Good day to all. This article will be interesting to everyone who works with metal. All the masters of their craft, faced with such a task when it is necessary to make many elements, for example, for a fence, railing, canopies, etc. To do this, cut a decent amount of blanks from metal wire, rods or strip. Of course, many will say that it is not a problem to make a conventional angle grinder, but angle grinder or electricity is not always at hand, and cutting a large amount of metal wire with angle grinder is a long and costly process for a metal strip. Here is the author of the channel "Kovko Kova4" and decided to assemble such a manual machine for cutting wires and rods do it yourself. Who cares how and from what, the author assembled the machine, as well as what he got as a result, read the article or just watch the video at the end of the article.
Materials used by the author:
Spring leaf 8 mm thick and 63 mm wide.
M 8 bolt threaded to half the bolt, washer and a pair of nuts to the bolt. 2
A hardened finger 10 mm thick washer to it and a cotter pin.
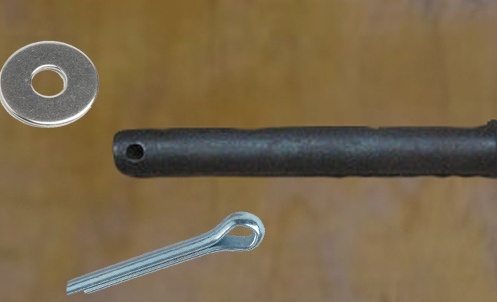
And one more bolt and an extended nut to it.
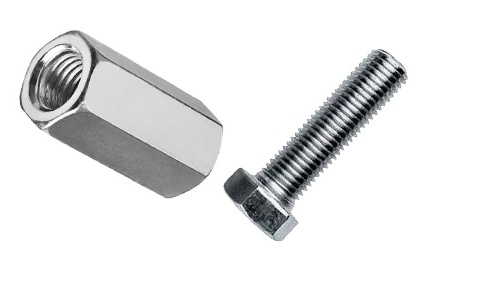
First of all, the author cut out all the details from a cardboard with a width of 63 mm and made a mock-up of the machine.
After the spring leaf was cut into pieces of the right size.
Then he transferred all the details from cardboard to pieces of spring.
Then, using angle grinders and a file, I cut and fitted all the details.
He also sharpened the cutting edge of the future machine. Sharpening for such machines should be slightly less than 90 degrees.
When all the machine parts were cut.
The author warmed up the details with cutting edges.
After he quenched these parts in oil.
The red-hot finger will be the axis of the driven part with teeth.
The second axis will be a bolt.
Next, I collected all the details.
Also details on the front sides of the machine.
After I checked the course of moving parts.
From the elongated nut and bolt, the master made a persistent-adjusting mechanism. Which is very important for the correct cutting of blanks. Also one more not unimportant advice from the author, there should not be a gap between the cutting parts, they should move into grinding in without any gaps and backlashes.
After the author has welded all the details.
After welding each seam twice.
On the machine bed, the author made holes in the corners for mounting the machine.
For the lever, the author took a pipe and was slightly crushed from one edge, so that it was worn on the leading part of the machine.
Such a small, hand-made stitch turned out by the author of our today's article.
Well, now, as usual, the test.
Bar 6 mm.
The strip is approximately 1.2-1.5 mm thick.
The workpiece is 8 mm thick.
3 mm strip.
The hairpin is 10 mm thick.
Round timber 10 mm.
That’s all for me. Thank you all and see you soon!
Video: