What is needed
In order to quickly and reliably put a hammer on the handle you will need:
1. A piece of rubber having a length slightly larger than the length of the end of the handle designed to fit the hammer, and a width equal to the length of its perimeter.
2. A small amount of any plastic lubricant, such as lithol.
3. PVA glue.
Rubber can be cut off, for example, from an old bicycle camera, but not of Chinese manufacture, which contains plastic.
How to plant
Attaching the tool head to the handle is as follows:
1. The upper end of the handle is treated so that it easily, without pressure, enters the hole of the hammer.
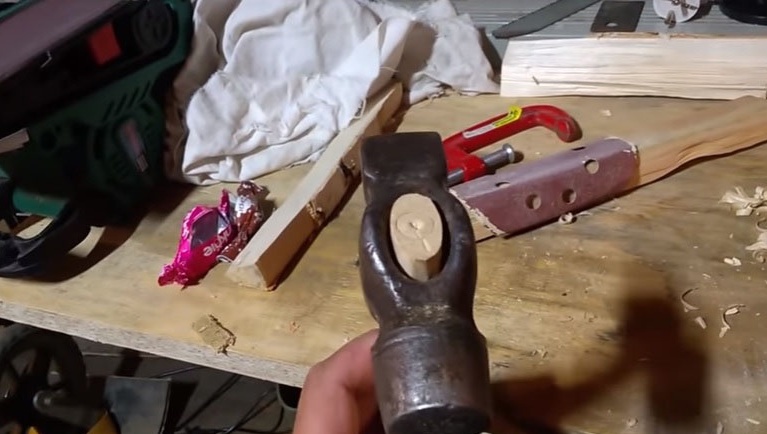
2. Rubber is wrapped around the end of the handle.
3. Lubricate the outside of the rubber with grease and put a hammer head on it.
4. Drive the hammer deeper into the handle, holding it vertically and tapping it with its free end on any surface.
5. Cut off excess rubber.
6. Coat the gap between the head and the handle with PVA glue. This is necessary so that subsequently they do not get water.
As a result, the hammer head fits onto the handle so firmly that it almost never flies when using the tool.
The advantages of such a hammer nozzle
In comparison with the traditional wedging of the handle, this method of hammer attachment has two very important advantages:
1. The wood of the handle of the hammer remains intact, its structure is not weakened by driving a wedge.
2. When working with such a hammer, the rubber “gasket” between the head and the handle absorbs and does not allow transmitting the force of blows directly to the handle, which significantly prolongs its service.
In this convenient and quick way, you can plant not only a hammer, but also a heavy sledgehammer or ax, the tool will hold on the handle reliably and firmly, regardless of its size and weight.
Video clip how to firmly put a hammer on the handle without using a wedge: