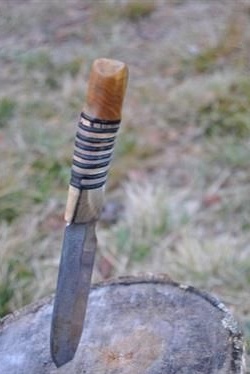
If you have some free time and an unnecessary spring from a truck or another car, then you can do it yourself make a pretty and unique knife. Perhaps the first time it will not be completely perfect, but the main thing is that it is made with your own hands. The main charm of this homemade is that the knife can be of almost any shape, you just need to turn on a little imagination.
Materials and tools for homemade:
• grinder;
• spring from the truck;
• file;
• epoxy resin;
• linseed oil.
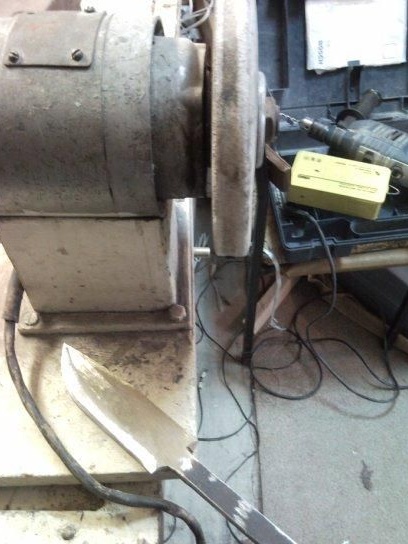
Knife making process
Material for the blade can be obtained at any car market, sometimes cars may lose spring right in the middle of the road. In this case, the spring from Kamaz is used. You can take it from another car, in which case the thickness of the blade will be less, and it will not be necessary to reduce it manually.
Step 1. Material Preparation
With the help of a grinder, the author cut it into three parts, since the part has a different thickness and a rounded shape, it is necessary to choose the optimal part for this type of knife. That part of the spring, which is ideally suited for the blade, is cut in half, in the end there are two identical blanks.
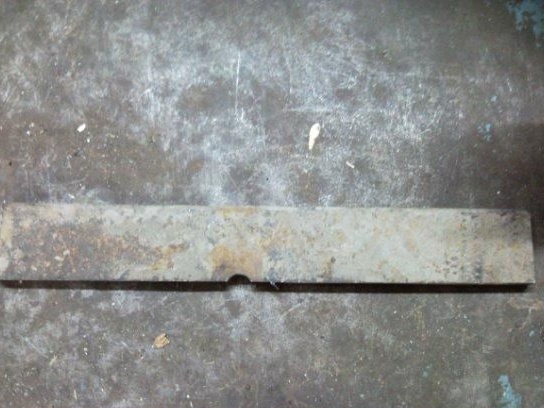
Step 2. The shape of the knife
You need to take the workpiece and roughly divide it into two parts in half, the knife blade itself will be made from one half, the second half will go inside the handle. The part that will be in the handle needs to be cut a little on both sides so that it becomes smaller and can fit in the handle.
Since the spring has a thickness of about 8 mm, and there are practically no such knives, you need to erase the thickness for a long time to the desired value. Then on the machine you need to make the shape of the blade, it is desirable that there is a fine-grained stone, otherwise, the knife will look rough and a little not accurate.
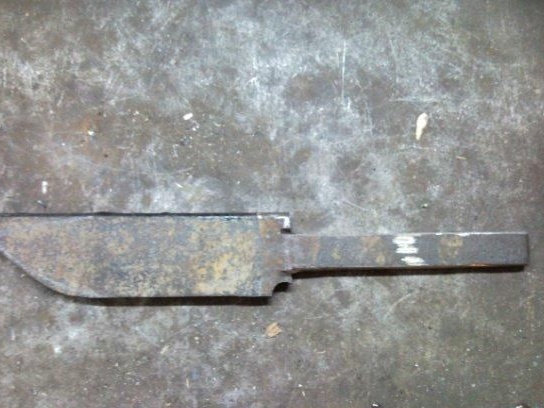
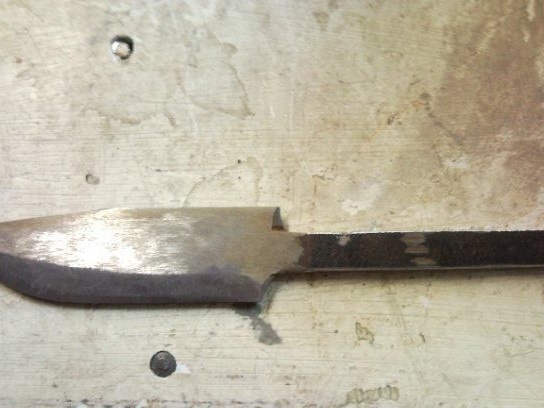
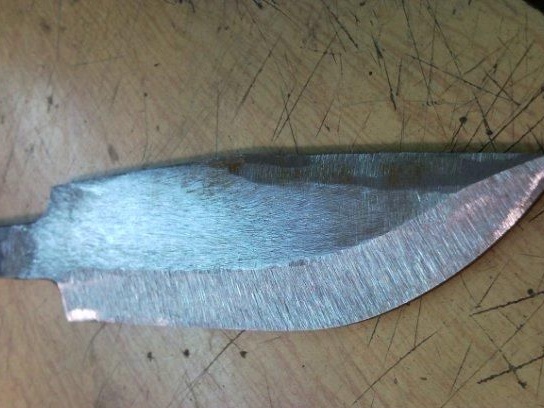
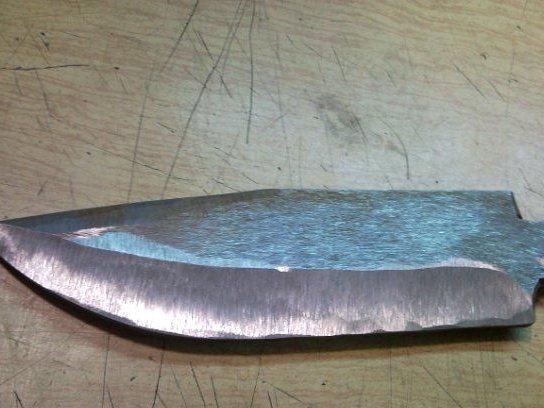
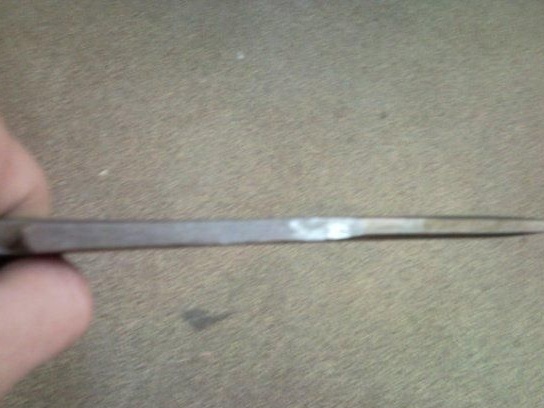
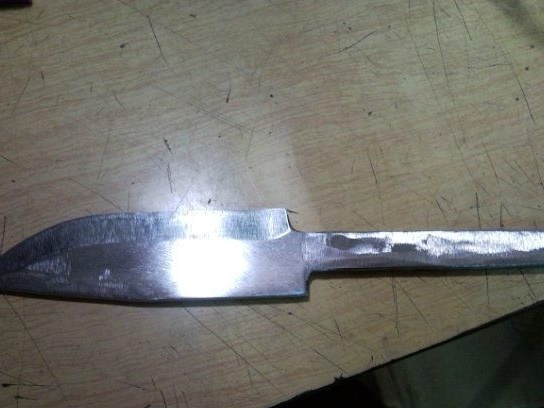
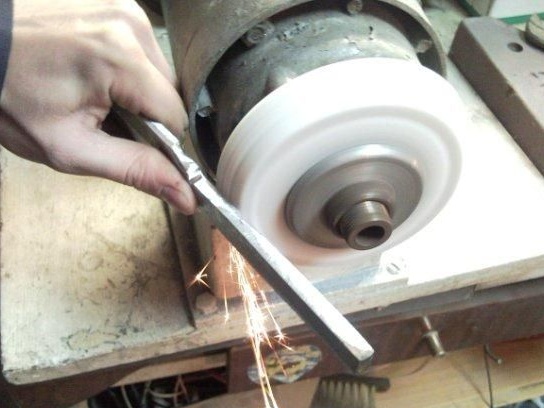
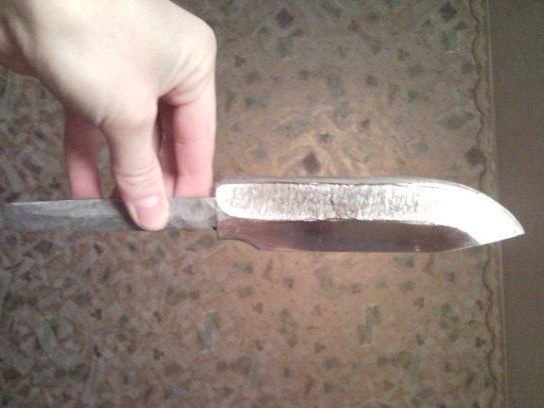
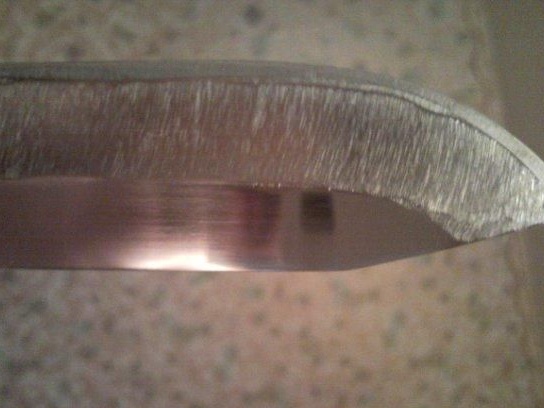
Step 3. Create a handle
You need to take a small wooden block (pay special attention to choosing a tree for the handle) and grind the handle of the desired shape, in this case you need to use your imagination and imagine how you want to see your future knife. With the help of a drill and needle file, a place is prepared for that part of the blade, which should be in the handle. For better fastening, you can use epoxy resin.
The author decided to make a combined handle using rubber, birch bark and a birch cap.
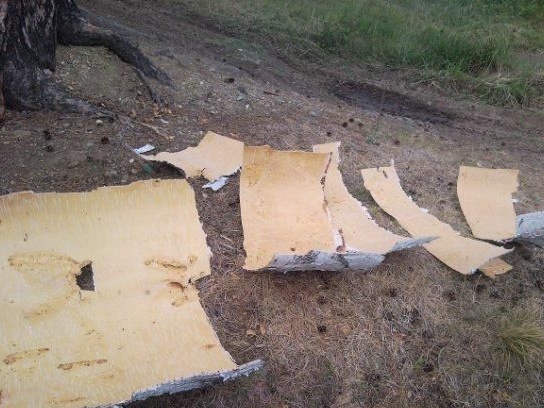
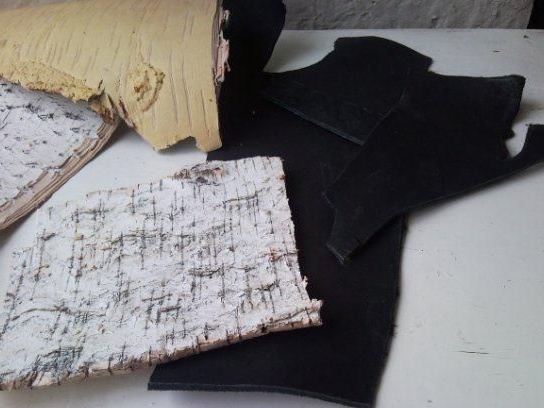
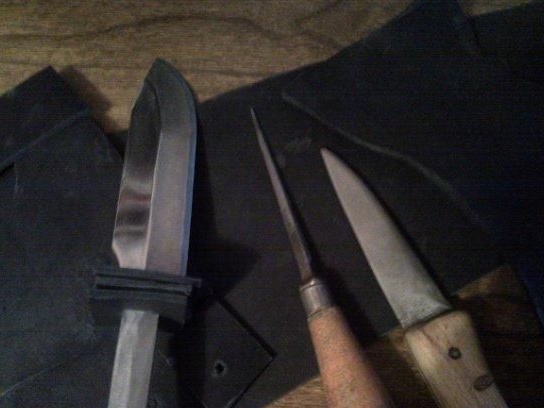
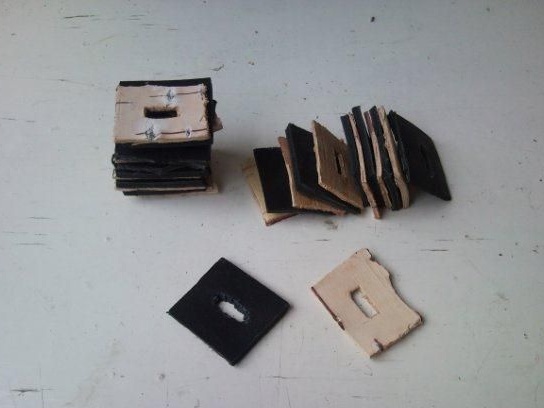
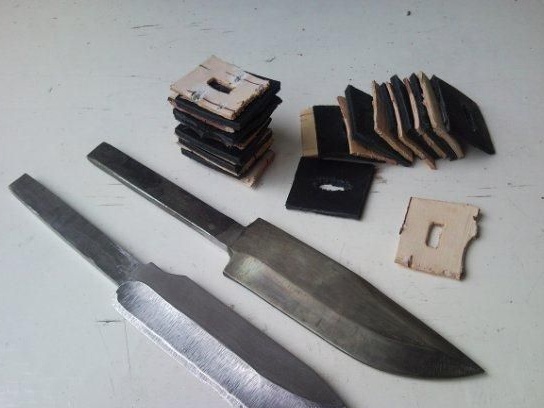
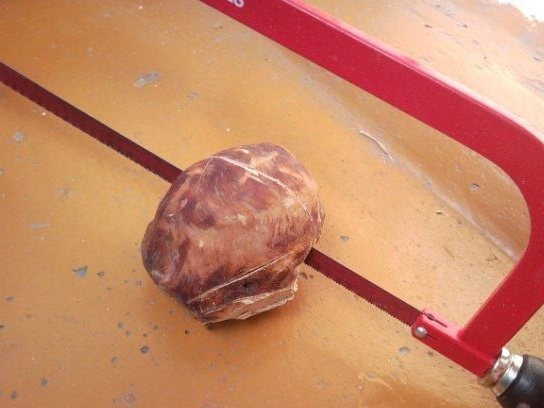
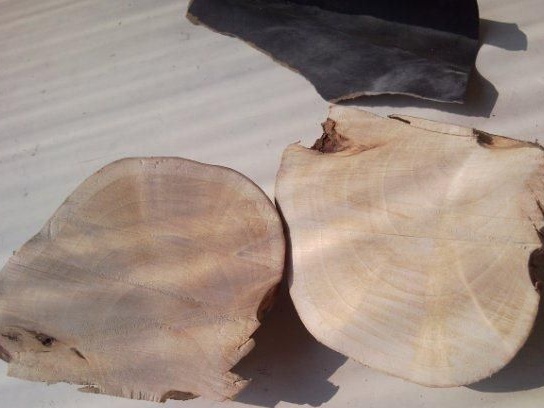
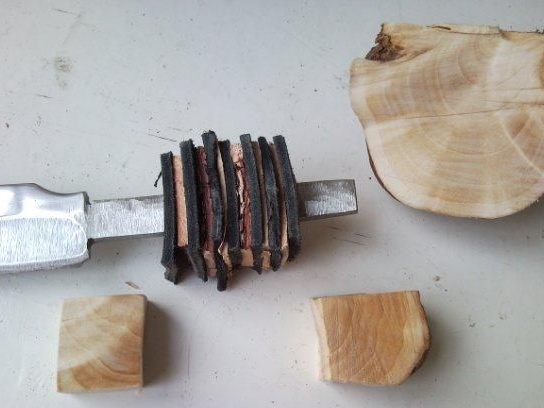
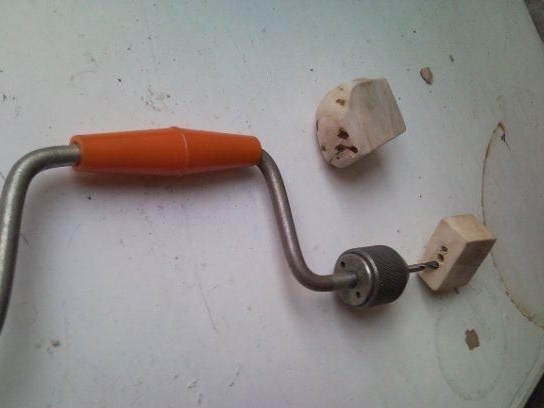
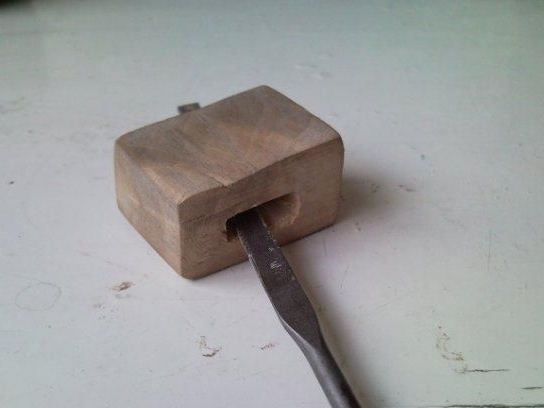
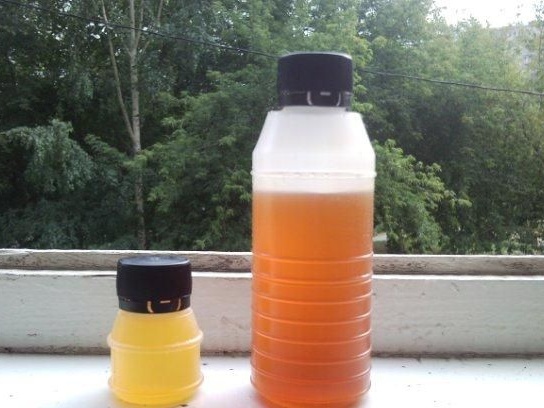
Cut off the excess and grind ...
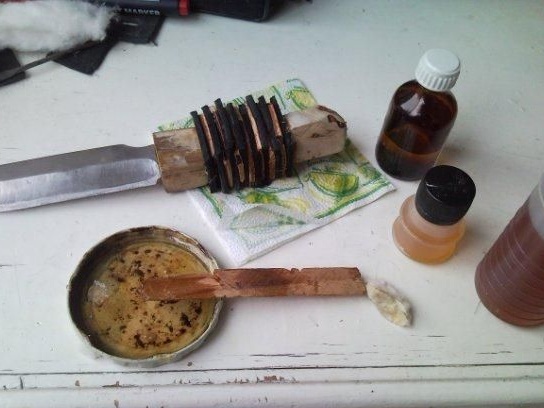
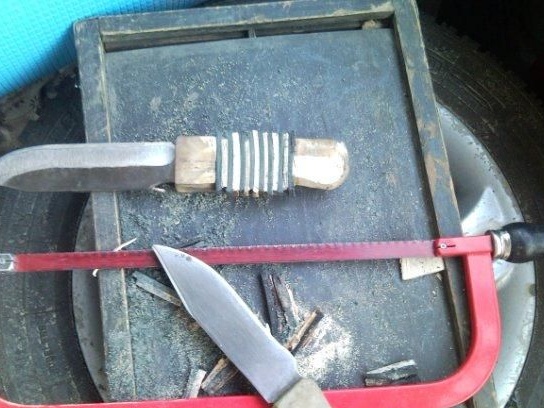
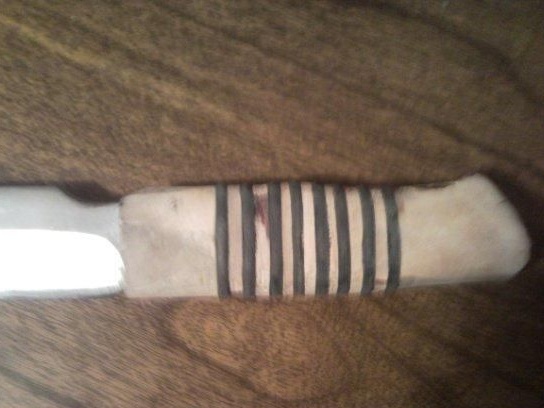
After all the procedures you need to handle the handle.You will need linseed oil, heated in a water bath to a temperature of 70-75 degrees. In this case, the knife must first be hidden in the freezer for 30 to 40 minutes. When connecting a cold knife and warm oil, bubbles begin to run along the handle, so the air leaves the tree, and this place is filled with linseed oil. This procedure needs to be done several times. After that, the handle of the knife is placed in oil for at least a day.
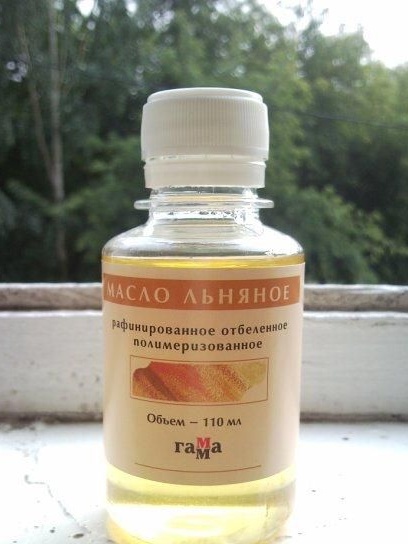
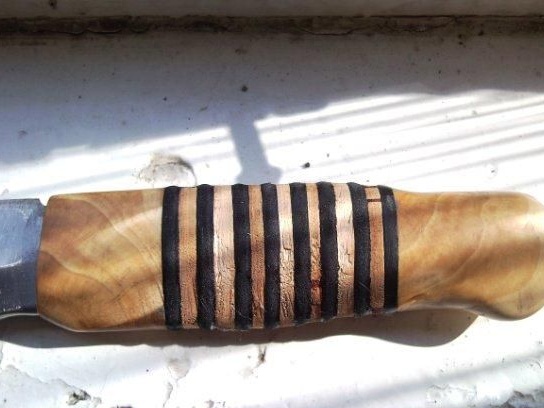
Step 4. Making the sheath
It will take a small piece of leather, in the shape of a knife you need to make a pattern. Holes are made using an awl (since the skin is a very tough material), and then the parts are sewn together with an ordinary strong thread.
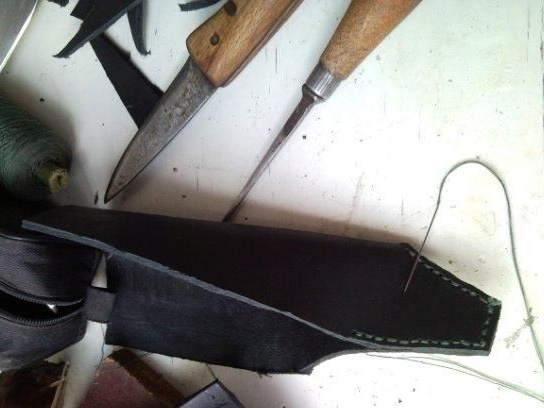
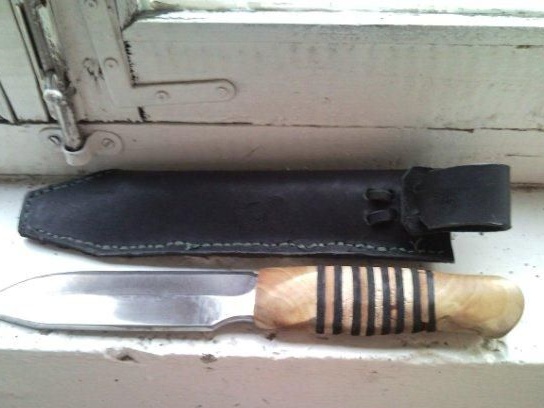
Conclusion
From a car spring, you can get a very beautiful and high-quality knife. In order for the blade to cut well, you need to make the angle of the cutting edge about 35 degrees, in which case, it will work well with wood, and chop various small objects.
Since the knife is made of heavy metal, its weight is not small, but in use it is rather a plus. No need to make a primitive pen, you can show a little imagination and give it an unusual shape, so immediately it becomes clear that the blade is really unique and made by hand. This knife is ideal for hiking.