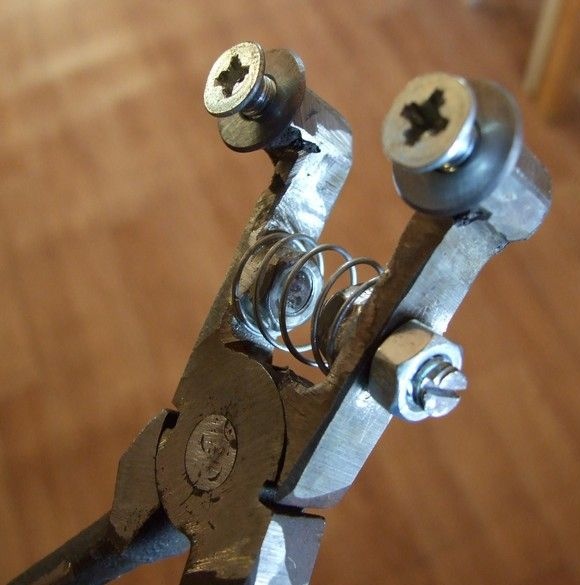
I’ll give you a debt by paying at the end - this is not a joke.
Fire - to letters, to an orphan - a dime and a Christmas tree.
Will I be a pale mediocrity, whether a black wolf,
I’ll give it right, I won’t overpay for nothing -
to everyone from that stained glass fragment.
Mean, ridiculous, but I want it so.
M.K.Shcherbakov “The Wolf”
Will I be a pale mediocrity, whether a black wolf,
I’ll give it right, I won’t overpay for nothing -
to everyone from that stained glass fragment.
Mean, ridiculous, but I want it so.
M.K.Shcherbakov “The Wolf”
For the embodiment of the idea that was born in the head, various materials are used in decorative art. One of the most interesting is glass. Due to its transparency, decorative products from this material can be very expressive. Glass-blowing is a completely special area of life and you can’t master it all of a sudden. But even from the usual flat painted glass at the stage of manufacturing the glass, many interesting things can be done. For example, a stained glass window or something like that, in a word a certain pattern, a kind of mosaic, from processed and fitted pieces of colored glass. Particularly advantageous, such products look where light passes through them. For example, windows, transparent ceilings, elements of interior and street doors, illuminated cabinet doors, and finally lamp shades. I have been trying to try myself in the manufacture of the latter for some time. I am selected, so to speak, in small steps, gradually acquiring equipment and tools. Here in the framework of this “pick-up” I also boast of another piece of iron. So, get acquainted - disk nippers for glass, often they are called “zag-zag” nippers, I don’t know why.
Here, it should be said that various techniques for the manufacture of stained glass are used, the materials used are somewhat different, but in any case, real glass (often, for simplicity, appropriate pieces of color transparent film are glued to ordinary window glass, so rather, this method should be attributed to imitations) stained-glass window, involves cutting glass. More or less accurately cut out pieces of colored glass with a glass cutter, and then, if necessary, precisely fit them to each other, turning the edges on a special grinding machine with a diamond working tool. Often at the stage of rough cutting, rather large pieces of excess glass remain, which it is not rational to grind with a diamond tool, but it is dangerous to cut with a glass cutter, you can ruin the part. In such cases, it’s a miracle how good our nippers are. Bzdyn, and order.Even more often, “zag-zagi” is used by colleagues in the workshop - craftsmen fiddling with a glass mosaic and in “fusing” (fusion of colored glasses in a special muffle stove). In a word, our piece of glass is useful, but like all good tools, it’s very expensive.
In the same places where the wire cutters are found, spare parts for them are also sold, most often carbide wheels. Having once met wheels, very similar in appearance, to a vulgar hardware store, the idea was born to make glass nippers on their own. These were spare parts from the tile cutter. A pair of wheels was purchased. It costs about 50 ... 100r apiece, depending on the diameter. Their purpose is exactly the same - to cut glass.
So, we’ll be curious about what the industry offers us.
The study of industrial analogues, so to speak.
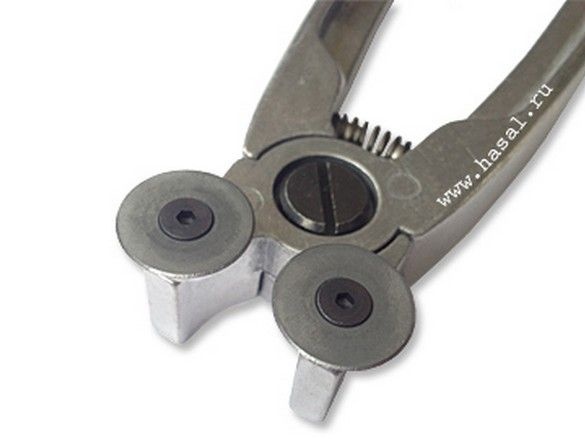
A fairly powerful design, short jaws, on the one hand providing ease of operation due to the large lever, on the other hand, it is not always possible to get to relatively large cuts. The travel stop inside the spring is not adjustable. Price hoo. It is equipped with such a “sock” for collecting glass debris, which is of course convenient.
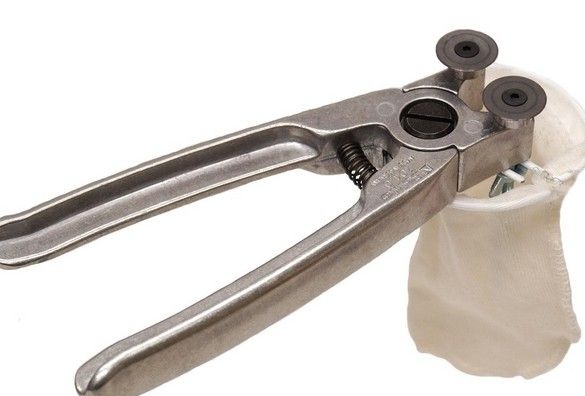
Some upgrade, probably convenient
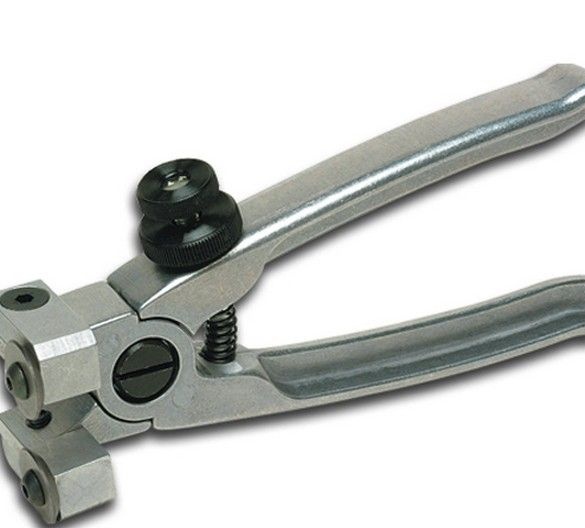
Electrical analogues come to mind - side cutters and end cutters. By the way, in these, the stroke depth is adjustable. They are even more expensive.
Design with a different spring and cutting wheels “inside”. Adjusting the depth of cut is.
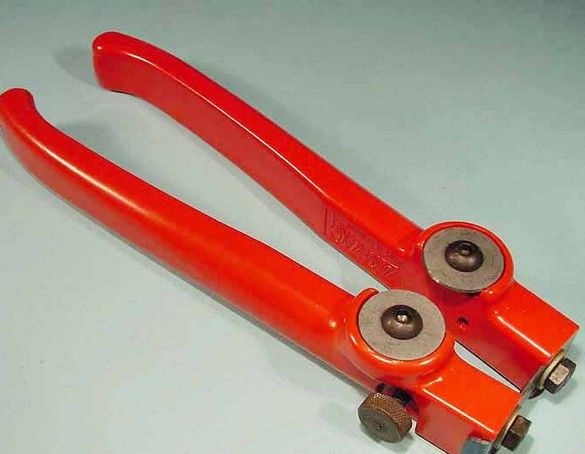
It is difficult to say how convenient the layout is, but they should be pretty cheaper, since the design is much simpler.
Relatively cheap option.
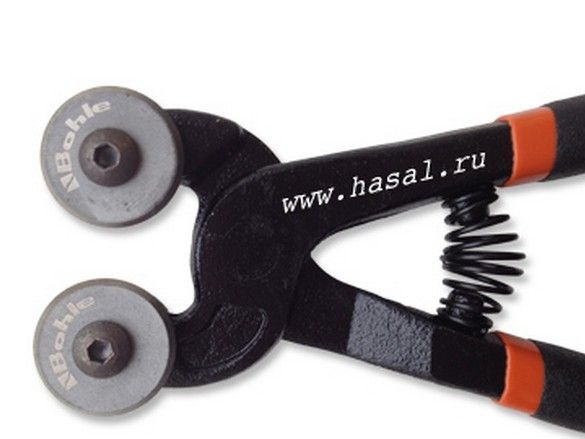
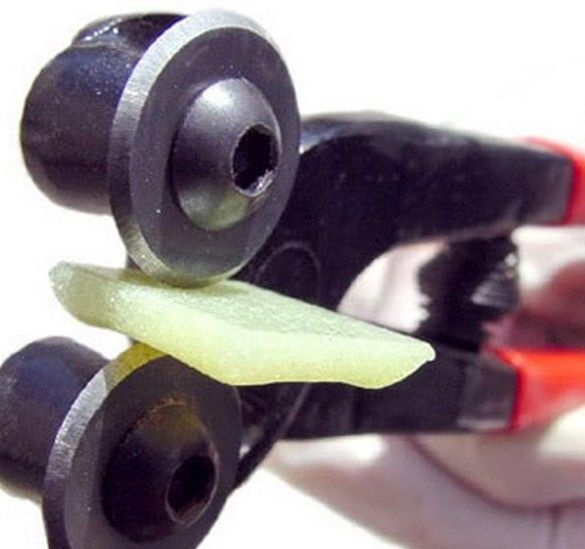
They are cheaper, they look thinner. Nothing is regulated. But probably still bite.
Our answer to Chamberlain.
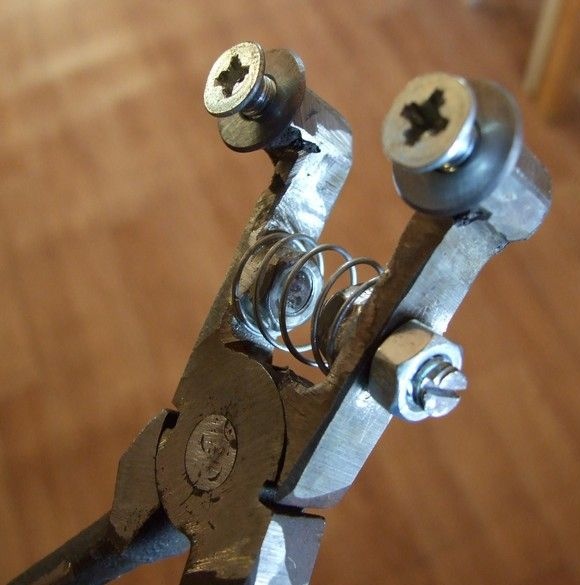
My performance of the nippers is made on the basis of pliers. Fortunately, they were lying around somewhere found, in a very poor condition - the plastic handles were melted, cut, the lips were pretty picky, everything was pretty greasy-oiled. In a word, it’s disgusting to take even with chopsticks.
What was used from the tools.
A set of metalwork tools, a small detachable machine (grinder), something for drilling, a gas torch plus soldering materials, a small welding inverter with accessories. A little patience and accuracy.
Training.
The pliers were scrubbed, washed with a solvent, the twisted handles were cut off, without them it turned out very gracefully. With a small cutting-off machine - a “grinder”, all nippers and a grasping “protector” are sewn from the inside of the lips, now all of this is useless to us, they will only get in the way. In this case, the pliers did not disassemble - the handles were fixed in the maximum open position, the right place was clamped in a vice. Carefully, having tried on the machine in advance. Yes, take care of safety glasses - small particles during such work sometimes fly unpredictably.
Design.
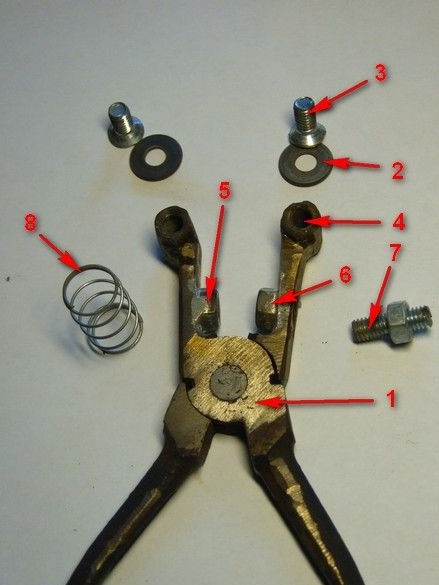
Carbide rings (2) have an inner hole diameter of 6 mm. So be it. As fasteners, an M6 screw (3) with a "sweat" head was used - the cone will better fix the cutting disc. It is screwed into the elongated nuts (4), they are called “connecting”, for greater durability, because the fasteners are not very good now and small threads often break off with any significant effort. The extended nut increases the reliability of the connection. The nuts are welded sideways to the lips of the former pliers (1). Neatly, half a thin electrode to aim was easier. Here, perhaps, brazing would be more appropriate. For example, brass, but for this you need a gas vapor burner, such as dental or jewelry. Those on gas without oxygen do not have enough temperature.
Actually everything. You can try to bite, however, for convenient work, you still have to do a stroke limiter and a return spring.The latter is for convenience, the first is for the health of carbide cutting wheels.
The stroke limiter was decided to be made of hardware parts. It was possible to quite elegantly combine the limiter with the return spring. The matched spring (8) fit nicely onto the M6 nut. By the way, if a spring is too tight, the force of its compression can be easily adjusted by lowering it into acid. Sulfur for example.
It was decided by the nuts “limit freedom” to the spring mentioned above, one of them could easily skip the screw regulating the width of the jaw closure. Nuts fit comfortably between the jaws. Perhaps the layout is not very successful - the depth to which you can climb to the cut line on the glass decreases, however, it was not easy to get below the hinge. The nuts are soldered with a torch, tin-copper solder for copper water pipes, with the corresponding flux in the form of a paste. The flux is slightly acidified, so the place of soldering should be washed well. By water. The nut (5) into which the depth adjustment screw (7) will abut is muffled by a piece of the corresponding threaded rod. Before soldering. So that the plug is also soldered. The result was a sort of stump. Under the nut (6), a hole slightly larger than 6 mm was drilled before soldering. So that the stopper is screwed into it from the outside. The screw for adjusting the depth of biting is also made of a piece of a hairpin; on the outer end, a slot for a screwdriver is sawn through a metal with a hacksaw. From spontaneous unscrewing is fixed with a lock nut from the outside. Adjustment is carried out using a screwdriver and a wrench, perhaps with frequent adjustment it will not be too convenient, practice will show, in the end, it will not be difficult to equip the screw and lock nut with small handwheels to screw them with your fingers.
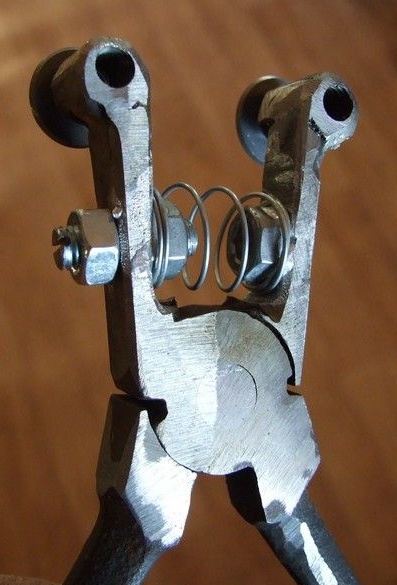
Sea trials were successful - an ordinary 4 mm thick window glass bites off quite successfully, and efforts to the tool handles have to be made quite moderate. Stained glass for stained glass should bite even easier. Extraneous glass chips do not form during operation.

It should be said that for the quality and effort of biting, the sharpening angle of the cutting wheels should be important. Probably, in factory tools, it is different from that used in tile cutter spare parts. And although the tile cutters showed themselves on the good side, it is worth trying sharper sharpening them, fortunately, the cost of the wheels is not high. Let me remind you that the processing of hard alloys is carried out with a diamond tool.