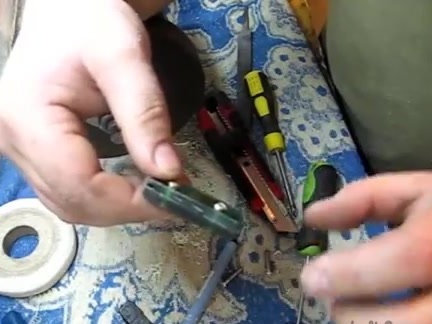
This craft necessary for those people who often work with dangerous blades. Because there is a big risk of getting a cut from the back of the blade when working. And as you know, such cuts heal very, very long and painful. To make it convenient to hold the blade in your hands and avoid unwanted wounds, you need to make a small frame for it.
Step-by-step instructions on how to do this can be seen in this video:
[media = http: //www.youtube.com/watch? v = iG3qPI-8t0w]
For work, we need to prepare the following:
- a piece of plexiglass;
- blade;
- ruler;
- scraper for plexiglass;
- pliers;
- marker;
- vernier caliper;
- drill;
- screwdriver;
- cogs;
- grinding machine;
- file;
- a screwdriver.
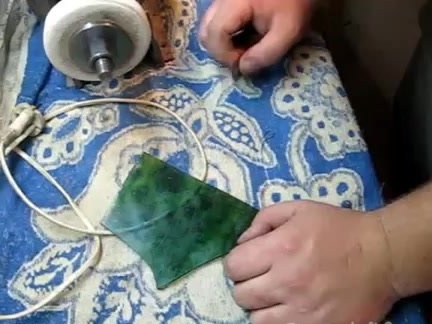
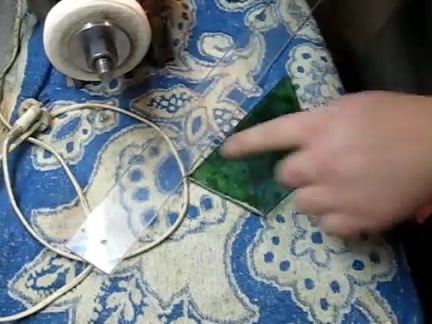
The frame for the blade is best made of brass. But in this case, it will be made of plexiglass.
For work, you can take any piece of plexiglass that you can only find among old things. If it is uneven, then we align it with a ruler and a square, scraping a shallow line, then to evenly break off the excess material with pliers. We need to make at least one flat angle.
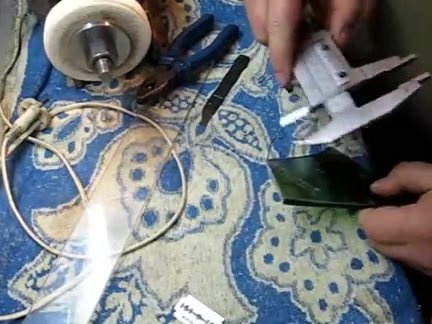
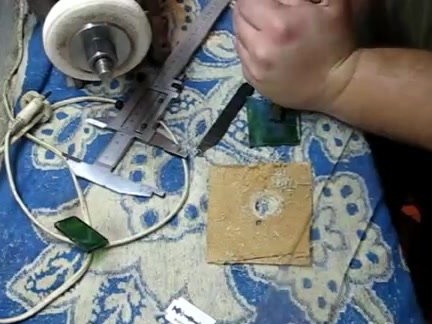
Next, we take our blade and try it on to this corner, position it the way we will frame it, i.e. leaving the blade on one side completely open. Do not forget about allowances when you outline the contours of the blade with a marker.
With a vernier caliper, we check the uniformity of the marked lines, try to maintain one size relative to the edge of the plexiglass. Measure the size horizontally and vertically.
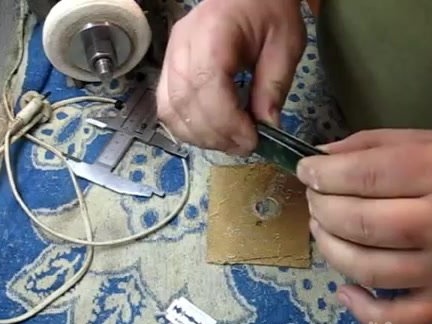
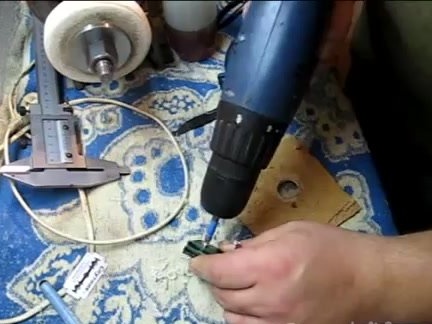
Next, we cut out two such marked rectangles by scraping and carefully breaking off, helping ourselves with pliers.
We got 2 pieces of blanks.
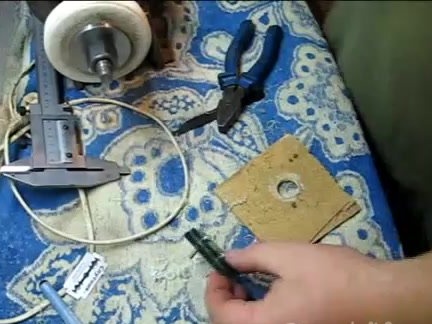
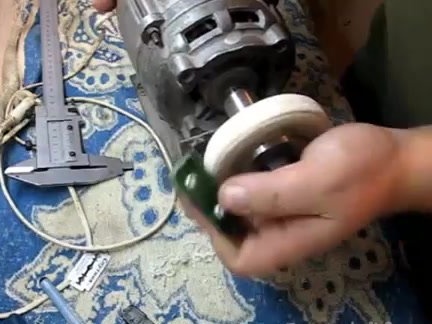
Drill 2 holes along the edges of the plates and cut into each thread.
We select the screws that are suitable for the holes made and fasten the two plates together, which will hold the blade.
Using a grinding machine, we process bonded plates, removing excess plastic and giving them a more aesthetic shape.
After the plates are turned, we unscrew the screws and clean the edges of the plates with a file and a knife.If the cogs are too long, they can be cut.
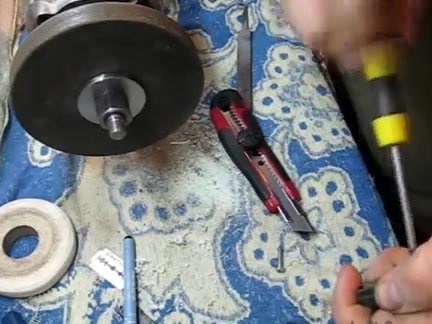
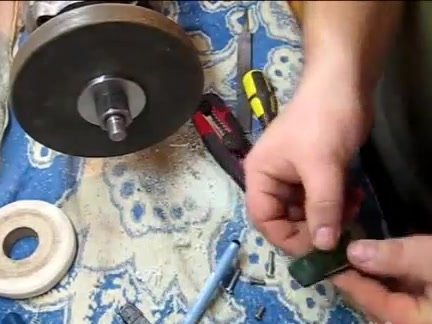
We insert the blade between the plates, return the screws to the place and twist them well.
Our rim is ready for the blade, now you can perform all the necessary work with the blade without fear of injury.