The muffle furnace is designed for melting aluminum, copper. It is also possible to burn ceramic products and harden steel. The design of the furnace presented in this article is adapted to work with aluminum.
Aluminum melts at temperatures above 660 degrees, and for the furnace to work properly, its heating elements must produce a much higher temperature, since even with good thermal insulation, part of the heat will be dissipated into the environment.
There are different ways of heating stoves: it is ignition by gas, coal, firewood. Electric heaters are also used. Heating the furnace by burning (gas, wood, coal) is much more economical than electric, but it also has its drawbacks, the main of which is the difficulty in adjusting the melting temperature, which limits the possibilities of using the furnace itself, such as polymer casting and artificial aging of metals . That is why the author of the article chose an electric heating method for his furnace.
The design of the muffle furnace.
In the center of the furnace there is a heating chamber, into which metal is filled and melted. It is surrounded by the so-called "heat accumulator" having a protective heat shield from the outside, which increases its cooling time.
A heat accumulator is needed to maintain the desired chamber temperature in those cases when metal should be filled several times in a row. It is important here not to overdo it, and not to make it too large, since it takes a certain time to heat it up the first time you turn on the furnace, and the larger its size, the longer the furnace will reach the desired mode.
Refractory brick was used as a material for the manufacture of the battery. From it laid out, something like a small well. In order for the edges of the bricks to fit snugly against each other, they are trimmed at the right angle. This can be done with a diamond wheel grinder. It is cut quite easily.
Housing
To create a furnace body, a metal sheet 1 - 1.5 mm thick is needed. A reserve is made in height, since there will be another layer of bricks at the bottom of the furnace.
Then a ring is bent from the reinforcement bar and its joint is welded. Its diameter is made with a margin for a thermal insulation layer. As it is welded, a sheet of metal is bent around it. The joint is scalded.
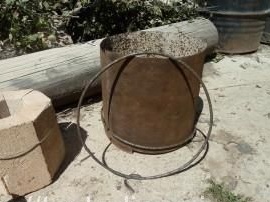
Next, the bottom of the furnace is made. From a sheet of metal (the same thickness as the case), a square is cut to the diameter of the case.
Then four bulging corners are cut off by a grinder.
The next step will be cutting grooves under the electric heater. Before this, the bricks in the assembled form are numbered, then stacked in one line and aligned with the level.
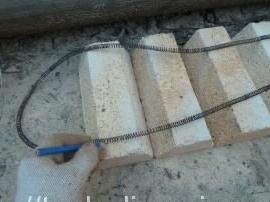
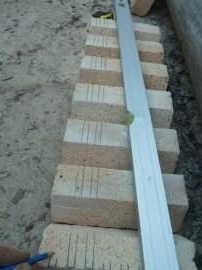
Spiral
Nichrome was used as a material for winding a spiral. The wire thickness is 1.2 mm. Its heating to 1000 degrees will occur with the passage of a current of 20 amperes. The furnace is connected to a 220 volt network, therefore, its power will be about 4.4 kilowatts. The length of the wire was 1230 mm.
For winding a spiral, you can use a metal rod 3 - 4 mm. The wire is wrapped around it, then removed. The spiral is ready.
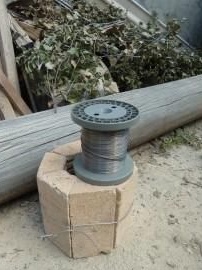
The wire through which voltage will be supplied to the furnace must have a cross section of at least 2.5 mm. This applies to the TOTAL wire going to and from the shield.
It also does not hurt to put a separate 25 ampere machine under the oven.
When laying the spiral, it is important to ensure that its coils do not touch each other, this can lead to a decrease in resistance and overheating of the spiral.
Thermal insulation
At the bottom of the previously prepared body lies sheet asbestos. A layer of refractory pouring (fireclay clay) pours over it. Next lies a layer of refractory bricks on which the camera will stand.
Bricks are laid out in their place in the order of numbering and are aligned in the middle. Joints between bricks are smeared with fireclay clay. A layer of asbestos is laid on the inner metal body.
In the case, holes are drilled for ceramic insulators to the heater wires.
Further, the space between the metal is poured with fireclay clay mixed with water. To speed up the solidification, you can slightly warm the oven, but it is recommended to do it in the fresh air, since asbestos vapor is hazardous to health. After solidification, the oven is ready for use.