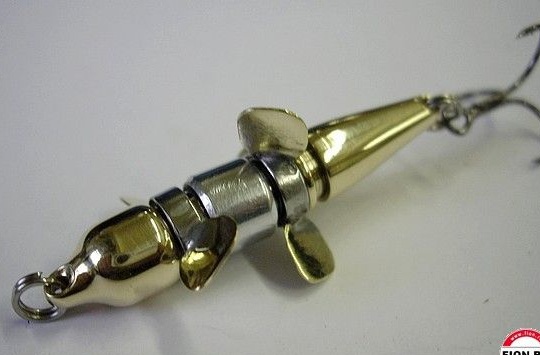
Surely not all anglers know this type of spinner as Devon. Its feature is that on such spinners there is one or several screws. During wiring, such a screw will rotate, emitting special vibrations and sparkling in the dark. This is what pretty much seduces a predator. In this article, we will look at an example of how to assemble a simple but effective Devon from a crane box.
Materials and tools for homemade:
- axle box crane (ceramics are best for the head part, and screw for the rear part, since it is longer);
- a hacksaw for metal;
- vise;
- drill;
- file;
- whetted;
- sandpaper;
- bearing (suitable from the hard drive);
- soldering iron with solder and acid.
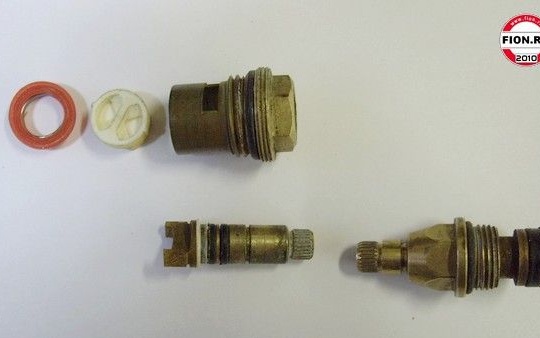
Devon manufacturing process:
Step one. Making a blank
First you will need to saw off the milled parts, for this you will need a vice and a hacksaw for metal. The result will be such a blank as seen in the photo.
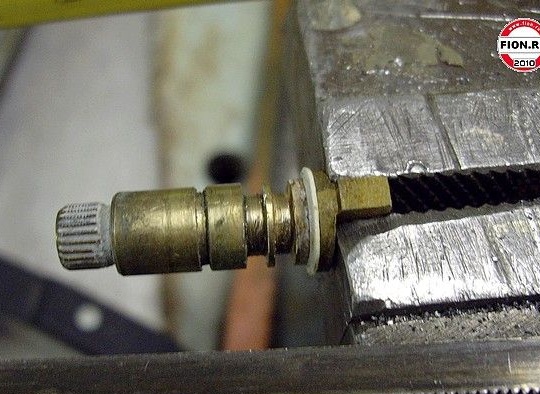
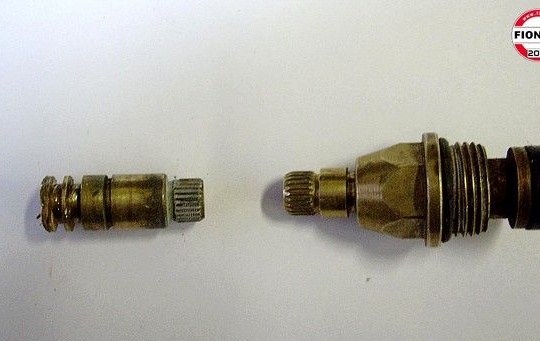
Step Two Making a bearing seat
An electric drill will be needed to create a bearing seat. The workpiece is inserted into the cartridge, and then with the help of a file under the bearing, an asterisk is ground. The most important thing here is not to overdo it and not to waste too much. In the process of work, you must constantly try on the bearing to the seat.
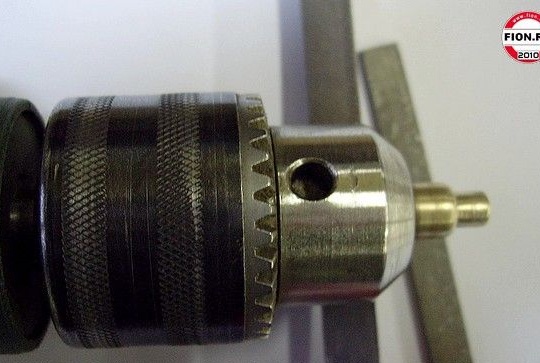
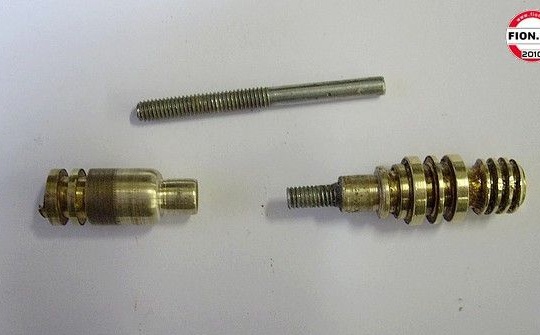
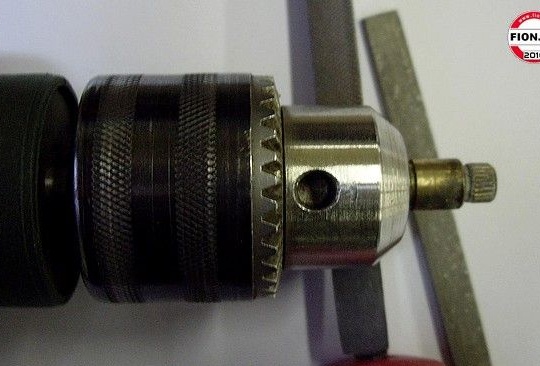
On the back, you also need to make a bearing seat. Excess parts are cut with a hacksaw.
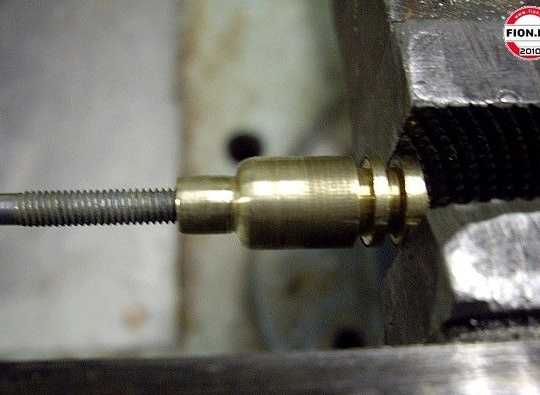
Step Three Sharpening work
With the help of a sharpener, the workpiece must be processed to the desired shape. The result will be the details, as in the photo. The auxiliary screws are screwed into them.
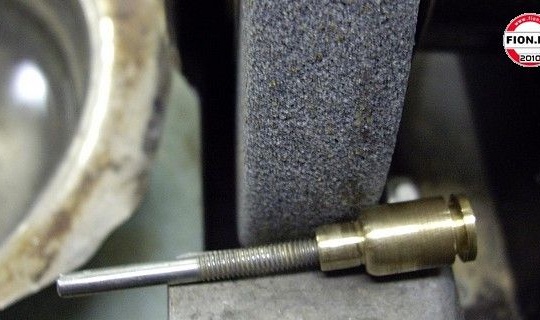
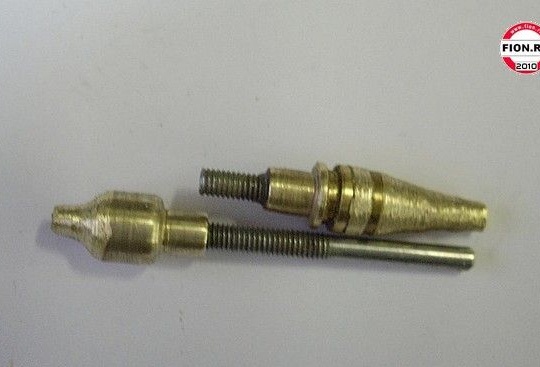
Step Four Give the final form
Now the workpieces are again inserted into the electric drill chuck and processed to the desired shape. Files, files, sandpaper come into play.
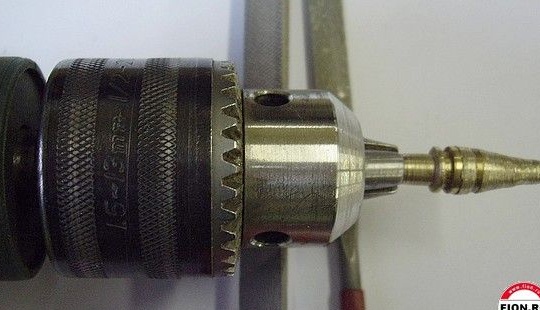
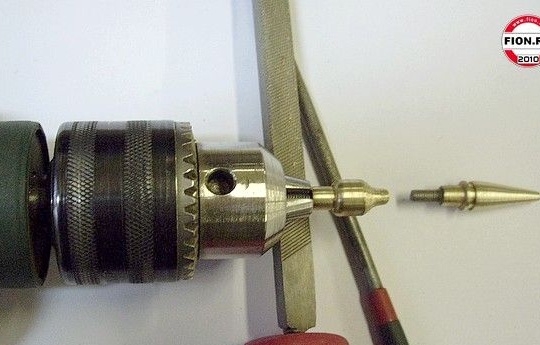
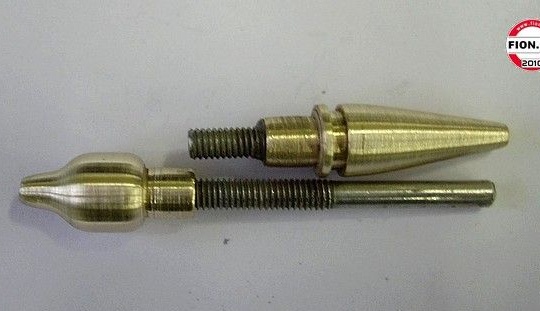
Step Five Make screws
To create rotating screws, you will need miniature bearings, such can be found in computer hard drives. And also brass strips will be needed. First, from brass, you need to cut strips of length and width to create blades. Then, in each strip using a needle file, a groove is made under the width of the bearing. This is necessary to give greater strength to the connection.
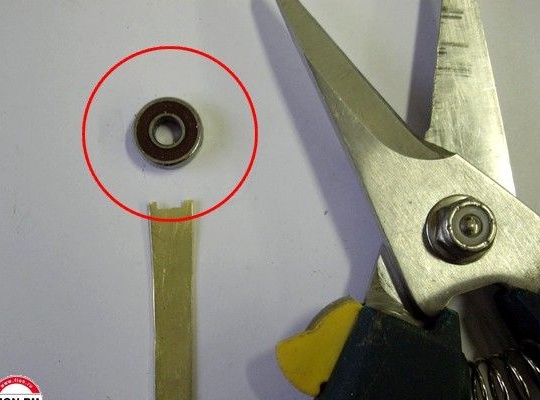
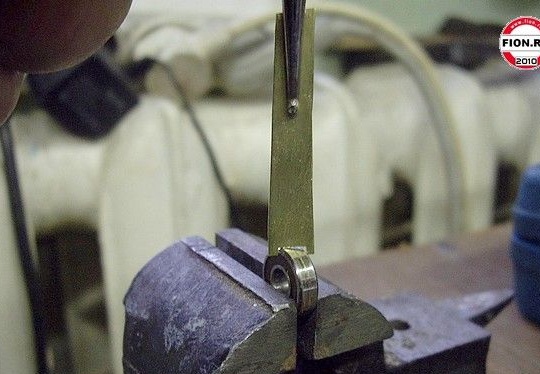
The first strip is soldered arbitrarily, and then, focusing on it, you can mark the installation sites of other blades. In order to solder the blade, you need acid. The soldering spots must be degreased first. After soldering, the joints are polished, excess is grinded. Well, then the stripes are given the desired shape and angle. As a result, the propellers will come out, as seen in the photo.
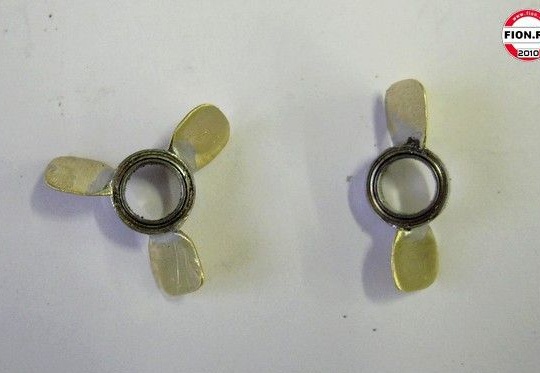
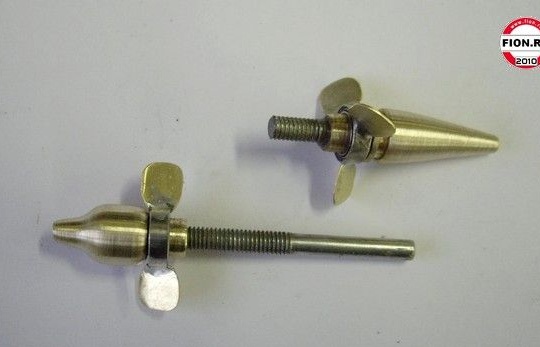
Step Six The final stage. Polishing and assembly
After a test fitting of parts, they can be polished to a shine. Each piece is polished separately. After polishing, everything can be collected.
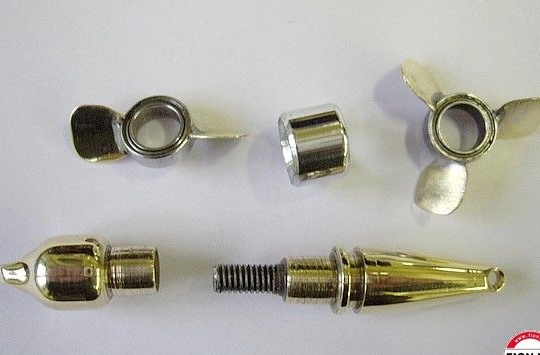
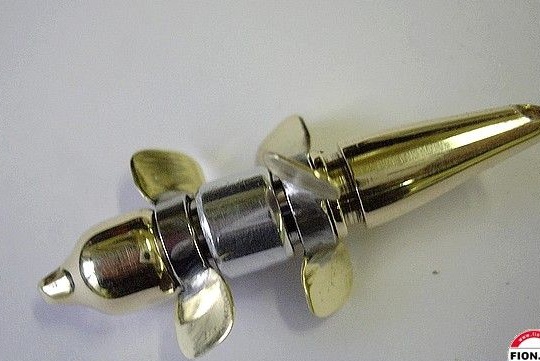
What the finished Devon looks like can be seen in the photo. Now it remains only to install two clockwork rings and a tee. You can start the test.