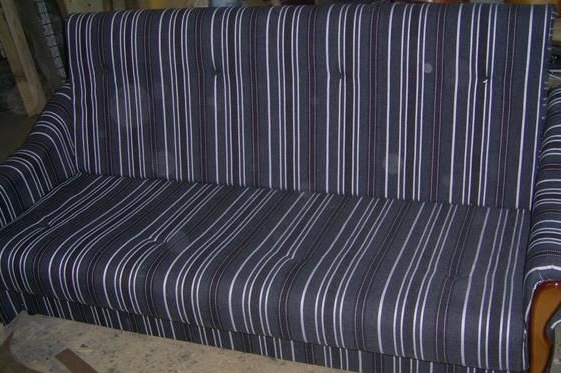
Make soft furniture not just, it requires attention and accuracy. But despite this, most items home furnishings, if desired, can be made do it yourself, for this it is necessary to have a desire, and appropriate tools. In this article, the author will describe the process of making a sofa book. model is very popular as it is very compact and easy to use.
To make a sofa-book we need the following:
Instruments:
- roulette;
- available cutting tool;
- angular ruler;
- a pencil;
- hammer;
- screwdriver;
- set of drills;
- set of wrenches;
- stapler.
Materials:
- foam rubber 25 of the density of the following sizes: 2000 × 1400 × 60 (1 sheet), 2000 × 1600 × 40 (1 sheet), 2000 × 1600 × 20 (1 sheet);
- fabric 6 m / p 1.4 m wide;
- transformation mechanism for a sofa-book (1 set);
- wooden lamellas and holders 32 and 64 pcs. respectively;
- non-woven 4 m / p;
- plastic legs (4 pcs.);
- fiberboard 1.7 × 2.75 with a thickness of 3.2 mm (1 sheet);
- furniture bolts 8 × 120 (4 pcs.);
- furniture bolts 6 × 40 (4 pcs.);
- furniture bolts 6 × 70 (8 pcs.);
- nut 8 (4 pcs.);
- nut 6 (12 pcs.);
- nails 70 (20 pcs.);
- nails 100 (40 pcs.);
- 89D screws (20 pcs.);
- 51D screws (16 pcs.);
- staples 10mm (1000 pcs.);
- staples 16mm (300 pcs.);
- glue for foam rubber;
- timber: 40 × 60 × 1890 (2 pcs.); 40 × 60 × 1790 (2 pcs.); 40 × 60 × 530 (6 pcs.); 40 × 50 × 330 (4 pcs.); 50 × 50 × 200 (4 pcs.);
- 25mm thick board: 1900 × 200 (2 pcs.); 800 × 200 (2 pcs.); 800 × 50 (2 pcs.); 1000 × 50 (12 pcs.).
Let's start manufacturing.
We make the first part of the sofa, a linen box.
For this we use the following sizes and materials:
- 2 boards 25 mm thick (40 mm thick or plywood 20 mm), 1900 mm long and 200 mm wide;
- 2 boards 800 mm long and 200 mm wide;
- 2 boards 25 mm 50 mm wide and 800 mm long;
- 4 beams 40 × 50 (50 × 50) 200 mm long.
When the body parts are ready, we begin to assemble the box. In order to strengthen the structure, we add two transverse beams, we fix everything with self-tapping screws. At the bottom of the box we install a sheet of fiberboard with a size of 1800 × 800 mm.
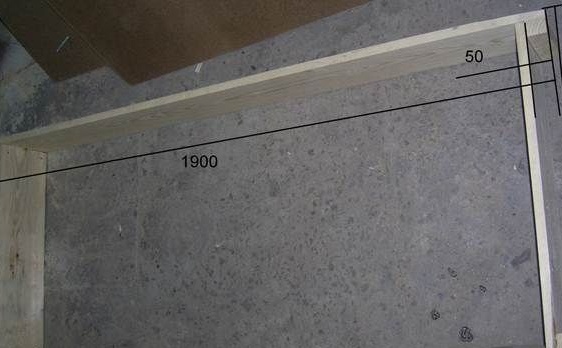
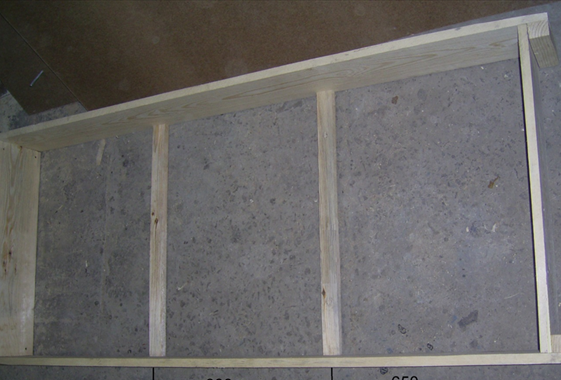
After we have done the linen box, we begin to collect the seats and backs.
We make two identical frames, with such dimensions 1890 × 650 mm, for this we use a bar 40 × 60 mm. We fix the parts with each other using nails and self-tapping screws.
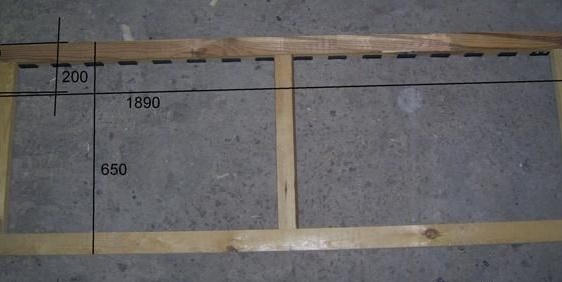
When both frames are assembled, we install wooden slats.
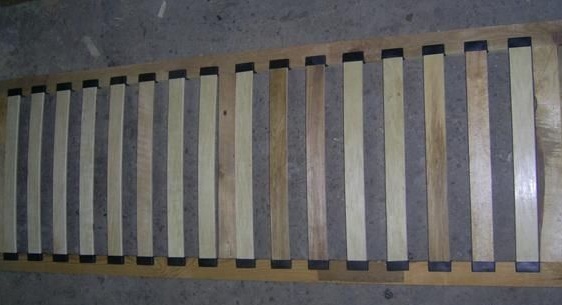
Next, we make the armrests. We take a fiberboard sheet, and according to the dimensions shown, cut out 2 left and 2 right armrests.
When these elements are cut out, we make a frame of wooden blocks along the contour of the product, we fix them with self-tapping screws or nails. Then we mark and make holes, we use a drill with a diameter of 8.5 mm, when everything is ready we put bolts 8 × 120 mm, after that we close the frame with a second sheet of fiberboard. Similarly, we do with the second armrest.
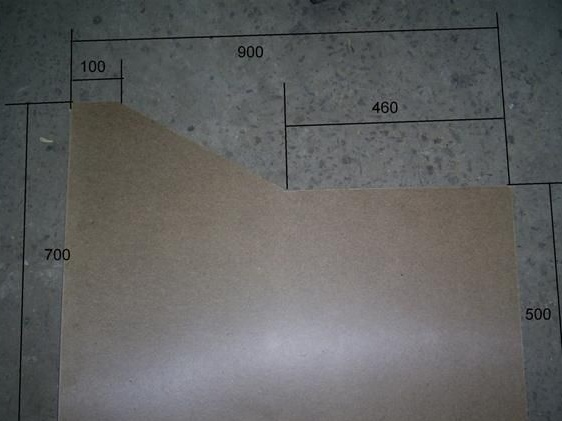
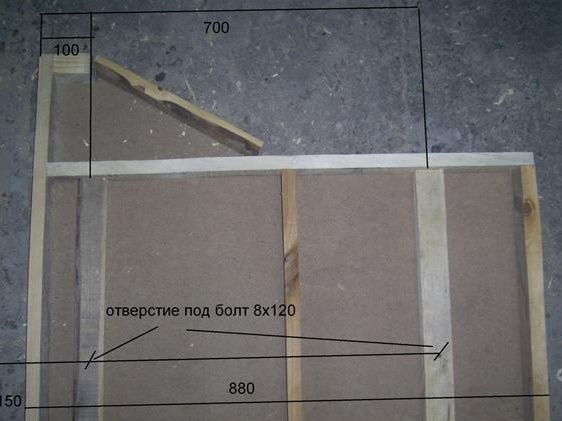
Now we return to the linen box, on which we need to make two holes on each side, using a drill with a diameter of 10 mm.
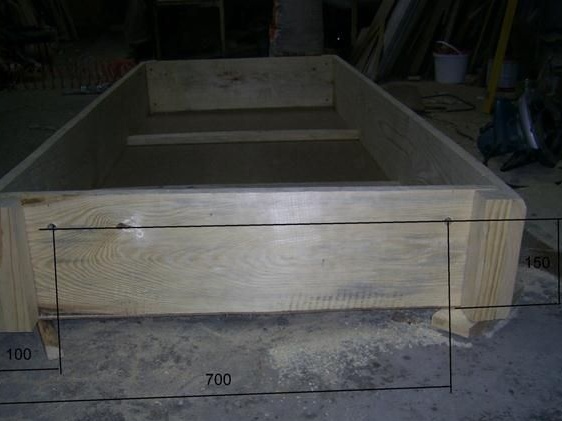
When all parts of the frame are assembled, you can begin to assemble them in a single design. We make installation of special mechanisms for transforming a sofa; they can be bought in specialized stores. We install them so that in the unfolded position between the seat and the back there is a gap of 10 mm, and the sofa code is complicated, the seat should not protrude beyond the armrests.
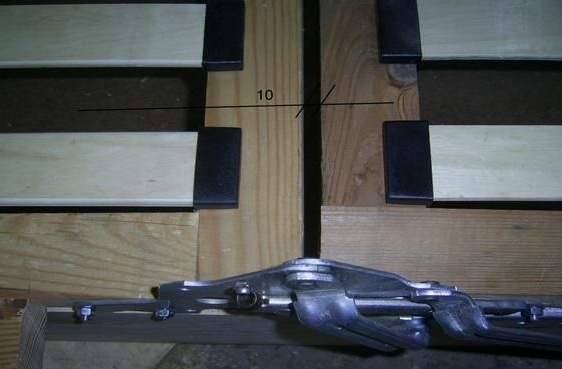
This is how the assembled sofa looks.
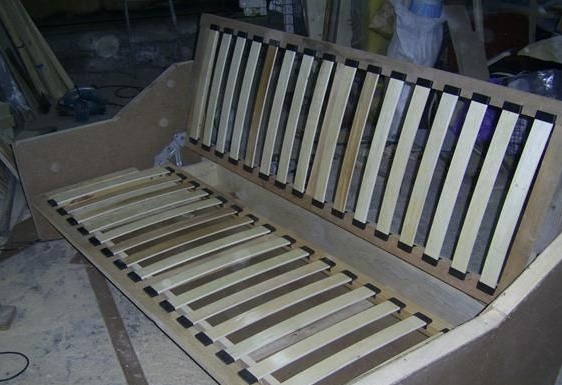
The structure can be further strengthened using wooden battens.
Next, we begin to sheathe the body with foam. To the place where the lamellas are located, we nail in flesilin. We put foam foam with a thickness of 60 mm on it. We cut everything according to the size of the frame, make cuts for the mechanism.
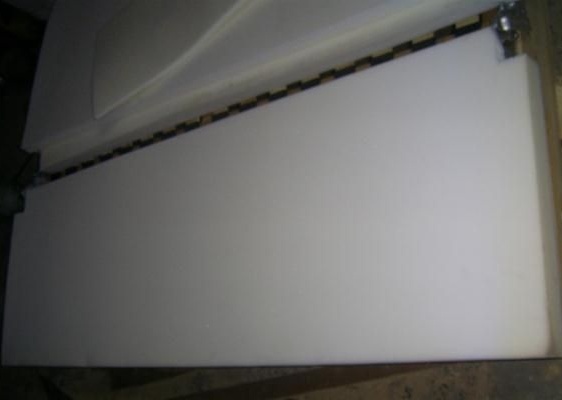
Now on the edge of the seat we put an additional strip of foam rubber with a thickness of 20 mm and a width of 200 mm, it is needed so that the edge of the sofa is a little softer.
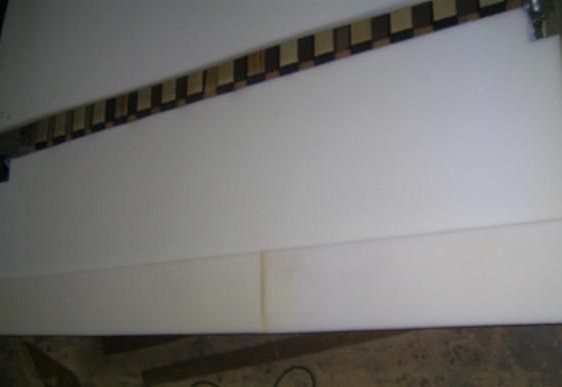
After that, we glue another layer of foam rubber with a thickness of 40 mm, the edges of which need to be brought under the seat. We do the same with the back of the sofa. Next, you need to pull on special covers that were previously sewn.
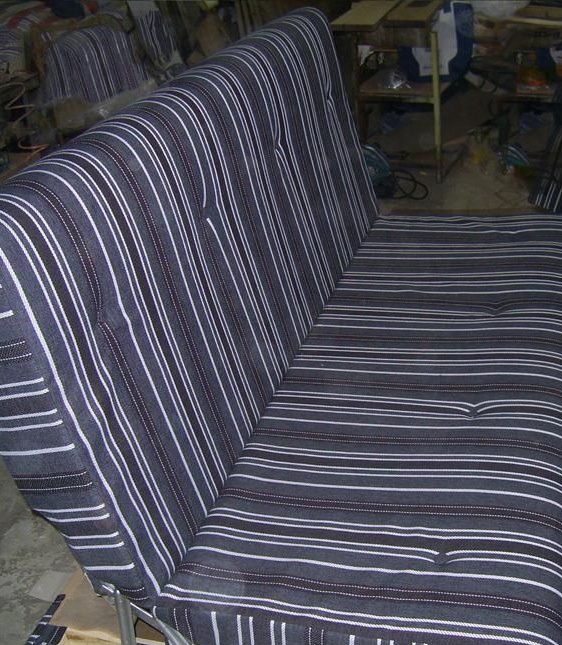
Now back to the armrests and finalize them, for this we take a foam rubber 40 mm thick and make a roll shape out of it. The beginning of the armrest should be about 150 mm wide, and narrowed to 50 mm closer to the middle, and so on to the end.
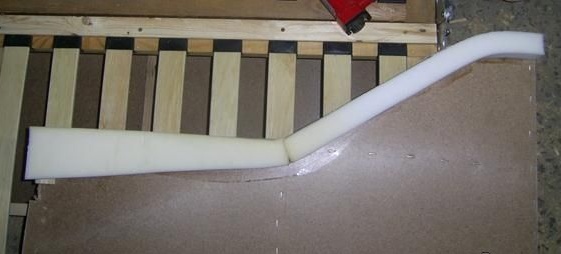
Now, on top of the armrest, we nail another layer of foam rubber with a thickness of 20 mm, it must be bent in the form of a roller. We fix with brackets and cut off the excess parts.
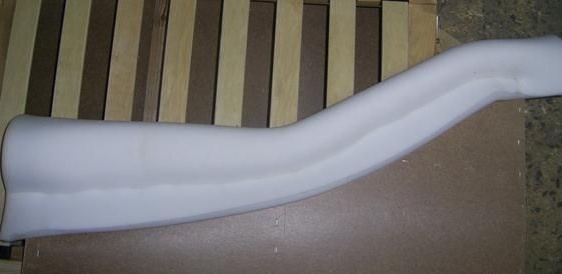
Next, the past should be deployed to itself with bolts, on which foam rubber with a thickness of 20 mm must be glued. We glue it, stepping back 320 mm from the bottom of the armrest.
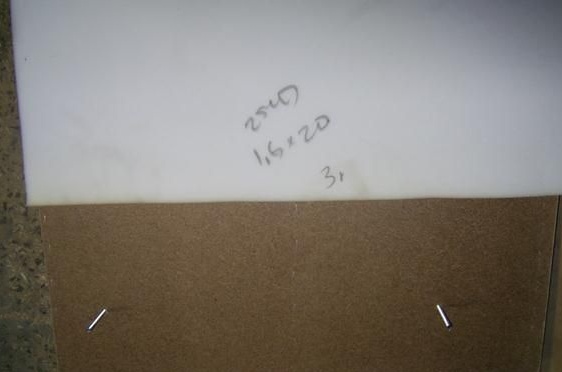
When the foam is finally adhered, you need to wrap the back part on top of the material. We fix it with brackets and cut off the unnecessary parts.
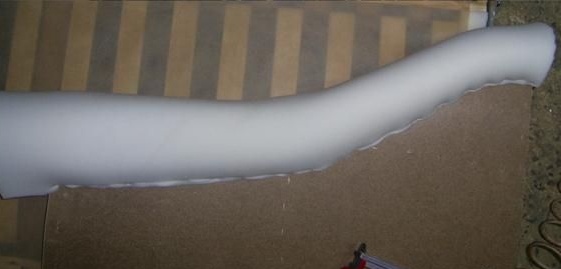
The sticking foam must be bent at the end of the bull’s side, as shown in the photo.
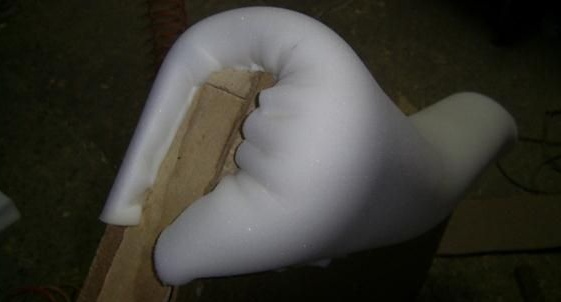
Now you can fit the armrests with fabric. Next, we install special fittings.
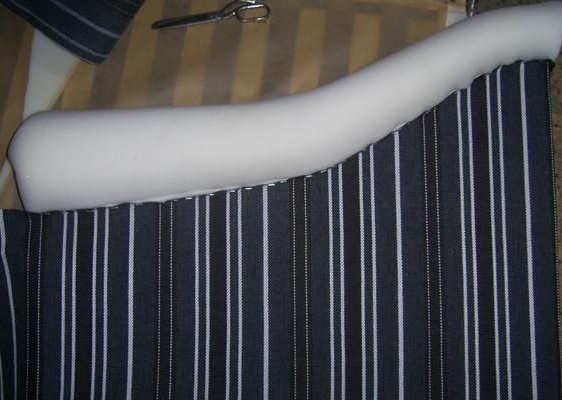
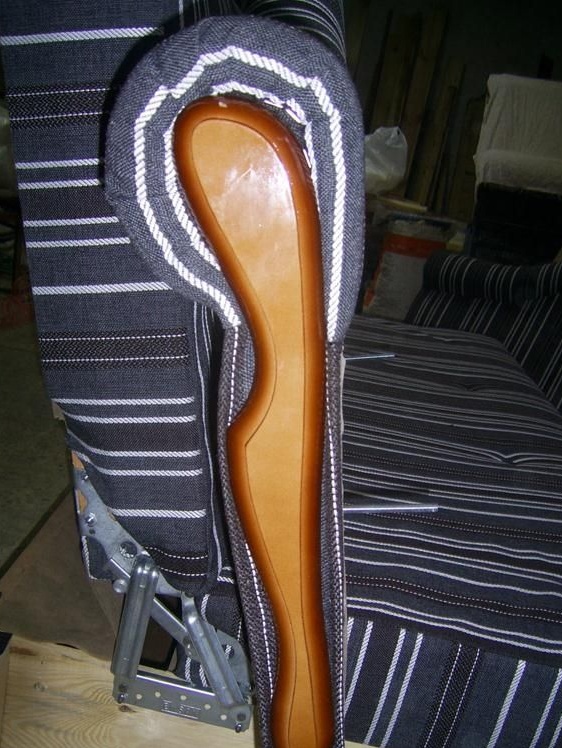
The sofa is assembled. So it looks in the finished version.
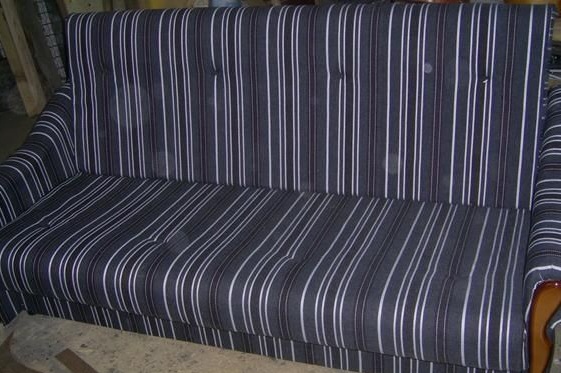
And so, when laid out.
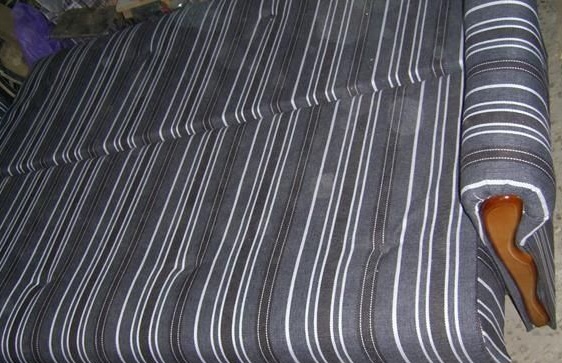
This article is over, thank you all for your attention.