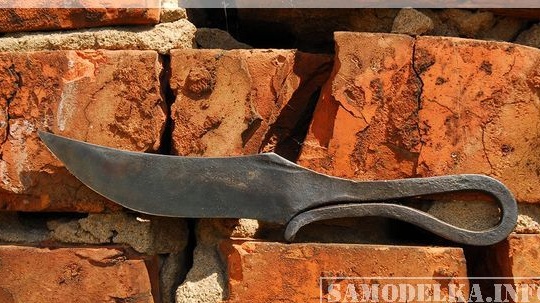
Blacksmithing is not a simple, but exciting activity. Forging from a piece of unnecessary trash a beautiful and useful thing is an occupation for a real man. Our author also decided to master the profession of a blacksmith and forge a knife from the outer race of the bearing.
Tools and materials.
Bearing;
Bake;
Anvil;
Hammer;
Bulgarian (metal circle, brush);
Ticks;
Vise
Two tubes with a diameter of 20 mm;
Sandpaper;
Capacity with engine oil.
First, the author of the grinder cuts the clip on one side along.
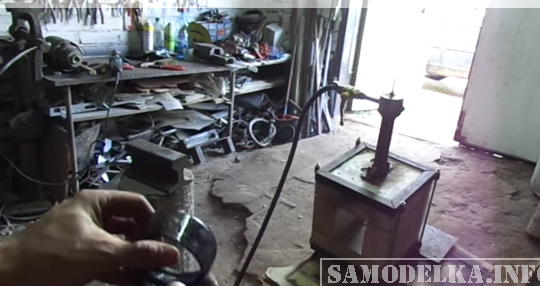
Since it is not possible to turn the workpiece in cold form, the author places it in the furnace. After the workpiece has warmed up, it removes it with the help of ticks.
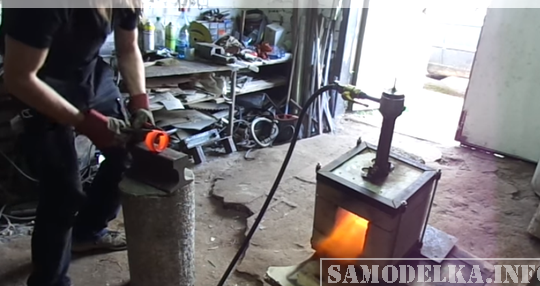
Clamping a red-hot part in a vice with the help of pincers unbends it.
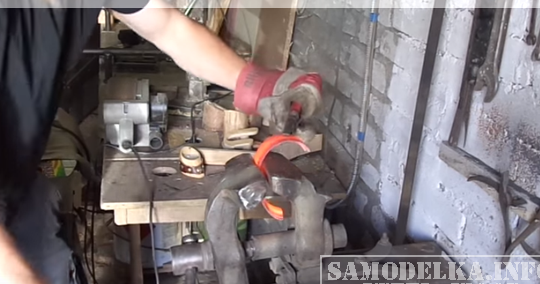
The result was a metal plate. Again, heating the workpiece in the furnace and putting it on the anvil with a hammer spills it, about half the length, to the desired thickness. From this part of the plate, a blade will be made in the future.
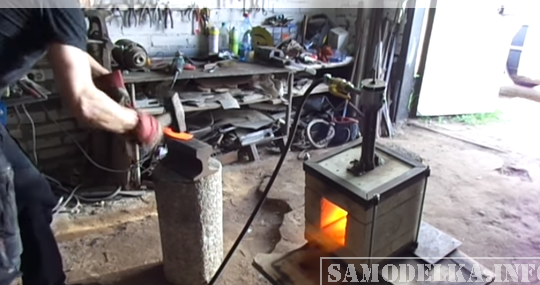
The inner part of the clip is not even as the outer, but has two grooves. Starting from the place where the splashed part ends, cuts off the edges, along the groove, with the grinder.
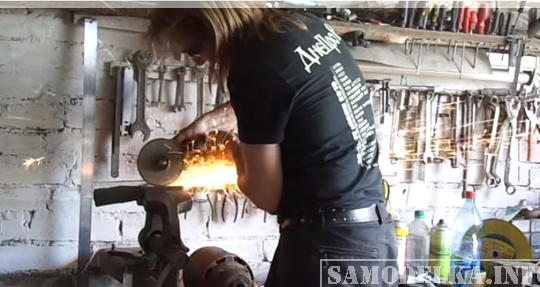
Further, the author continues to form a pen. Heating it and tapping it with a hammer stretches, giving its tail part a square shape of about five by 5 mm.
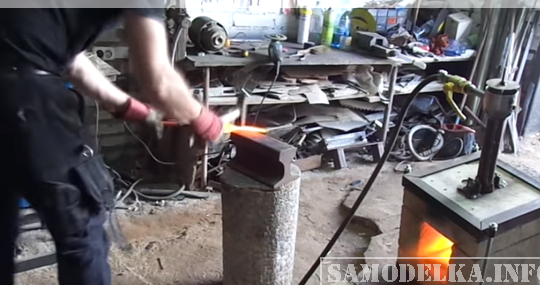
Again, heating the tail part and setting the transition point from the wide part to the narrow on the rib, tapping the hammer with the hammer shifts the tail part to one side and aligns it.
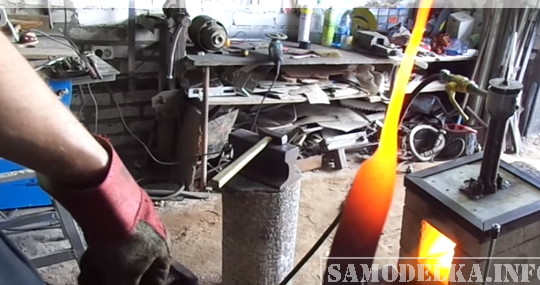
Having drawn with a marker the sting of a knife cuts it out with the help of a grinder.
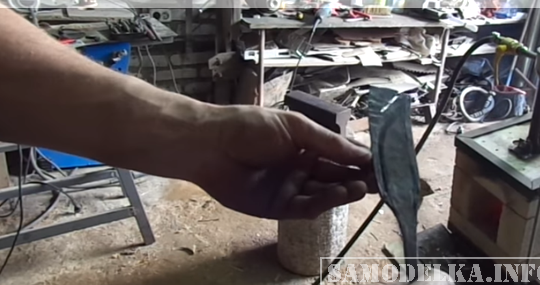
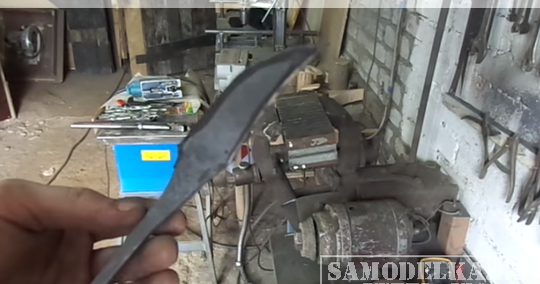
Gives the knife smoother lines.
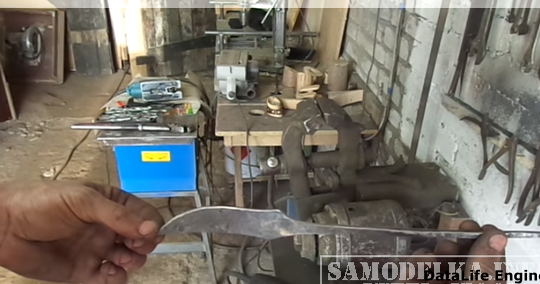
Further, the author shapes the pen. Having heated the shank, it begins to round it around two tubes and pincers clamped in a vice. The diameter of the tubes is approximately 20mm. When the metal gives in poorly, it warms it again and bends until the handle acquires the desired shape.
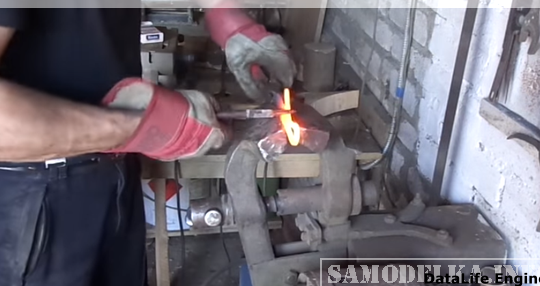
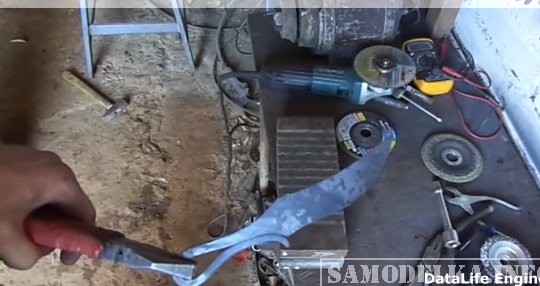
By installing an iron brush on the grinder, the knife is cleaned of scale.
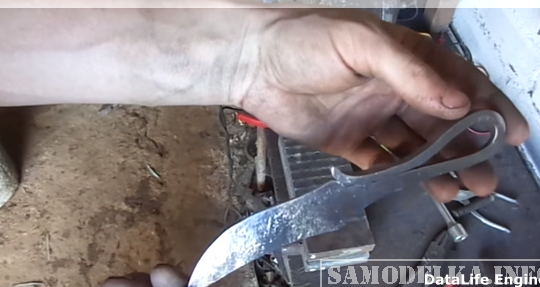
Sharpen the blade of a knife.
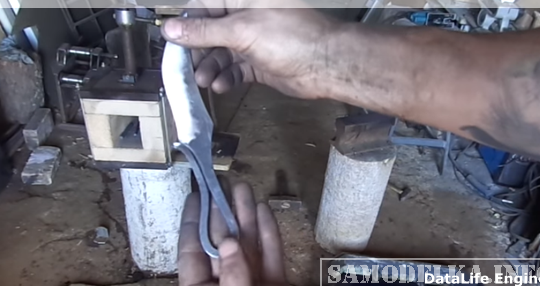
For hardening and burnishing, heats the knife in the furnace to a red tint and puts it in oil for a couple of seconds. Here is the result.
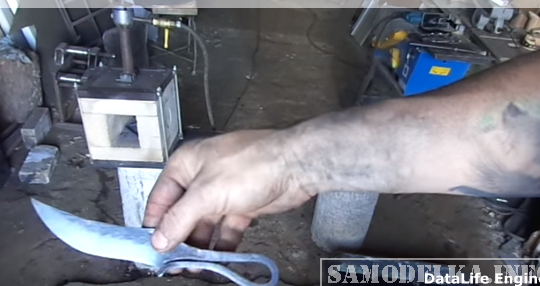
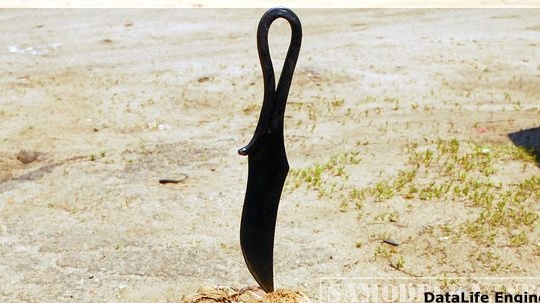
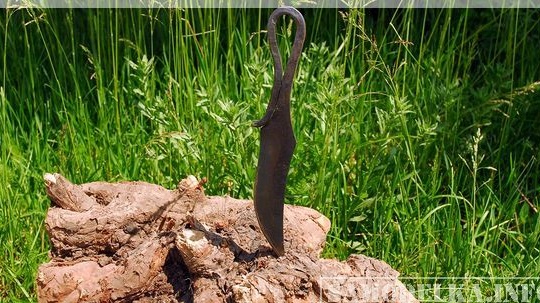
In more detail the weight of the process can be seen in the video.