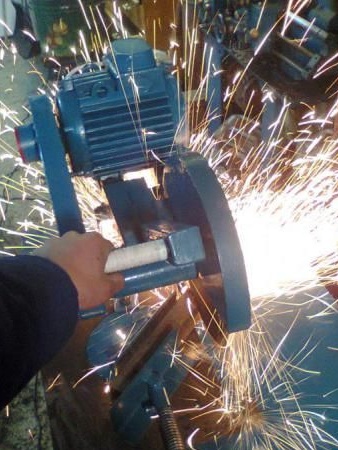
Almost every workshop has such a necessary and difficult to replace tool as a grinder. It is quite versatile and is used for cutting metal, wood, cleaning and polishing various surfaces. But sometimes you have to work for several hours, which affects the tiredness of the hands. In this case, especially during everyday work, such a thing as a cutting machine can be very useful. It requires much less physical effort, and also provides a much higher precision cutting. In this article, the author presents a photo report on the creation of such a machine.
The materials and tools needed to assemble the machine will be listed in the article.
The author began with the manufacture of the spindle. It was whetted under 306 bearings, and has a diameter of 30 mm.
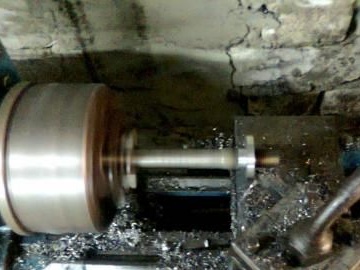
On one side there is a seat under the pulley, on the other hand a thread is cut (as on a standard grinder). Under the fastening of the cutting wheel.
Outside the bearing seats are made of a suitable pipe diameter.
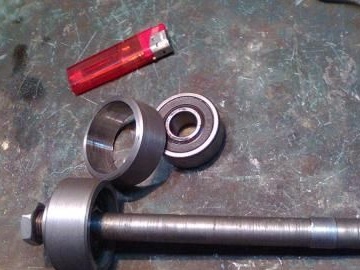
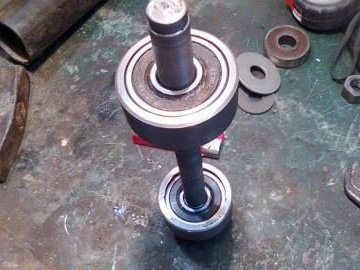
Seats are planned for bearings, between them a pipe of the same diameter is welded.
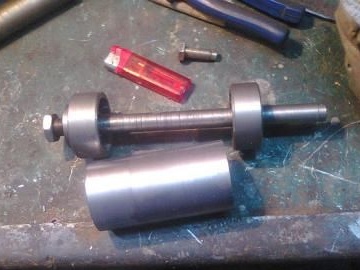
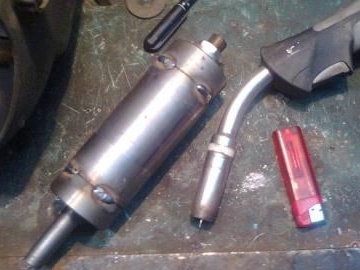
A pulley is worn on one side:

The centering nut is the same as on a regular grinder.
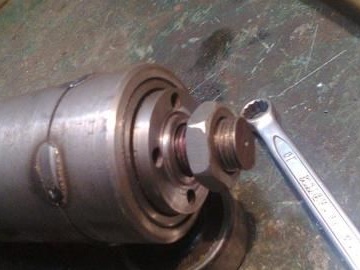
A 3 kW engine with a rotation speed of 1,500 rpm was used for the machine. A stand was made for him, with longitudinal holes, to adjust the belt tension. Between the stand and the pulley were welded 2 profiles of 40 mm.
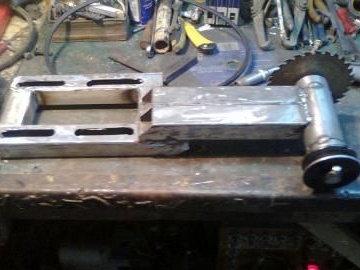
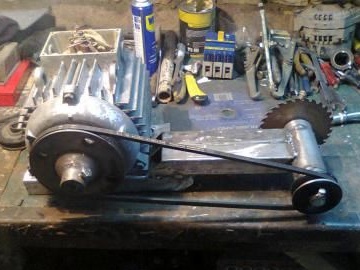
Further, from a sheet metal 2 mm thick, a protective casing was cut out and boiled out:
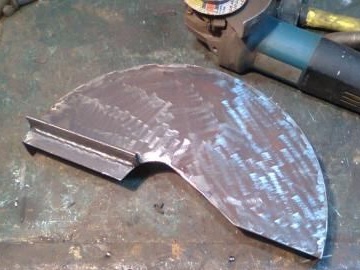
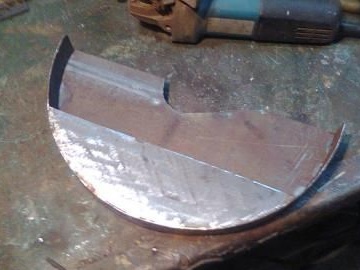
Through the corner, the casing is welded to the fortieth profile. Before doing this, it is advisable to put on a spindle a cutting wheel (300 mm) so as not to lose with its position. The distance from the circle to the inside of the casing should not be less than 5 - 6 mm.
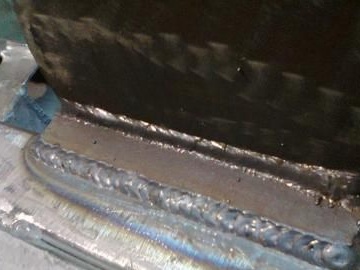
Next, a hinge was made to secure the entire structure. Two pipes inserted one into the other with a slight backlash were used as a hinge.
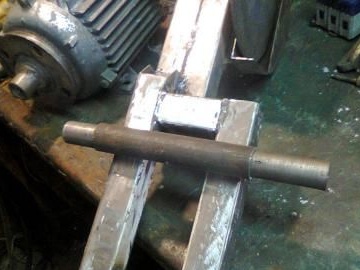
A worktop was made under the machine. The thickness of the sheet of the working surface is 5 mm. The legs and partitions are made of 50 corners.
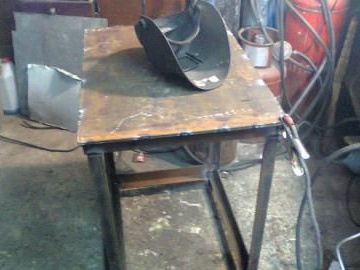
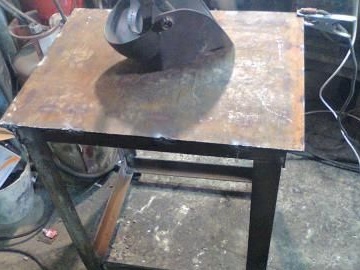
A hinge is welded to the countertop:
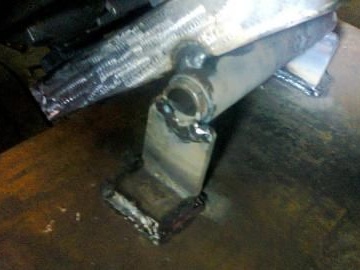
The same profile of 40 mm was used as the material for the manufacture of the handle, and a metal rod suitable in size.
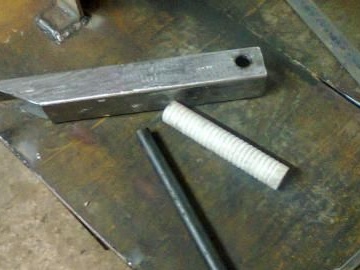
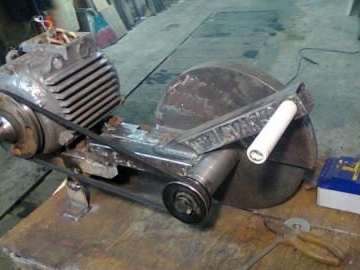
For rigid fixation of the workpiece during cutting, yews are needed. To make two metal corners and a threaded rod for a nut from 150 water valves and a nut itself will be needed.
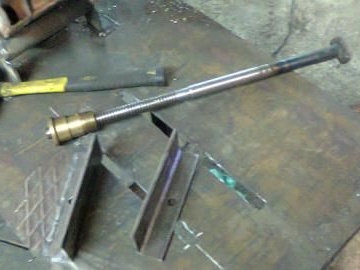
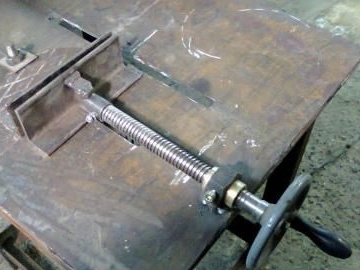
A protective casing for the belt is made of sheet metal:
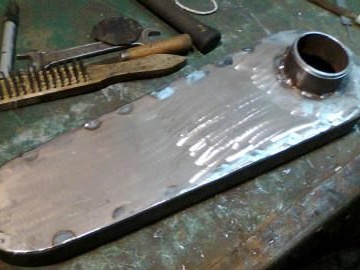
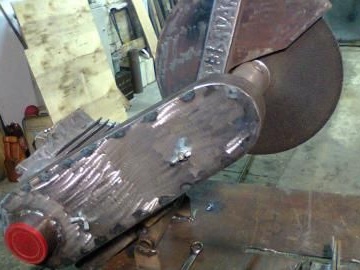
Next, the electrical part of the machine is mounted, consisting of an automatic machine and a trailer for turning off the engine.
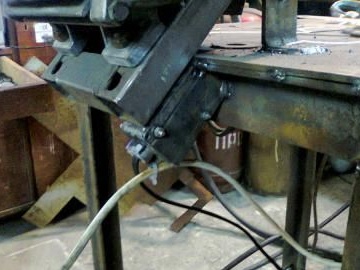
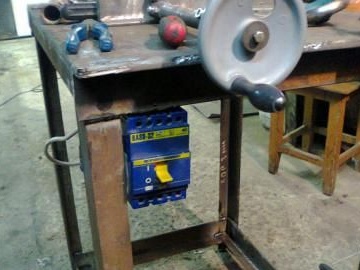
Welded plate to protect against sparks.
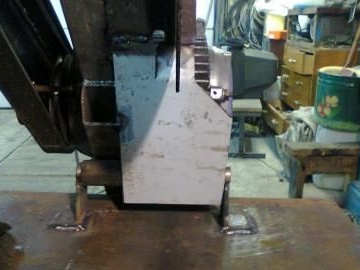
The table is being finalized, wooden shelves are added to it.
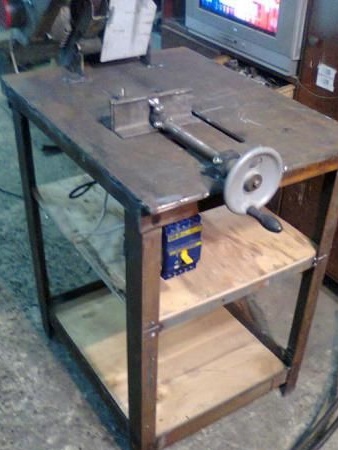
And here is what the finished machine looks like after painting:
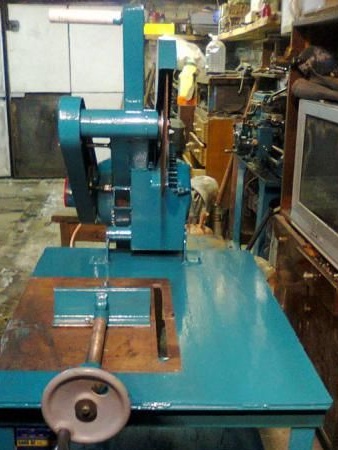
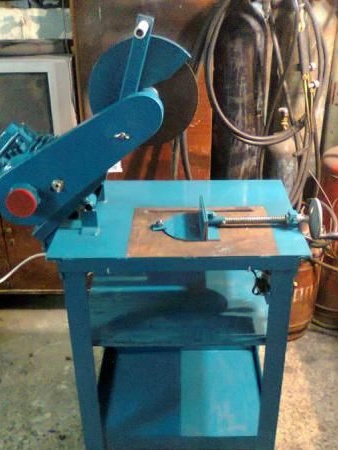
And here is the result of his work:
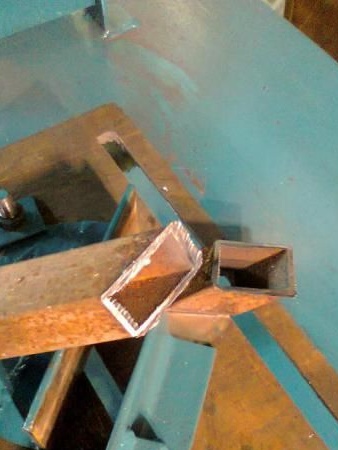