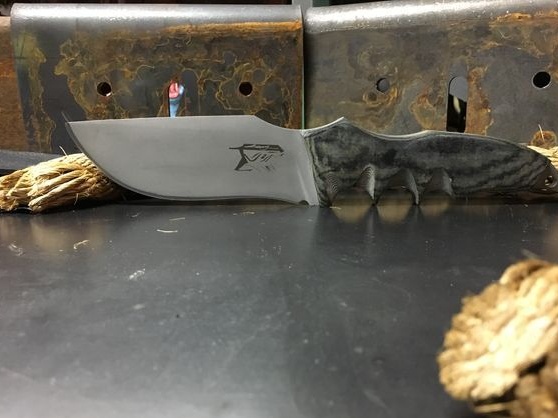
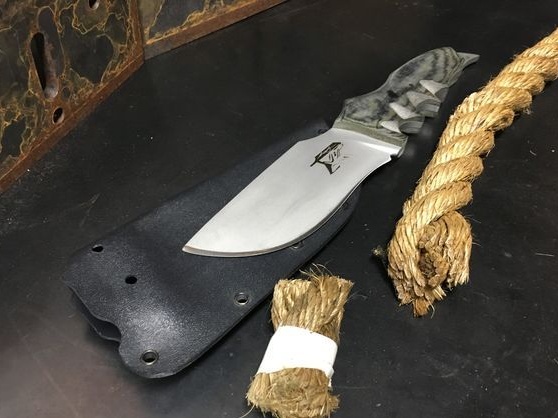
If you see such a knife somewhere in the store, then it can hardly be distinguished from some cool brand that sell for a lot of money. It is not so difficult to make such a knife, of course you need a certain set of tools. Specifically, in this case, the author used such an "exotic" as a sandblasting apparatus and a device for applying laser engraving. But many craftsmen make such knives only with the help of a grinder and a belt grinder. In addition to the knife itself, the author also made a sheath for him.
Materials and tools for homemade:
- strong sheet steel;
- linen mikarta;
- vise;
- grinder;
- sandblasting machine;
- laser engraver;
- a furnace for hardening metal;
- sandpaper;
- belt sander and more.
The process of making a knife:
Step one. Design development
All such knives are made according to one principle, first you need to make a knife design on paper. You can invent it yourself or find it on the Internet ready and then print it on a printer. Next, the design needs to be cut and a piece of paper attached to a piece of steel from which the knife will be made. Well, then it remains to circle the shape with a sharp object.
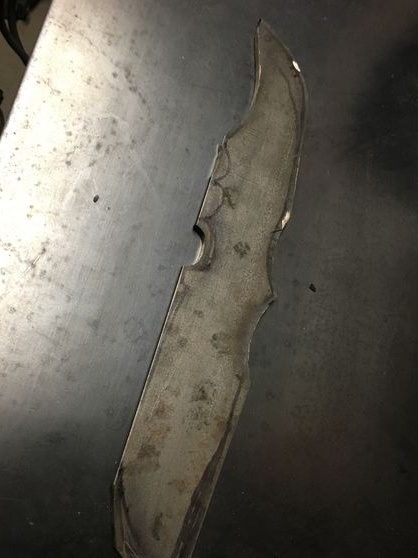
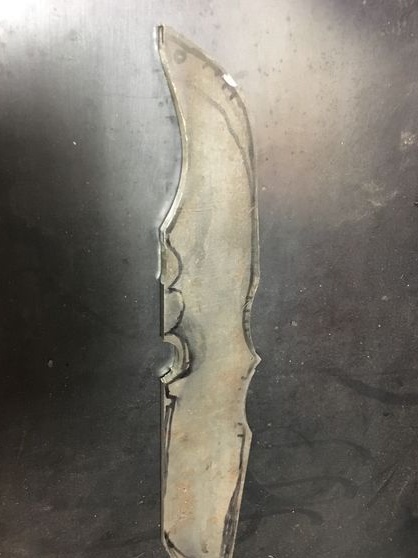
The author cut out the profile with a grinder, cutting wheels and grinding wheels will be needed. You need to work slowly, slowly, adhering to all necessary safety standards. You can still use the grinder and other tools for metal processing at your discretion.
Finger grooves are most conveniently made using a rotary sander.
Step Two Creating a knife profile
You can create a beautiful high-quality profile using a belt sander. The author chose the angle manually, well, the eye, without using any additional clamps. In this process, there are two interesting points, breaking which, you can ruin the workpiece.
The first refers to the case when the metal is very overheated. This leads to its active oxidation and reduces strength.
And secondly, if the steel is made too thin, the knife can easily “lead” and the blade will become wavy. The author recommends grinding to a size of at least 1/8 inch, and the starting material was 1/4 inch thick.
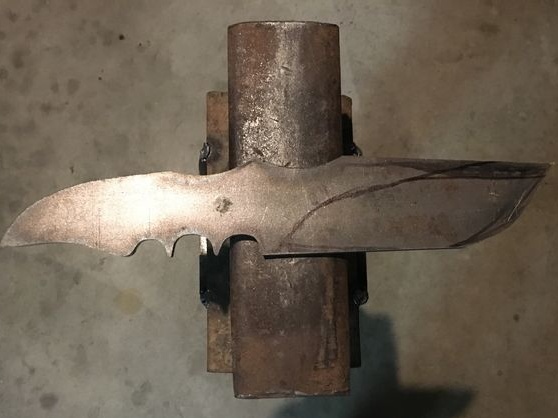
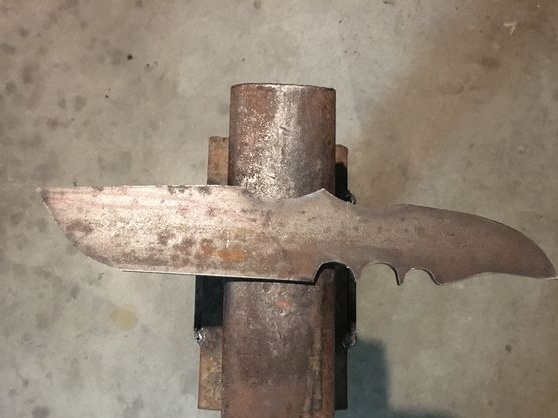
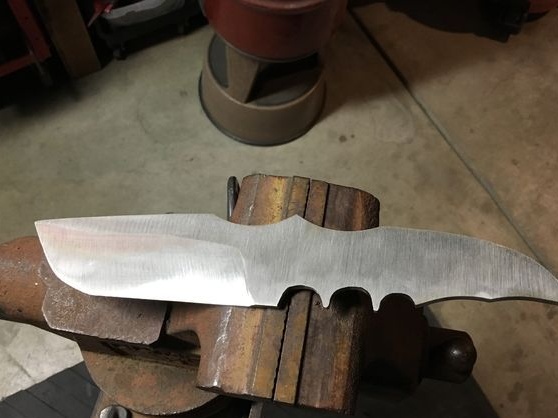
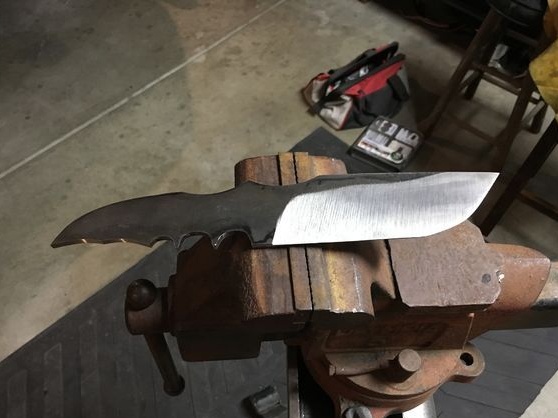
Step Three We temper steel
It is necessary to harden the knife in any case, unless it is decorative. So they can even cut the wire without fear that there will be a dent on the blade. For hardening you will need a furnace, and in a pinch, a good bonfire.The workpiece must be heated to a bright orange color, and then cooled in vegetable oil. The author does two-stage hardening, at first only the cutting edge is lowered, and then the entire knife is lowered into the oil. As a result, the blade turns out to be brittle, but strong, and the knife itself has a small plastic, which does not allow it to break under heavy physical exertion.
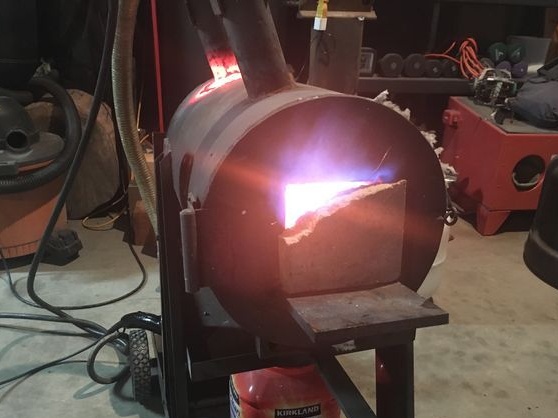
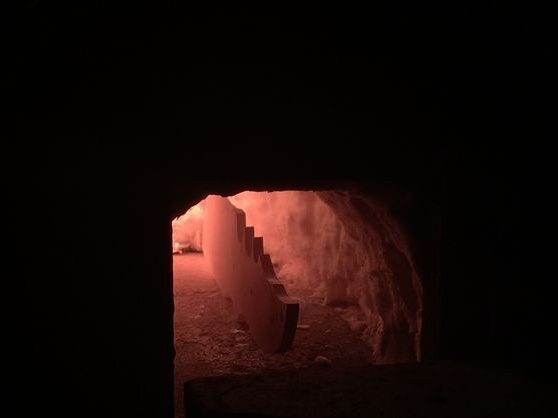
Step Four And again we grind
Now the knife needs to be processed again on a grinding machine, since after hardening the metal will probably darken. In addition to this, now you need to set the final profile of the blade. Here you need to be very careful, as the knife will become sharp and you can easily get hurt, as the author did. When working, you need to use good thick gloves.
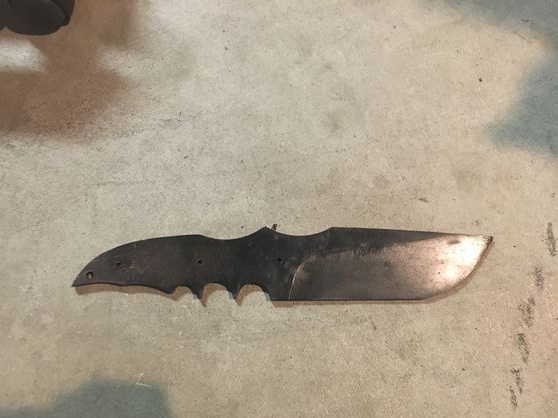
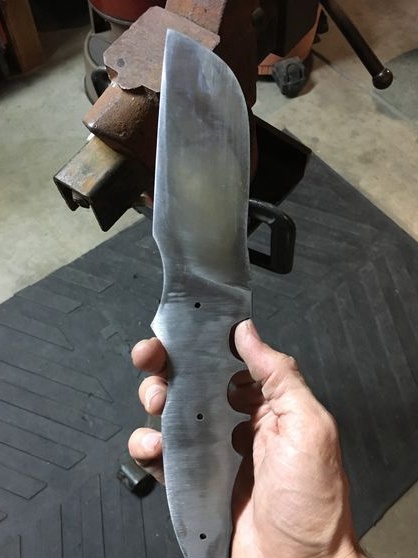

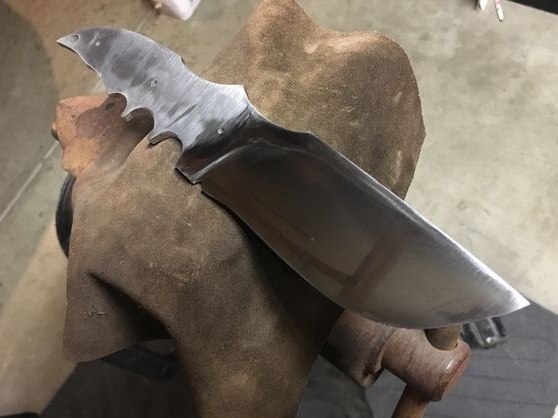
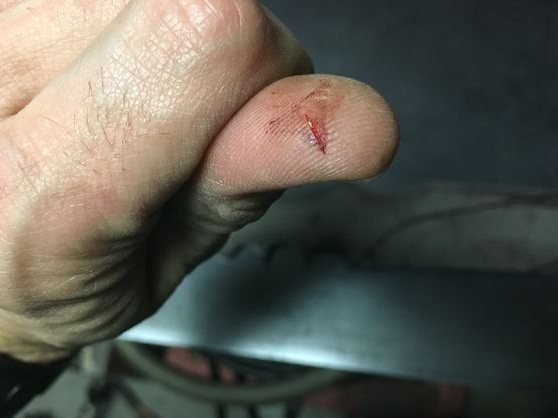
Step Five Sandblasting
Since the author decided to make the surface of the knife matte, the workpiece was placed in a sandblasting machine. This procedure is best carried out in an appropriate cabinet, so there will be less dirt. The result is such a blank as shown in the photo.
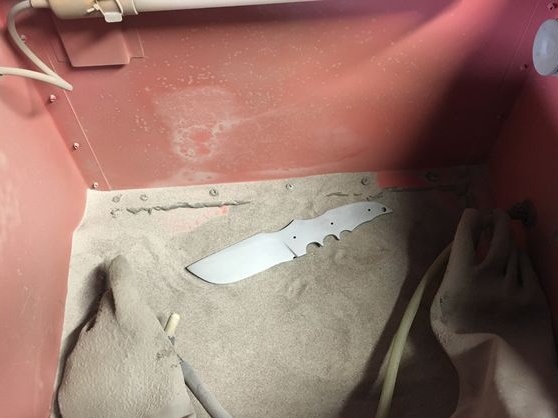
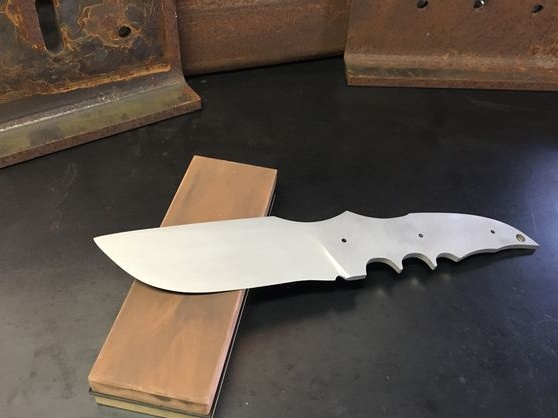
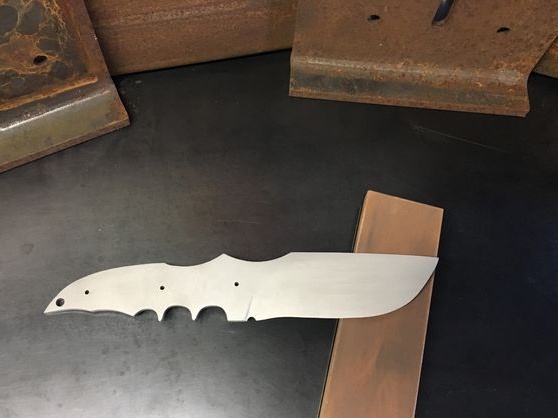
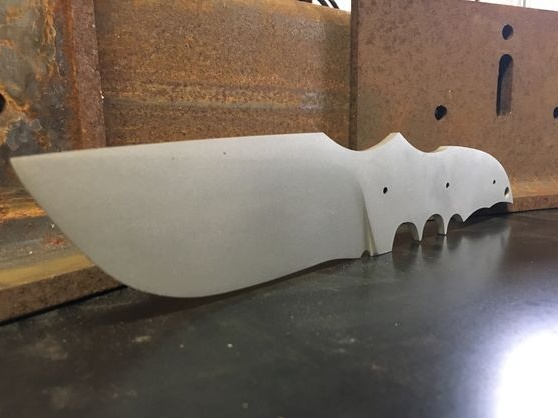
Step Six Start making a pen
The creation of the pen in this article is given special attention. Linen mycarta was chosen as the material for production. This material consists of several layers and is very durable.
The knife must be attached to the material and circled with a sharp object. Then you need to cut two halves in size a little more than the profile of the knife.
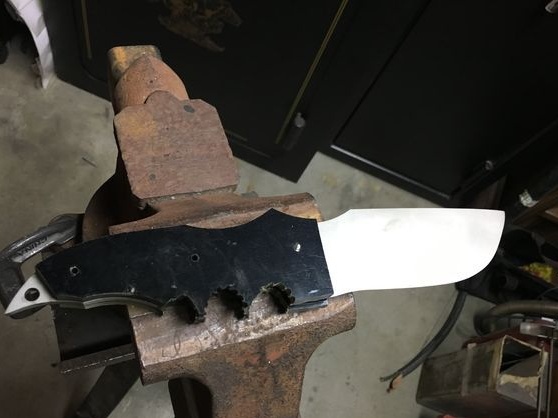
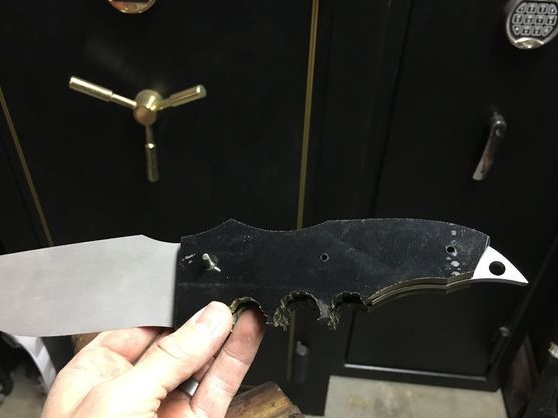
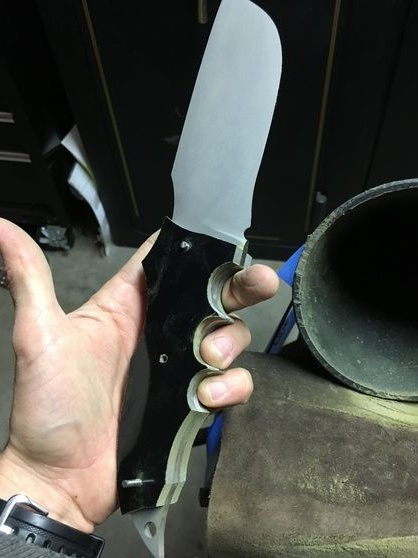
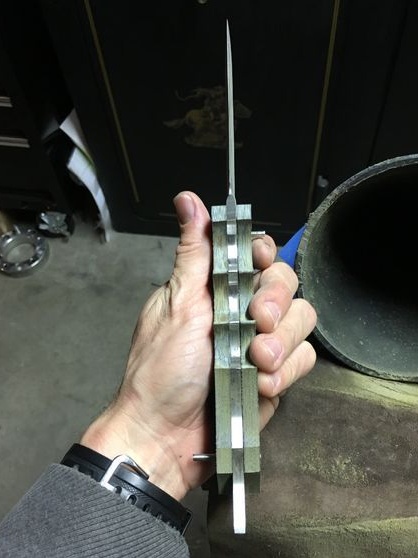
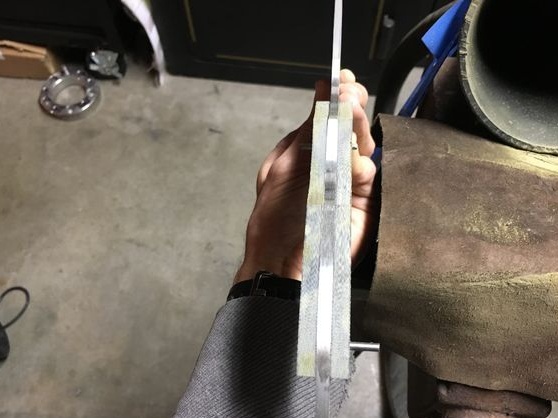
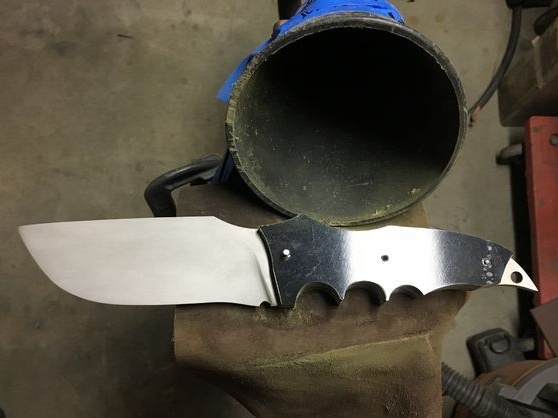
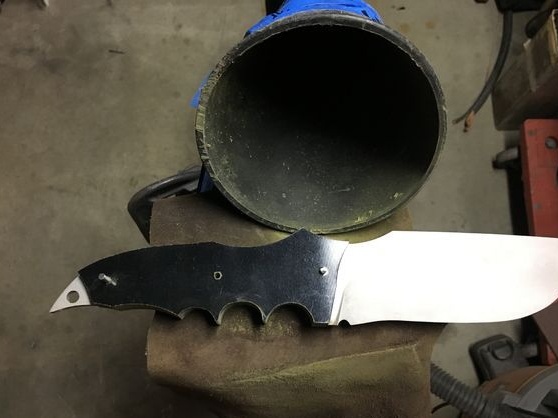
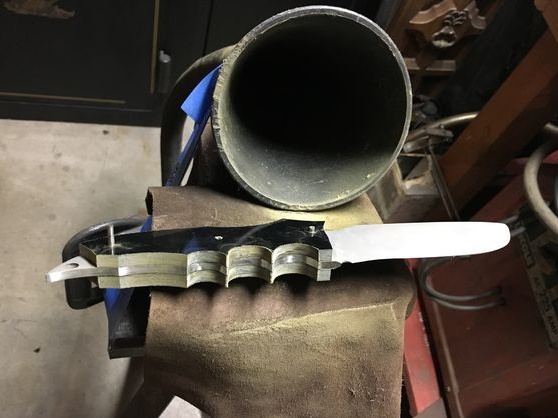
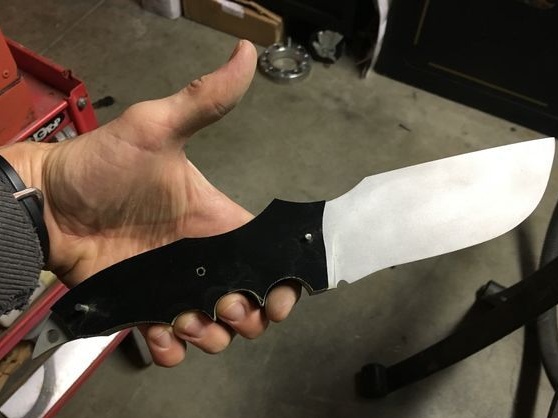
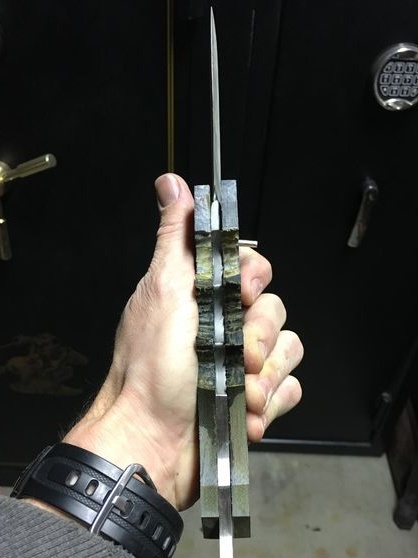
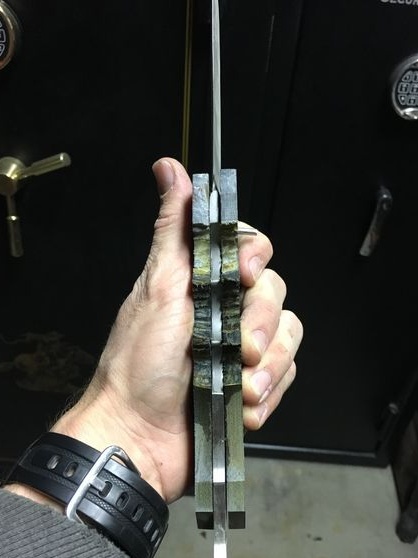
To assemble the handle through it and the knife, you need to drill holes, then pins are inserted into these holes. They must enter freely, without much effort. Well, now we need again our belt sander, with it you need to make the handle profile with one whole knife profile.
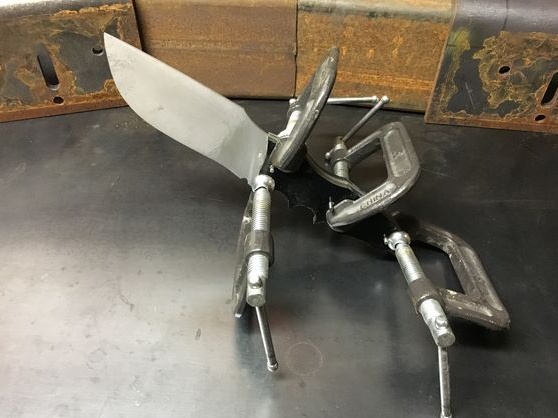
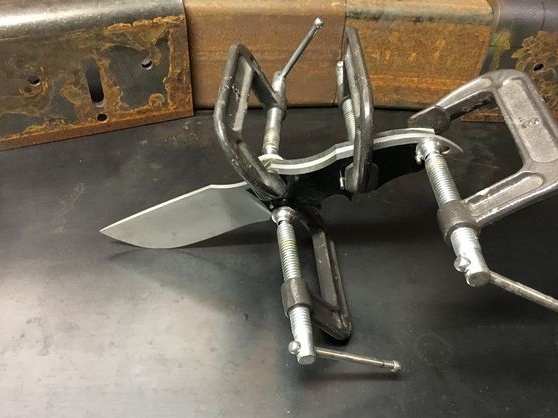
At the end, the handle can be assembled, this is done with epoxy glue. Both halves are lubricated, clamped in a vice and left until the glue is completely dry.
Seventh step. Finalization of the handle
After the glue has completely dried, it will be necessary to return to the grinder again. Now you can remove the remains of dried glue, as well as set the final profile for the pen. The author chose a form that would be convenient for him, fingers rest comfortably in such a handle, and the knife lies securely in his hand.
Also at this stage you can achieve the need for the thickness of the handle, not forgetting about the weight balance.
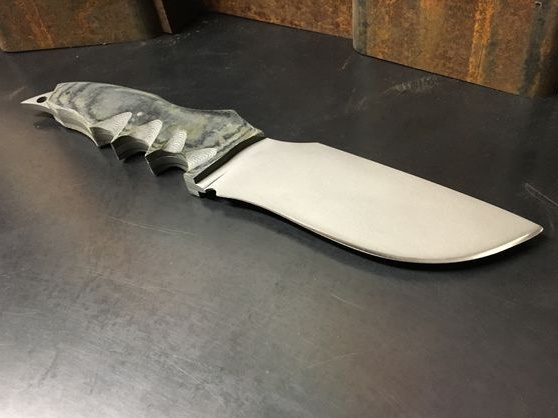
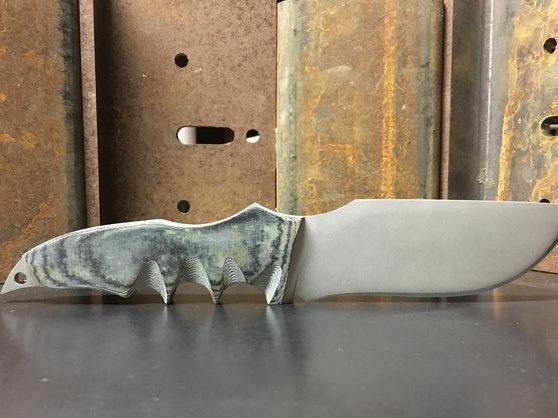
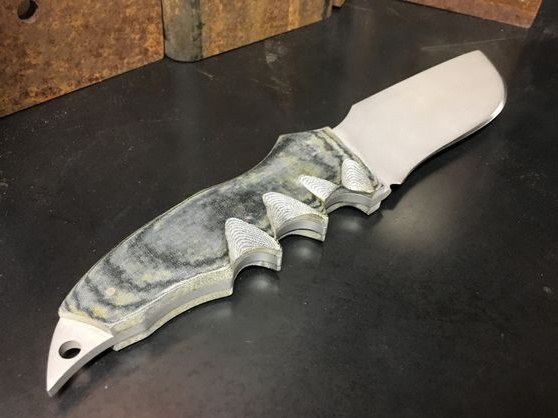
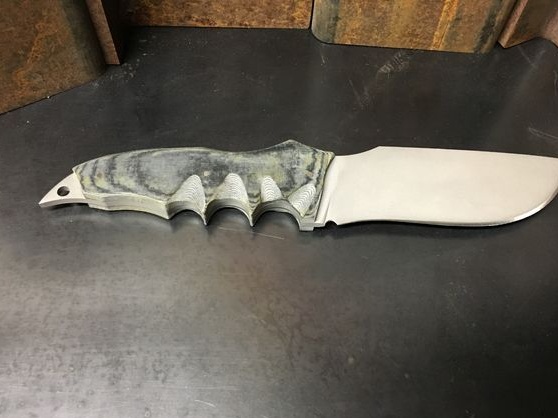
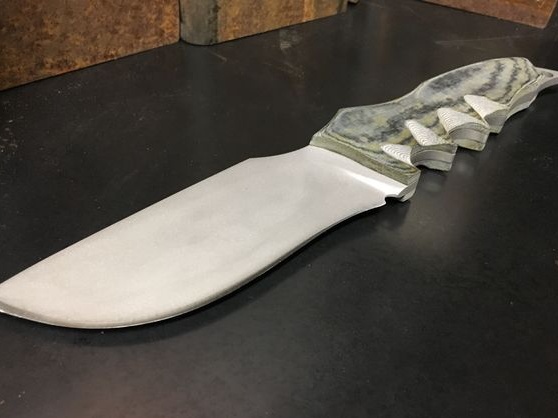
Step Eight. The knife can be tested!
To test the knife, the author took a thick piece of rope and without holding its edge, cut off a piece without problems. If the blade of the knife was too thick, then the knife would not cope with such a task. Also in this moment the key role is played by the weight of the knife and the shape of the blade.
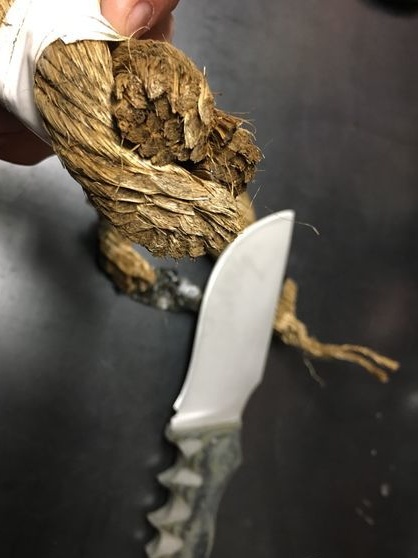
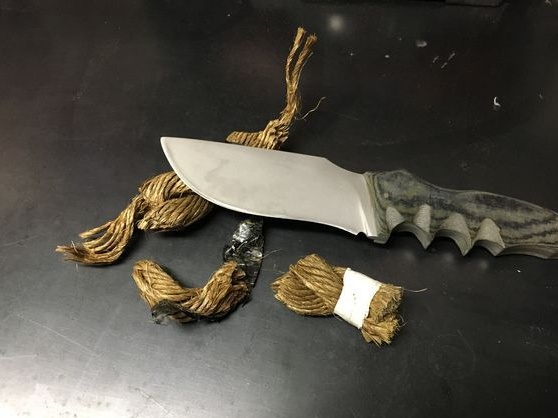
Step Nine. Final stage
The author has a laser engraver, so with his help he brings a key touch to his knife. The logo emphasizes the uniqueness of the knife. In addition, each artist must leave a painting on his painting.
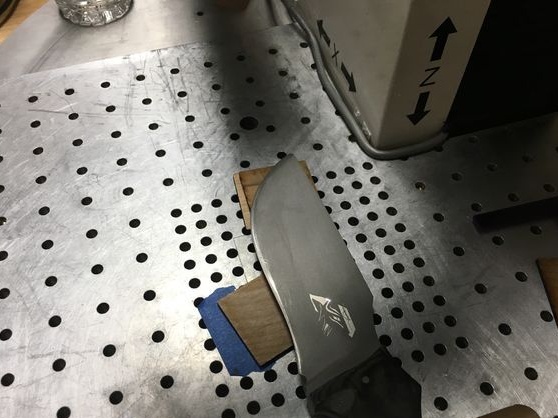
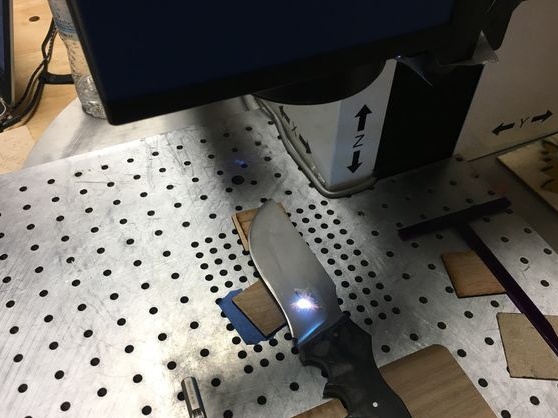
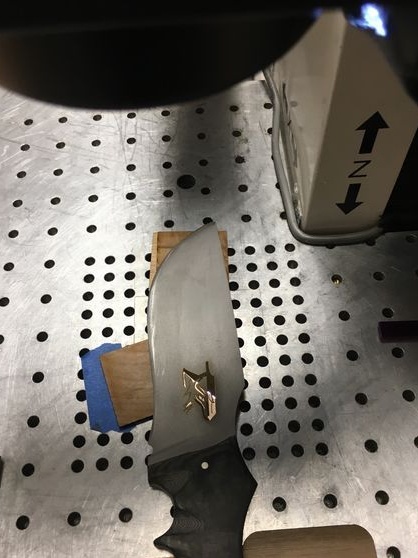
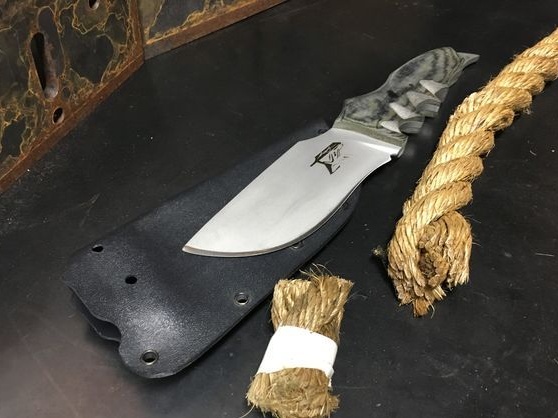
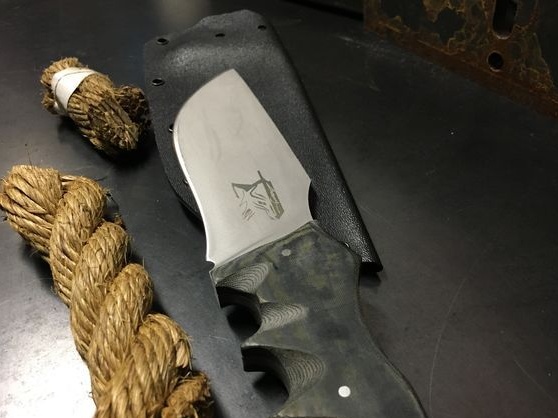
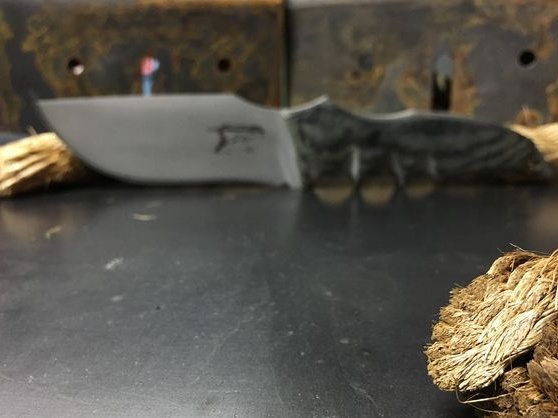
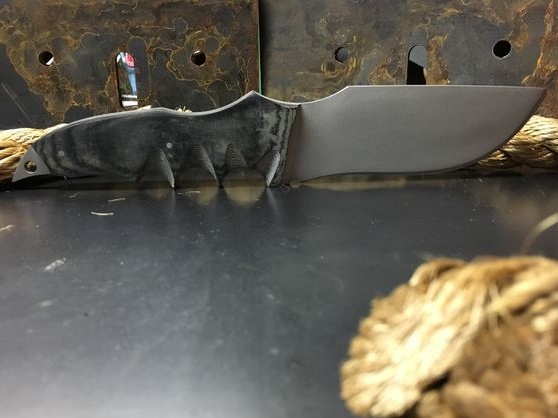
That's all, the knife is ready as a valuable, original gift. She also needs to be sheathed, as he is very sharp. Unfortunately, the author did not show us the sheath manufacturing process.