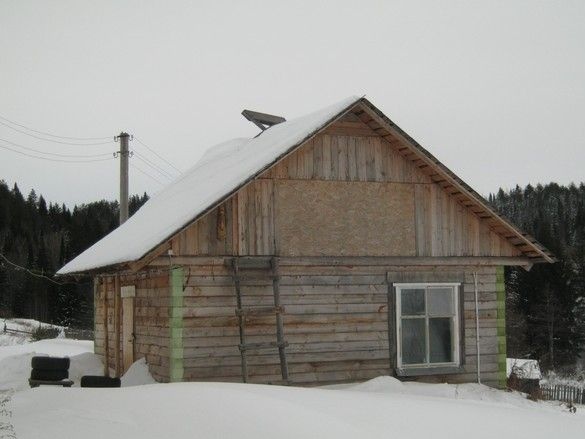
What could be more beautiful than living in a village? Own house with a stove, fresh air, the absence of neighbors nearby, the forest outside the window, spring water - uh, what can I say! However, for any person with a thirst for technical creativity, these are also, in truth, unlimited possibilities. This is not a kitchen corner, with a grunt homethat he smoked here again, with his soldering iron and not a balcony, where only a yogi can fit in with sweat. In a word, there is where to turn around, swing, where to store your technical. More beautiful than this, it can only be our own “warm” workshop, because we live far from Africa and have been cold for more than half a year.
The garden and construction season is over and there is a great opportunity to thoughtfully do something for the soul. However, in the summer it is also worthwhile to devote a little time to your own entertainment, so as not to forget the smell of rosin, and in general, not to lose the joy of life. It is convenient to allocate for this, an hour and a half in the evening, when the mosquitoes dominate the street. In a word, you need a personal technical space where access for the female part of the family is only under personal supervision and only for admiration for the owner who can do complex and incomprehensible things (Oh my husband, how smart you are! And how do you manage to be able to do it all-all-all ?!). It’s a kind of personal technical kingdom, where everything is arranged according to one’s own understanding. It is clear that for the middle zone of Russia, it is necessary to make this space heated, and the fence insulating.
The middle strip is a forest zone, the tree here is a common material for low-rise construction and perhaps the most inexpensive. By comparing the cost of available materials for walls erected without the use of heavy lifting equipment, we make sure that yes - coniferous logs and boards are cheaper. Moreover, in recent years, with the increasing fashion for environmental friendliness, wood has also become a popular material in this sense. Buildings made of wood may have absolutely no interior decoration, a sort of country style, very popular with our overseas sworn friends. However, the latter advantage is more relevant for residential premises.
So, the type of structure is one-story, wooden walls made of timber, the roof is gable. The foundation is tape shallow, the floor is earthen.
Having consulted at the nearest sawmills, we clarified the possible assortment, as a material for the walls, a beam of 150 x 150 mm was chosen.Compared to logs, the beam allows you to do with a minimum carpentry qualification, smooth vertical surfaces are easily sheathed outside, less accumulate dust from the inside.
The size of the workshop was selected based on the maximum use of whole beams - 6 x 6 m. These are the overall dimensions of the foundation. The size of the floor inside will be, respectively, 300 mm smaller on each side.
The place for the workshop was initially chosen quite far from the house, so that the howl of an electric instrument does not disturb the people in the house, however, closer to the start of construction, the workshop was moved closer. Subsequently, it turned out to be a good decision - to drag in the snowdrifts in winter would be much further. And in the summer, every day extra hundreds of meters. The place was chosen according to many criteria - convenience, aesthetic appearance of the building, coupled with other buildings, the absence of shading for beds, and convenient landing sites in the future. The future workshop, oriented to the cardinal points, like the rest of the building. The roof, based on the preferred wind directions, it would be better to orient in a different way, but it didn’t turn out very nicely. I had to sacrifice practicality for the sake of aesthetics.
What was used.
Instruments.
A classic set of trench tools - shovels, magic crowbar, sledgehammer. Garden car. For marking on the ground - ropes, tape measure 30m, long construction level, water level. Carpentry and carpentry tools, of course - a good ax on the arm. It is very good if there is a chainsaw or even better - a chain electric. Used a “furniture” stapler. A screwdriver, “Bulgarian”, “gun” for mounting foam came in handy. Tools for concrete work, including buckets, a trough for the preparation of concrete, water tanks. In some places, welding came in handy.
Materials
In addition to the timber, a board was used, mainly “inch” (2.5cm) and “floor” (50mm) thick. Ruberoid. Materials for the preparation of concrete. It is clear - nails, screws. Foam, roll insulation on the ceiling.
The foundation was marked, a narrow trench was opened along the width of the shovel bayonet. To the depth, umm ... knee-deep. Sand filling was made at half depth, in thin layers, with tamping, wetting with water from a watering can. A plastic film is laid on the sand, the side walls of the trench are also lined with polyethylene. The task of the film is to prevent water from concrete from absorbing into the ground. Reinforcement without fanaticism - two rods from the bottom, two from the top. Armature with a diameter of 10, 12 mm.
Concrete is poured flush with the surface of the soil, concrete is not liquid - to be laid, not poured.
On top of the subterranean part of the foundation, a removable formwork of thin boards is installed. Four shields were made, one and a half to two meters, so that the angle could be cast. After, the corners connected. Thick concrete can greatly save on materials by blocking up small objects, possibly hollow.
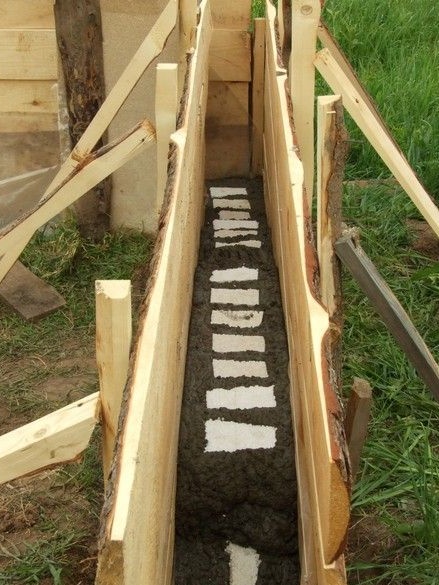
Miracle how good glass bottles are - and void-forming elements and the disposal of hazardous waste. Plastic ones are also suitable. When all the bottles in stock run out, it is very convenient to organize voids with ordinary white polystyrene, both packaging and specially purchased. It is sold in the form of sheets of various thicknesses, it is not expensive at all.
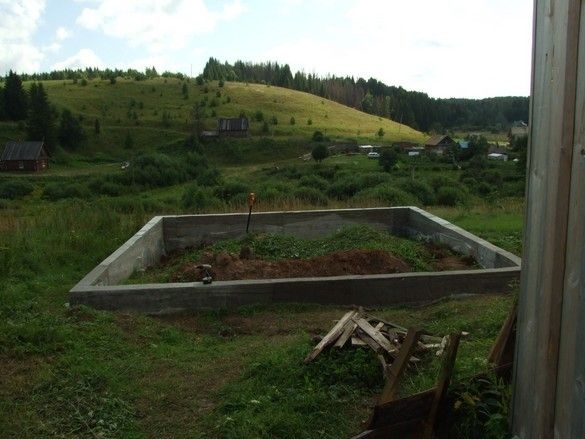
After the casting of the foundation is completed, the entire formwork is removed, the soil is leveled inside the foundation.
A timber was brought from the sawmill. Specialists arrived, two people. When they collected the log house at home, they used lifting equipment - device, like a small crane on a tractor. Frankly, I assumed that it would be here, too, but more often than aspirations, carpenters, spitting on their hands, briskly took up the wooden pieces and in almost two incomplete days collected almost the entire "blockhouse". I barely had time to cut them dowels for clogging.
Finished on their own - the "experts" did not finish - they promised, but did not come. With their employer, we paid for what has already been done and said goodbye.
Bars, rafters were independently raised and installed. I only had to purchase a spiral drill of large diameter and length for drilling holes for nails.
The rafters and their harness were conceived from boards, it was already easy with them in the sense of movements. Rafters from a wide board 50 mm thick. The ridge angle, previously drawn in the CAD, several options, the most aesthetic one was chosen, which also allows making reliable “tightening” between the rafters, so that you can go under them in the attic, slightly bending down.
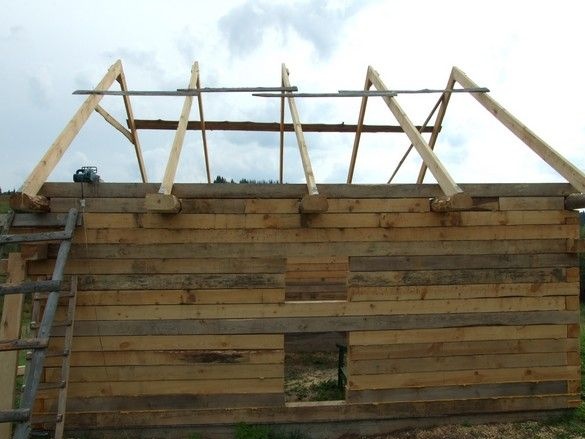
The rafters are placed on the rafters. The ends are fixed with metal strips. After installing the rafters in a vertical position, they were fixed with "technological" fasteners. The reinforcing boards were pinned to the connection of the two rafters, I don’t know what they are called correctly.
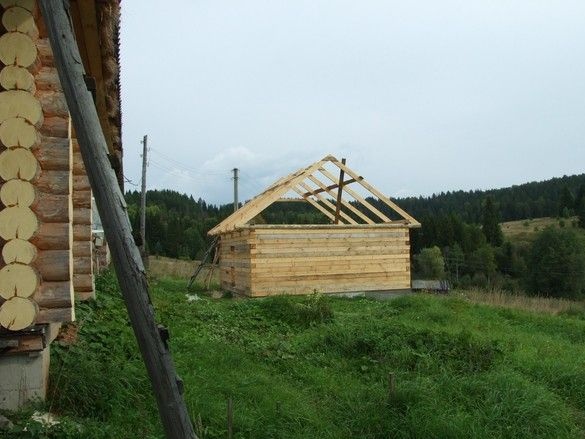
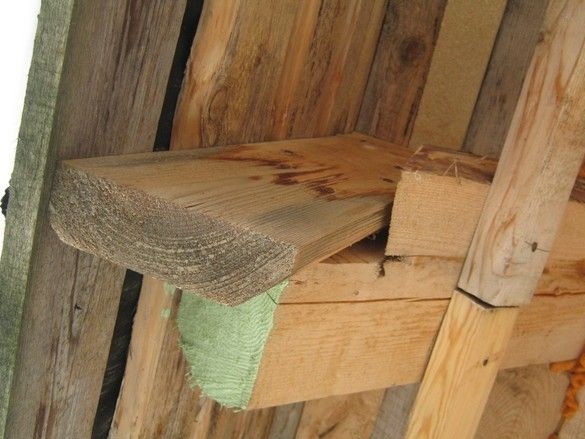
A certain extension of the rafters was made, for the removal of the lower edge of the roof beyond the edge of the rafter beam, this will allow the flowing water not to wet the log, in addition, a piece of thick board additionally connects the rafter beam with the rafter.
The next step was to pump crates from non-thick boards. For the first time, the roof was supposed to be made of roofing material, so it made it thicker. Finally, the roof itself - two layers of roofing material, long slats, small cloves.
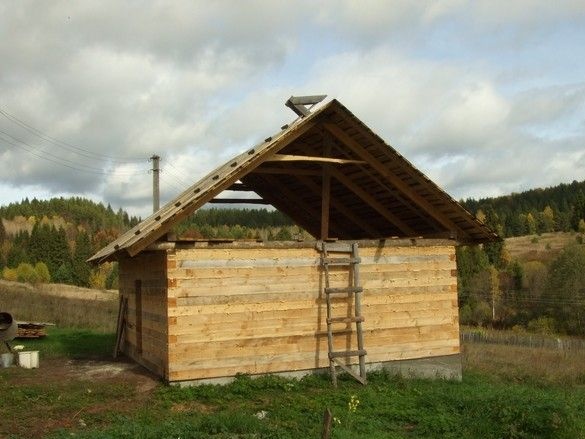
The entire standard set of reinforcing elements has been completed - puffs slightly above mid-height on each pair of rafters, two pairs of braces on each side. All of the boards are 30mm. Nails 100mm, under the caps of nails put "body washers M6". Marked and sawn doorway.
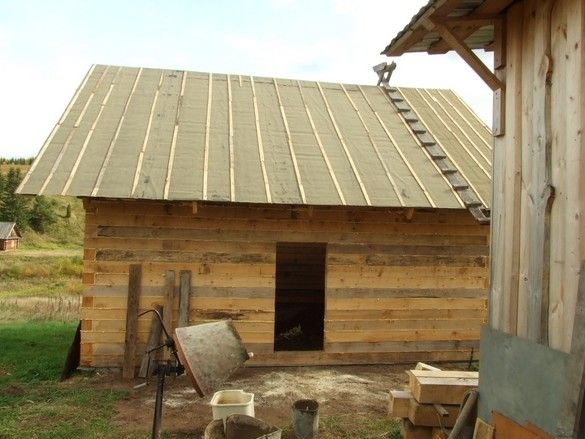
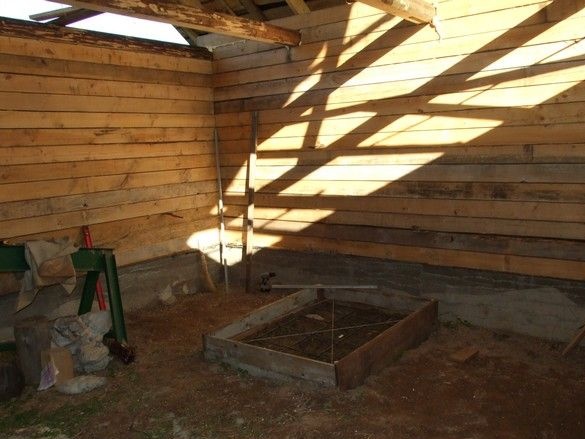
Not shelving, cast foundation for the furnace.
Ceiling, gables, door. The window appeared in my second year, the first, I lived without daylight, like a mole.
The ceiling is insulated by rolled rolls of mineral insulation. In two layers, I hope temporarily, so I tried to get by with a minimal sharp.
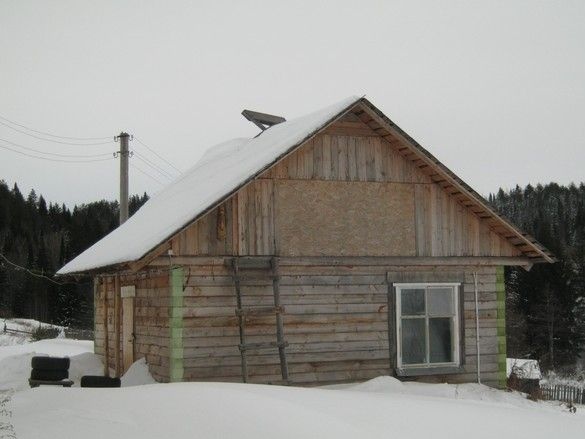
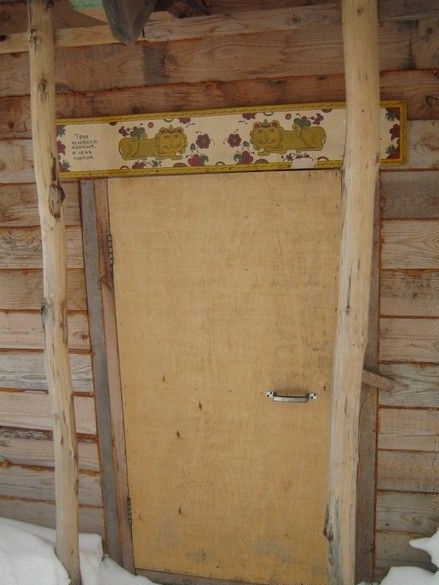
Gradually, the workshop is being improved, a brick stove is built, along the entire northern wall there are shelving up to the ceiling, the lower shelf of which is a table for small sitting work, including for experiments with electricity. In the center, a home-made pin-pong table, standard sizes. Unfortunately, it turned out to be such a comfortable working surface that it is released quite infrequently. Thoughtfully divorced electricity with an abundance of outlets in any corner.
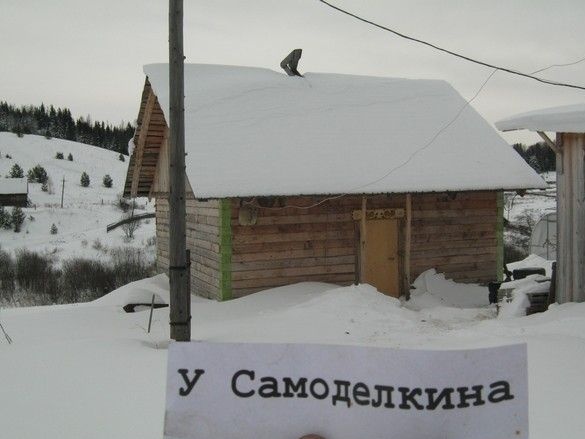
Of course, much still needs to be done, much would be desirable, however, and what is, allows, without exaggeration, to bliss.