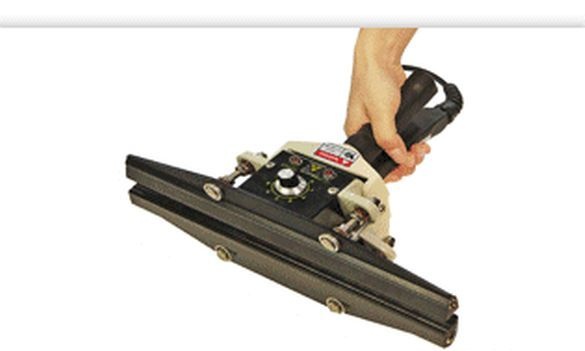
Recently, inexpensive machines for welding a plastic film have appeared on the market, but their drawback is the performance of one operation. Author homemade offers to make a multifunctional "sealing machine" do it yourself. The author also shows several examples of the operation of such a device.
Tools and materials:
-Soldering iron
- Two tips for the soldering iron
PTFE tape
-Rule
-Two self-tapping screws
PVC film
-File
-Hammer
-Sandpaper
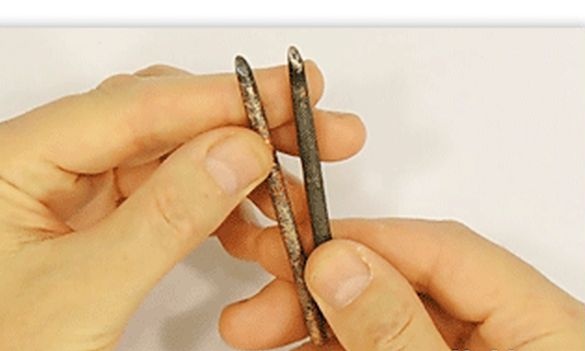
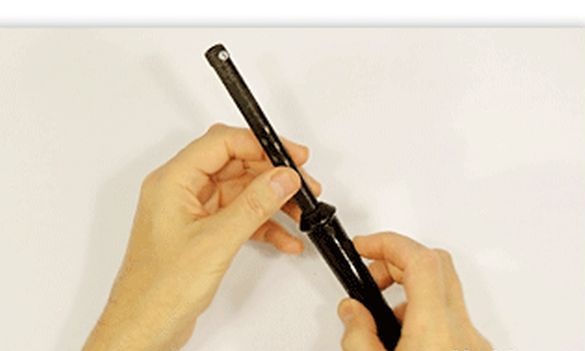
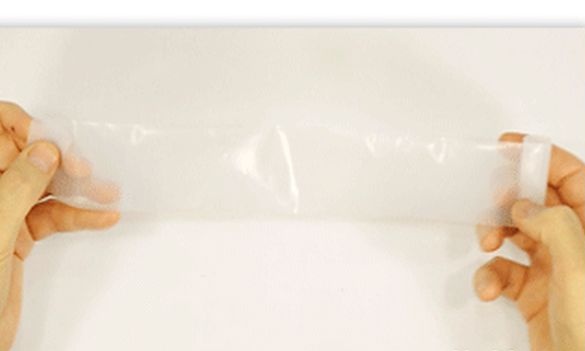
The author purchased the fluoroplastic tape in the market where they sell heating elements. If it is impossible to purchase a tape, you can replace it with a substrate from self-adhesive wallpaper. The author recommends using a soldering iron at 40-60 watts.
Step 1: Making a mandrel for welding and trimming

The first mandrel is required to seal the edges of the bag and at the same time removes excess film.
The principle of operation is simple. The film is pressed against the surface of the guide. Along the guide, a mandrel is inserted into the soldering iron, which seals the edge of the film and at the same time “cuts off” the excess. In this case, the angle of inclination of the mandrel is 30 degrees, and the rounding of the end face does not allow to damage the template.
To make the mandrel, the author flattened the end of the sting with a hammer. With the help of a file, he gave it the final shape. Sandpaper polished the surface.
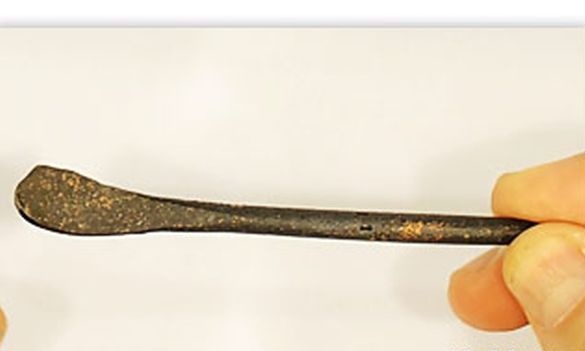
Step 2: Production of a mandrel for welding bulkheads
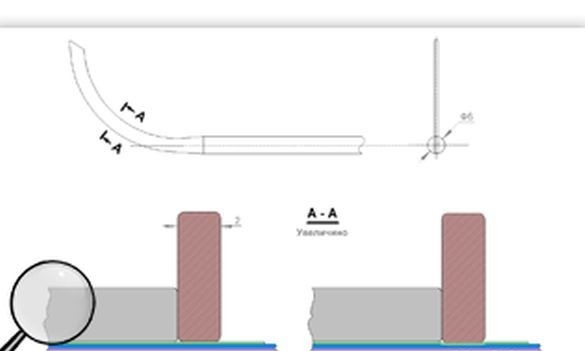
The second mandrel is designed for welding partitions in manufactured products, and has a flat work surface. In contrast to edge welding, when welding partitions, it is necessary to place a fluoroplastic gasket between the mandrel and the film. Such a mandrel is capable of welding two films of 0.1 mm each. Empirically, the author found that with a fluoroplastic gasket thickness of 0.08 mm, a working surface of the mandrel equal to 2 mm is necessary for welding a 0.1 mm film.
To make the mandrel, the author used the second sting.
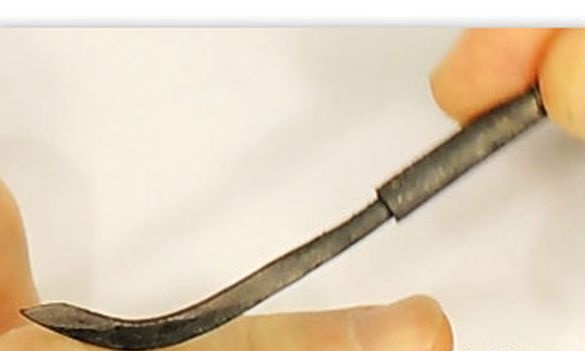
Step 3: Making the retainer
Not all soldering irons have the option of replacing the tip. The author found a way out of the situation by drilling a hole in the bottom of the soldering iron and cutting the thread for the screw.

Step 4: Making the Guide
In order for the mandrel to move smoothly on the surface, the author used a ruler. A fluoroplastic tape was fastened to one edge of the ruler with screws. The guide is ready.
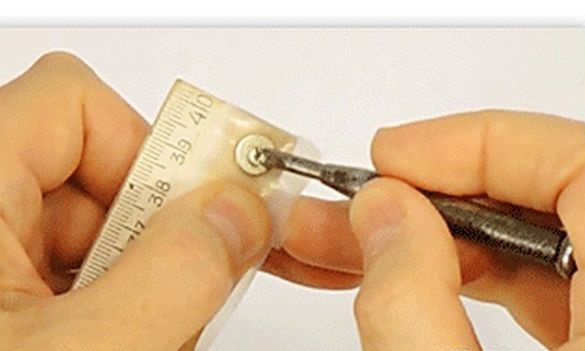
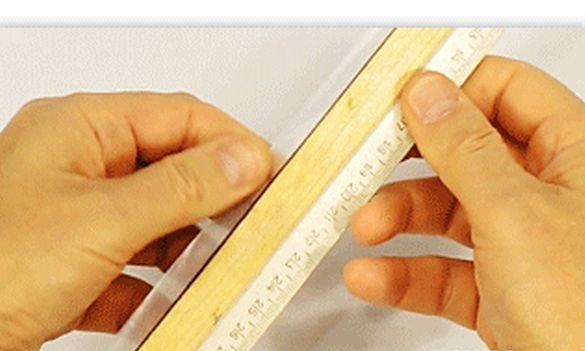
The device for soldering the film is ready. Consider a few examples of the use of such a device. According to the author, it is best to solder at a mandrel temperature of 300-350 degrees.

Production of packaging for several types of fasteners
Of course, you can pack all the fasteners (or other small parts of different functionality) in one cell, but it is much more convenient if each type has its own compartment.
First you need to draw a template on a piece of paper. The author marked the edge on the template with a dashed line, the middle is solid.
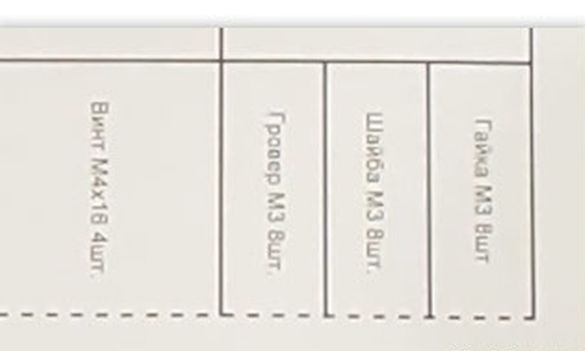
On a hard surface, using tape, secured the template. I put two pieces of film on the template, slightly larger than the template. I installed a mandrel for partitions in the soldering iron. He pressed the film guide to the template. Since the internal compartments are first soldered, the guide is installed with the fluoroplastic tape down. Holds a mandrel fixed in a soldering iron and heated to the desired temperature along the internal lines of the template.
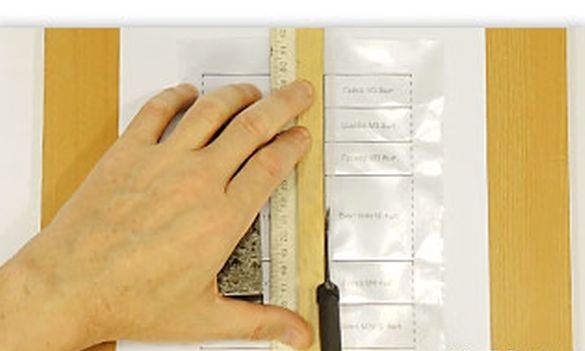
After compartments have been formed, the mandrel changes and seals and cuts the side walls of the package.
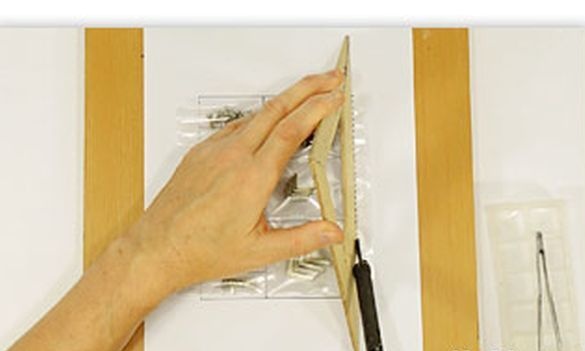
Fills compartments with necessary details.
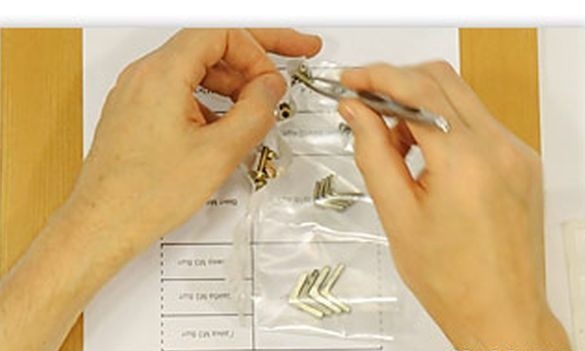
Seals the remaining edges.
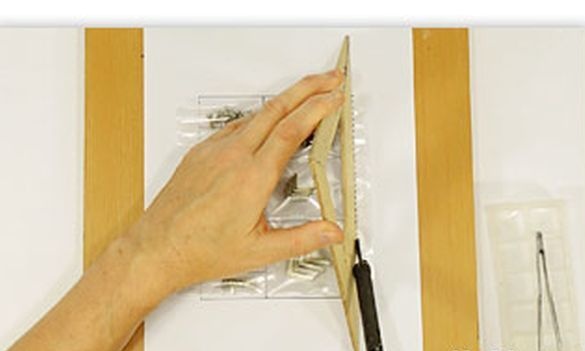
All is ready.
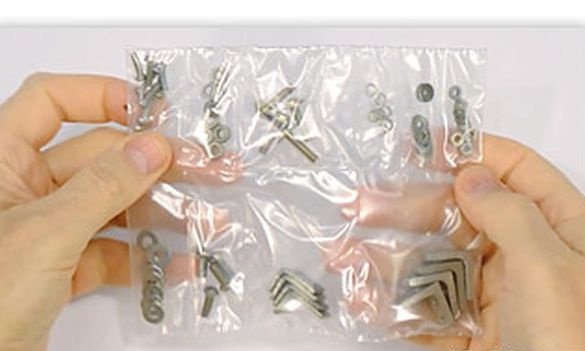
Remote Case
For the manufacture of a cover, it is better to use shrink film.
Having measured the remote control in the thickest place, I made a template and cut the film according to the template.
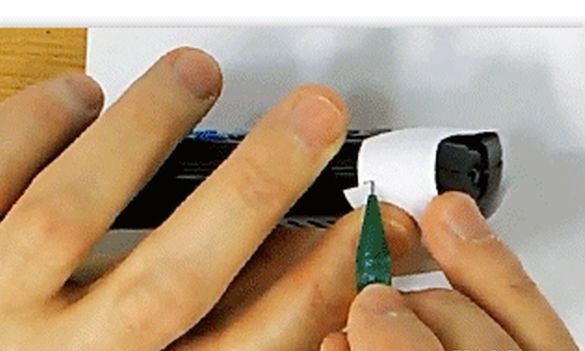
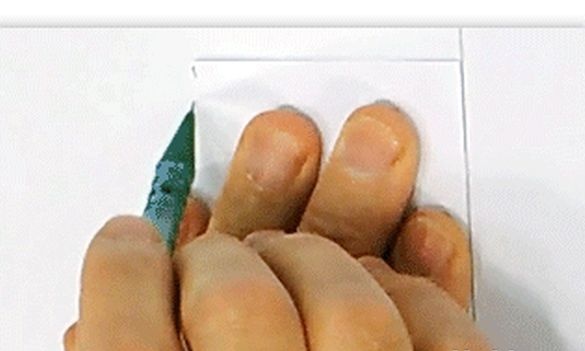
I wrapped the remote control in foil and sealed the edges.
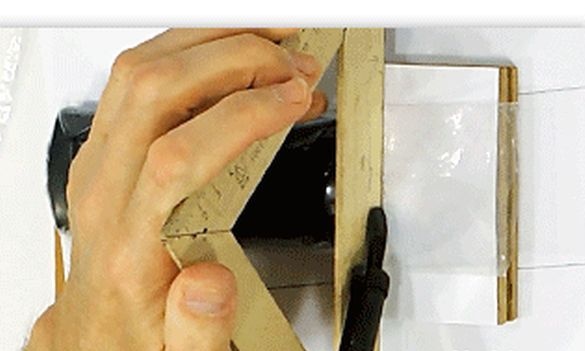
With the help of a hairdryer, I set the film over the entire surface of the remote control.
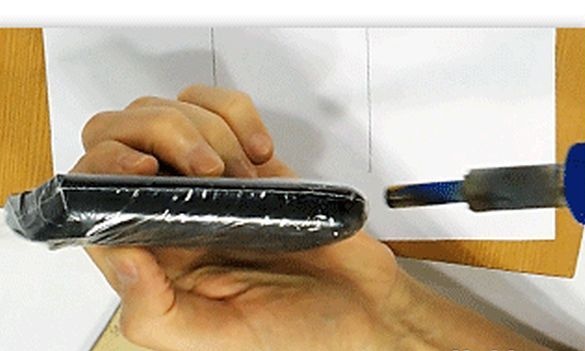
The cover is ready.
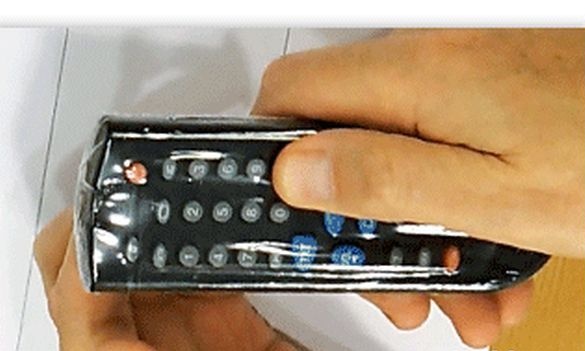
Making cassettes for ice.
According to the template, the cells were soldered.
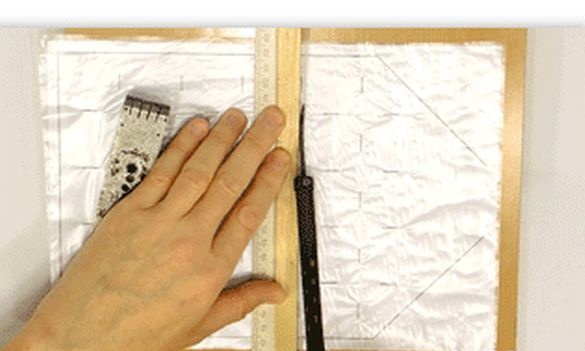
Cut off the neck of a plastic bottle.
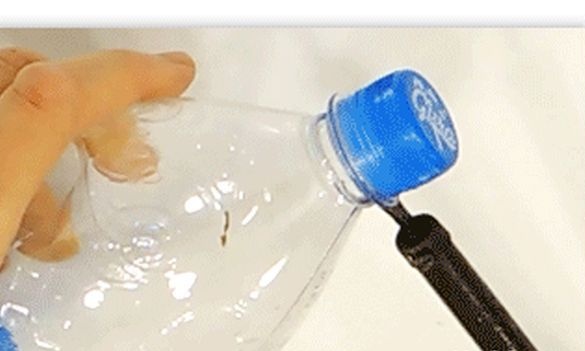
He slipped the unsealed part of the cartridge into the neck and filled the cartridge compartments with water. Tightened the cork. Put the cassette in the freezer.

To make it easier to separate the ice from the packaging, you can hold the cassette under warm water.
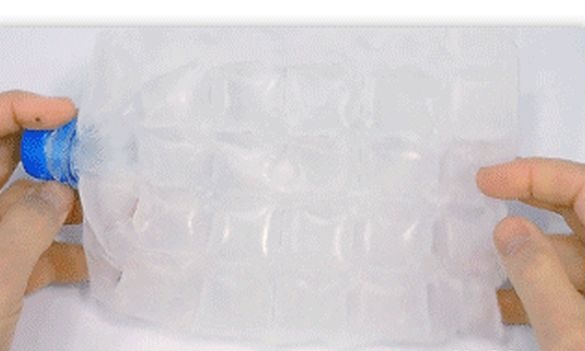
Template for cassette, as well as for battery cases can be downloaded:
You can watch more details about homemade work on the video.