Hello dear readers!
In any workshop or the garage, one of the most important and necessary tools in the repair or manufacture homemade it's a vice. But the cost of a seemingly simple tool is now quite high. I will tell you how you can make yourself reliable locksmith's vise from a steel corner or channel, and other metal trash.
Necessary materials:
- A channel or two welded along a corner.
- Steel corners
- Sheet steel, plates
- Steel stud or finished screw
- Bolts, nuts, washers
- Spray paint
- Litol grease.
Tools used in the manufacture
- Welding machine
- Bulgarian with cutting and cleaning discs
- Drill, metal drill
- Ruler, square, marker.
Manufacturing process
Since the channel of a suitable size could not be found, it was necessary to weld two corners along.
Photos of the start of production have not been preserved, so I am applying the scheme. For subsequent photos, everything will be clear.
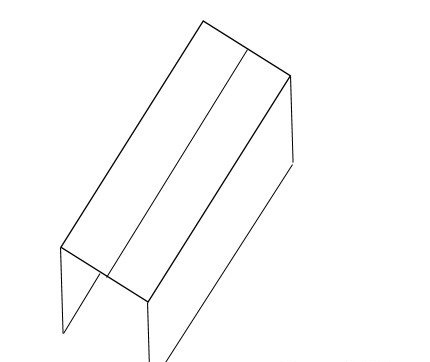
We make the base of a vice from two corners and plates. I used 5mm thick. First, we weld a sleeve with a female thread or several nuts for a vise screw onto the bottom plate. They must be lifted above the platinum by welding with a gap or by placing a plate of the required thickness so that in the future they are in the center of the guide channel and there is no misalignment of the vise screw.
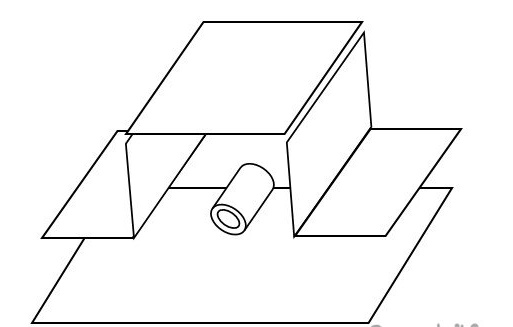
Putting it on tacks, we check that the guide channel moves freely at the base without noticeable backlash and scald completely.
On the channel, we weld the jaws of a vice and reinforce the corners. These will be movable sponges.
Similarly, we produce the second fixed jaws by welding them to the base.
We reinforce the lining on the corners
We weld the plate to the end of the guide channel in which there will be a hole for the vise screw.
The screw was made from a stud by welding the cooker from the collar of the old socket wrench.
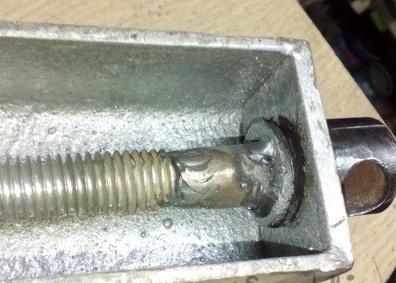
Welded reinforcing plates on the inside of the jaws.
I cleaned the irregularities with a cleaning disk and scalded the base on the office, made a hole for the mount.Made removable sponges from a spring.
I drilled and cut the thread under the sponge.
And so that when striking with a hammer, the bolts of the jaws should not be cut off, the thrust shelves under the sponges should be welded, and well-welded, weld more metal. From the same spring I cut and welded an anvil for small works.
After final grinding with a petal disc and painting from an aerosol can, the vice looks like from a store and ready to work.