Every peasant living on his land, even if it is poor, must have a tool for its (land) cultivation. In the beginning I had one shovel, then two, then a rake and a pitchfork were added to them, and, finally, there was a need to acquire a mechanical device, in common people - a motor block. Well, in fact, how much can you bend your back on the field .... A cultural trip to the shops in search of something suitable plunged me into gloom, everything "suitable" cost from 20 thousand tickets of the Bank of Russia. Or more. And here, as always, I was helped out ... by the heap of scrap metal that one of my good friends collects in our village.
So, from this scrap metal I got what was left, namely: a frame with a frame, a piece of motor and screws from the Krot motoblock, which is somewhere .., once .., in Soviet times, something ... someone ... in the garden plowed. It is clear that everything that was delivered was in a deplorable state, of course, who will hand over a good thing in scrap metal!
To make an electric traction motor block, I needed the following:
1. Actually, the walk-behind tractor in the form of a pile of old scrap metal
2. Electric motor from an old 4 kW elevator
3. Capacitors 1 ... 3 microfarads 400 V in the amount of 70 pieces.
4. Switch 250V 10A
5. Cord with plug 5 m
6. Insulating tape 2 rolls
7. Bolts, nuts for mounting the engine to the frame.
8. Drill, drill.
9. Grinder, welding.
He went through the gearbox, straightened the screws with a sledgehammer, and removed everything unnecessary, leaving only the pulleys, frame and steering wheel of the walk-behind tractor. Without even trying to restore the disassembled engine, I immediately decided to screw instead ... an electric motor!
Moreover, in the garage 4 kW engine from a freight elevator has rusted for a long time. He also got to me on the occasion when a freight elevator was changed at a friend’s store. It was not possible to pick up the entire elevator; I only got an electric motor.
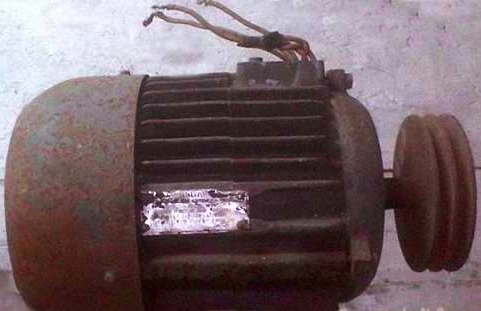
As it turned out, the motor was three-phase, at 380 V, so I had to redo the circuit of its connection to a single-phase 220V network using a phase-shifting capacitor.
There are a lot of schemes and formulas for calculating on the Internet on this subject, after a short search and several practical experiments, I chose this one.
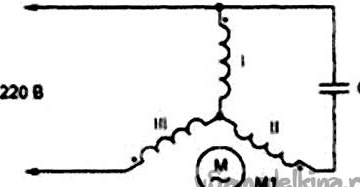
The problem was with the capacitor. For reliable engine start, the calculations required a capacitor with a capacity of at least 100 μF, a voltage of at least 400 V, and 60 μF would be enough for operation. Naturally, I did not have such a powerful capacitor. IN "electronics»There were such capacitors on sale, but, firstly, this is not our way, and secondly, for the money I pay, the local tractor driver will plow the whole garden with his hands, not like his own tractor. I tried to use electrolytic capacitors in series connection. Due to the fact that the use of electrolytic capacitors in various switching options (with and without diodes) did not give a positive result, I will not give these schemes here. Maybe someone did, but I don’t. The engine worked, but the capacitors quickly began to heat up and explode. I tried to put paper capacitors, such as MBM or BMT, but in this case, the capacitor bank became comparable with the motor itself. Help came unexpectedly ... from boards from burnt computer power supplies. In each of the boards, I found several ceramic capacitors for 1 uF 400 V. I shoveled a bunch of burnt boards from the power supplies, and having checked all my stock of radio components, I scored various capacitors as much as 78 uF.
I soldered all the found capacitors in parallel into small blocks, and connected the blocks together and brought the wires out. The result was a capacitor bank, which I wrapped well with electrical tape, sealed it in a plastic bag, put it in a plastic bottle, then in a can and screwed it to the motor.
Then he connected the contacts in the junction box according to the above diagram and checked the operation of the motor.
Then everything was simpler: I cut off the old pulley with a grinder, welded a new pulley directly onto the engine shaft, picked up a suitable belt, installed a tension roller, adjusted the manual clutch on it ... and the electric cultivator is ready!
I put the wires from the engine into the corrugated hose and held it out in the steering wheel tube. I put a powerful switch near the handle, and brought the cord with the plug out of the other steering tube.
It looks, of course, this device is monstrous, but in our village not even such dinosaurs are sometimes found.
Previously, I used various gasoline motoblocks many times, rented them from friends or neighbors. But now I felt, as they say, the difference. Impressions from work - fantastic, plows quickly, without noise and smoke, everyone likes it and everyone wants to try it! A six-meter bed in two passes plows in 7-8 minutes. And the cost of operating such an electric motor unit is many times lower and simpler than gasoline.
In the course of work, it turned out that if you adapt, then the wire does not interfere. The extension cord I use is home-made, at 30 m, from a simple light wire. And it's good that he is not powerful, and not branded. Once I still jammed it (wire). So he just broke, and the walk-behind tractor stopped. Even the machine on the shield did not work, and nothing sparkled. Then he simply connected the ends, insulated, and again into battle.
And one more interesting detail. When I wanted to sharpen the cutting edges of the screws, my neighbor, a local peasant, saw, and dissuaded me. The fact is that if the edges of the auger are sharp, then the roots of the weeds (especially the bindweed) are cut by the lobes and then grow very quickly, and twice as much. And if the edges are dull, then the roots and grass are wound on the screws, and then you just pick it out and throw it away with your hands. Here is such a weeding along with plowing.