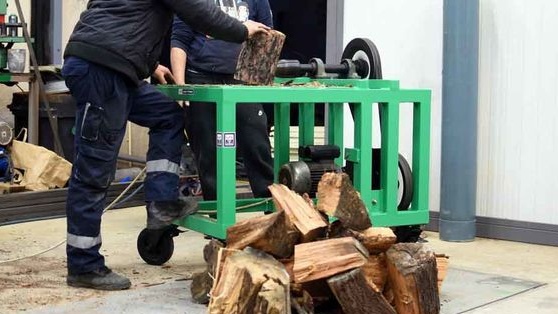
Winter is approaching, and for many residents of private homes this means the opening of the firewood season, if there was no time to do it in the spring. To bring firewood to the courtyard is not the most difficult, their splitting can be considered the most tedious and lengthy. For those who do not like to chop wood with an ax or those who chop them in bulk for the purpose of selling, you can make such a machine for yourself.
This is one of the easiest firewood chopping machines. It works on the basis of an electric motor that drives a threaded cone, which is popularly called a “carrot”. As the cone climbs into the wood, it expands it more and more and as a result, the stump breaks.
Materials and tools for homemade:
- engine (used at 3000 rpm);
- a square pipe or corner for the manufacture of a frame;
- two pulleys and a belt, which will reduce speed by 10 times;
- bearings with screws and nuts;
- a steel sheet for the manufacture of a desktop;
- wiring, switch;
- welding, grinder and more.
The process of making wood splitter:
Step one. Make the frame
We begin the manufacture of the machine with the frame. Although there will not be large loads, such as, for example, on hydraulic machines, the frame needs to be made strong. For its manufacture, the author needed a square pipe with dimensions of 60 mm x 60 mm x 2 mm. If we talk about the dimensions of the frame, then they are: width 80 cm, length 106 cm and height 62 cm.
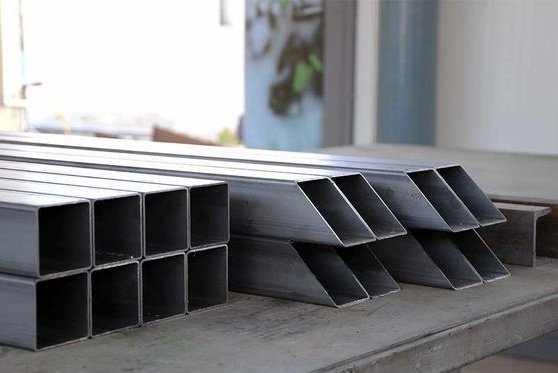
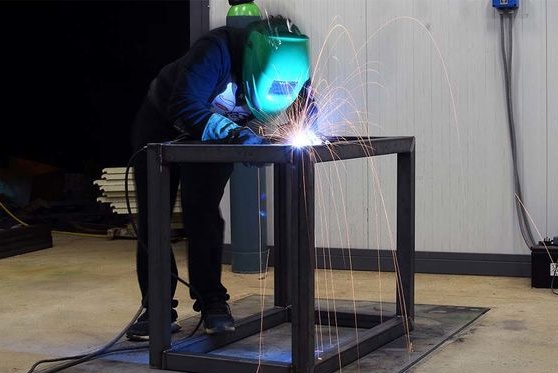
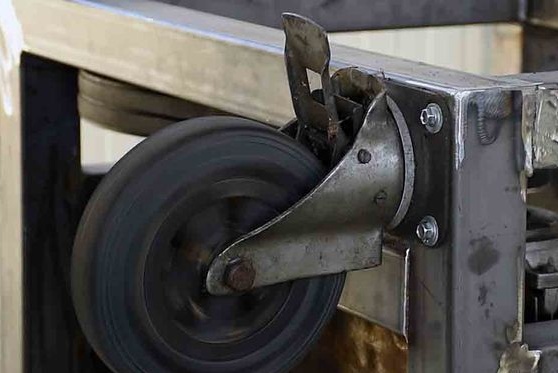
If you are thinking of moving your machine, then equip it with wheels. The author adapted the wheels with a size of 18 cm, as a result, the height of the machine was 80 cm. Of course, here the height must be selected for growth, the main thing is safety and convenience. We cut the pipes and weld the frame.
Step Two Engine, pulleys and cone ...
The author used a single-phase motor for his machine with a speed of 3000 rpm. To get the required power at the output, the speed must be reduced at least 10 times, this is done by selecting pulleys. We put a small engine, and a large cone. You can use three or more pulleys to maximize understatement.The author installed four pulleys, one on the engine, one on the cone, and two more are on the axis located between them.
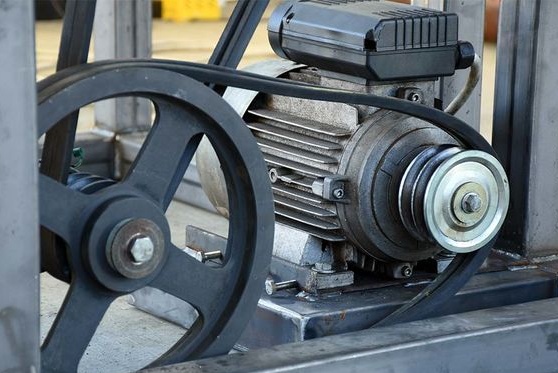
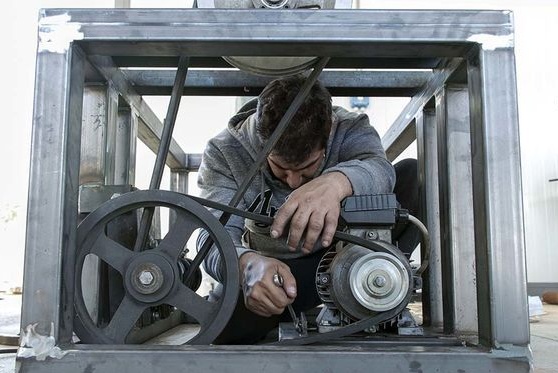
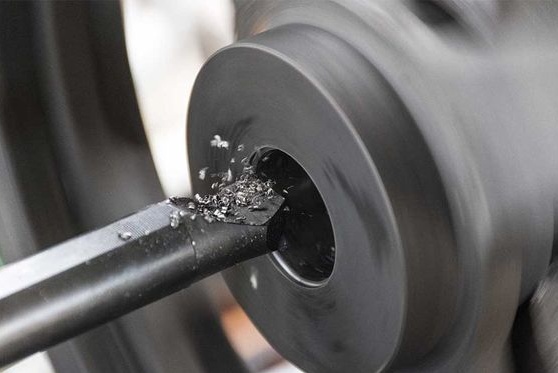
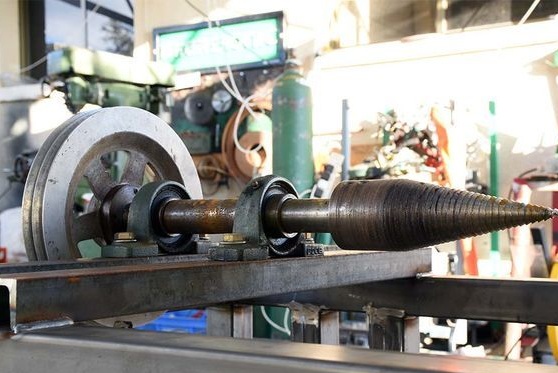
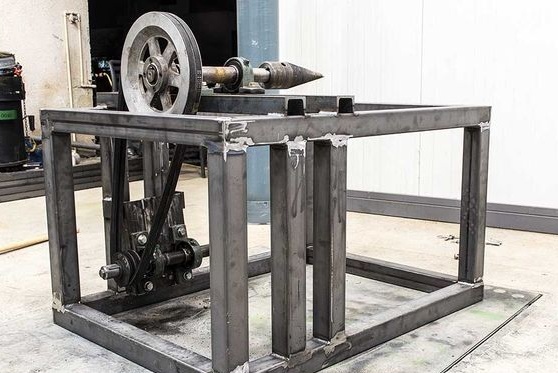
As for the cone, the author bought it, as he could not do it himself. This spare part will not cost too much if ordered from a turner. The thinnest part of the cone is 8 mm thick and the widest is 80 mm thick.
Step Three Desktop
To make a desktop, use thick sheet steel. Do not forget that when splitting wood, the stump will also want to rotate, and will rest on the table. In addition, you will need to make a special emphasis, which will additionally protect your hands if the stump wants to crank. This emphasis is made of a piece of a thick plate, it must be sharpened in the form of an ax. Further, this part is welded parallel to the cone.
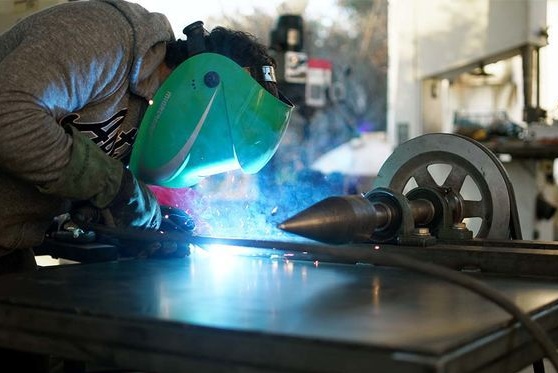
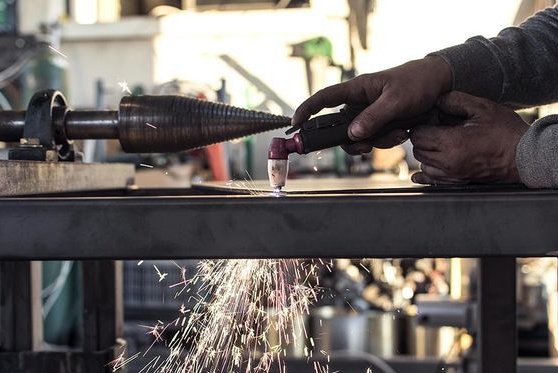
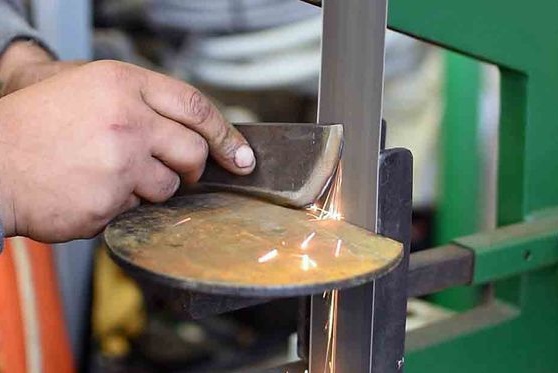
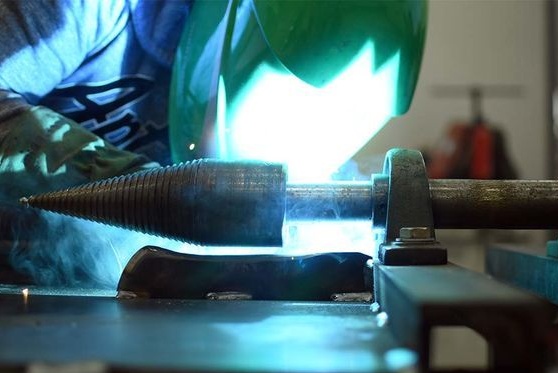
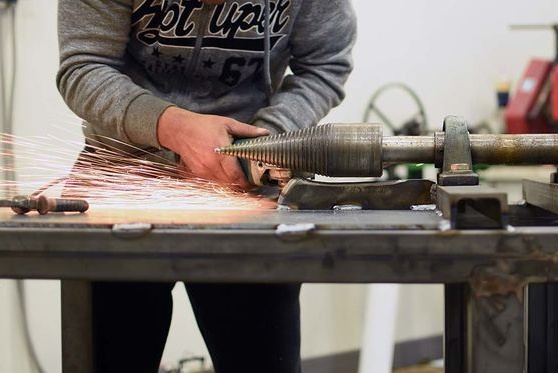
Step Four Painting and testing
In the end, you can paint the frame so that it does not rust and delight the eye. According to the author, in tests the car showed itself perfectly. Using a small electric motor will be appropriate for home goals, since it is silent, turns on and off quickly. The only thing I would like to remind is to observe safety rules. Buy and place a button for immediate placement in a place where you can immediately turn off the machine if something happens.
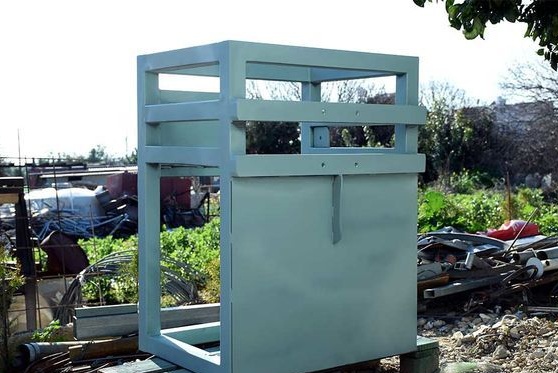
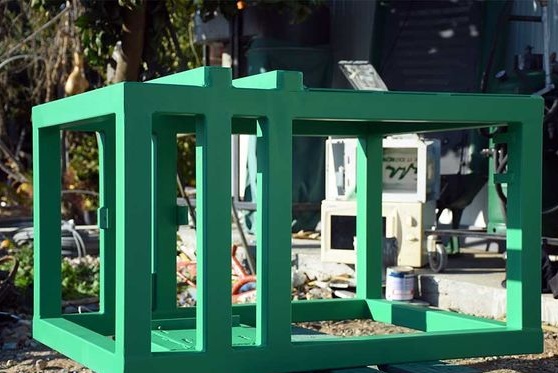
If you need a really powerful unit, and most importantly a mobile one, you can use a gasoline instead of an electric motor.
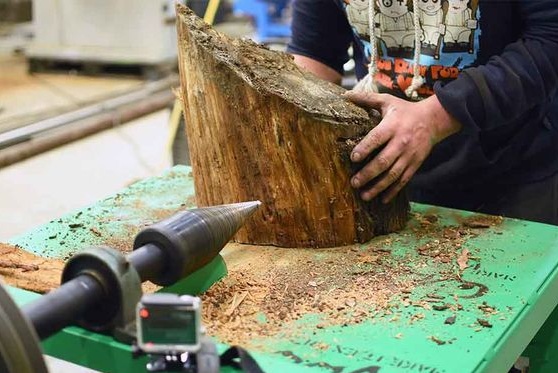
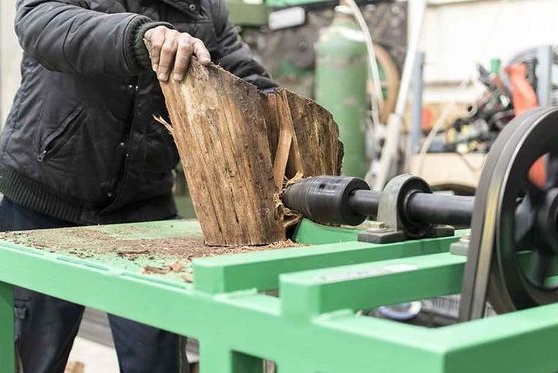
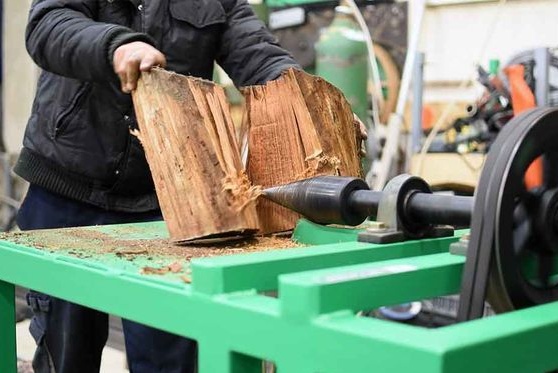
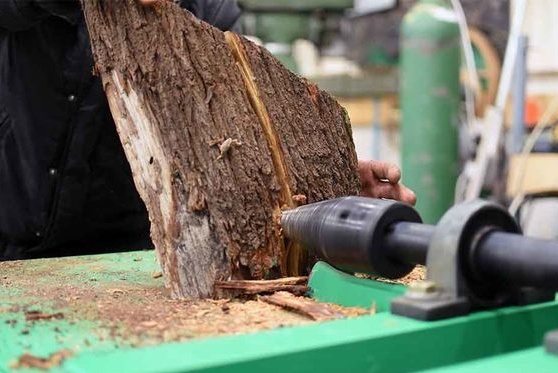
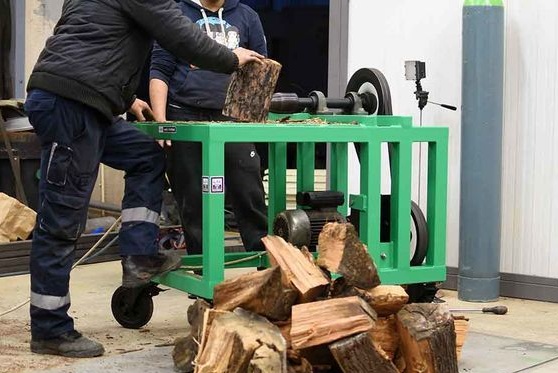
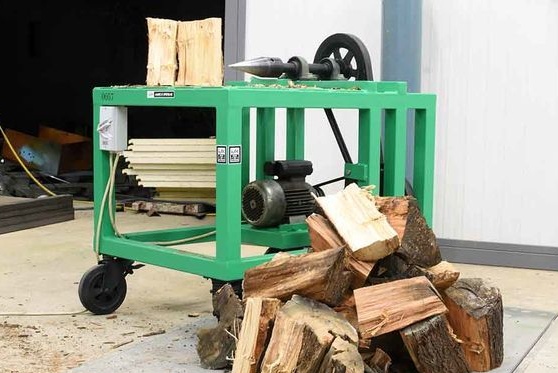
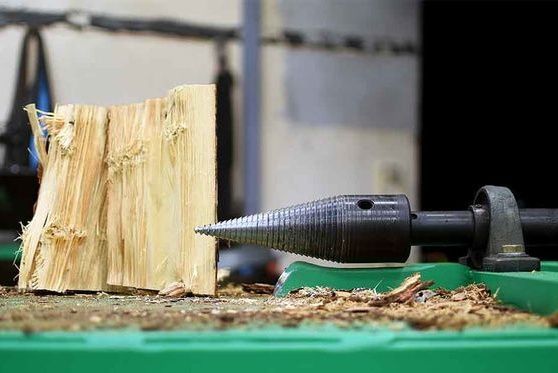