Friends Hello! After making the propane burner, it is time to make a smelting furnace. Long thought of what to make of it. Considered various options. Lay out of fireclay bricks and frame with a corner. It was possible to weld a metal frame, put it inside with brick and insulate it with cotton. It all seemed somehow complicated to me, and getting the same heat-resistant cotton wool in our region turned out to be a problem. The most ideal option was to lay the stove out of special stoves similar to a foam block. I don’t remember exactly what they are called, but this material has excellent thermal insulation and holds a temperature of 1300 ° C. At the same time, it is lightweight and quite durable and can serve as a frame. Unfortunately, getting them from us is very difficult. Therefore, I had to make it from available materials.
An empty 50 kg barrel from under the primer came into my arm. I decided to use it. He stepped back from the top about 10 cm and cut off in a circle. There were residues of primer inside, and several bottles of solvent had to be poured in order to wash and dissolve everything. Plus it turned out 2.5 l primer for huzhuda. The rest, which did not succumb, had to blur. After all the procedures, we got a good body and a cover for the future furnace. Before laying out the inner firebox, it is necessary to make a hole on the side and insert the tube, preferably a stainless steel. A gas burner will be inserted into the tube. To prevent the burner from falling out, I drilled three holes from the edge of the pipe, welded m8 nuts, and screwed in the bolts. Another hole on the side wall of the barrel is needed for a thermocouple, but this is optional. Before filling, you need to insert a tube. We select the height under the burner based on the thickness of the bottom. And we make the bottom so that the brick placed on it is flush with the barrel and does not bulge. Further, I cut out squares from 2 mm of iron. This will be a platform for loops, as the wall thickness of the barrel is small. The plates are curved for a snug fit to the walls. Records need 4 pieces of 2 on each side. One will be outside the other inside the barrel. They are twisted together by M6 bolts. I used the same plates on the sides of the barrel.Trim tubes will be welded to them. On these tubes, the barrel will hang on the frame, and occupy either a vertical or horizontal position. Only after that it will be necessary to lay out the inside.

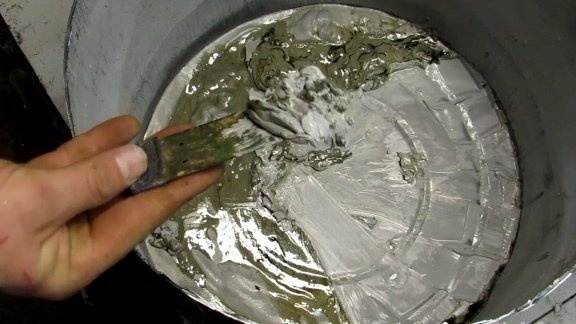


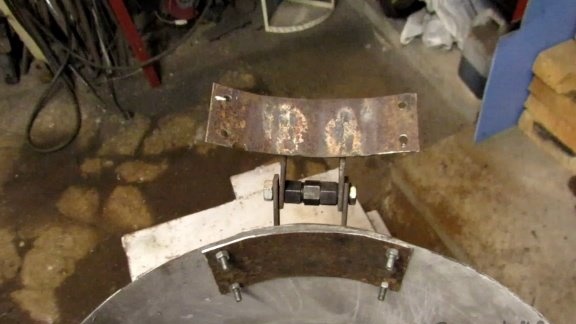
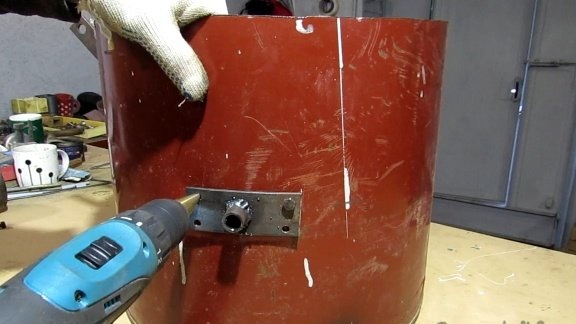
So, let's begin. The first thing I did out of fiberglass was to cut a circle around the diameter of the barrel and lay it on the bottom. Further, the furnace refractory mixture was used. She holds it at a temperature of 1700 ° C. Throwing and spreading this mixture, he achieved the necessary thickness of the bottom, and fireclay brick lived upstairs. A reinforcing mesh was also placed in the solution layer. I left this whole thing overnight for setting the solution. The next day, I started laying out the firebox itself. He put the bricks upright. Contained 6 pieces in the shape of a hexagon. One brick needs to be cut in the place where the tube will pass. After that, completely filled the entire empty space with a solution. I wanted to place a glass mat inside the barrel to insulate the walls. But he was afraid that all this would hang out. After all, the furnace will be used in horizontal and vertical position. Now the cover. In the center there is a hole and it is necessary for the gas to exit. From a 2mm sheet of steel, I cut a strip of width equal to the height of the lid. He twisted it in a ring and welded it in the center. Before filling, a glass mat ring was placed in the lid. In order for the solution not to spill out and stay in the lid, a reinforcing grill was welded inside.
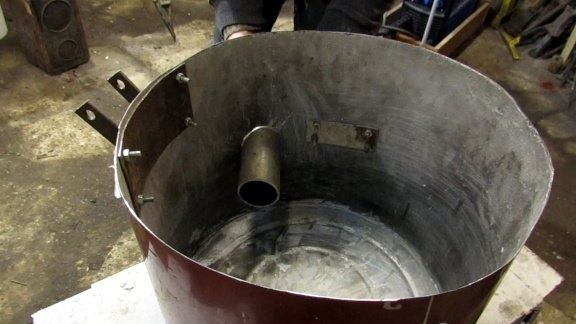
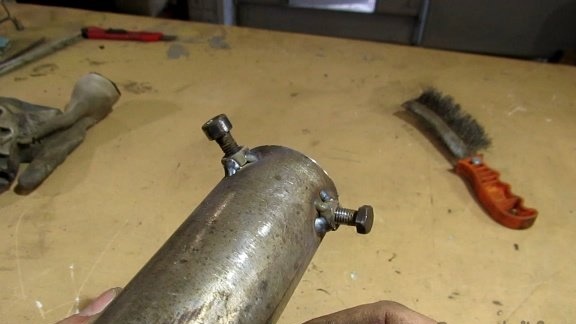
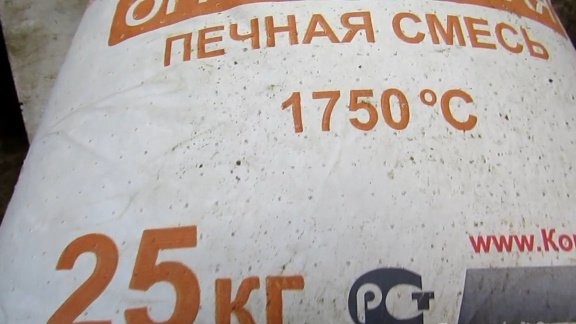
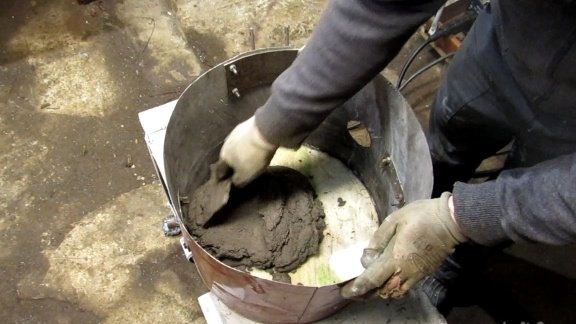
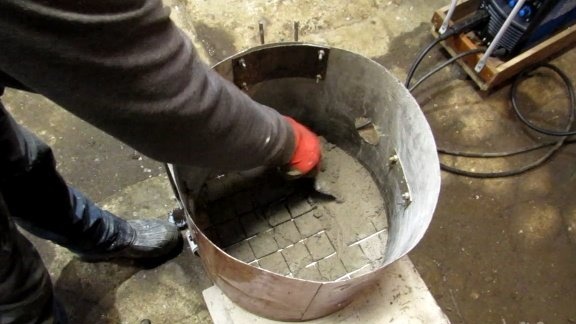
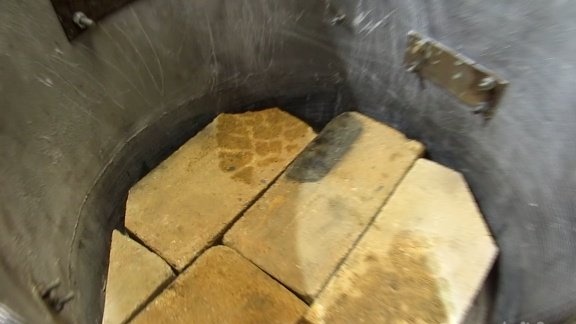

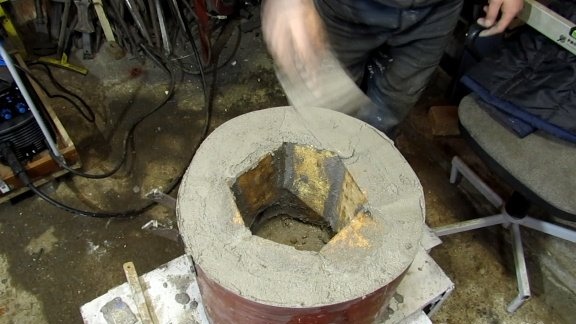
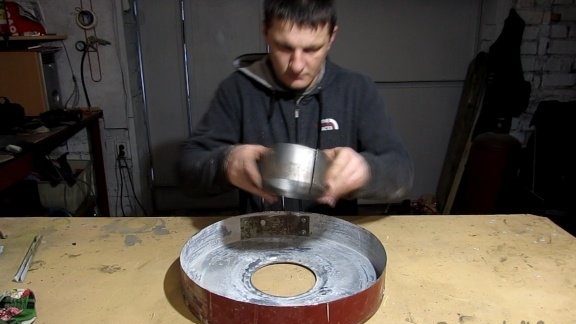
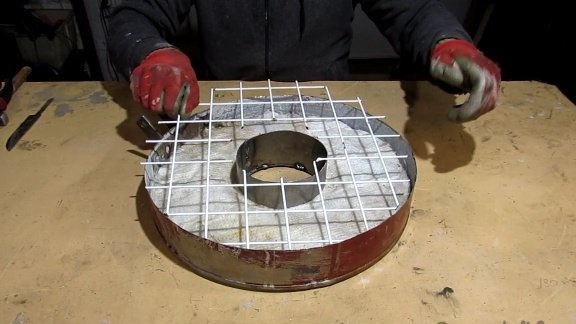
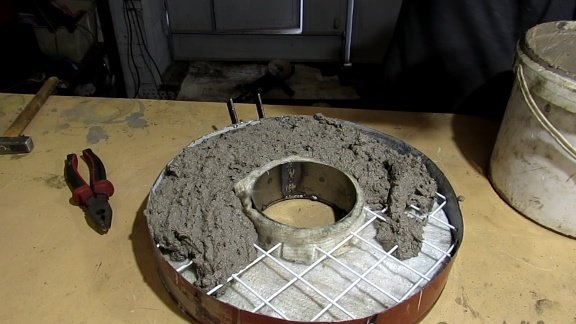
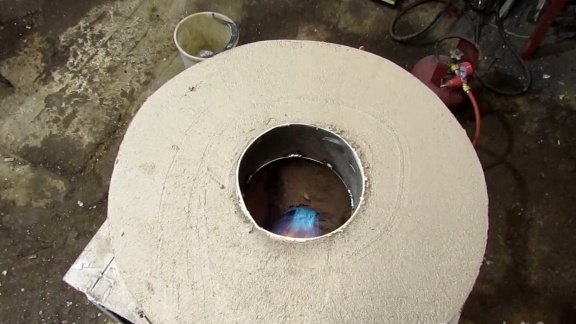
After all the preparatory operations, I filled everything with a solution. This monumental design died for about 2 weeks with periodic heating. While the whole thing was dry, I welded the frame. It consists of two pieces of the corner of the five, interconnected by reinforcement at the edges. In the center of the corners there are racks on which nuts are welded. Bolts are screwed into the nuts, and they play the role of a rotary axis. On these bolts, the furnace will occupy a horizontal or vertical position. To fix the furnace in the desired position of the tube on the side wall of the furnace, two plates with a hole were welded. And on the racks welded nuts. When tightening the bolt, it enters the hole in the plate, and the barrel is fixed. After assembling the frame, painted it with the remains of this same primer. And the stove body itself was carefully cleaned and painted with heat-resistant spray paint. I will say in advance that during test melts the paint did not burn out, and the stove body was heated to about 100 ° C.
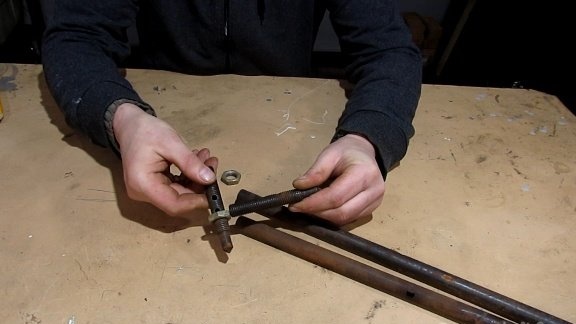
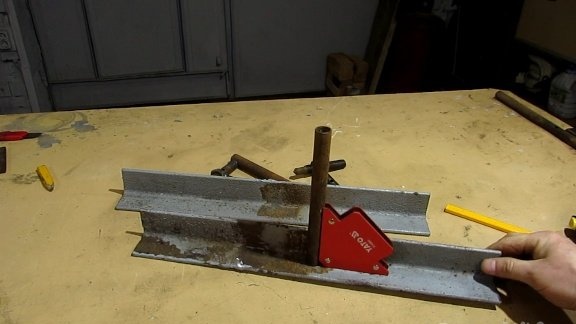
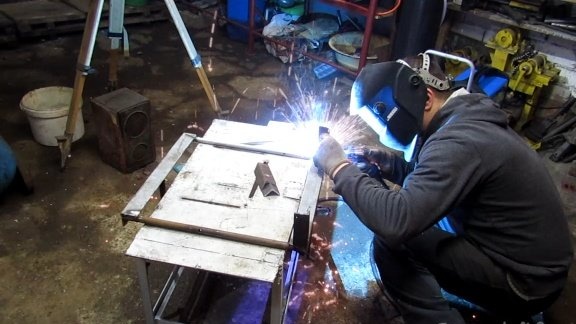
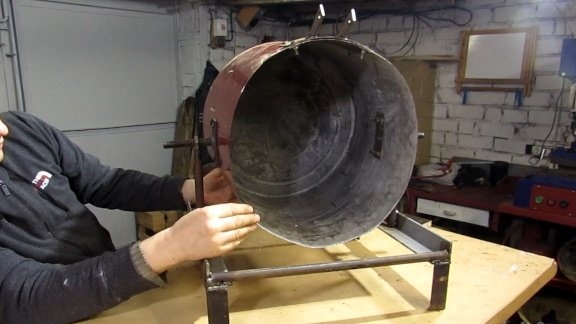
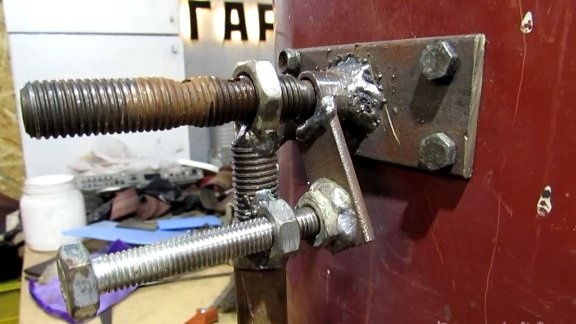
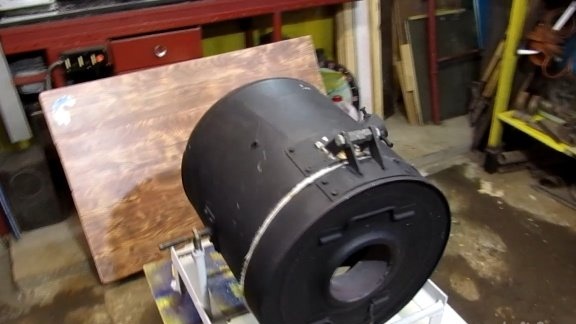
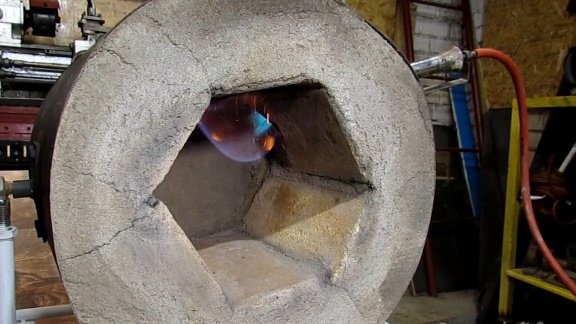
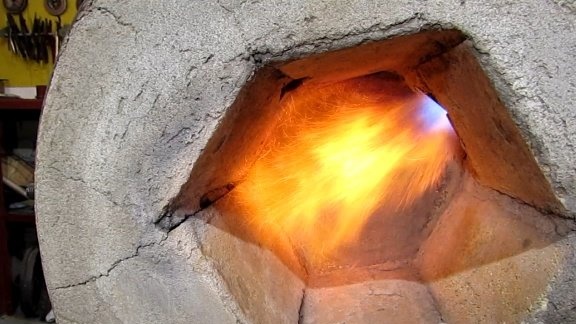
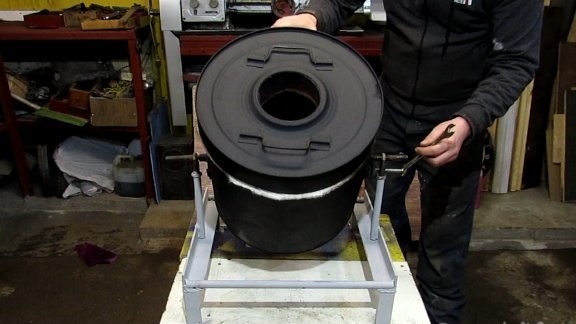
I also had to weld an exhaust hood 50 * 50 cm. For hoods. He threw the corrugation and stuck it in the ventilation duct. There is also a fan for hoods. I plan to swim in the garage and breathing this is not good.
[medium] [medium] https://bgm.imdmyself.com/uploads/posts/2020-01/1578419829_20191226_204300.jpg [/ medium]
That's all. The oven is ready. Also, for melting metal, a crucible was made from a piece of pipe with a diameter of 100 mm. The volume was about 2 liters and it will be used for aluminum. For brass, I cooked a stainless steel crucible. Also along the way were made ticks for a small crucible. For a large crucible, he made hooks and hooks, as well as a blade for removing slag. I want to say that the stove turned out to be excellent, and at the moment it has already produced about 30 kg of finished aluminum. And this is about three swimming trunks. That is, once heated, 10 kg of metal received.
In such a furnace, any non-ferrous metals suitable for casting jewelry can be melted. If you do not want to bother, it will help you jewelry workshop Moscow.
Tools required: Welding, grinder, drill, trowel, putty knife, hammer, keys, drills. From materials: glass mat, fireclay brick, stove mixture, mesh, sheet iron, bolts, nuts, paint, corners, tubes.
To control the temperature, I ordered a controller and a thermocouple in China. Links in the description under the video!
Below I leave the rollers about the manufacture of the stove and about the smelting of aluminum. Relax with good music and nice shots. Maybe I forgot something and there you can consider everything in more detail. Thank you and see you soon. Till!