There are many uses for empty glass bottles to create unusual things. Of these, vases, glasses, a variety of lamps and candlesticks are often made. Naturally in most homemade these glass bottles are processed, namely they are cut. Cutting the bottle evenly without cracks, chips, or additional scratches is not an easy task. It was to facilitate this task that this machine for cutting glass bottles was made. It is quite easy to manufacture, and all the materials necessary for its assembly are very cheap. Thanks to its design, it will be much easier to cut bottles than most other methods.
The materials that were used to create the machine for cutting glass bottles:
-wooden plank
small diameter plastic pipe
glass cutter
self-tapping screws
metal ruler
- guide from the furniture cabinet
epoxy resin
- L-shaped bracket
- several neodymium magnets
felt nibble
Description of the manufacture of a machine for cutting glass bottles:
Step One: Platform.
A wooden board will serve as a platform for the machine. It should be thick enough and wide for ease of use.
Cutting out or taking a finished piece of board you can varnish it so that in the future the tool has a more presentable appearance.
Step Two: Rollers.
Then a small diameter plastic tube was taken, from which two pieces were cut. Holes were made in these pieces of the pipe, each with 2 through holes at the edges. Through these holes, the tubes will be attached to the platform of the machine and act as a kind of rollers, since the glass bottle will easily slide on plastic. The upper holes of each of the tubes were enlarged so that through them it was convenient to fasten the tubes to the screws.
To avoid unnecessary scratches in the subsequent cutting of the bottles, it is necessary to carefully clean all burrs on the tubes.
Step Three: Work on the glass cutter.
Further, the author began work on the next component of the machine, namely the cutter.
For the manufacture of the cutter, a standard glass cutter was taken. In the glass cutter, a handle was sawn off as unnecessary, and two holes were made to fix it on a wooden plank.
Step Four: Guide.
Then the guide was taken from the usual furniture drawer. In order for it to serve in the design of the future machine, a milling cutter was made for each of the holes along its edges, so that the caps of the self-tapping screws reliably hide. After all, when working on glass bottles, every scratch can ruin under the tree.
Step Five: Build
Then the author began to assemble the obtained basic components for the machine. A glass cutter was screwed to the board, and tubes were also attached. Everything was done as shown in the photographs. The distance between the tubes should be chosen so that when placing the bottle on them, from its surface there is enough space left to the surface of the plank itself, while the bottle must be firmly fixed between the tubes when pressed.
The fastener of the glass cutter should be such that when pressing and scrolling the bottle, a thin line remains on it. If you get too much chips, or it only slightly scratches the bottle, then you should change the location of the glass cutter.
The easiest way is to use a test unnecessary bottle to find the optimal position.
The main thing is not to overdo it with pressure on the bottle, as it can burst.
Step Six: Attaching the Guide.
Then a prepared guide is fastened between the tubes. To make it convenient to measure the cut of bottles directly on the machine, the author decided to fix a metal ruler on this guide. To do this, the ruler was cut along the length of the guide and glued with epoxy glue. Then the load was laid on it until the glue completely dried.
Seventh step: Locking slider.
In order to prevent the bottle from moving out during scrolling, and its cut was fairly even, the author decided to make a bounding slider.
For these purposes, an L-shaped bracket, several strong neodymium magnets and a piece of felt were used.
Having placed magnets on one of the bracket parts, the author wrapped them in felt and attached them to an iron ruler. Since strong pressure should not be exerted on the bottle, a similar design of the slider will be able to hold its desired position.
Step Eight: Testing the machine.
Now you need to check the resulting bottle cutting machine.
Thanks to the ruler and the magnetic slider, the bottle is sliced quite smoothly, although of course a lot depends on the accuracy of the user himself. Therefore, it is worth starting to practice on unnecessary bottles.
Having cut the ring on the bottle, it is necessary to warm it slightly above the candle, then draw it with ice and the bottle should crack evenly along the cut line. If this did not work out right away, then the procedure should be repeated. This process is clearly demonstrated in the images below.
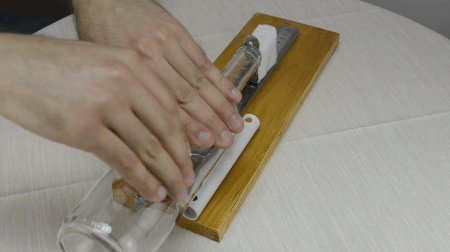
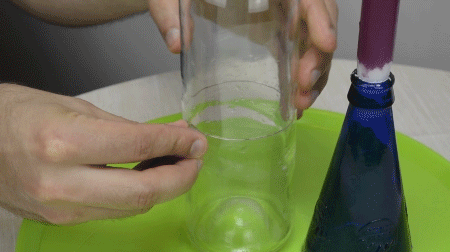