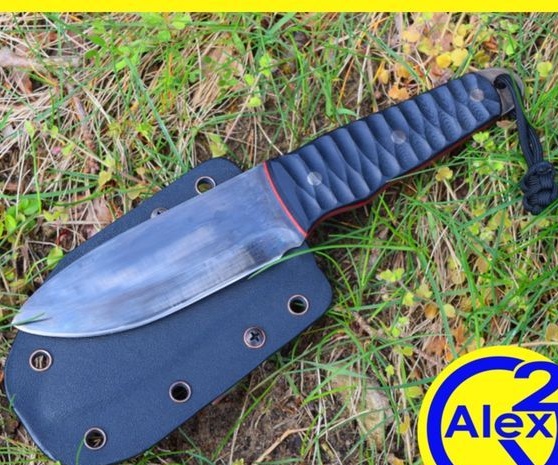
The author decided to make this knife and present it to his nephew, who turns 13 years old. So in size, it is made appropriate. But using this approach, you can effortlessly make a blade of any shape and size.
Everything is made of high-quality materials, the material for the blade is high-carbon steel, which the author specially bought for such purposes.
Materials and tools for homemade:
Materials:
- a source of high carbon steel (thickness 3.2 mm);
- inserts of red color (G10 - 1 mm x 40 mm x 250 mm);
- steel rod for pins (6 mm);
- black sheet Kydex;
- epoxy and more.
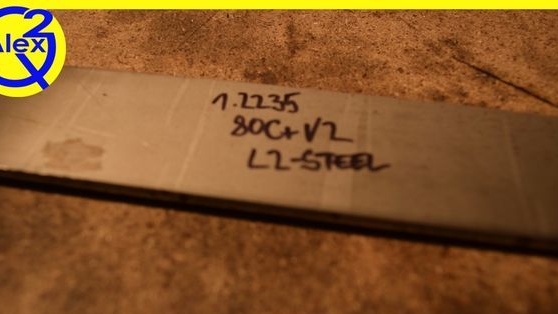
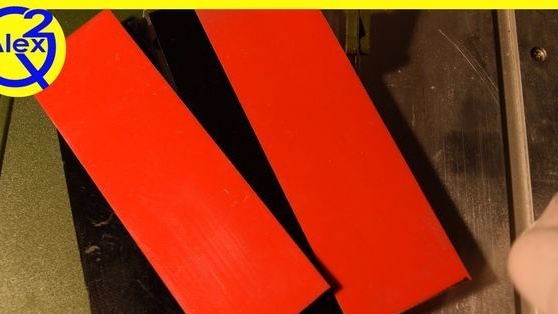
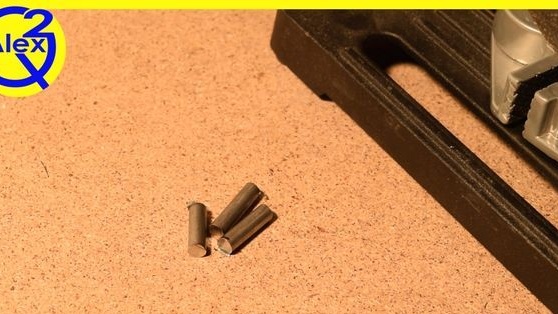
Instruments:
- a grinder with grinding and cutting discs;
- a good drill;
- belt grinding machine (or other grinding machine);
- sandpaper for the machine with grit 600, 1000, 1200, 1500, 2000;
- a propane burner or other heat source whose temperature exceeds 1200 degrees Celsius;
- refractory brick;
- linseed oil, wax.
The process of making a knife:
Step one. Design and Template
First you need to create the right knife project on paper. Well, then just cut it. Then it will be very convenient to produce a blade profile on it.
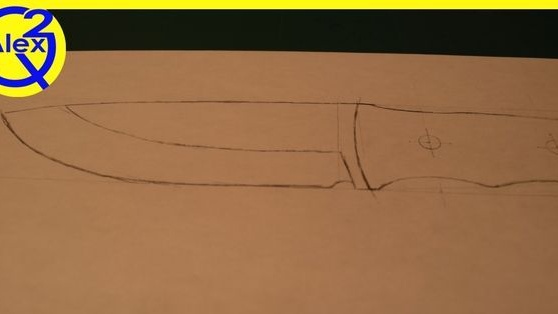
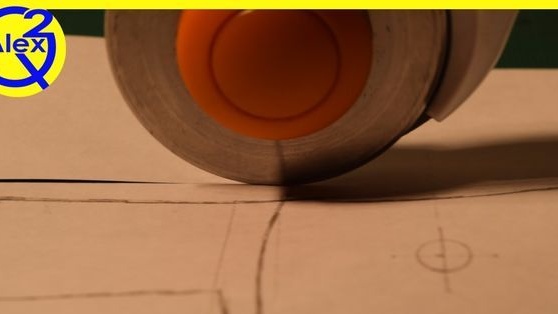
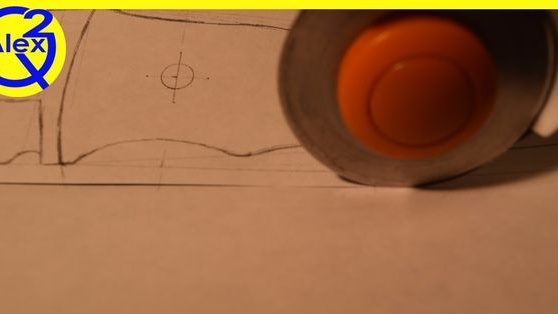
Step Two We form a blade profile
First of all, the author determines how long the workpiece is needed. Now you just need to cut off excess from it with a grinder or other tool.
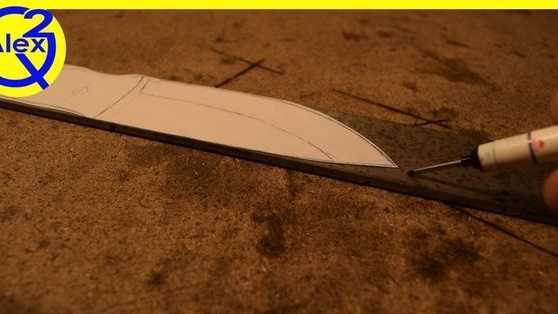

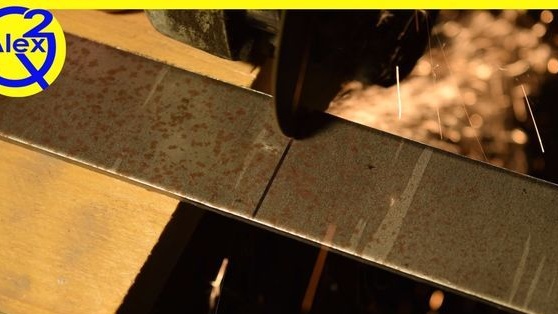
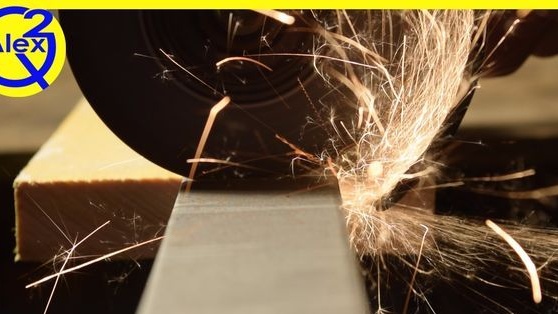
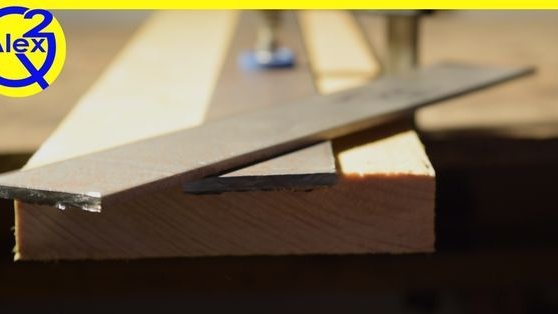
Further, it is advisable to grind the workpiece thoroughly to level it, as well as remove rust and other contaminants. Sharp edges can also be flattened for safety. For such purposes, the author used a belt sander.
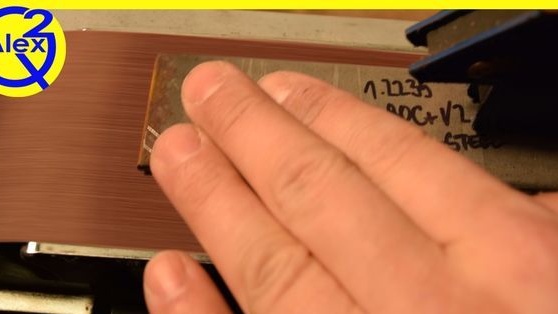
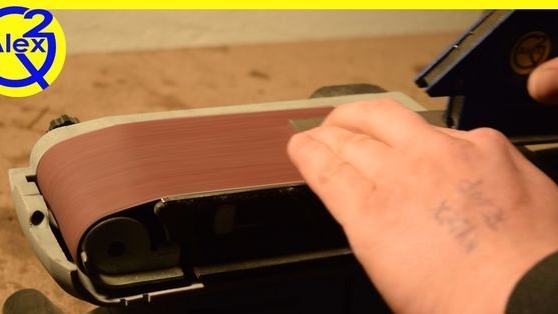
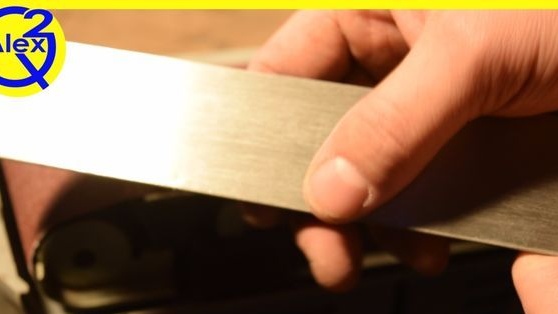
After that, a template cut from paper should be glued to the blank.
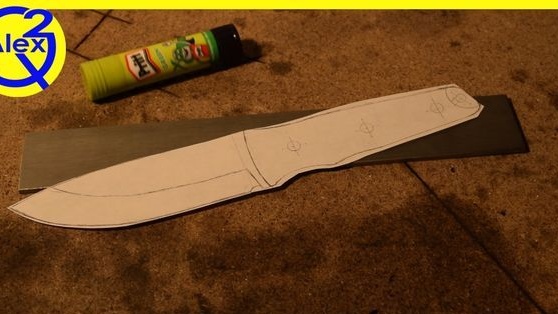
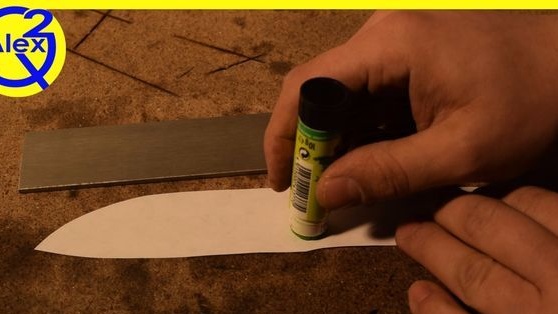
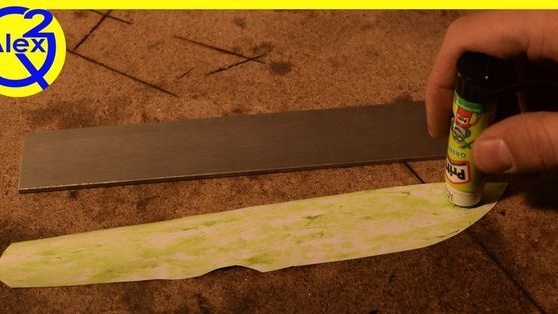
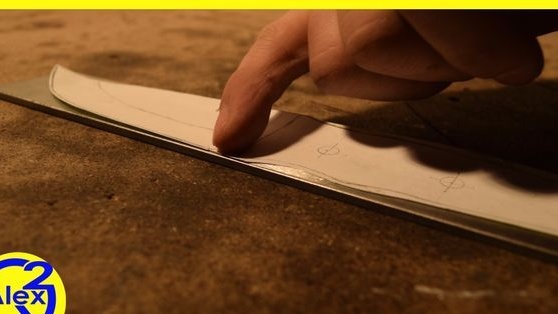
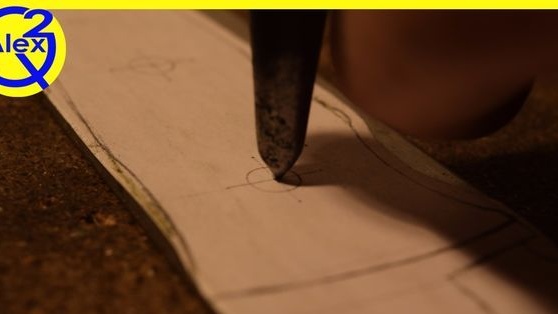
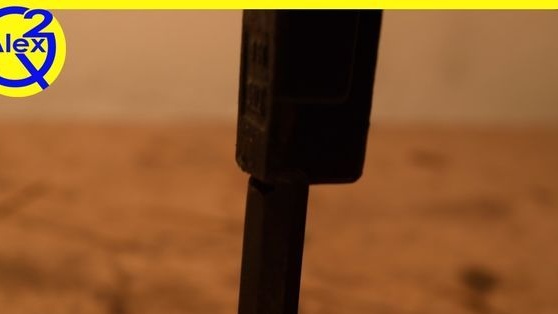
It is important not to forget to make marks on the metal where the holes will be located. They can be tilted.
Well, at the conclusion of the stage, the author forms the primary profile of the blade. Here you will need a grinder or grinder with a grinding wheel with a grit of 40.
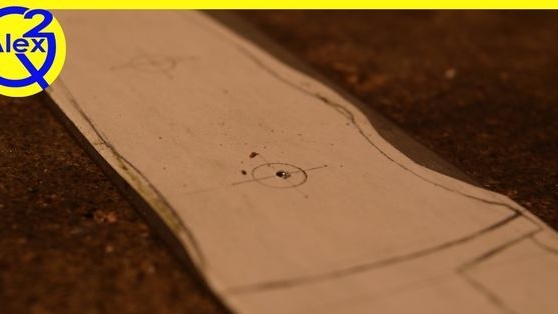
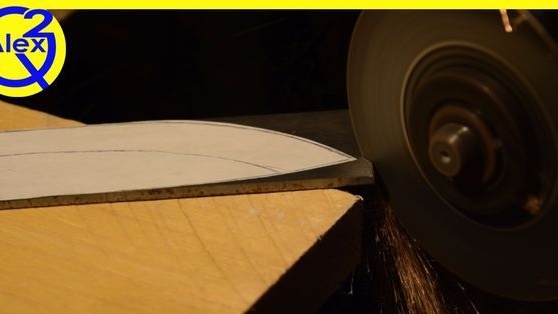
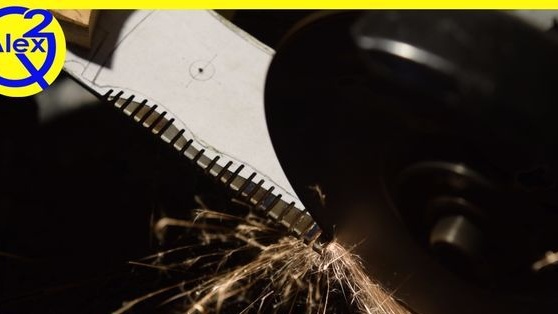
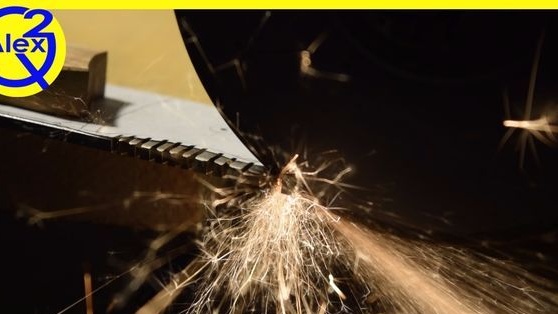
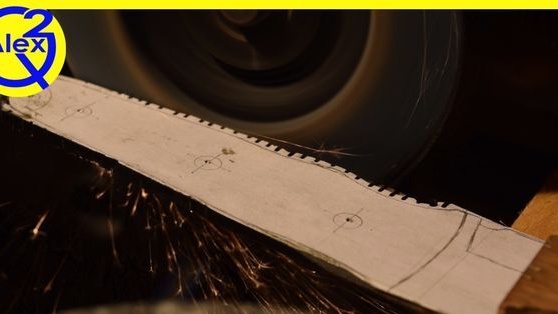
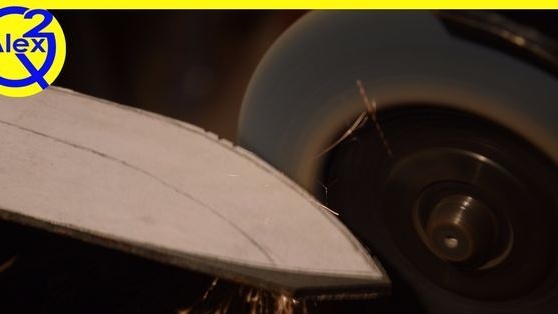
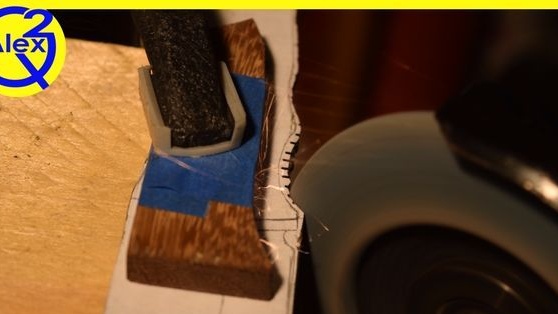
Step Three We work on a belt sander
Now the knife can be cleaned of the glued template, as well as trim the profile.
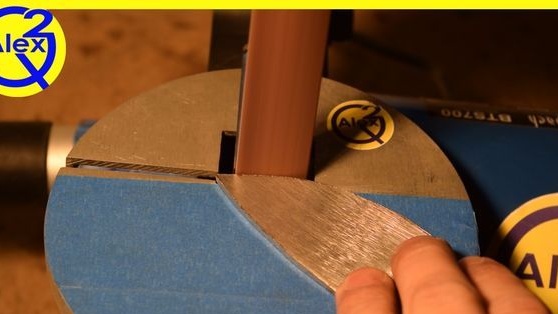
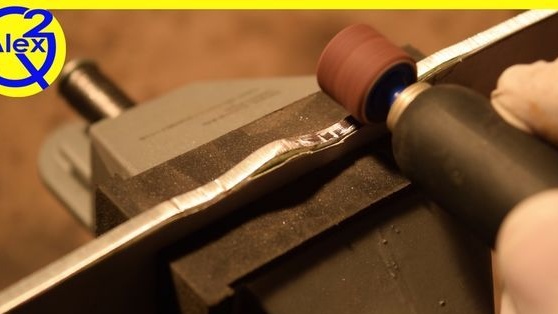
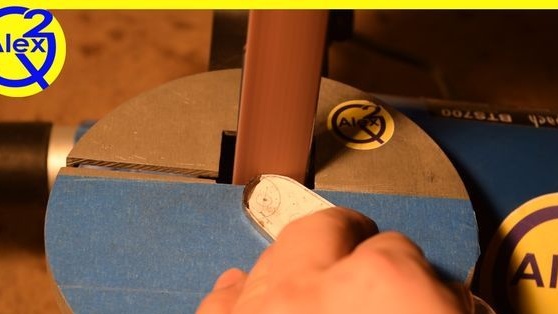
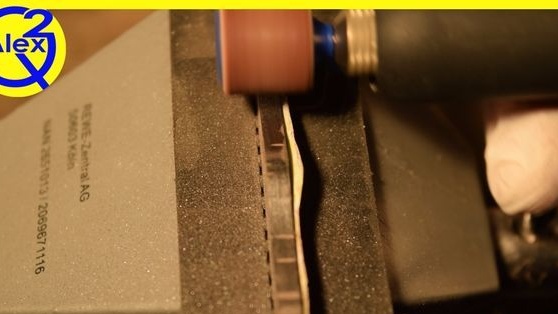
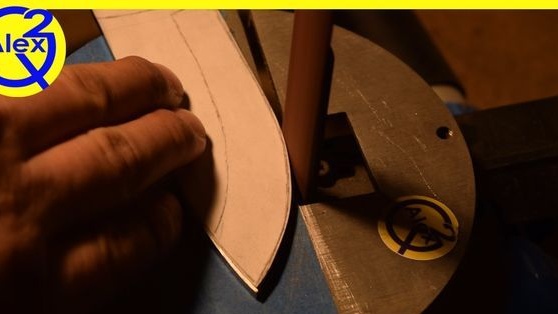
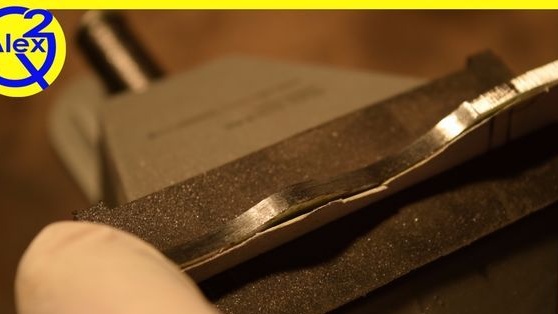
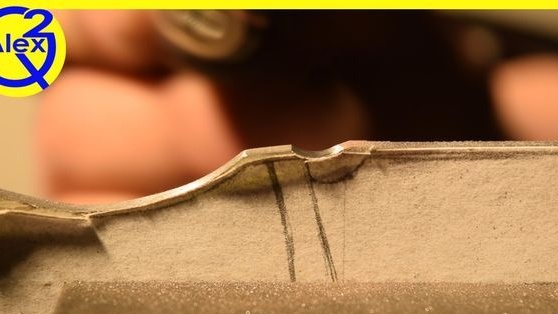
Step FourDrill holes
At this stage, the author drills holes in the workpiece. At first glance, this task seems simple, but it is sometimes not so easy to drill high carbon steel.
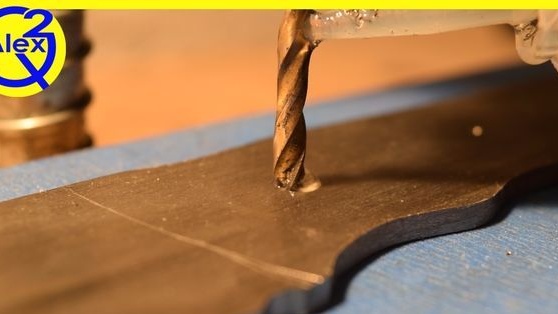
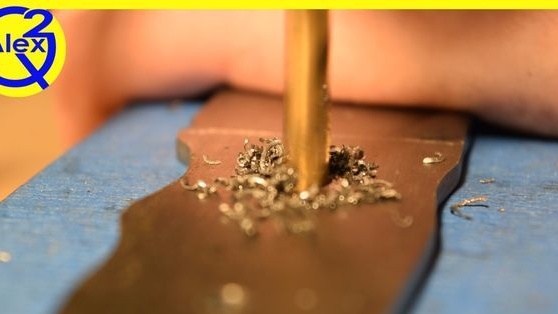
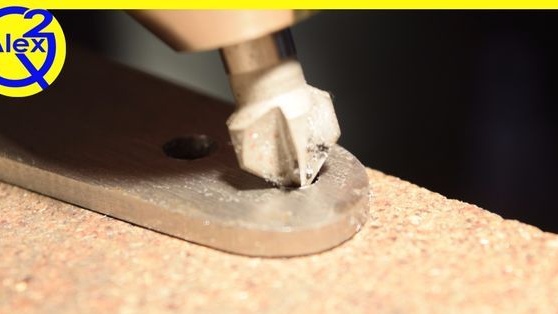
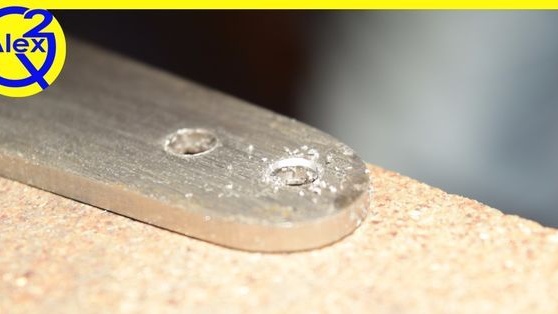
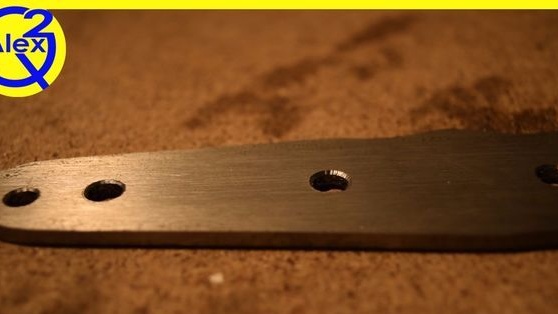
Step Five Knife bevels
The author decided to approach the manufacture of bevels with complete seriousness. First, he carefully marked everything out, determined the necessary angles, and then began to form bevels on a belt sander.
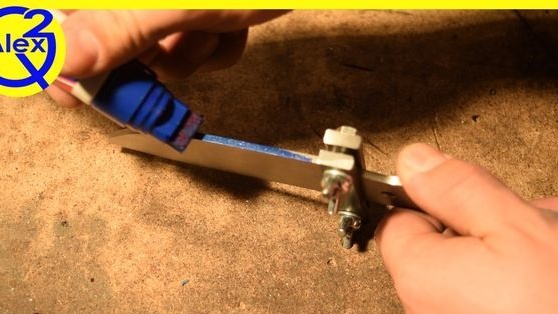
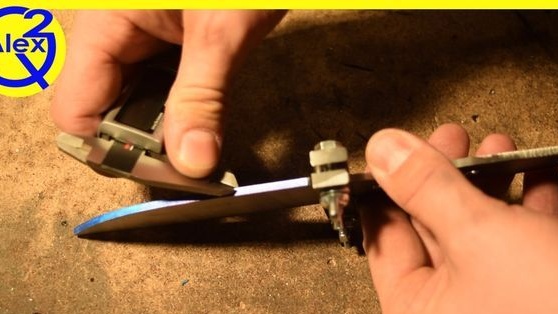
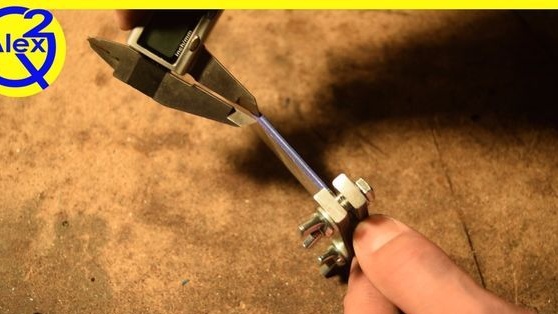
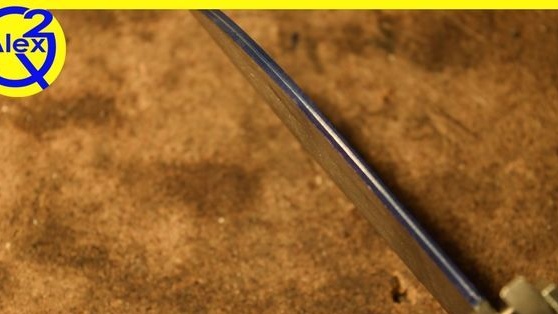
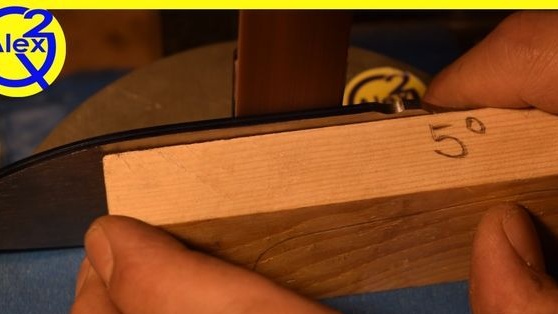
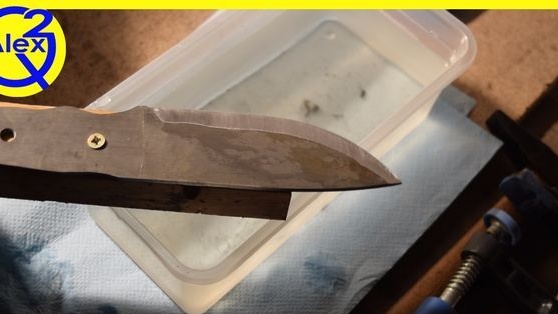
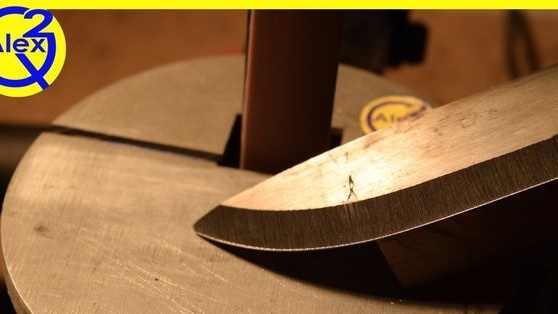
Step Six We temper the blade
Hardening is a very crucial moment in the manufacture of a knife. To harden steel with a high carbon content, it must be heated to a bright red or orange color, and then cooled in oil. The author heated his preform from 80CrV2 to a temperature of 840 ° C - 880 ° C, and then cooled it in vegetable oil.
You need to heat “from the back”, while the heat will be distributed down to a narrower part. The specified temperature must be maintained for about 5 minutes, so that the steel warms up all evenly. After lowering the oil into steel, let it cool completely.
If the blade is hardened well, it should not be taken with a file.
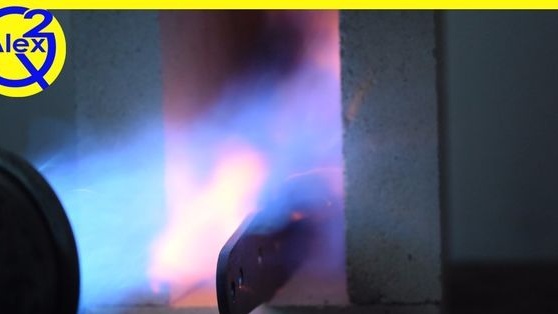
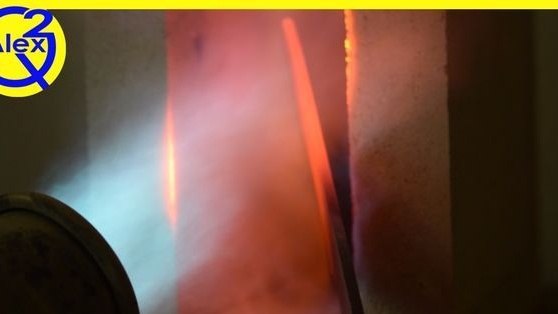
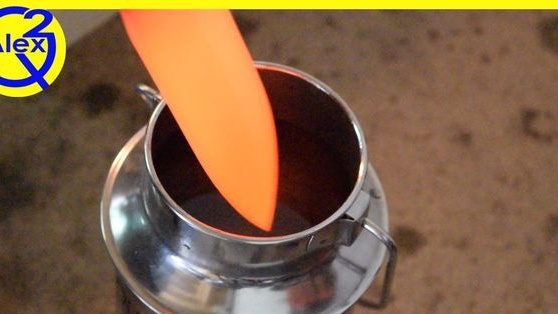
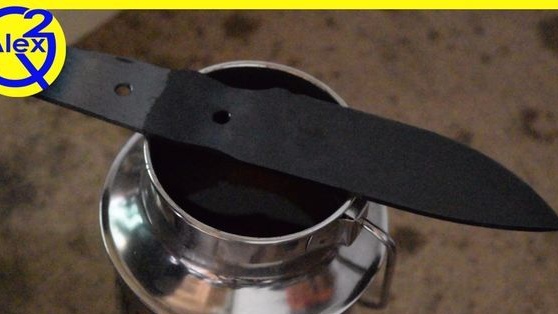
After that, the knife will need to be cleaned with sandpaper.

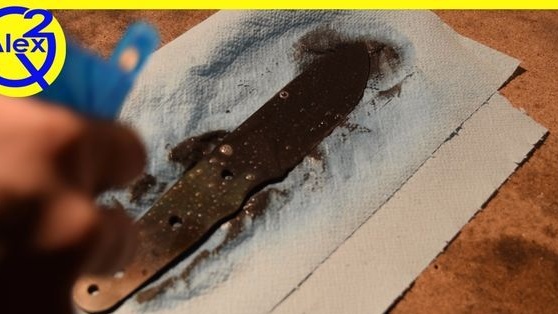
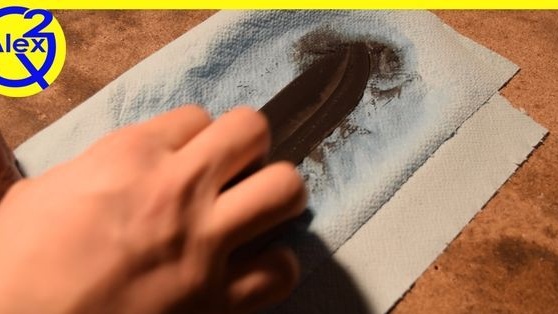
To achieve the ideal hardness of the knife, now the steel needs a little release. Here you will need an oven, in it you need to warm the knife for two hours.
Here are examples of temperature conditions depending on the type of steel:
150 ° C (302 ° F) - 63HRC
200 ° C (392 ° F) - 60HRC
250 ° C (482 ° F) - 57HRC
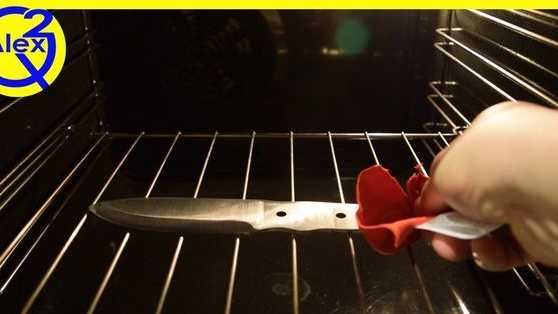
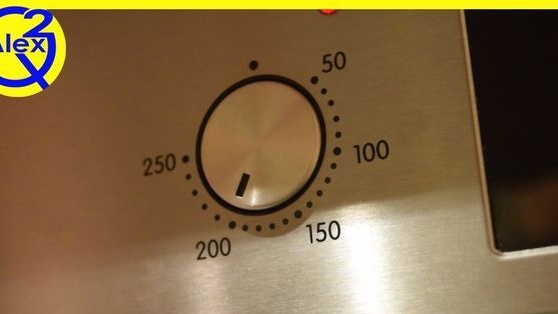
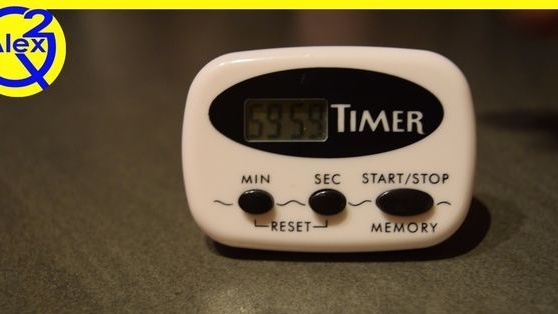
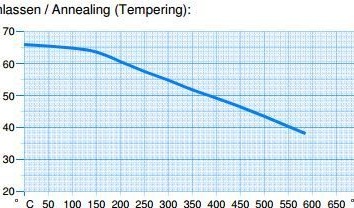
Seventh step. Pen making
To make a pen, the author decided to purchase a G10. Red and black parts were selected. This whole thing is going classically. First you need to attach the blade to the material and circle the shape. Then all the parts are pulled together, the holes for the pins are drilled and connected.
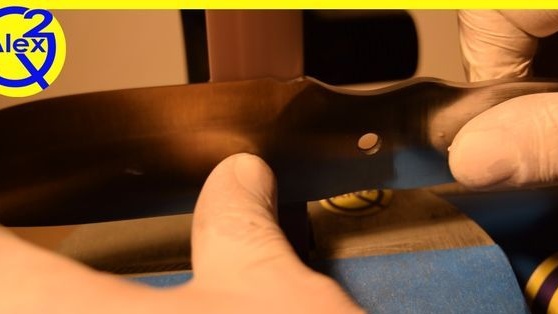
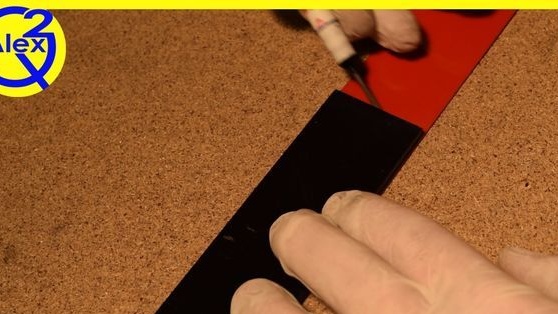
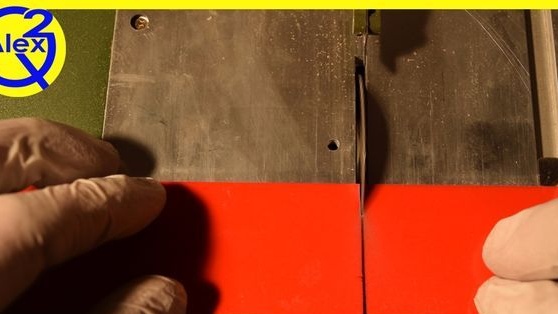
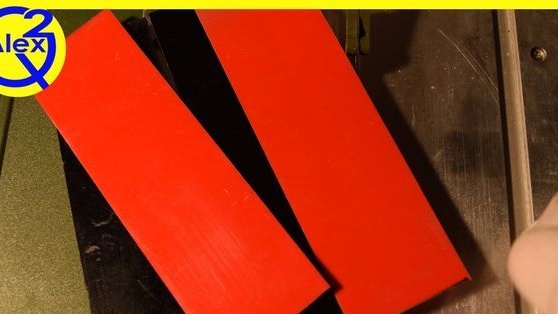
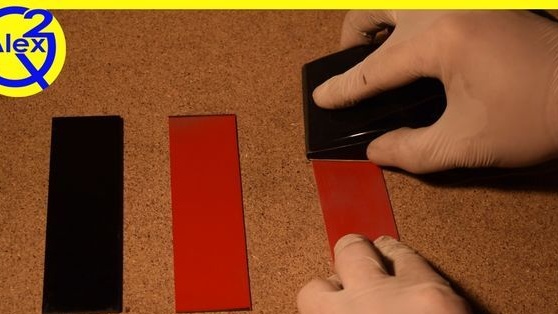
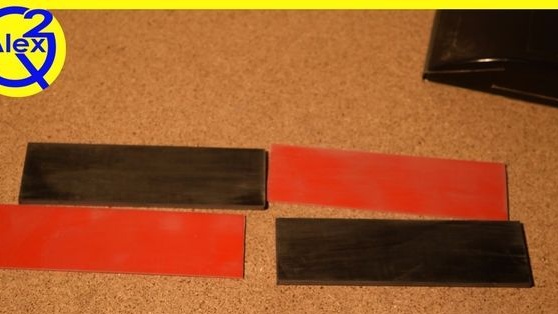
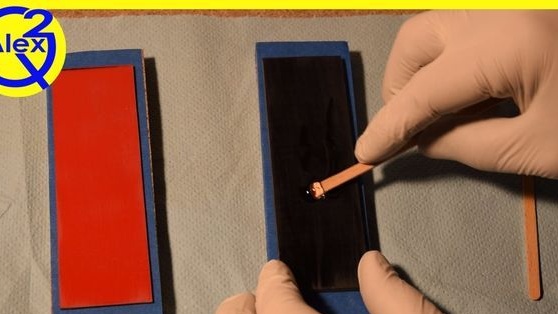
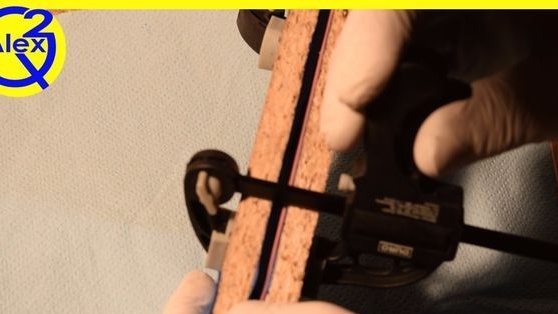
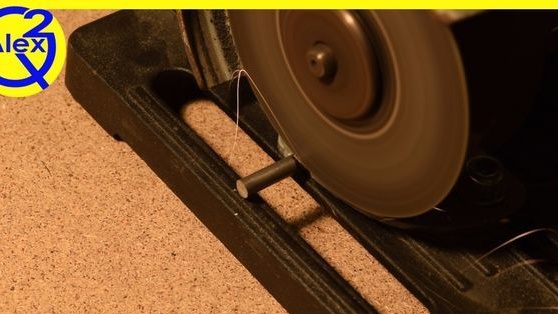
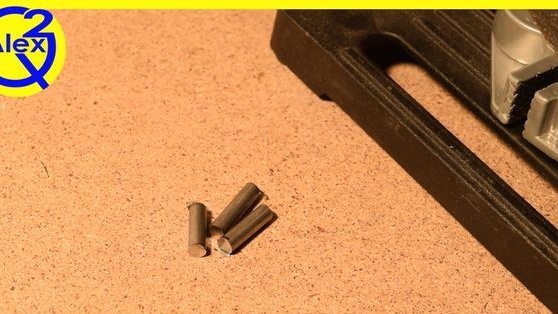
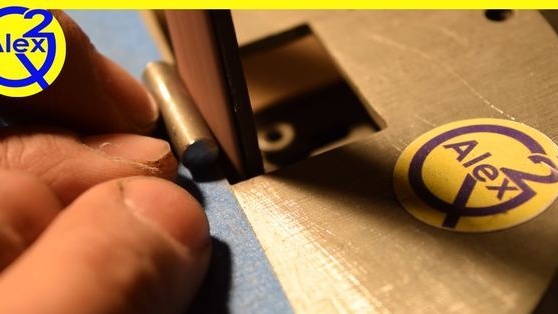
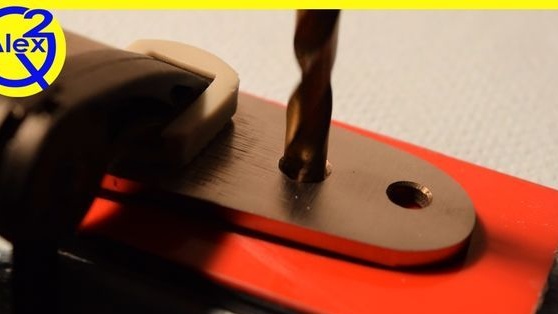
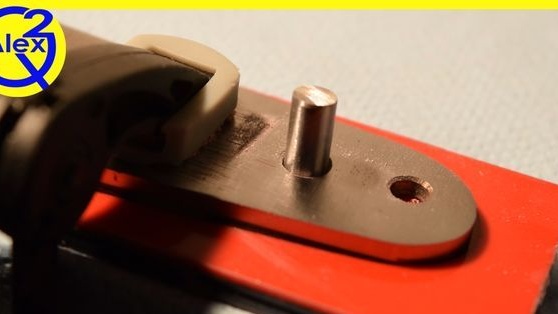
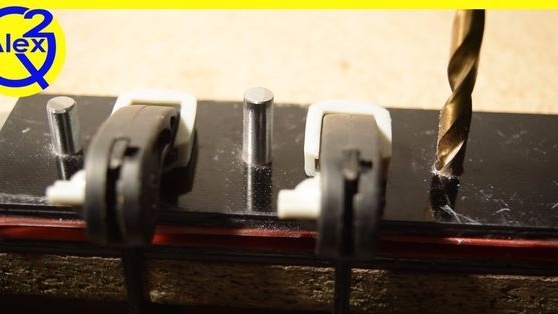
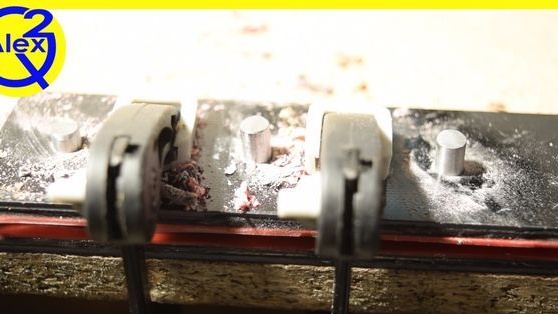
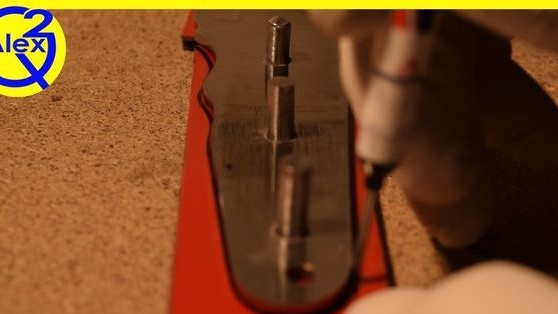
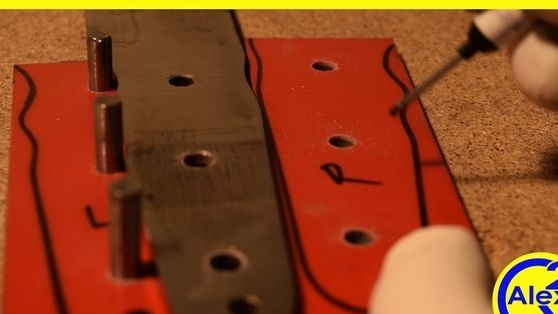
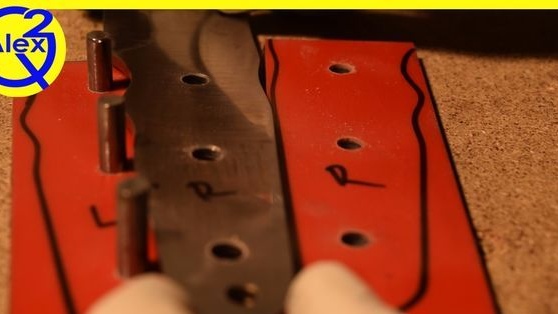
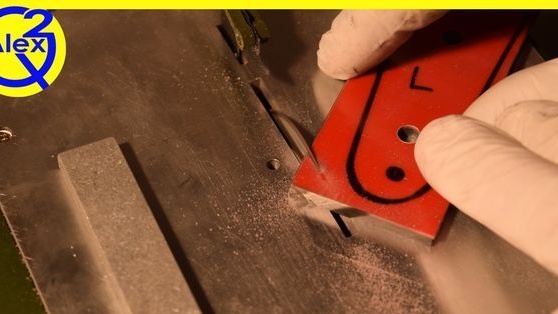
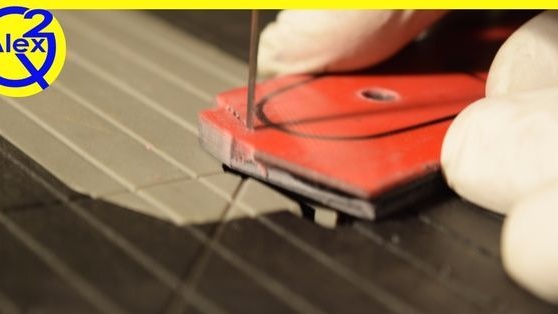
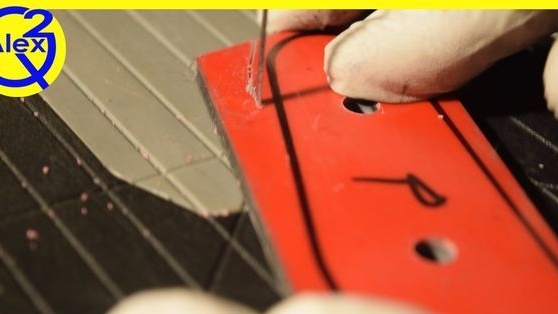
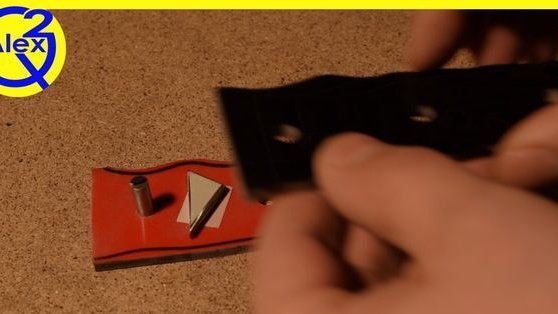
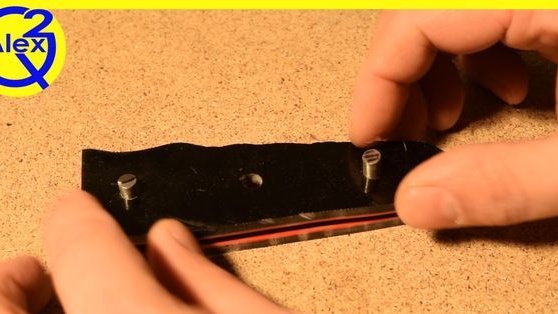
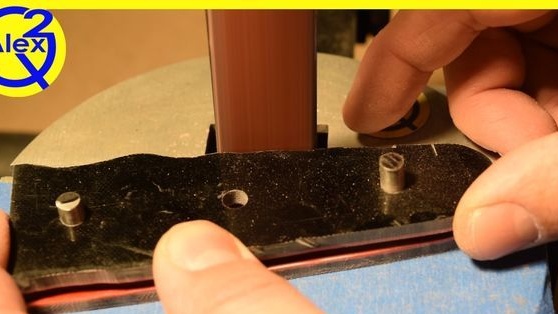
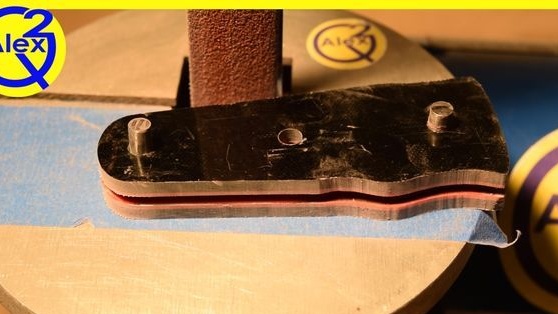
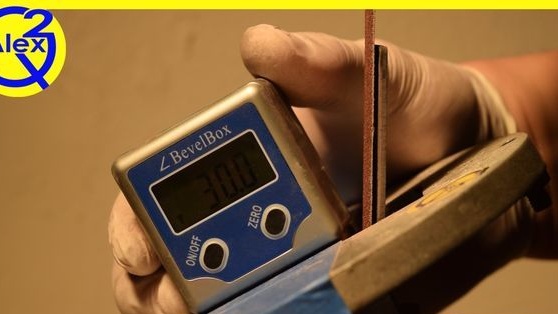
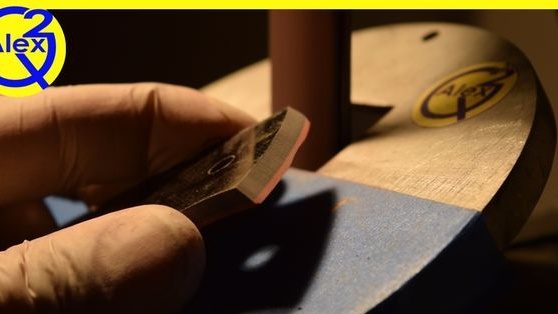
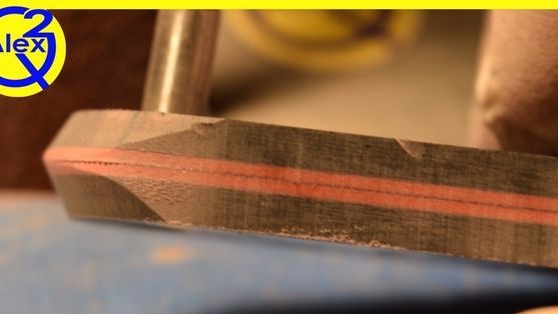
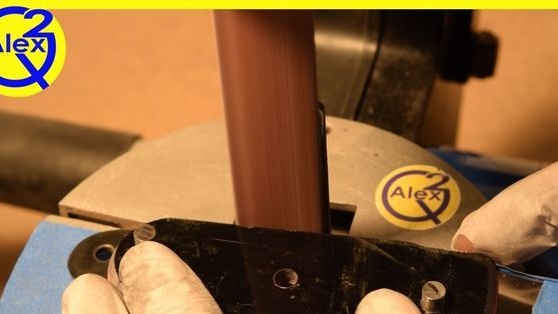
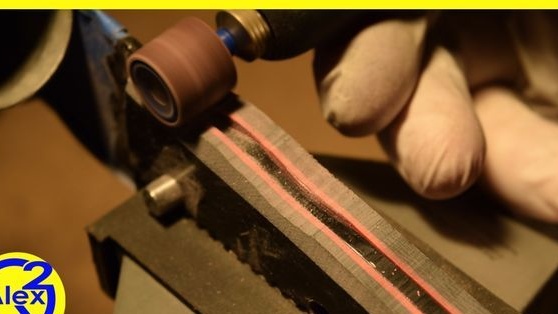
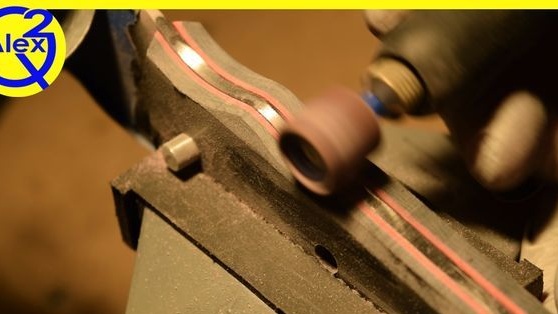
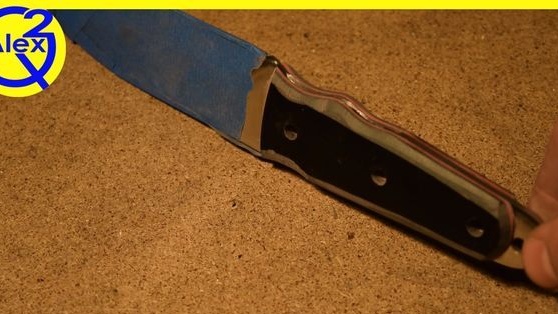
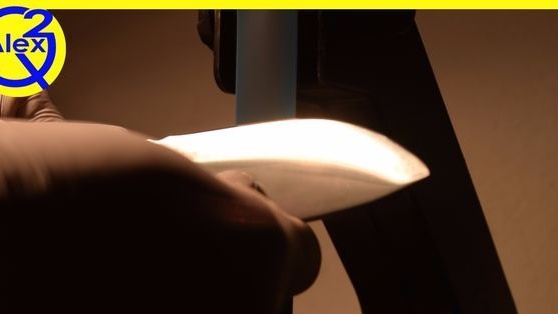
The handle is glued with an epoxy, after it hardens, the handle can be finally sanded.
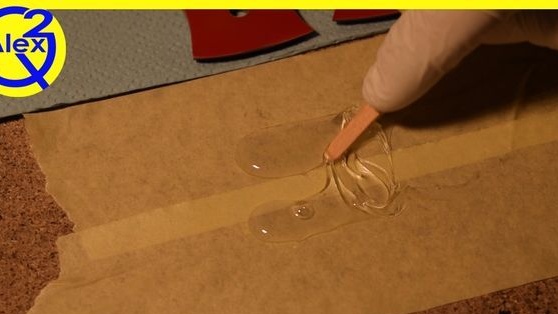

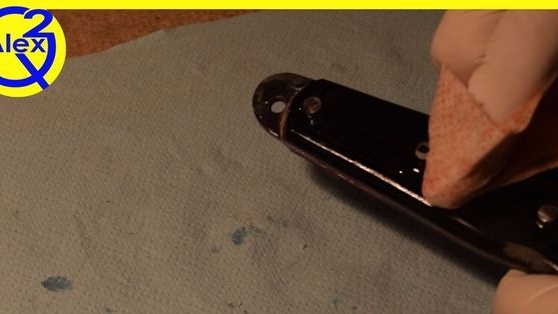
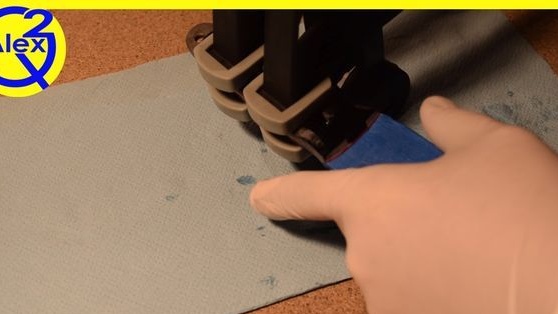
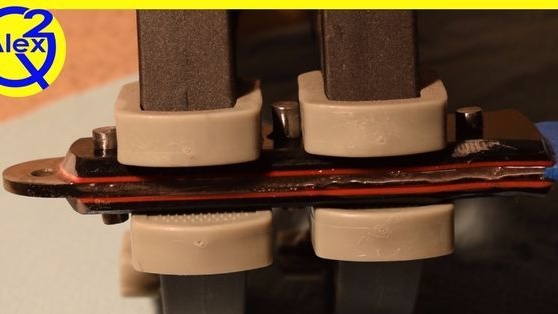
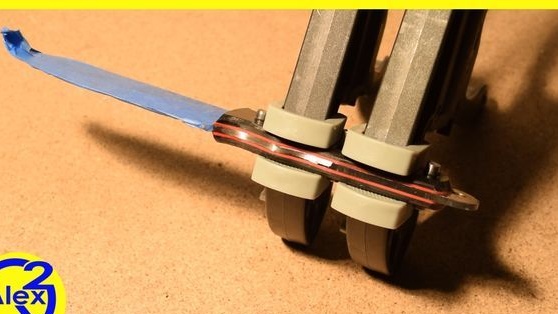
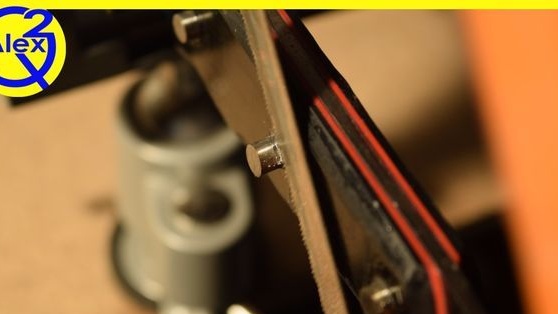
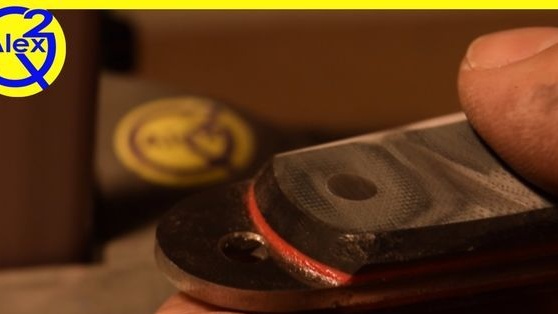
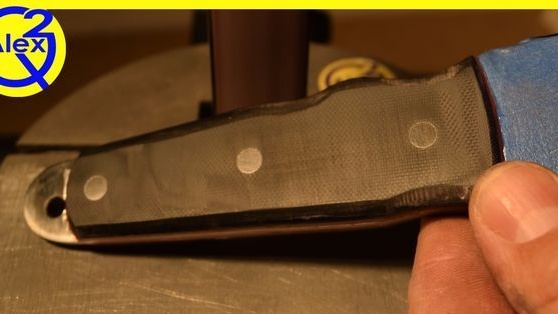
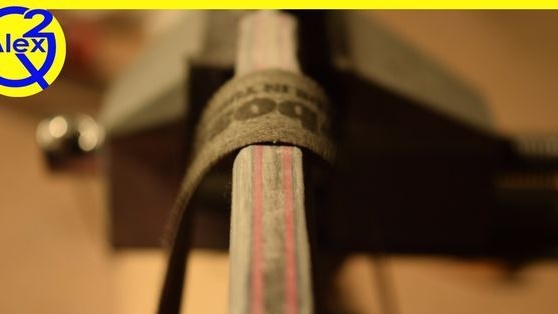
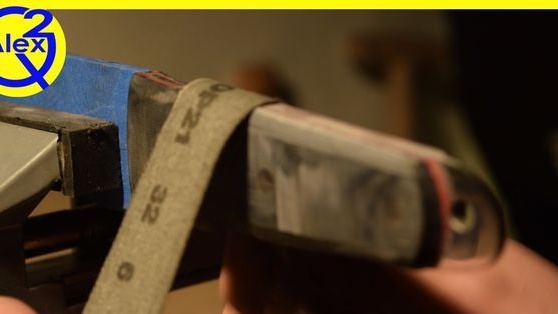
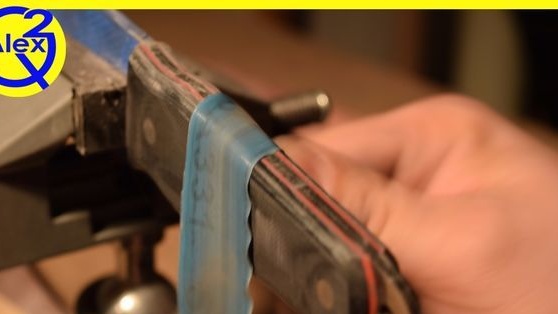
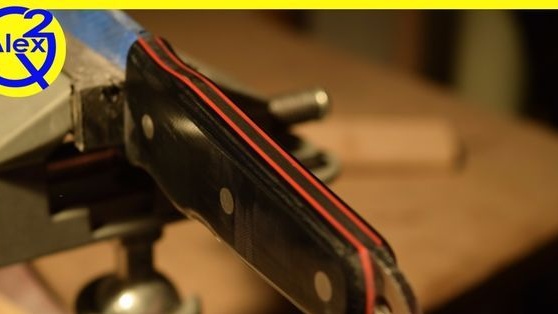
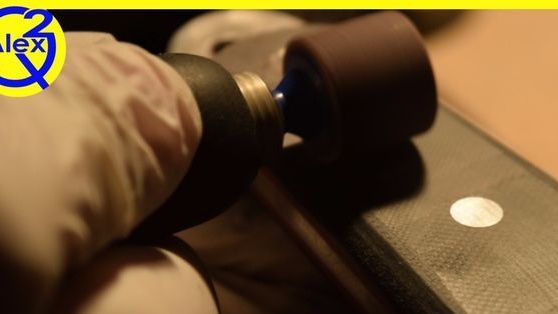
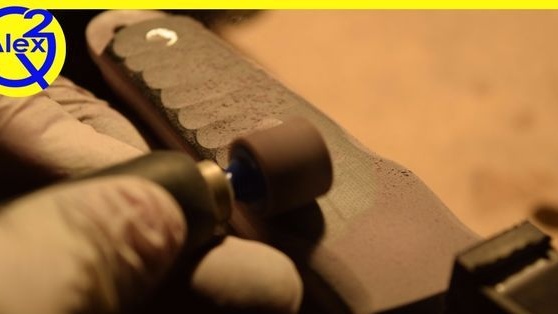
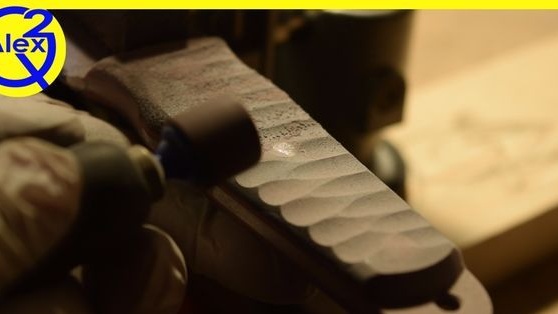
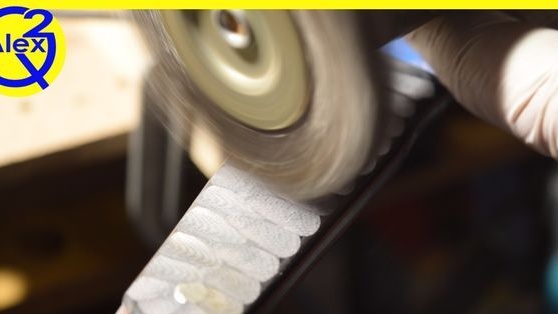
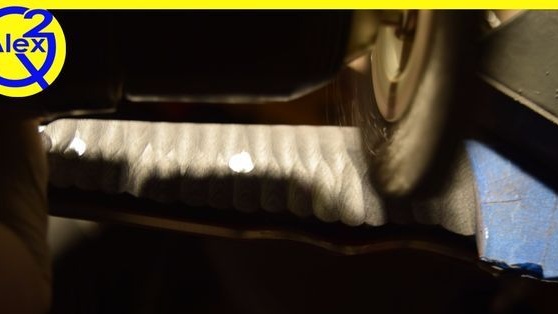
The author also forms ribbing on the handle for a comfortable fit in the hand and a beautiful appearance.
Step Eight. Patina
To protect the metal of the knife from rust, the author decided to cover it with a patina. To speed up this process, a special reagent was purchased.
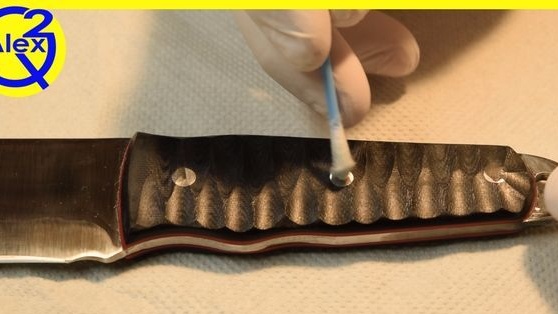
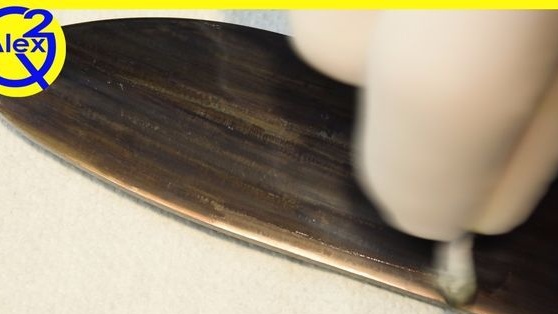
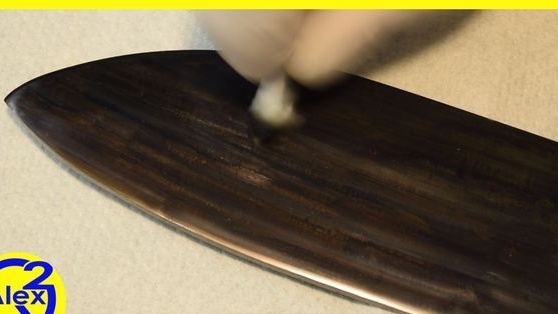
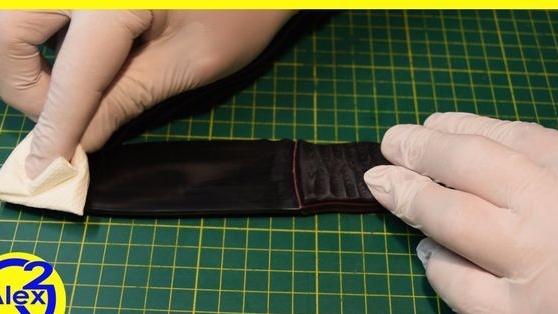
Step Nine. Sharpening and checking the knife
The main sharpening of the knife is done on a belt grinder, but it gets perfect sharpness with manual sharpening. Here, water stone with a grain size of 3000 and 6000 is used.
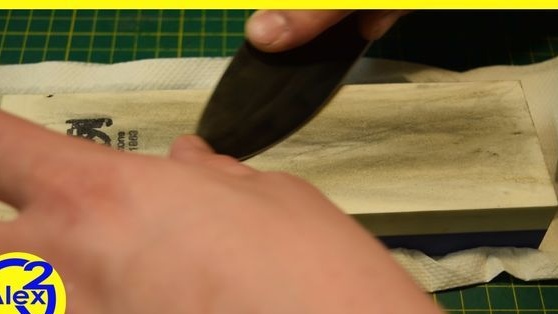
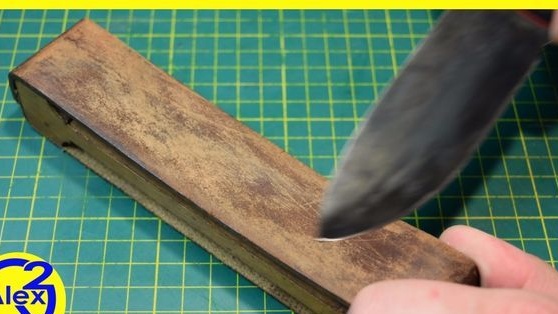
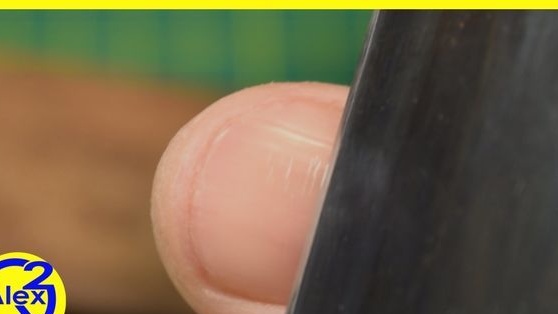
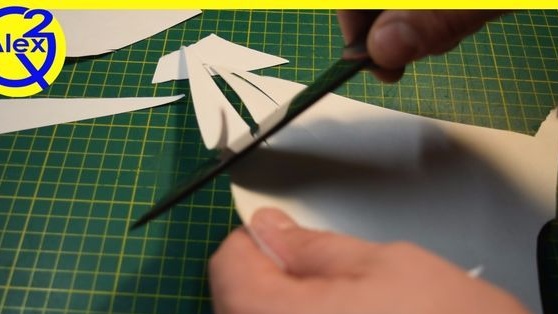
Sharpening should be such that the knife cut the paper without any problems.
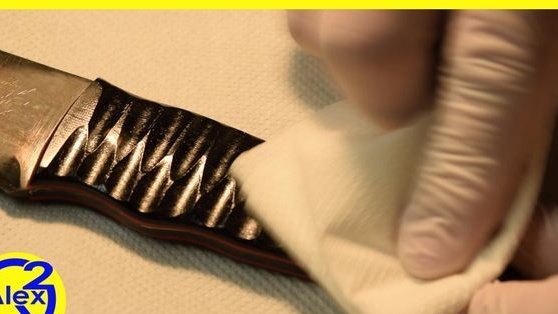
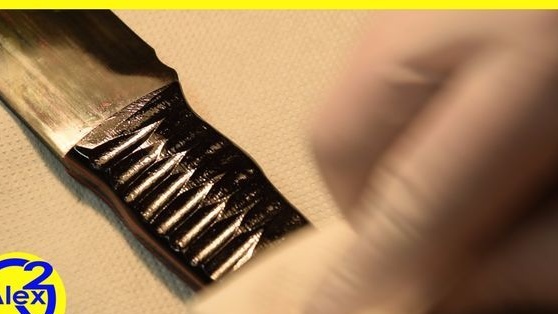
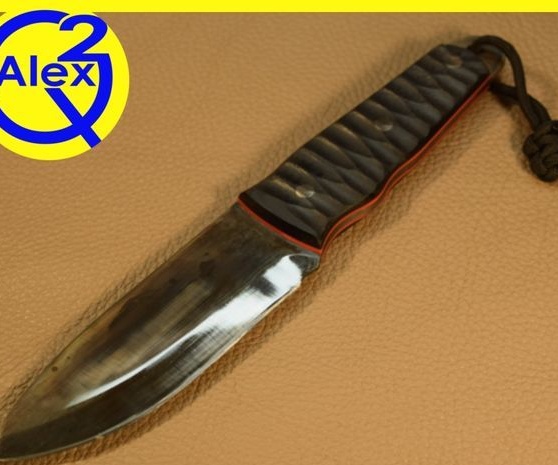
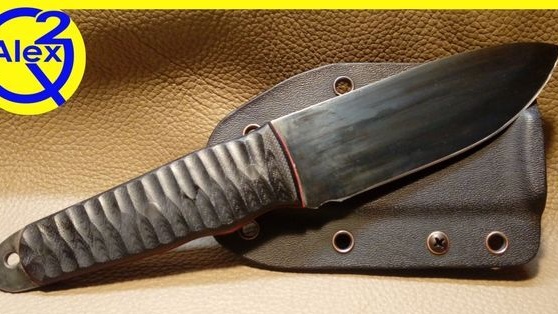
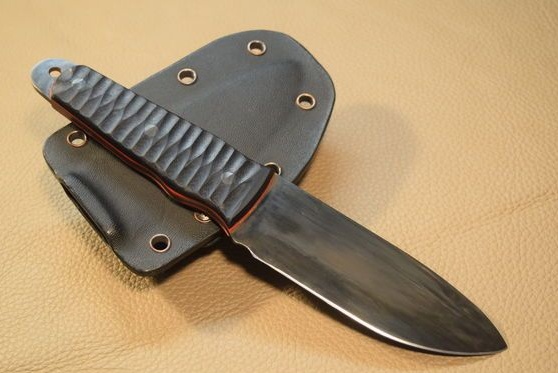
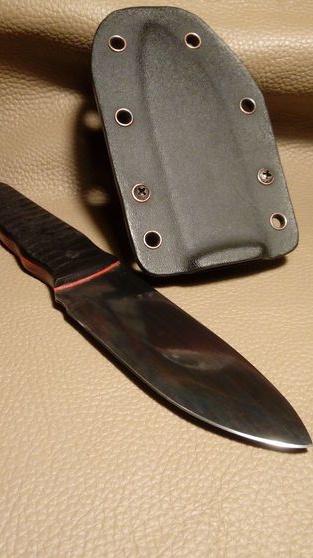
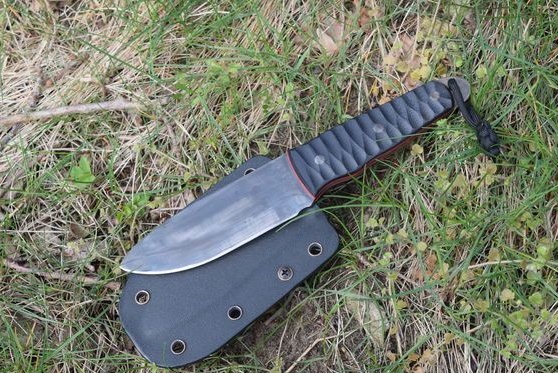
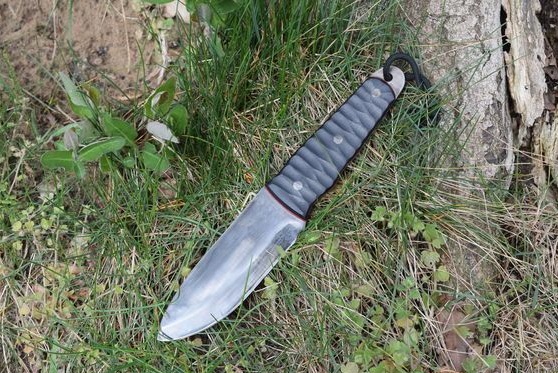
In conclusion, it is coated with oil for protection.