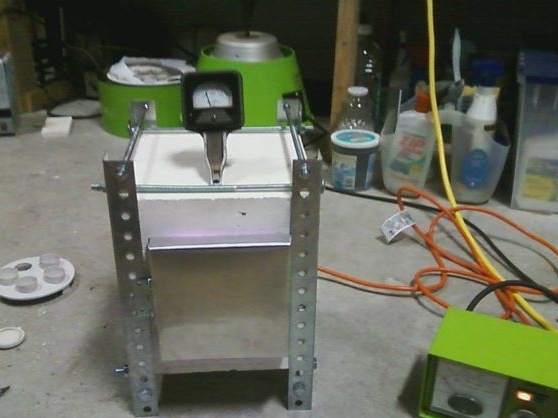
If you have a need for annealing metals, creating ceramics, smelting non-ferrous and precious metals, you can build yourself such a simple furnace. Most of these stoves cost a lot of money, according to the author, in his region the prices are around $ 600-12,000 per stove. In our case, the furnace cost only $ 120, not counting the temperature controller. This small oven can produce temperatures around 1100oC.
Going to homemade simply, all parts are not expensive, and they can also be quickly replaced if the furnace malfunctions.
Some craftsmen manage to make wedding rings in such furnaces, earrings, various talismans, brass knuckles and much more.
Materials and tools for homemade:
Materials:
- bolts and nuts (8x10, 1/4 inch);
- seven refractory bricks (they must be soft, since they will need to be grooved, dimensions 4 1/2 "x 9" x 2 1/2 ");
- a corner to create a frame;
- a square sheet of metal for the door (the author used aluminum);
- a heating element (you can buy ready-made spirals for the furnace, or wrap your own nichrome)
- heat resistant contact screws for attaching the spiral;
- a piece of good cable (must withstand at least 10A).
From the tools:
- a hand drill with a suitable nozzle for cutting grooves in a brick;
- wrench;
- pliers;
- a hacksaw;
- drill;
- nippers and more.
The process of making a homemade furnace:
Step one. Make the grooves
First you need to determine how wide the spiral is, depending on this, the depth and width of future grooves in the bricks is determined. Next, you need to draw them on the brick with a pencil. The author’s grooves have a shape in the form of the letter “U”, all grooves of this shape are two pieces, that is, they are cut on two bricks. On that brick, which will be located in the back of the furnace, you need to make two parallel grooves as in the photo. As a result, after the assembly of the furnace, the spiral will receive approximately a "P" -shaped shape.
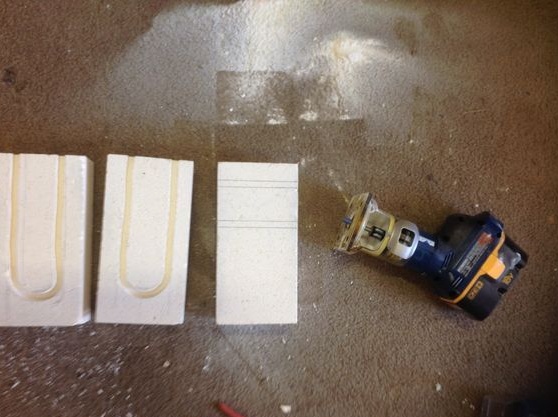
Step Two Installation of a heating element
Before installing the heating element, you need to collect the bricks, having decided on the dimensions of the furnace. Most likely, the bricks that go to the floor of the furnace will have to be cut, since two such bricks will form too large a bottom. You can cut them off with a grinder with a disk for concrete, well, or even with an ordinary cutting disc.
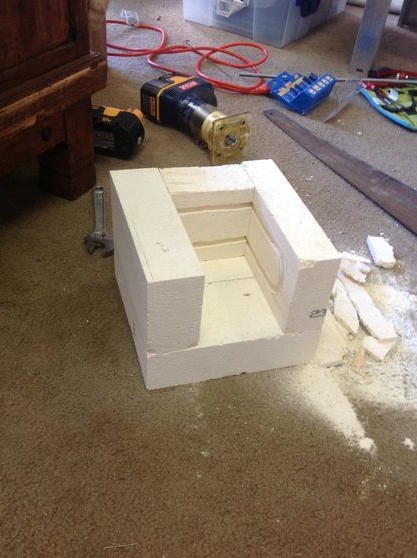
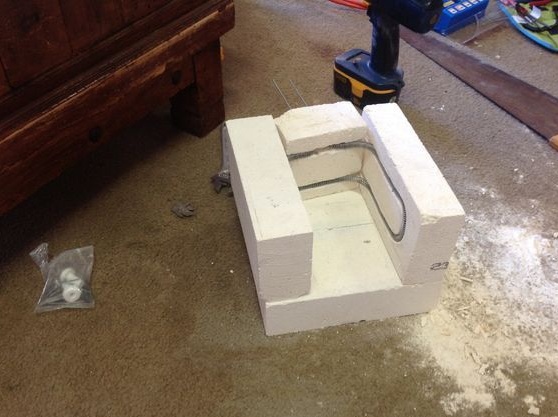
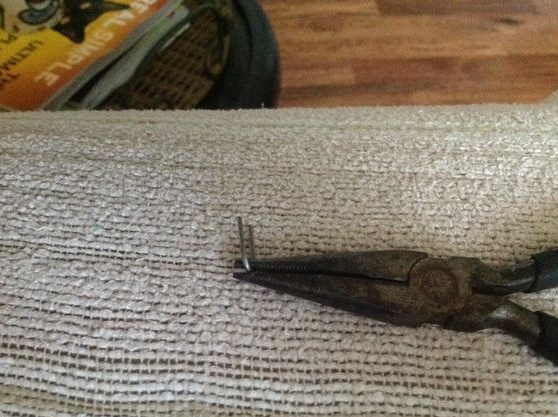
Well, then you can install the spiral.Most likely, it must first be stretched to the desired length. If you will wind the spiral yourself, then you need to calculate how long and thickness the wire should be, there is a ton of information on the Internet for this.
Well, then you can lay the oven in the groove. To fix the spiral, the author uses metal brackets, under which holes will need to be made in the brick. Particular attention should be paid to connecting the spiral to the wire. Special screws with ceramic washers should be used here, and the screws must be taken more authentically. Otherwise, the insulation of the wire will either constantly burn and stink, or it will constantly burn due to high temperature.
Our people learned to make such contacts from old car candles when ancient electric stoves with an open spiral were used.
Particular attention should be paid to the choice of material from which the spiral is made. The maximum temperature that the furnace can give out will depend on this. The spiral must withstand high temperature loads. For such purposes, the author chose a wire of the NiCr type. Most of these wires are designed for temperatures of about 1340aboutC. If you require higher temperatures, you can choose other types of wires that are suitable for this.
Step Three Making the stove frame
To create a frame you will need a corner, you can use steel or aluminum. Four pieces of aluminum form the legs, and two more go to the bottom and support the weight of all the bricks. You can use not two corners, but four to create the lower support. However, this is not necessary, as a result, the design is still pulled together with bolts and nuts, these bolts hold the bricks below.
Two or one and a half bricks will need to be laid in the upper part of the furnace, as well as below. Well, how everything is going, you can see in detail in the photo.
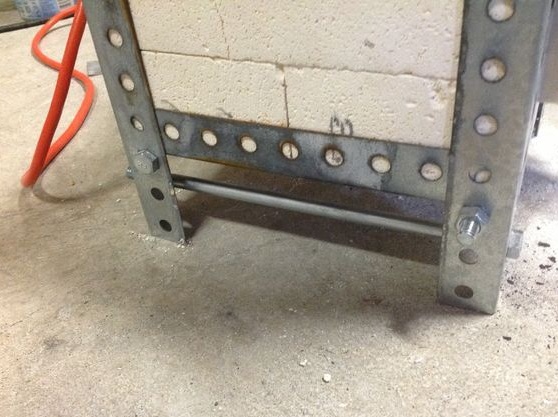
Step Four Make the door
To create the door you will need a sheet of metal, the author used aluminum. First, you need to draw a square or quadrangle on the sheet, depending on the size and shape of the door. Next, this square must still be circled in a circle, stepping back you need a distance for fixing the refractory material. Well, then cut the pieces at the corners, as seen in the photo.
As a refractory material auto used a Kaowool stove. It must be cut to the size of the previously drawn square. Well, then the plate is laid on the sheet, and the remaining edges of the sheet are bent, thereby holding the plate.
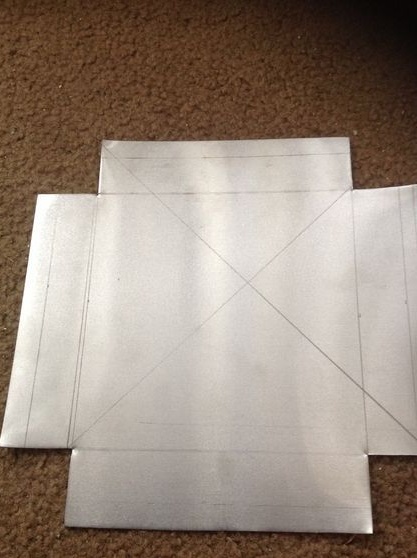
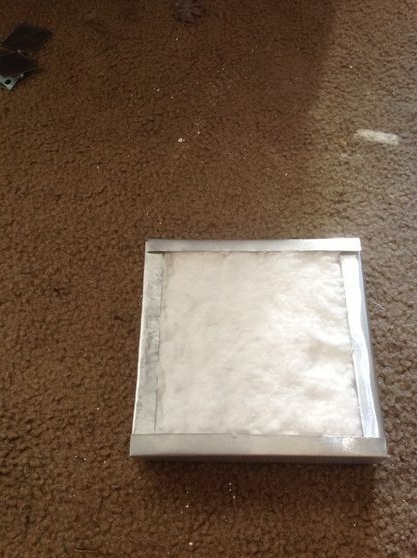
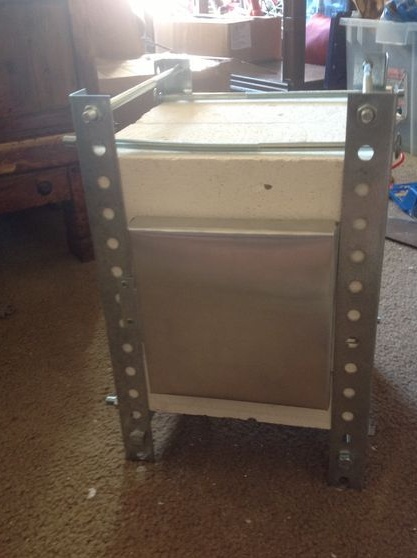
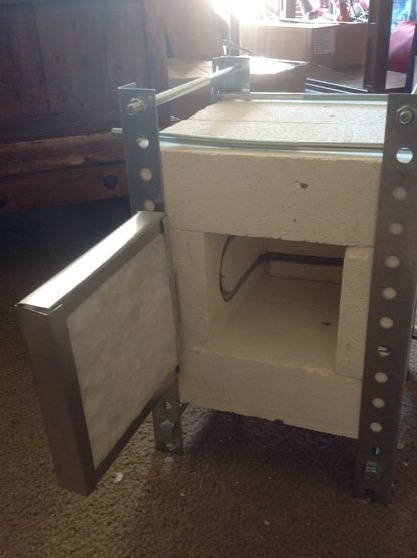
That's all, now the door needs to be hinged with screws and nuts to the furnace, having drilled a couple of holes. As an insulating material, you can use other accessories. The latch for the door can be done, but not.
Step Five We supply electricity
To connect the spiral, you need to use a good wire with a thick core, which can withstand at least 10A. Among other things, the furnace is connected through a regulator, it will help maintain the temperature in a given state. You will also need a furnace thermometer, according to which it will be possible to more accurately monitor the temperature in the furnace.
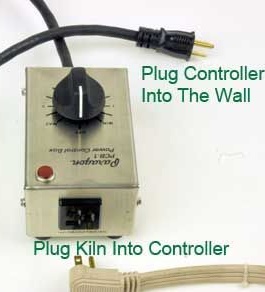
It is important to remember that such a furnace consumes a lot of energy, so all wiring must be in good condition, and the machine must withstand the load that the furnace creates.
Step Six Testing the stove
Before starting, the oven must be installed away from substances and materials that can easily catch fire. It should not be included on a wooden floor or floor with linoleum. It should be brick, concrete and so on. Now the oven can be turned on and tested. It is important to remember what temperature the selected wire is designed to not overheat the spiral.
According to the author, his furnace was able to give out a temperature of 1260 degrees Celsius and showed excellent performance.