that in any case the plates would be mounted using self-tapping screws.
He made struts about 1 mm thick to fit them between the plates. He placed them on the box, and clamped the widest in place. He then marked the locations of the mounting holes with a drill and a stick.
Then you need to drill holes for self-tapping screws in the frame. These holes are not so important, but it’s better not to risk it, otherwise you can split the tree. It will also help to tighten the screws more accurately.
Bonding small felt pads made of wool near the holes with hot glue.
Then the master secured the plates with screws and felt washers. He enlarged the shank hole so that only the felt washer under the head of the screw touches the tree.
But there was a feeling that they were a bit stuck, and the master thought that the children would probably eventually start pulling the felt.
To solve this problem, the master drilled holes for drowning the self-tapping head and felt washer a few millimeters below the surface.
The master used several punch punches (which were designed to work with leather) to make felt washers. First, a small blow is applied to the central hole, and then a large blow to cut the perimeter of the washer.
Then we screw the screws with felt washers.
Thanks to this decision, the sound was pretty good. Self-tapping screws and felt washers did not dampen vibration.
Then the master made a hammer for the xylophone. Ideally, there should have been rubber around him, but it’s useless for children to do this. Therefore, the master used very light and relatively soft wood to make a hammer head.
After the master glued the head to the stick, he turned it on a belt sander to give it a ball shape.
The entire impact resistant surface of the hammer head is the side of the wood fiber, so it is less hard.
This instrument sounds very lively. This sound is more like a hard buzz. It turned out not so soft and clean, compared to the sound of a rubber tape at the end of a stick.
If you like homemade author, then try to repeat and make. Thank you for attention. See you soon!