Homemade tracked all-terrain vehicle PARMA - This is a product of Michael from Perm. He began construction since January 2012 and now all-terrain vehicle Parma cuts through the swamps and impassable roads of our country.
All data is taken from the forum site , where he shares his best practices and skills under the nickname mishanya68.
Tasks originally assigned to the all-terrain vehicle.
In the technical requirements and wishes, the following items:
1. confident movement on snow of medium depth and density for the Urals.
2. capacity 2 people, plus 50-80 kg of cargo.
3. minimum, must confidently stay on the water (the main use of fishing and buoyancy for safety).
4. The main application of snow and ice is 90%, the rest is autumn and spring-snow with mud.
5. the maximum use of finished serial parts and assemblies.
In connection with this project, he re-read the topics on the "Basin", "Luntik", "Barsik" and "Yukon" - these are ready-made all-terrain vehicles described on the site . Many thanks to the authors of the projects for sharing their experience, best practices and drawings that they used.
Based on the experience of previous builders outlined an approximate design
1. turn on the differential with the rear axle, but put the cylindrical.
2. The engine is 2-cylinder, Chinese-made with a cylinder capacity of 690 cubic mm.
3. transmission: belt variator - gearbox from VAZ 5-speed - rear axle from VAZ.
4. Dimensions 2500x1750 mm.
The rear axle is taken from the "Lada" classic. Instead of wheels, sprockets are dressed (drive wheels for the track)
The beam was used. After disassembling, after checking for straightforwardness, I cut off the excess and immediately cleaned it, cleaned it with petal circles with grain 40. It turned out quickly enough, 1.5-2 hours for everything, and cleaning took about 30 minutes. But this time is later saved on welding and painting.
The engine is made in China.
Drawings have been developed for the production of guides, which are fixed to the inner side of the track tape and prevent the caterpillars from moving off during movement and turns.
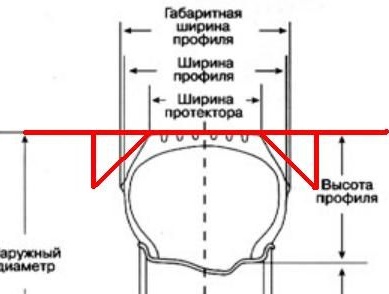
The axle shaft is factory.
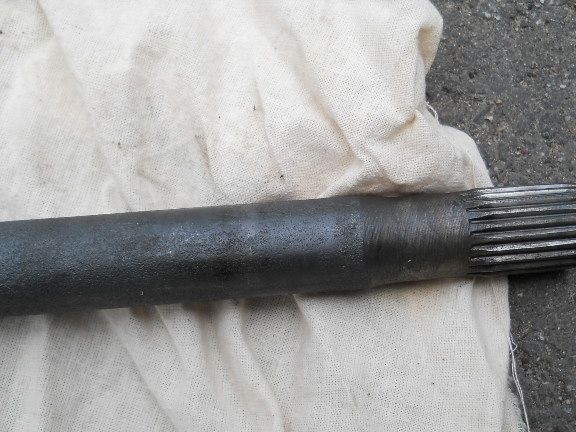
Axle bought, find the differences! Therefore, it was decided to leave the factory axles, but with the replacement of bearings.
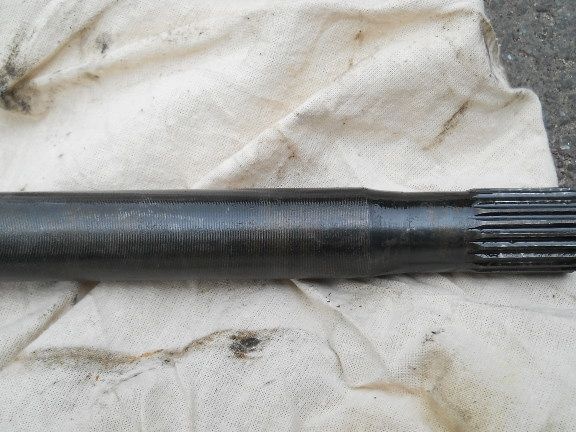
I bought belts for the production of tracks in a rubber goods store at a factory in Perm.
It is possible in more detail: what is "increased strength" ??? In numbers.4 gaskets is good, is 12 mm not a lot?
The strength of the tape is created by the gaskets - the rest is rubber, which in itself does not carry a load, BUT protects the gaskets from damage. For example, I took one so that it was 3-4 mm on one side (outer) and 1 mm on the other (inner) side. On the inside, almost no damage is expected, and excess thickness - excess weight and not small! As for the gaskets - they are ALWAYS of the same thickness - 1mm., The rest of their quantity!
According to the footage: I took 4 pcs. with a length of 6.5 m, width-150mm, thickness-8mm, ply-7. It turned out 10 thousand rubles.
He began to cook the frame of the future all-terrain vehicle. Someone calls the frame, someone the boat, someone the skeleton, and the author calls this design a keel, since the all-terrain vehicle is more suitable for swimming.
Rounded in front of keel should improve floating quality car making.
It was decided to make an all-terrain vehicle without a balancer, as it is intended for travel in the winter, the roads are smoother, the weight of the structure is reduced, and it is technically easier to implement.
The frame assembly with track rollers on both sides, the wheels are used the most ordinary and common with R 13 from VAZ, the bottom of the star is raised from the floor by 350 mm, the wheel with a diameter of 570 mm.
Preparation of tracks for the manufacture of tracks.
Mounting plates.
Template for drilling.
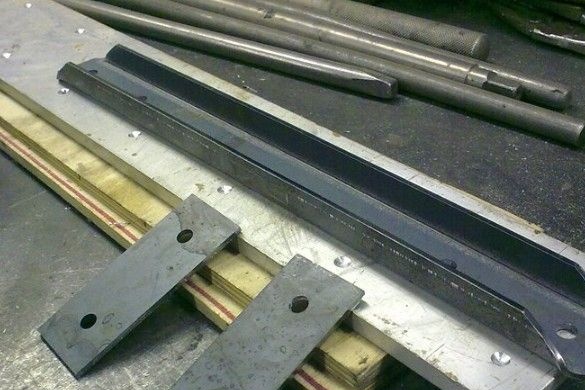
Finished holes on the conveyor belts for the manufacture of tracks.
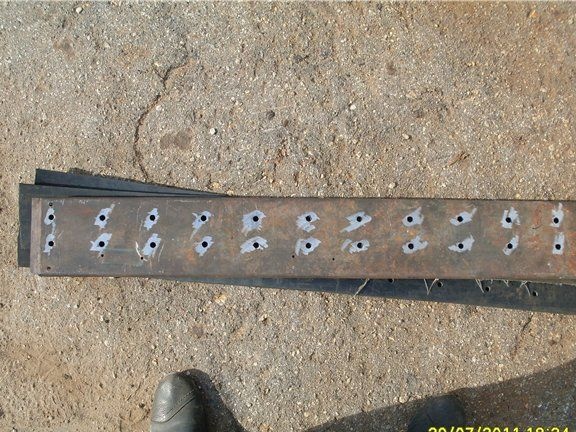
Drilling holes according to the pattern.
Assembly.
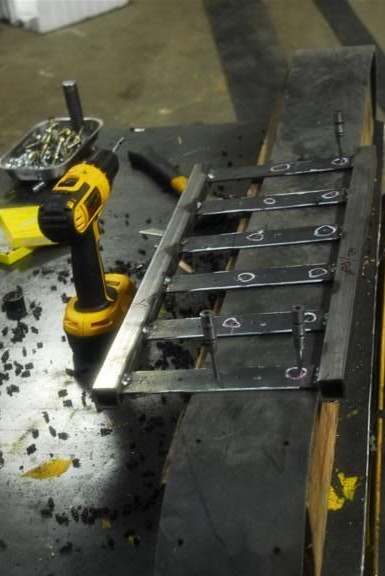
Device for drilling holes in rubber according to the method of a punch, but there is no need to beat on a punch, it is clamped into the drill chuck and the rubber is cut, very good holes are obtained and the effort is less.
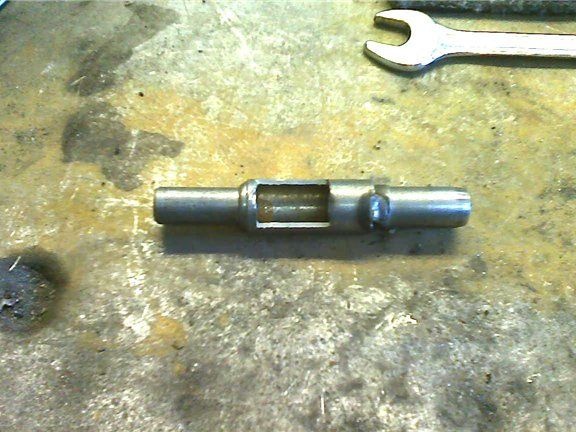
You can look at the video how to do it.
Photo of a fixture clamped in a drill chuck.
Photo devices for bending pressure plates and bent plates.
One caterpillar is ready.
Safety precautions. In order not to hurt to beat against the ends of the pipe and not to be scratched, it is better to protect yourself, even with gloves.
The caterpillar fits the sprocket, all the tracks are in contact with the teeth.
Front view.
The tension mechanism, made so that both sloths are pulled simultaneously, there are pros and cons to this method. Plus, the biggest-the same tightness of the tracks, provided that the tracks are the same during manufacture and are equally stretched, simplicity in execution and reliable mounting of the sloth axis. Subject to these conditions, driving straightness is ensured.
Cons-poor sealing of the boat, as the sloth shaft passes inside the boat, if one caterpillar has flown off, then both sides are relaxed in order to put on. Also to remove for repair if necessary.
Plates for attaching tension mechanisms.
Cuts and amplifiers are welded.
The fastening of the bridge.
Installation of disc brakes on the bridge from the VAZ, due to braking of the driving wheels, the all-terrain vehicle will rotate during the ride.
Guides on the inside of the track, at the upper bend along the edges of the canine, are 9 mm extended, this is with a plate width of 40 mm, the thickness of the steel is 2.5 mm. this is the limit for a press with a force of 10 tons.
Guides, with a plate welded inside for fastening to tracks.
Tool for making guide plates using a press.
This will guide the tension wheel.
The guide plate touches the brake hose from the disc brakes on the sprocket, so you need to change the brake hoses and put on the "Niva".
Clearances between the guides for the passage of the track through the sprocket of the track are permissible.
All plates are chopped and bent.
The caterpillar is the most labor-intensive and labor-intensive part of an all-terrain vehicle.
The caterpillar and sprocket should interact with each other without jamming at the entrance and exit of the star. Verification done.
Watch the video.
Engine installation.
Installing the clutch and gearbox.
Cardan installation.
CVT on the engine pulley. Transmission, so far only positive results, Kayurovsky CVT works with the Chinese engine very clearly. Initially, the problems were with releasing the belt at idle, but after adjusting the carb, everything returned to normal. Completely lets go at about 1000-1100 engine revs, setting at about 1500-1700 rpm. It is completely compressed by about 2500-2800 vol.
I could not understand why, by ear, the maximum speed was less than 3000 rpm, then I saw the gas restriction bolt completely wrapped, the Chinese apparently twisted for a quiet break-in, and also completed the control levers.
The first departure took place. First impressions are great.
All that I said about differential rotation is not entirely true. There are moments about which a little later. The all-terrain vehicle turned out to be quite light and nimble so far.
By the garage hands rolls in one, unfolds in 2 people. In the video, the surface is packed with snow, the first and third gas transmission, I press the levers with one finger, there is almost no noise from the stars.
He finished work with the controls (gear shifter and gas drive), and also made a universal joint protection frame. Made a small trip. Now everything is working clearly. Tomorrow I’ll make out everything for boat welding and painting.
Dismantled the all-terrain vehicle for welding and painting.
Flipped onto his back.
I scalded the bottom, there were sides and can be painted.
Braces installed.
Pulley shaft inside the casing.
Scald the sides and painted.
Painted everything inside.
Gearbox outside with oil fill plug and differential.
The inner lining of the rear part is corrugated aluminum sheet, 1.5 mm thick. This is corrugated aluminum. One side is smooth, the other is corrugated. Thickness is from 0.5 mm to 5 mm. It also varies in the brand of aluminum, one is solid, you’ll bend horseradish, the other bends quietly.
It is this 1.5 mm, the cost of the sheet 1.2mh3m almost 4t.r. The skin took 2 sheets.
Covering vnutryanka front part.
Covering the driveshaft setting the gear lever.
Gearbox trim and gearshift linkage mounting.
Sheathing outside.
Mounting the sides.
Engine compartment
Hood on the engine.
Frame for windshield.
Air intake and engine cooling hole.
He finished the hood and installed the seat.
I installed the lights and connected.
Handsome man!
Seats for passengers.
Departure
The seats are ready.
The control levers are ready.
Installed a fuel tank.
There are a lot of videos, if anyone is interested, you can look at the website. Improvements to the all-terrain caterpillar Parma will continue after break-in and troubleshooting. And now we wish good luck to all-terrainers.